You could try a plenum directly in the block - a circular volume milled along the axis of the turbine - with an outlet on one of the faces to your main external plenum.
Owen
Owen
Owen- was just about to post when I saw yours.
Great minds think alike 😀. That is what I'm working on now.
Back from pump planning to actual work..
First another chapter in the motor journey. I had discovered that when the motor was left idle for an extended period of time (days), the top bushing would loose enough of it's oil to cause a light scrub. After re-oiling it, it would go away. With a load, I found it was much worse..it would start to scrub after 20 min. or so. Clearly the oil was too light for the job. In addition, the intermittent noise returned. We have been experiencing some bitter cold lately (single digits), and I suspected the metal had contracted enough in my unheated shop to have broken some glue joints on the motor mount. As much as I really didn't want to, I broke down the motor to re-lube and inspect it. Sure enough, two rubber blocks had come free. I re-glued them, and while that was setting, inspected the spindle and bushings. The bushings looked great, but the spindle was a little scuffed. This was caused from the scrubbing. Rather than oil, I reassembled with Mobile1 synthetic bearing grease. This worked a treat. It's as quiet as ever, and in addition, I filled the void in the pulley bottom that covers the bushing, making a dandy grease well. I ran it for several hours under load with no problems. Let's hope that this is the end of it.
The last thing I had done in the shop was to break off a tap in the motor strap for the belt tensioner I've been working on. After punching it out, I drilled the hole clean, and pressed in an aluminum pin, and re-drilled and tapped. Here is the strap, and the matching clevis...
I then mounted a pin in the motor cutout of the plinth for a pivot point...
and drilled a matching hole in the bottom of the motor..
Next I fabricated the bracket for the adjusting screw, and assembled the tensioner...
I still need to polish the pieces, and fabricate a purdy knob for it, but it works fantastic. I used a 28 TPI screw, giving me approx .036” of travel per revolution at the screw, and due to the pivot location, about half that at the motor. Setting up belt tension is actually fun now, compared to the nightmare of fudging the motor by hand before. Here is (finally) the table spinnin' under it's own power with the new motor assembly...
The new pulley profile is excellent. After dialing in the tension/angle, the belt holds it's position dead center. Under load, and the table sitting on a spongy bench, the motor does manage to vibrate ever so slightly..probably made worse from the thinner motor shelf. This noise is barely detectable with a stethoscope on the bottom plinth, but I couldn't detect anything (even with my screwdriver test) on the top plinth. I'm OK with this, and I suspect beefing up the motor shelf, and the table sitting on a proper stand will either eliminate it, or at a minimum, reduce it further.
As far as airborne noise goes, if you hold your ear an inch or so from the pulley, you can hear the hiss of the belt running on the pulley...thats it. You can also feel a slight vibration if you lightly touch the running belt..I'm OK with this as well. The minuscule level of energy here is unlikely to effect my platter.
I'm a happy lad 😀
I said I can see the light at the end of the tunnel earlier. Tallying the remaining tasks has made me realize it's a fairly distant light (finish work,stand, arm,etc.)..but at least I can see it.
-Casey
Edit: I forgot to mention that the motor comes inside with me now.
Great minds think alike 😀. That is what I'm working on now.
Back from pump planning to actual work..
First another chapter in the motor journey. I had discovered that when the motor was left idle for an extended period of time (days), the top bushing would loose enough of it's oil to cause a light scrub. After re-oiling it, it would go away. With a load, I found it was much worse..it would start to scrub after 20 min. or so. Clearly the oil was too light for the job. In addition, the intermittent noise returned. We have been experiencing some bitter cold lately (single digits), and I suspected the metal had contracted enough in my unheated shop to have broken some glue joints on the motor mount. As much as I really didn't want to, I broke down the motor to re-lube and inspect it. Sure enough, two rubber blocks had come free. I re-glued them, and while that was setting, inspected the spindle and bushings. The bushings looked great, but the spindle was a little scuffed. This was caused from the scrubbing. Rather than oil, I reassembled with Mobile1 synthetic bearing grease. This worked a treat. It's as quiet as ever, and in addition, I filled the void in the pulley bottom that covers the bushing, making a dandy grease well. I ran it for several hours under load with no problems. Let's hope that this is the end of it.
The last thing I had done in the shop was to break off a tap in the motor strap for the belt tensioner I've been working on. After punching it out, I drilled the hole clean, and pressed in an aluminum pin, and re-drilled and tapped. Here is the strap, and the matching clevis...
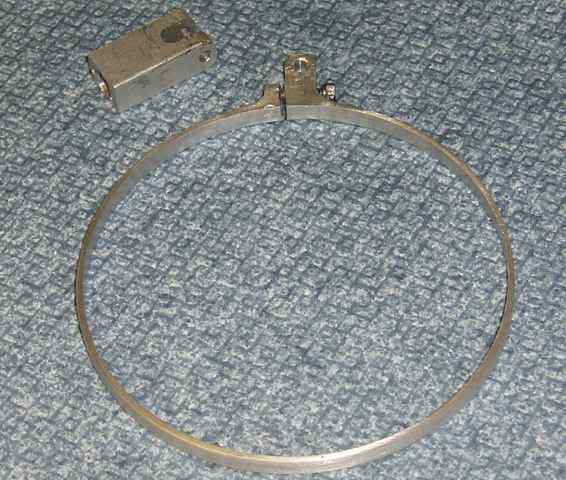
I then mounted a pin in the motor cutout of the plinth for a pivot point...
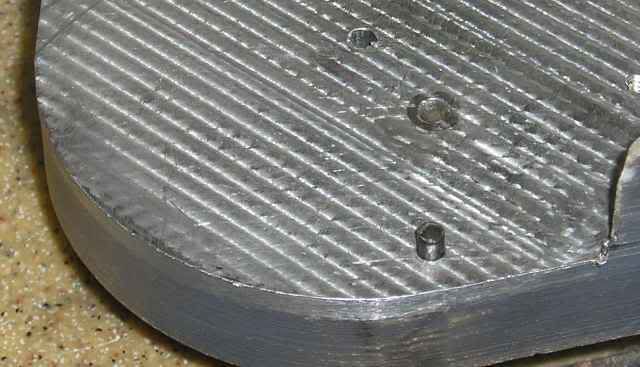
and drilled a matching hole in the bottom of the motor..
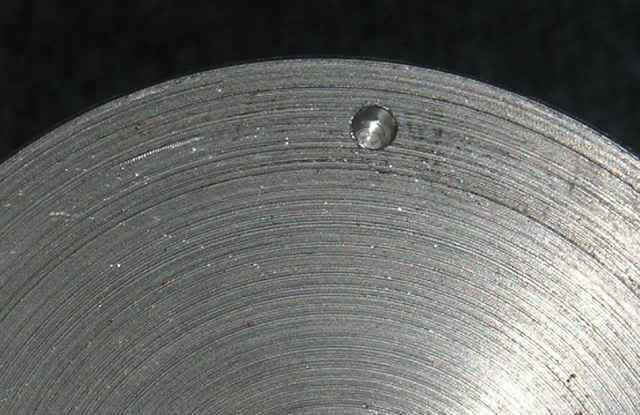
Next I fabricated the bracket for the adjusting screw, and assembled the tensioner...
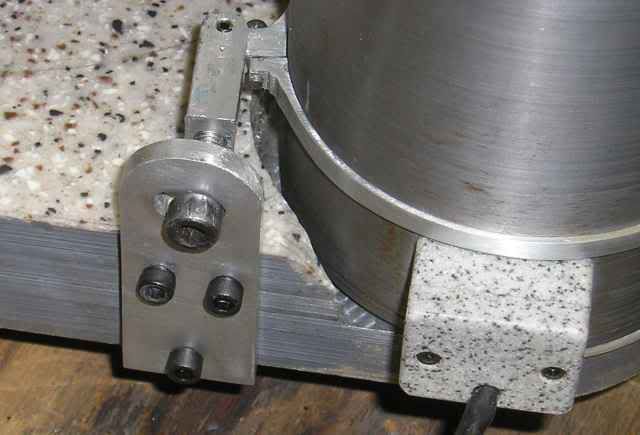
I still need to polish the pieces, and fabricate a purdy knob for it, but it works fantastic. I used a 28 TPI screw, giving me approx .036” of travel per revolution at the screw, and due to the pivot location, about half that at the motor. Setting up belt tension is actually fun now, compared to the nightmare of fudging the motor by hand before. Here is (finally) the table spinnin' under it's own power with the new motor assembly...
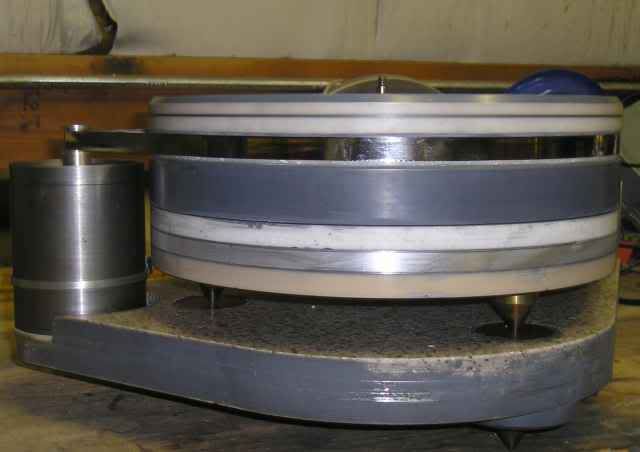
The new pulley profile is excellent. After dialing in the tension/angle, the belt holds it's position dead center. Under load, and the table sitting on a spongy bench, the motor does manage to vibrate ever so slightly..probably made worse from the thinner motor shelf. This noise is barely detectable with a stethoscope on the bottom plinth, but I couldn't detect anything (even with my screwdriver test) on the top plinth. I'm OK with this, and I suspect beefing up the motor shelf, and the table sitting on a proper stand will either eliminate it, or at a minimum, reduce it further.
As far as airborne noise goes, if you hold your ear an inch or so from the pulley, you can hear the hiss of the belt running on the pulley...thats it. You can also feel a slight vibration if you lightly touch the running belt..I'm OK with this as well. The minuscule level of energy here is unlikely to effect my platter.
I'm a happy lad 😀
I said I can see the light at the end of the tunnel earlier. Tallying the remaining tasks has made me realize it's a fairly distant light (finish work,stand, arm,etc.)..but at least I can see it.
-Casey
Edit: I forgot to mention that the motor comes inside with me now.
This thread is turning into some kind of lexicon on TT design, it's freaking huge! There's so much in here I think I'd have to print it and read it over a weekend... maybe we could even reduce it, and other posts, down into a beginners primer...
But seriously, the effort and result you're getting is incredible. You could do all this without too much effort using CNC... but to do it by modifying a drill press to radius the table demonstrates a mind and skill at work, excellent work matey! 😀
We had our entire slate tile roof redone just recently and they also replaced all the lead lining. There was nothing wrong with the lead, but it would be messy by the time it went back on.
So I now have my own body weight, or more, in lead. Coupled with a massive university machine shop, I'm tempted to start my own table... as soon as the workshop guys will let me
But seriously, the effort and result you're getting is incredible. You could do all this without too much effort using CNC... but to do it by modifying a drill press to radius the table demonstrates a mind and skill at work, excellent work matey! 😀
We had our entire slate tile roof redone just recently and they also replaced all the lead lining. There was nothing wrong with the lead, but it would be messy by the time it went back on.
So I now have my own body weight, or more, in lead. Coupled with a massive university machine shop, I'm tempted to start my own table... as soon as the workshop guys will let me
Hello eeka chu,
It certainly has grown into an unwieldy monster. I'm in “negotiations” with my computer geek son to help me put up a web page with a much condensed version of this thread. This won't happen until my turntable version of the “Truman Show” comes to a conclusion though.
Thanx 🙂
[Homer] M..M..M..M.....SEE.N.S-E-E-E-E [/Homer]
Thanx again. I have to constantly remind myself when something comes out less than ideal (the recessed motor shelf for example) of the sub-standard stuff I have to work with. When you can only afford what I can afford, you've got 2 choices..give up..or figure out how to get there from here. Option 2 often takes several intermediate steps.
Careful now. The EU bureau-weenies get the vapors at the mere mention of lead in your solder..imagine the convulsions the knowledge of your stash would cause. You don't want the Pb gestapo visiting in the dark of night
.
Go for it!!
-Casey
This thread is turning into some kind of lexicon on TT design, it's freaking huge! There's so much in here I think I'd have to print it and read it over a weekend... maybe we could even reduce it, and other posts, down into a beginners primer...
It certainly has grown into an unwieldy monster. I'm in “negotiations” with my computer geek son to help me put up a web page with a much condensed version of this thread. This won't happen until my turntable version of the “Truman Show” comes to a conclusion though.
But seriously, the effort and result you're getting is incredible.
Thanx 🙂
You could do all this without too much effort using CNC.
[Homer] M..M..M..M.....SEE.N.S-E-E-E-E [/Homer]
but to do it by modifying a drill press to radius the table demonstrates a mind and skill at work, excellent work matey!
Thanx again. I have to constantly remind myself when something comes out less than ideal (the recessed motor shelf for example) of the sub-standard stuff I have to work with. When you can only afford what I can afford, you've got 2 choices..give up..or figure out how to get there from here. Option 2 often takes several intermediate steps.
We had our entire slate tile roof redone just recently and they also replaced all the lead lining...So I now have my own body weight, or more, in lead.
Careful now. The EU bureau-weenies get the vapors at the mere mention of lead in your solder..imagine the convulsions the knowledge of your stash would cause. You don't want the Pb gestapo visiting in the dark of night

Coupled with a massive university machine shop, I'm tempted to start my own table... as soon as the workshop guys will let me
Go for it!!
-Casey
Casey,
Why not go down the submersible motor route such as used in various water pumps but use oil ?
Are you going to build a Ladegaard arm or something else with air suspension ?
Why not go down the submersible motor route such as used in various water pumps but use oil ?
Are you going to build a Ladegaard arm or something else with air suspension ?
Hi Graeme,
I'm trying to picture it, but unfortunately I'm drawing a blank. Could you explain a little more?
It's for an arm, the Ladegaard at a min, but I'm thinking about something a little more ambitious. I may use it to inflate a bladder to hold a mag suspension table base centered as well.
-Casey
Why not go down the submersible motor route such as used in various water pumps but use oil ?
I'm trying to picture it, but unfortunately I'm drawing a blank. Could you explain a little more?
Are you going to build a Ladegaard arm or something else with air suspension ?
It's for an arm, the Ladegaard at a min, but I'm thinking about something a little more ambitious. I may use it to inflate a bladder to hold a mag suspension table base centered as well.
-Casey
Sorry, I see mentioning the Ladegaard in this thread complicates the question but a number of commentators on the Ladegaard thread raise a viable option in seeking to minimise the TT motor noise when they suggest an aquarium air pump for your arm.
We may be at cross purposes, but in many aquarium pumps, the motor is sealed and is submerged. If you detached one of these pumps and resealed the motor, it could be submerged in an outer casing like your present one, but filled with a light oil which just might be noiseless.
Graeme
We may be at cross purposes, but in many aquarium pumps, the motor is sealed and is submerged. If you detached one of these pumps and resealed the motor, it could be submerged in an outer casing like your present one, but filled with a light oil which just might be noiseless.
Graeme
Thanx for following up Graeme. I get it now.
That's an interesting idea..If my Tesla follies fall flat, I'll give it a try.
-Casey
That's an interesting idea..If my Tesla follies fall flat, I'll give it a try.
-Casey
Graeme Hancock said:Sorry, I see mentioning the Ladegaard in this thread complicates the question but a number of commentators on the Ladegaard thread raise a viable option in seeking to minimise the TT motor noise when they suggest an aquarium air pump for your arm.
We may be at cross purposes, but in many aquarium pumps, the motor is sealed and is submerged. If you detached one of these pumps and resealed the motor, it could be submerged in an outer casing like your present one, but filled with a light oil which just might be noiseless.
Graeme
those are aquarium pumps for water filtration. the ones for the ladegaard are the air pumps for the air bubbles. they should not be submerged 🙂
neutron7-
Thanx for that 😉. I was trying to picture an oil submerged air pump
.
For once, there actually was a reason for my confusion.
-Casey
those are aquarium pumps for water filtration. the ones for the ladegaard are the air pumps for the air bubbles. they should not be submerged
Thanx for that 😉. I was trying to picture an oil submerged air pump

For once, there actually was a reason for my confusion.
-Casey
There are very quiet pumps available out there, but unfortunately I cannot say where, other than that I had a bubble etcher at work many years ago. This thingie had a cast alu membrane pump, appx 6x3" in footprint. This pump was extremely quiet. Unfortunately the etching tub and the pump went out 20 years ago, so I have no clue of make or mark...
BTW - Casey
Congrats with a marvellous project! I have been reading from day one, - and I have a Teres bearing I made, left very lonely in a draw at work......
BTW - Casey
Congrats with a marvellous project! I have been reading from day one, - and I have a Teres bearing I made, left very lonely in a draw at work......
Casey, Neutron, I have confused you.
I am talking about the turntable motor, not the air pump for the ladegaard arm. I'll try again.
If you still have unacceptable motor noise in the turntable motor, a submersible motor may be the answer. I suggested, layman style, detach the pump from the motor, reseal just the motor and submerge the motor in a cylinder filled with a light oil. Oil is less conductive of sound than water and less corrosive.
My reference to aquarium pumps was only an example of where you might find an appropriate submersible motor.
I'm sorry for misleading you.
As for the belt noise, I see in Art Dudley's January 2007 column, Pink Triangle mods for the LP12 including 2 slave pulleys. I assume that with only 3 minimal contact points around the platter, there would be less belt noise. Worth a look.
Keep up the good work, it's inspirational.
Graeme
I am talking about the turntable motor, not the air pump for the ladegaard arm. I'll try again.
If you still have unacceptable motor noise in the turntable motor, a submersible motor may be the answer. I suggested, layman style, detach the pump from the motor, reseal just the motor and submerge the motor in a cylinder filled with a light oil. Oil is less conductive of sound than water and less corrosive.
My reference to aquarium pumps was only an example of where you might find an appropriate submersible motor.
I'm sorry for misleading you.
As for the belt noise, I see in Art Dudley's January 2007 column, Pink Triangle mods for the LP12 including 2 slave pulleys. I assume that with only 3 minimal contact points around the platter, there would be less belt noise. Worth a look.
Keep up the good work, it's inspirational.
Graeme
AuroraB-
I have searched the web, and have come up with a few commercial offerings that I could live with. In the spirit of this project however, I would much prefer DIY if possible. And in the spirit of coming clean, I have an ulterior motive/confession...I am a closet Tesla doofus. The man was a true genius, as well as the victim of his time. Because he had to sell himself to 19th century America, he developed his inner P.T. Barnum. His mix of absolute intellect and showmanship has muddied the waters somewhat..it can be hard to separate the wheat from the chafe. Every since I read this book, I have been looking for a practical application of any of his work..a tribute if you will, and I think I've found one.
Thanx 🙂
Now that is just sad 😉
Graeme-
No problem. I want to hear all ideas, some work out, others not so much. My misunderstanding did get me to thinking of ways to oil damp noise though..so I got something out of it anyway.
This is where the real misunderstanding occurred, and illustrates the shortcomings of an online discussion. Noise, like most things, is relative. The baseline for my comparisons is absolute zero..an unobtainable ideal. To illustrate this, get a large screwdriver, and with any source of background noise eliminated (turning off the shop fluorescents in my case), press the handle firmly in your ear, and while holding your breath, touch the shank to various parts of your turntable.
Warning: If you are susceptible to Audiophilia Nervosous, this could trigger an attack!!
In a recent review of the $65,000 Continuim turntable in Stereophile, the reviewer pointed out that this was the only turntable he had ever reviewed that he couldn't detect noise with his stethoscope.
This should give you some idea of my work. As it stands right now (and I haven't finished tweeking), using the technique described above, and the motor running the 20+ pound platter, I can just barely make out some motor noise in the bottom plinth, and more importantly, nothing in the top. As for airborne noise, the dominant noise (other than my crappy splice that makes a minor * tick *) is the rushing/hissing noise of the thin Mylar rolling over the machined face of the pulley..this you have to place your ear next to the motor/pulley (within an inch or so). Playing with the setup last night, I discovered that the tension change of moving the motor a couple thousandths of an inch with my tensioner was enough to change the volume/pitch of this noise.
As of now ( always subject to change 😉), my noise level is within my tolerance, and will only get better as I refine the setup.
Thank you..I will 🙂
-Casey
There are very quiet pumps available out there, but unfortunately I cannot say where, other than that I had a bubble etcher at work many years ago. This thingie had a cast alu membrane pump, appx 6x3" in footprint. This pump was extremely quiet. Unfortunately the etching tub and the pump went out 20 years ago, so I have no clue of make or mark...
I have searched the web, and have come up with a few commercial offerings that I could live with. In the spirit of this project however, I would much prefer DIY if possible. And in the spirit of coming clean, I have an ulterior motive/confession...I am a closet Tesla doofus. The man was a true genius, as well as the victim of his time. Because he had to sell himself to 19th century America, he developed his inner P.T. Barnum. His mix of absolute intellect and showmanship has muddied the waters somewhat..it can be hard to separate the wheat from the chafe. Every since I read this book, I have been looking for a practical application of any of his work..a tribute if you will, and I think I've found one.
Congrats with a marvellous project!
Thanx 🙂
and I have a Teres bearing I made, left very lonely in a draw at work......
Now that is just sad 😉
Graeme-
I'm sorry for misleading you.
No problem. I want to hear all ideas, some work out, others not so much. My misunderstanding did get me to thinking of ways to oil damp noise though..so I got something out of it anyway.
If you still have unacceptable motor noise in the turntable motor, a submersible motor may be the answer.....As for the belt noise...
This is where the real misunderstanding occurred, and illustrates the shortcomings of an online discussion. Noise, like most things, is relative. The baseline for my comparisons is absolute zero..an unobtainable ideal. To illustrate this, get a large screwdriver, and with any source of background noise eliminated (turning off the shop fluorescents in my case), press the handle firmly in your ear, and while holding your breath, touch the shank to various parts of your turntable.
Warning: If you are susceptible to Audiophilia Nervosous, this could trigger an attack!!
In a recent review of the $65,000 Continuim turntable in Stereophile, the reviewer pointed out that this was the only turntable he had ever reviewed that he couldn't detect noise with his stethoscope.
This should give you some idea of my work. As it stands right now (and I haven't finished tweeking), using the technique described above, and the motor running the 20+ pound platter, I can just barely make out some motor noise in the bottom plinth, and more importantly, nothing in the top. As for airborne noise, the dominant noise (other than my crappy splice that makes a minor * tick *) is the rushing/hissing noise of the thin Mylar rolling over the machined face of the pulley..this you have to place your ear next to the motor/pulley (within an inch or so). Playing with the setup last night, I discovered that the tension change of moving the motor a couple thousandths of an inch with my tensioner was enough to change the volume/pitch of this noise.
As of now ( always subject to change 😉), my noise level is within my tolerance, and will only get better as I refine the setup.
Keep up the good work, it's inspirational.
Thank you..I will 🙂
-Casey
Graeme Hancock said:Casey, Neutron, I have confused you.
I am talking about the turntable motor, not the air pump for the ladegaard arm. I'll try again.
If you still have unacceptable motor noise in the turntable motor, a submersible motor may be the answer. I suggested, layman style, detach the pump from the motor, reseal just the motor and submerge the motor in a cylinder filled with a light oil. Oil is less conductive of sound than water and less corrosive.
My reference to aquarium pumps was only an example of where you might find an appropriate submersible motor.
I'm sorry for misleading you.
As for the belt noise, I see in Art Dudley's January 2007 column, Pink Triangle mods for the LP12 including 2 slave pulleys. I assume that with only 3 minimal contact points around the platter, there would be less belt noise. Worth a look.
Keep up the good work, it's inspirational.
Graeme
OH! i see what you mean now. yes the reference to "aquarium pump" and Ladegaard did indeed confuse me 🙂
Re-reading my above post, I wasn't as clear as I wanted to be.
I forgot to clearly state what I believed that shortcoming to be..our individual references. We each have our own point of reference, and unless we can figure out a way to share them, the meaning can get lost. What I wrote after this was an attempt to illustrate mine. It could be read that I was comparing my table to the Continuim, I wasn't ( I couldn't without having access to one..most unlikely), rather, I was trying to illustrate how difficult it is to achieve the noise levels I've been aiming for.
On the noise front, I believe I know why I've experienced a slight increase in motor vibration (from undetectable to barely detectable). I was first suspicious when I re-mounted the motor on the repaired mount, and adjusted it on my “kinda horn” jig. It seemed at the time that the side-to-side movement (shimmy) of the motor was greater than before. This didn't make sense, so I wrote it off, and proceeded to reassemble the motor. Note to self..never write anything off. I believe that the motor hanging at a slight angle from the broken glue joints on the mount, and the subsequent multiple deep freeze/thaw sequence it went through in this state, re-shaped the Sorbothane coupling in the motor coupler slightly, knocking out the alignment. I'm really not worried about the increased vibration per se (the end effect is barely detectable), but I am concerned with the stress this presents the motor. The way I see it, I have two options..see if the problem corrects itself by running it with the repaired mount (see if the Sorbothane returns to it's original shape), or replace the coupler. Having spent many years repairing gear that wasn't engineered for easy repair (consumer gear), I made sure that breaking down my motor was easy, so it's no big deal getting back in to replace the coupler if needed. If the problem doesn't correct itself by the weekend, I'll replace it.
-Casey
This is where the real misunderstanding occurred, and illustrates the shortcomings of an online discussion.
I forgot to clearly state what I believed that shortcoming to be..our individual references. We each have our own point of reference, and unless we can figure out a way to share them, the meaning can get lost. What I wrote after this was an attempt to illustrate mine. It could be read that I was comparing my table to the Continuim, I wasn't ( I couldn't without having access to one..most unlikely), rather, I was trying to illustrate how difficult it is to achieve the noise levels I've been aiming for.
On the noise front, I believe I know why I've experienced a slight increase in motor vibration (from undetectable to barely detectable). I was first suspicious when I re-mounted the motor on the repaired mount, and adjusted it on my “kinda horn” jig. It seemed at the time that the side-to-side movement (shimmy) of the motor was greater than before. This didn't make sense, so I wrote it off, and proceeded to reassemble the motor. Note to self..never write anything off. I believe that the motor hanging at a slight angle from the broken glue joints on the mount, and the subsequent multiple deep freeze/thaw sequence it went through in this state, re-shaped the Sorbothane coupling in the motor coupler slightly, knocking out the alignment. I'm really not worried about the increased vibration per se (the end effect is barely detectable), but I am concerned with the stress this presents the motor. The way I see it, I have two options..see if the problem corrects itself by running it with the repaired mount (see if the Sorbothane returns to it's original shape), or replace the coupler. Having spent many years repairing gear that wasn't engineered for easy repair (consumer gear), I made sure that breaking down my motor was easy, so it's no big deal getting back in to replace the coupler if needed. If the problem doesn't correct itself by the weekend, I'll replace it.
-Casey
I had intended to hold off on any air pump work until the rest of the table was done, but not knowing if it will work or not has been nagging at me (my implementation, not Tesla's turbine which most definitely works). Since I believe I have everything I need, and it's not a big project, I've decided to bounce back and forth as the mood strikes me. The plan is to make the housing out of Corion and/or Lexan I have laying around, and use Cd-Roms as discs, other than the spindle and motor assy., I should be able to throw together a “proof of concept” pump in a day or so of work, which no doubt will be strung out. I'll simply draft the design actual size, and use the drafts as templates to cut out the pieces with my rotory tool and router. If the first attempt works, or is very close, cool...I'll invest the effort to fine tune it. If not, then I will know it's been a fool's errand, and look at a more conventional air source.
The biggest unknown for me has been the motor to drive it. It needs to be quiet, spin somewhere between 1500-5000 rpm, and have enough oomph to work against the air pressure I'm after. Digging through my junk, I came across a pile of Pabst muffin fans I had pulled from the same motor controller I got the aluminum for my bottom plinth from...
Other than the fact it had blades hanging off it, and it was integral to the fan housing, the motor was pretty close to ideal..120V, 3000rpm, 20 Watts, and running you hear the fan, not the motor. Hmmm I sez. I decided to see if I could pull a usable motor out of it's fan prison. I broke off the blades, trued up the hub with my press mounted Dremel/file, cut out the support arms, and cleaned it up (about an hours work total)...
Beauty. The motor is running in the picture (obviously) just sitting on rubber discs. It's stone quiet, and if you look at the edges of where I cut the supports you'll notice that there isn't any vibration to blur the flash less picture. I plan to run a flat belt around the finished portion of the hub to drive the pump.
Thats one less thing for me to agonize over 😀
-Casey
The biggest unknown for me has been the motor to drive it. It needs to be quiet, spin somewhere between 1500-5000 rpm, and have enough oomph to work against the air pressure I'm after. Digging through my junk, I came across a pile of Pabst muffin fans I had pulled from the same motor controller I got the aluminum for my bottom plinth from...
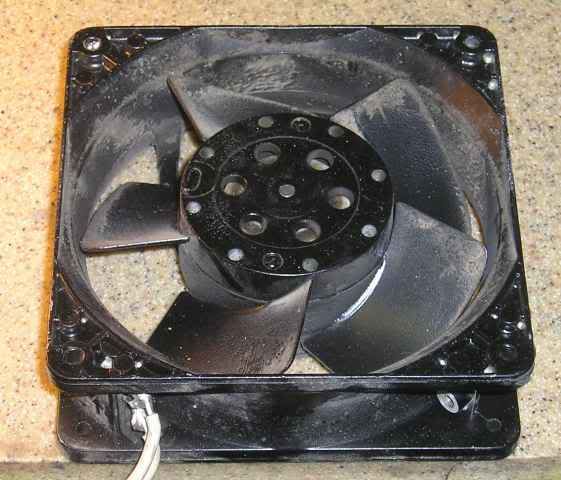
Other than the fact it had blades hanging off it, and it was integral to the fan housing, the motor was pretty close to ideal..120V, 3000rpm, 20 Watts, and running you hear the fan, not the motor. Hmmm I sez. I decided to see if I could pull a usable motor out of it's fan prison. I broke off the blades, trued up the hub with my press mounted Dremel/file, cut out the support arms, and cleaned it up (about an hours work total)...
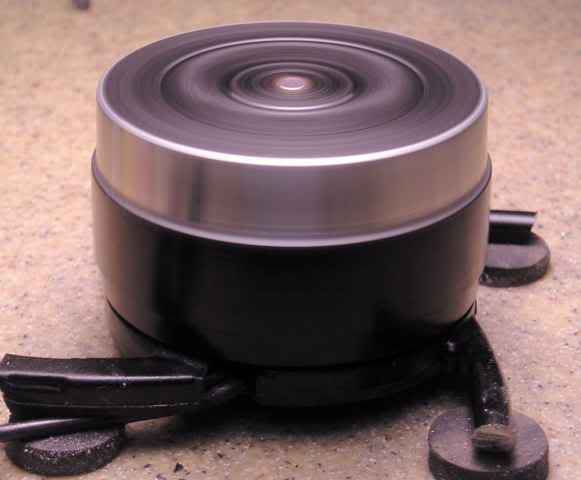
Beauty. The motor is running in the picture (obviously) just sitting on rubber discs. It's stone quiet, and if you look at the edges of where I cut the supports you'll notice that there isn't any vibration to blur the flash less picture. I plan to run a flat belt around the finished portion of the hub to drive the pump.
Thats one less thing for me to agonize over 😀
-Casey
From Graeme
This is very interesting... A machinist friend and I postulated this a couple of years ago as a way of minimizing bearing wear and noise. Then, I saw an article on the Funk Firm Vector table and my reaction was: 'too late, as usual'.
If I read Graeme's post correctly, this is a good enough idea that someone is adding the 60deg idler shives to a Linn. Pretty inspiring.
This adds new dimention to my project of a new skeleton frame for my ancient, obscure Unity Rotary Platform (25lb of beautifully polished brass on a slab of low-grade plywood
). I was wondering whether to incorporate the idler idea. Sounds more and more likely.
Well, I'm off to search out info on the Pink Triangle mods.
Jess
As for the belt noise, I see in Art Dudley's January 2007 column, Pink Triangle mods for the LP12 including 2 slave pulleys. I assume that with only 3 minimal contact points around the platter, there would be less belt noise. Worth a look.
This is very interesting... A machinist friend and I postulated this a couple of years ago as a way of minimizing bearing wear and noise. Then, I saw an article on the Funk Firm Vector table and my reaction was: 'too late, as usual'.

If I read Graeme's post correctly, this is a good enough idea that someone is adding the 60deg idler shives to a Linn. Pretty inspiring.
This adds new dimention to my project of a new skeleton frame for my ancient, obscure Unity Rotary Platform (25lb of beautifully polished brass on a slab of low-grade plywood

Well, I'm off to search out info on the Pink Triangle mods.

Jess
Casey,
I dont think anyone misunderstood your reference to the Continuim, besides, it's now passe. Your sights now need to be set on the announced, but as yet unseen Goldmund, a steal at a paltry $300,000 !
Graeme
I dont think anyone misunderstood your reference to the Continuim, besides, it's now passe. Your sights now need to be set on the announced, but as yet unseen Goldmund, a steal at a paltry $300,000 !
Graeme
I plan to run a flat belt around the finished portion of the hub to drive the pump.
Hey Casey - I hate to be a party-pooper, but you should be careful about expecting any lifespan from these muffin fan motors, especially with any side-thrust load on them. Just driving their fan blades they will wear out in about a year of continuous duty.
I work with computers (nearly 30 years now) and these things are the most-replaced component (other than keyboards smashed by frustrated users) on computers today.
The upside, however, is that they are plentiful and cheap, so make several!
Jess
Hey Jess-
All of this is true...with garden variety BLDC fans. I myself have cursed the fans in my PC more often than I can count. These, however, are a completely different animal. They are German made synchronous ac motors with bearings to die for...and very expensive. They were designed for industrial duty in a nasty environment. These particular units were pulled from an 80's-90's vintage industrial multi KW 3-phase VFD that probably cost more than your house 😀. When I pulled them, they had a thick layer of nasties on them, and all appeared to be original...everyone still works quietly.
I just timed the spin down to get a handle on the bearing condition...It spun for 1min, 39 sec. Before coming to a full stop after unplugging it
I think it will handle what I'm going to ask from it, and if it does die on me, I've got 5 more to try 😉
-Casey
Hey Casey - I hate to be a party-pooper, but you should be careful about expecting any lifespan from these muffin fan motors, especially with any side-thrust load on them...I work with computers (nearly 30 years now) and these things are the most-replaced component (other than keyboards smashed by frustrated users) on computers today.
All of this is true...with garden variety BLDC fans. I myself have cursed the fans in my PC more often than I can count. These, however, are a completely different animal. They are German made synchronous ac motors with bearings to die for...and very expensive. They were designed for industrial duty in a nasty environment. These particular units were pulled from an 80's-90's vintage industrial multi KW 3-phase VFD that probably cost more than your house 😀. When I pulled them, they had a thick layer of nasties on them, and all appeared to be original...everyone still works quietly.
I just timed the spin down to get a handle on the bearing condition...It spun for 1min, 39 sec. Before coming to a full stop after unplugging it

I think it will handle what I'm going to ask from it, and if it does die on me, I've got 5 more to try 😉
-Casey
- Status
- Not open for further replies.
- Home
- Source & Line
- Analogue Source
- Corian Turntable Fun