using 4mm aluminium as a baffle, bolted on to the wood underneath. Changing the aluminium front plate would allow for trying out different units if the cutout behind were generous. what effect would this have on sound? It would be stiff, of course.
Something i've wanted to try for sometime. I've got the aluminum, and the shop next to Chris' does waterjet cutting so sometime
bamboo. Looks nice and available as worktops for instance, as well as flooring
A wonderful material. There are a range of products. The stranded outer, cored plywood is by far the stiffest (and very dense). I've a pair of Fonken & a pair of dMar-Ken7 awaiting drivers in this last. Not cheap stuff, but with care in construction nothing but a clear finish needed.
Chris has made comments in other threads on construction "issues"

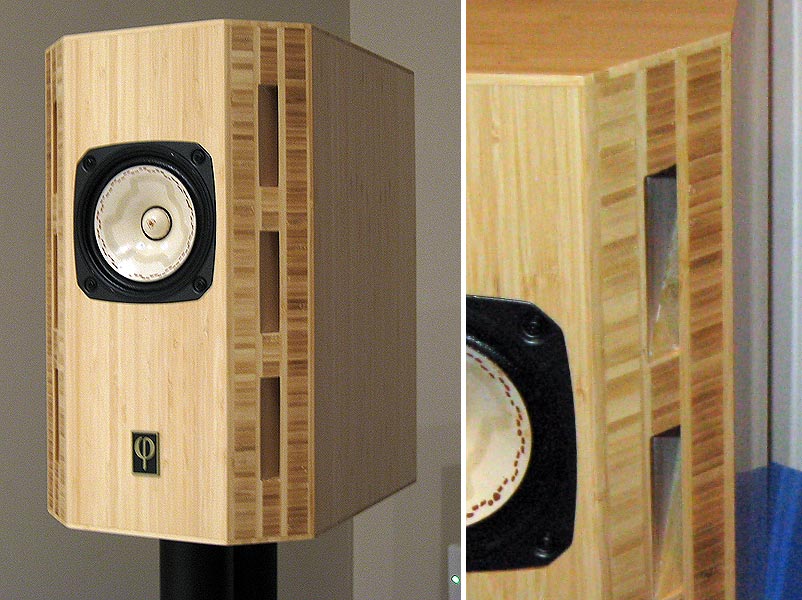
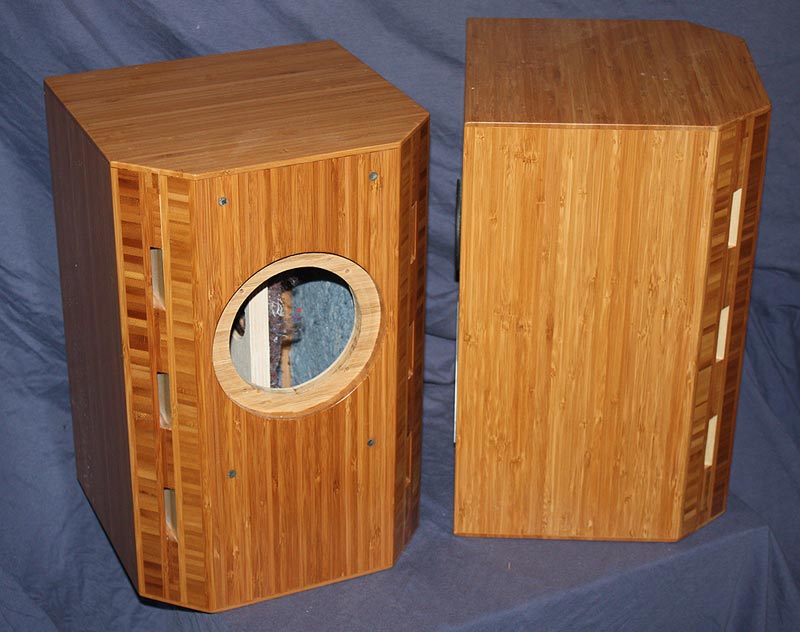
various plastic laminates. High-density polyethylene HDPE for instance or Tufnol - see 20mm - Direct Plastics Online
That looks interesting -- calling it a laminate is a bit of a stretch (i consider a laminate to be used like a veneer -- a good plastic laminate, inside & out, can go a long way to stiffening a box panel. Like Corian or other solid surface plastics it may have some practical issues (Chris?). We have discarded as a box materialCorian except for top & bottom instead of veneer.
Be nice if the specs were in a comparable format.
ASTM D 3043 Method D Flexural Strength (MOE/MOR)
- ¾ inch thick, 1-ply, Edge Grain: 179 MOE/11,371 MOR average
- ¾ inch thick, 3-ply, Cross Core: 148 MOE/9,109 MOR average
- ¾ inch thick, 3-ply, Cross Core Strand: 268 MOE/14,762 MOR average
Carp Brand TUFNOL Sheet
- Tensile strength 68 Pa
- Young's modulus 6.5
sound deadening Green Glue as a filler between layers
I've seen lots of discussion on this already (here and on stereonet.au). Geddes doesn't think it as good as it should for constrained layer construction
Thre constrained layer is very effective, but dramatically complicates a build.
dave
This is what I was thinking of doing. Did you put any material between the alu front and the MDF or was it just bolted straight on? Did the alu plate cover the whole front or just round the speaker units?
andy
Just bolts so far but I may glue them later. My idea is that the dissimilar materials damp each others natural resonance - and it seems to work well.
This is still work in progress - I'm thinking that I will try a separate cab for each driver - but I attach a pic for progress thus far . . .
Attachments
I had a go with solid beech for subwoofers and have been blown away with the stiffness of the material. So much so they're not braced AT ALL!
They look damn great too. Some of you may have seen these images elswhere as I've been trying to sell them and messed around loads with it LOLOL.
Material is 40mm and 29mm thick
They look damn great too. Some of you may have seen these images elswhere as I've been trying to sell them and messed around loads with it LOLOL.
Material is 40mm and 29mm thick
Attachments
Last edited:
Just bolts so far but I may glue them later. My idea is that the dissimilar materials damp each others natural resonance - and it seems to work well.
This is still work in progress - I'm thinking that I will try a separate cab for each driver - but I attach a pic for progress thus far . . .
I love the look of this, very tasty looking
Ive been thinking about making a laminate of some undecided wood, perhaps aluminium plate, and an acrylic or something, maybe nylon, maybe finishing with glasstape and resin on the inside, and wondering if it was worth persuing. After seeing this project, i think i should definately give it a try.
Last edited:
I love the look of this, very tasty looking
Thanks, when they're finished the ali will be covered with cork - I heard cork was a good choice as a outer covering because of the uneven surface.
The difference between these composite baffles and original 1" MDF baffles that came with these cabs is quite significant so I think it's well worth experimenting.
My top two choices would be what I did here with ali & mdf or 6 - 9mm MDF or similar on the outside lined with 12 - 18mm of concrete inside. I tried this latter method with OB and it worked well.
My general take is to simply use two dissimilar heavy materials bonded together to damp resonances - but however much we can reduce cabinet vibration it's very hard to eliminate it completely so next I try a different cab for each driver to stop inter driver interaction.
Village plank - where did you get that solid beech? I'm in the UK too and interested! As far as I gather, strips glued together are more stable and less likely to crack.
Andy
Andy
Village plank - where did you get that solid beech? I'm in the UK too and interested! As far as I gather, strips glued together are more stable and less likely to crack.
Andy
Here you go....
Beech Worktops
I dare you to have a go with Wenge lolol..... super expensive!
Indeed the 40mm x40mm staves are 93 times stronger than MDF and 66 times stronger than birch ply of the same thicknesses in tension testing. People need to listen to this as I will only say this ONCE...... you ready........ Drum roll...... PROPERLY KILN DRIED AND TREATED HARDWOOD WILL NOT MOVE, SPLIT, WARP, CHECK, SHRINK OR EXPAND...... END OF!!!!!
Last edited:
This recently generated graph is relavent to this discussion.
It shows the relative energy available to excite a resonance relative to a likelihood of 1 at 300 Hz. 300 Hz was choosen because this is considered the typical point where half the energy in the music is above, and half the energy below, and is key to one of the suppositions that leads to a 1/forth power.
A/ 1/second power falls out of the way a cone driver works to mantain flat frequency response
I argue that we can achieve the 4th power by considering:
B/ the "quantity" of music falls with increase in frequency
C/ the effectiveness of the panel material's damping increase as the wavelength decreases vrs material thickness
dave
It shows the relative energy available to excite a resonance relative to a likelihood of 1 at 300 Hz. 300 Hz was choosen because this is considered the typical point where half the energy in the music is above, and half the energy below, and is key to one of the suppositions that leads to a 1/forth power.
A/ 1/second power falls out of the way a cone driver works to mantain flat frequency response
I argue that we can achieve the 4th power by considering:
B/ the "quantity" of music falls with increase in frequency
C/ the effectiveness of the panel material's damping increase as the wavelength decreases vrs material thickness
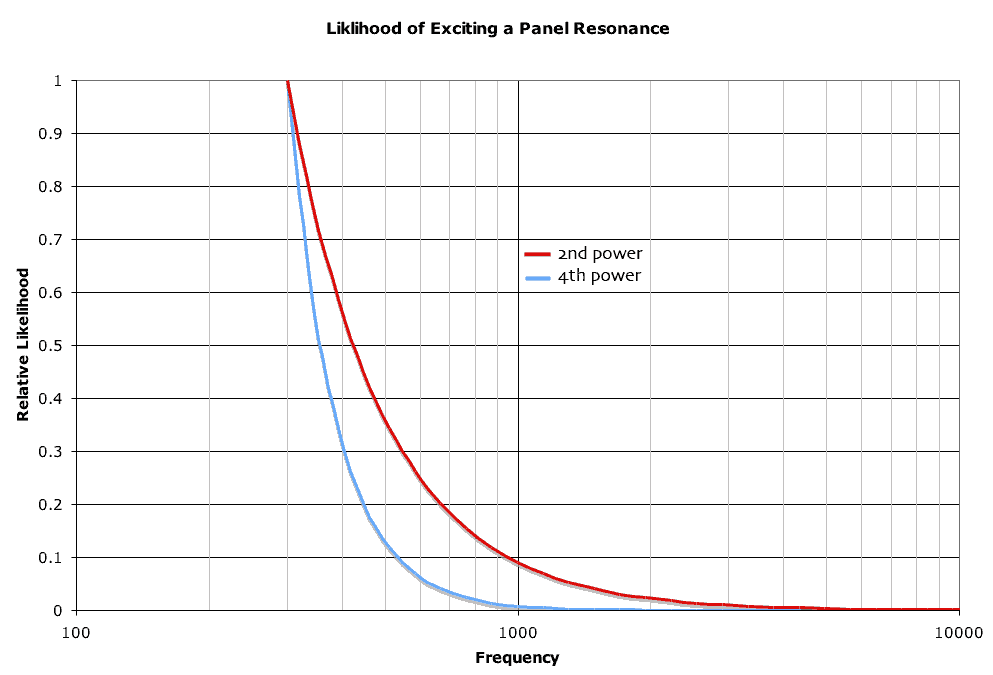
dave
Gentlemen, first I have to say - I'm an (automotive) engineer. I don't believe in rumours and hearsay, I prefer data over politics. Instead of belief I trust in data. In 2008 a German magazine - stereoplay - published in one of their issues a supplement about DIY loudspeakers. One of the six articles, written by Bernd Timmermanns (inventor of many DIY loudspeakers, like the Needle), was about best material for loudspeakers. You can read it here, when you use an online translator, ie. Google (hopefully the link works):
Boxenselbstbau - Gehäusematerial - stereoplay - Magnus.de
Take a look at the graphs and come up with your own opinion. My personal conclusion from this article is, in general: the heavier - the better, due to higher density.
Outcome is that at roughly the same thickness, slate scores the highest over concrete and MDF, which finished on third position. Famous baltic birch ends up on rank 7 from 8 contestants.
Baltic birch is the preferred material for all highly stressed applications and the No. 1 for PA speakers. By the way, I used baltic birch for my own DIY speakers ...
Helmut
Boxenselbstbau - Gehäusematerial - stereoplay - Magnus.de
Take a look at the graphs and come up with your own opinion. My personal conclusion from this article is, in general: the heavier - the better, due to higher density.
Outcome is that at roughly the same thickness, slate scores the highest over concrete and MDF, which finished on third position. Famous baltic birch ends up on rank 7 from 8 contestants.
Baltic birch is the preferred material for all highly stressed applications and the No. 1 for PA speakers. By the way, I used baltic birch for my own DIY speakers ...
Helmut
Alas, here we come to the perennial issue that was most pertinently voiced by Sir Nathaniel Barnaby in the 1870s: viz. that anyone can set a criteria & claim something to be unsuitable if it does not conform to the goalposts they have established. One person can do that, and then another person can come along, change the criteria, and claim the exact opposite.
The discussion re. build materials has been repeatedly held on many threads on DIYaudio & has been very thoroughly dealt with by some very knowledgeable members. However, FWIW, since it has cropped up again:
-Since it is essentially impossible to build a box which does not resonate at all, it becomes a matter of controlling panel resonance, i.e. pushing it to a region where there is little energy available to excite it. In practical terms, this means we either need to move the panel Fs above or below the functional BW of the enclosure.
-Moving panel Fs upward, above the operating BW of a bass enclosure is relatively easy by using a light, stiff panel (sometimes with some strategic bracing). Since stored energy rapidly drops with increasing frequency, the panels require very little damping.
-Moving panel Fs down, below the operating BW of a bass enclosure is much harder. Extremely high mass is needed given that the lower the Fs, the greater the amplitude & the wider its BW will be. Since it is rarely practical to go to this extreme, the high[er]-density / mass panel will typically require much more damping to push its resonance modes to a sufficiently low level to be acoustically innocuous.
-About 1 1/8in of MDF is ~equal to the stiffness of 3/4in BB plywood based on their respective MOE values, albeit with substantially greater mass.
The discussion re. build materials has been repeatedly held on many threads on DIYaudio & has been very thoroughly dealt with by some very knowledgeable members. However, FWIW, since it has cropped up again:
-Since it is essentially impossible to build a box which does not resonate at all, it becomes a matter of controlling panel resonance, i.e. pushing it to a region where there is little energy available to excite it. In practical terms, this means we either need to move the panel Fs above or below the functional BW of the enclosure.
-Moving panel Fs upward, above the operating BW of a bass enclosure is relatively easy by using a light, stiff panel (sometimes with some strategic bracing). Since stored energy rapidly drops with increasing frequency, the panels require very little damping.
-Moving panel Fs down, below the operating BW of a bass enclosure is much harder. Extremely high mass is needed given that the lower the Fs, the greater the amplitude & the wider its BW will be. Since it is rarely practical to go to this extreme, the high[er]-density / mass panel will typically require much more damping to push its resonance modes to a sufficiently low level to be acoustically innocuous.
-About 1 1/8in of MDF is ~equal to the stiffness of 3/4in BB plywood based on their respective MOE values, albeit with substantially greater mass.
Last edited:
seems like the ideal topic to allow hype into the forum.
Having built many cabinets out of both materials over the years I am at pains to hear the difference, even allowing for the bracing argument. My take is that 99% of the builders here would not be able to tell the difference either.
There will always be technical specifications to give schoolboys material to argue about, but in an area such as this who can relate the actual spec to what they hear? not many is my guess.
Hype aside, this argument does seem to get trotted out when there is a need to discredit somebodies design or build.
The bigger issue I would have thought would be the safety of the material when used in a DIY environment. But I can't see the problem when mdf is used in a controlled dust-free environment.
Having built many cabinets out of both materials over the years I am at pains to hear the difference, even allowing for the bracing argument. My take is that 99% of the builders here would not be able to tell the difference either.
There will always be technical specifications to give schoolboys material to argue about, but in an area such as this who can relate the actual spec to what they hear? not many is my guess.
Hype aside, this argument does seem to get trotted out when there is a need to discredit somebodies design or build.
The bigger issue I would have thought would be the safety of the material when used in a DIY environment. But I can't see the problem when mdf is used in a controlled dust-free environment.
Hello,
I did myself experienced the effect of material on the sound of DIY speakers.
First one : I made a 2D oval enclosure (and straight the third D) for cheap speakers (Audax AP100Z0)
To allow this semi-oval, I used 5mm plywood bended on the front and back MDF oval baffles. (Overall height is about 20cm)
Knocking this enclosure with one finger let it "sing" quite a lot.
Music played by this speaker is really "living" and neutral. No box sound.😛
I built aferward a "real egg" shape (flattened for the front baffle) with slices of MDF. The enclosure thickness is something between 15 an 25mm (depending on the slice of the egg).
The sound, with same speaker, is rather dull and unappealing.
Another project conducted me to build a double wall enclosure (lateral panel) made of inner 6mm pine and outer 5 mm ply, separated by 6mm space. The aim was to fill the space with sand.
I never had to fill this space between, because this speaker sound so neutral and light, 😀 despite the finger knocking sound is very present.
These were only experiments, and as I do not have Scottmoose knowledge, I din't expect thie results.
But reading Scott' explanations, I tend to the same conclusions as his !
Plus one added : bending plywood adds stiffness without increasing mass !
Cheers
I did myself experienced the effect of material on the sound of DIY speakers.
First one : I made a 2D oval enclosure (and straight the third D) for cheap speakers (Audax AP100Z0)
To allow this semi-oval, I used 5mm plywood bended on the front and back MDF oval baffles. (Overall height is about 20cm)
Knocking this enclosure with one finger let it "sing" quite a lot.
Music played by this speaker is really "living" and neutral. No box sound.😛
I built aferward a "real egg" shape (flattened for the front baffle) with slices of MDF. The enclosure thickness is something between 15 an 25mm (depending on the slice of the egg).
The sound, with same speaker, is rather dull and unappealing.

Another project conducted me to build a double wall enclosure (lateral panel) made of inner 6mm pine and outer 5 mm ply, separated by 6mm space. The aim was to fill the space with sand.
I never had to fill this space between, because this speaker sound so neutral and light, 😀 despite the finger knocking sound is very present.
These were only experiments, and as I do not have Scottmoose knowledge, I din't expect thie results.
But reading Scott' explanations, I tend to the same conclusions as his !
Plus one added : bending plywood adds stiffness without increasing mass !
Cheers
More off topic noise: I spent a very entertaining weekend with these once:
Kiso HB-1
Sticking your head against them, the sides were relatively quiet (?!) but the backs were singing! They do not sound particularly coloured and are very musical. Totally against conventional wisdom as far as speaker enclosure construction is concerned.
My hunch is that its the pattern/harmonic relationships within resonant structures that we respond to. We are tuned to recognise and respond to natural sounds, some materials naturally have more pleasing/natural harmonic relationships in their resonant signature than others.
Kiso HB-1
Sticking your head against them, the sides were relatively quiet (?!) but the backs were singing! They do not sound particularly coloured and are very musical. Totally against conventional wisdom as far as speaker enclosure construction is concerned.
My hunch is that its the pattern/harmonic relationships within resonant structures that we respond to. We are tuned to recognise and respond to natural sounds, some materials naturally have more pleasing/natural harmonic relationships in their resonant signature than others.
Possibly, but from my POV, you don't want panels to audibly resonate; a speaker is not a musical instrument, it is there to reproduce the material which is fed to it, not make contributions of its own devising. Granted, that's a bit of a grey area in the single-driver world, where the drivers themselves & many cabinets do not necessarily have, say, a particularly linear frequency response, but the point remains.
Generally speaking, I do think Ed has a good point. MDF is a whole lot better than nothing at all. That said, it's technically inferior to something like BB ply, so I'm loath to recommend it, especially for large enclosures.
IIRC, one idea that was floated a while back was to use wood-hardener on it. How much of a difference it would make I don't know; I think people who tried it ran into some issues with the stuff causing small internal cracks / fractures over the medium - long term, so YMMV.
Generally speaking, I do think Ed has a good point. MDF is a whole lot better than nothing at all. That said, it's technically inferior to something like BB ply, so I'm loath to recommend it, especially for large enclosures.
IIRC, one idea that was floated a while back was to use wood-hardener on it. How much of a difference it would make I don't know; I think people who tried it ran into some issues with the stuff causing small internal cracks / fractures over the medium - long term, so YMMV.
Last edited:
Possibly, but from my POV, you don't want panels to audibly resonate; a speaker is not a musical instrument, it is there to reproduce the material which is fed to it, not make contributions of its own devising.
On that, I think we all agree. Its achieving it that's the tricky bit! It's well documented that we can hear deep into a music signal. Subjectively it may well be that one resonant series at -30dB below mean SPL may be more acceptable than a more atonal one at -45dB. The Kiso's made me think about it, as they do work very well.
-35dB is taken as an acceptable threshold, so providing panel Fs & preferably its hamonic structure as well are outside the operating BW of the cabinet, that is achievable; whether someone feels it's worth it is another matter of course.
Take a look at the graphs and come up with your own opinion. My personal conclusion from this article is, in general: the heavier - the better, due to higher density.
And read the text as good i can with google translate. The context of the data presented removes so much information as to be useless. And with no description of the detail of the experimental apparatus (in particular, its size) the test provides as much information as a tweet. The only thing that does come out is that thicker material is better (only like materials can ne compared), but we knew that already.
What is graphed, i assume, is the energy under the curve for the entire range 100 Hz to 12 kHz, removing all imformation about the frequency of transmission and the Q.
This is akin to the common, and completely useless, THD measurement.
dave
My hunch is that its the pattern/harmonic relationships within resonant structures that we respond to. We are tuned to recognise and respond to natural sounds, some materials naturally have more pleasing/natural harmonic relationships in their resonant signature than others.
I have made conjecture that if high-Q resonances could be placed in between notes on the well-tempered scale they will be less likely to be excited.
dave
-35dB is taken as an acceptable threshold, so providing panel Fs
The results of studies that Toole shows in his book indicate that the threshold depends on the Q of the resonance. Higher Q resoances are harder to detect.
dave
- Home
- Design & Build
- Construction Tips
- Discussion on what materials to build speakers out of