The limit on compression driver size is mainly its being an edge-driven dome, right? Why don't they turn it around and put a conventional motor behind the dome? Wouldn't that allow for gigantic compression drivers? Of course you'd have to have some way of having the dome shape on front but a nice strong coupling to the VC on the back, but that shouldn't be too big of deal. Would there be no merit to a driver like that?
Conventional dome shape diaphragm size is compromise between high frequency breakup and output potential, a 4 inch diaphragm diameter is pushing the limit of acceptable performance.
A number of driver manufacturers use annular ring diaphragms rather than domed diaphragms, making for larger diaphragm area with less distance across, this might be close to what your idea is.
A number of driver manufacturers use annular ring diaphragms rather than domed diaphragms, making for larger diaphragm area with less distance across, this might be close to what your idea is.
I was thinking more for use down to midbass range as opposed to the usual ways of horn-loading a cone driver for that purpose.
I was thinking more for use down to midbass range as opposed to the usual ways of horn-loading a cone driver for that purpose.
A horn loaded cone IS a compression driver.
Offhand, I can think of about a dozen "usual" ways of horn-loading a cone driver.I was thinking more for use down to midbass range as opposed to the usual ways of horn-loading a cone driver for that purpose.
Perhaps you could draw a picture of what you are proposing.
http://www.troelsgravesen.dk/Jenzen-D/DiamondStudy.pdf
but some think Be may be better
but some think Be may be better
http://www.google.com/url?sa=t&rct=...8IH4DA&usg=AFQjCNHsf41FL4FZW9lvMqJtDgSdBhXYlAEven CVD diamond cannot top beryllium. CVD diamond’s speed of sound is very high but its mass density is almost twice that of Be and the CVD diamond is very
brittle.
The limit on compression driver size is mainly its being an edge-driven dome, right? Why don't they turn it around and put a conventional motor behind the dome? Wouldn't that allow for gigantic compression drivers? Of course you'd have to have some way of having the dome shape on front but a nice strong coupling to the VC on the back, but that shouldn't be too big of deal. Would there be no merit to a driver like that?
This is just off the top of my head, so I may have missed a couple things.
I believe there are three things that we battle when designing a compression driver. The first challenge is maximum output. Maximum output will generally be dictated by displacement, as long as you have sufficient power available and your voice coil doesn't overheat.
So the obvious solution would be to increase xmax, cone size, or both.
But that leads us to the *second* challenge. Which is that your upper frequency limit will be dictated by mass. (read this: http://volvotreter.de/downloads/Edgar-Show-Horn.pdf)
So we see that challenge one and challenge two are at odds with each other. When you try to increase output by raising displacement, you end up limiting high frequencies. And this isn't just in one dimension, it's in two. Raising xmax raises mass because the suspension gets heavier. Raising the cone area by making the diaphragm larger ALSO raises mass. (This is why TAD uses beryllium in their diaphragms, you can raise the high frequency limit by lowering the mass.)
The third challenge we face when engineering a compression driver is getting the entire surface of the diaphragm 'in phase'. That's a REALLY complex topic. Here's a pic of a compression driver that was cut in half, showing how the phase plug equalizes the pathlengths:
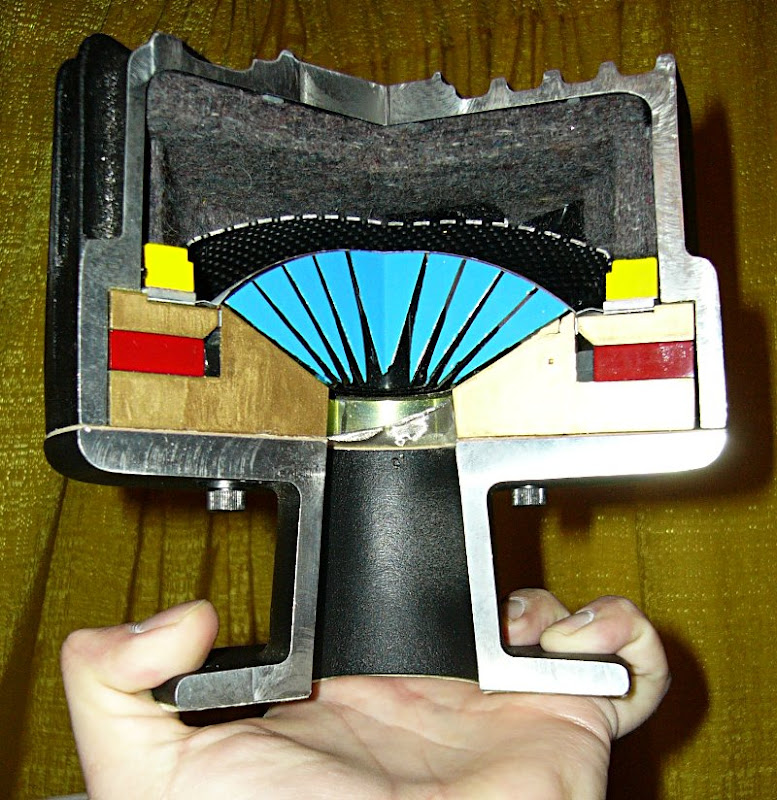
Long story short:
We have three competing criteria, and they're at odds with each other. If you optimize for one criteria, it's often at the expense of another. And that's why horns work best when each driver covers a narrow bandwidth. It's not possible to have one driver cover a wide range in a horn.
Well, I guess you could, but the efficiency would be very very very low.
(Back loaded horns can have a wide bandwidth with a single driver, but that's because 80% of their bandwidth isn't horn loaded; only the lowest octave is.)
I was not talking about trying to get good HF performance from a large diaphragm, I was talking BIG and low frequencies. I guess maybe the actual question is whether there would be any benefit to the sort of thing in my sketch rather than just having a cone crudely mated to a large horn throat, or through a slot/hole.
Your idea is kind of halfway like the Community M4, which worked OK for a decade kind of halfway in the middle of the audio spectrum, 250-2500.Like this (relative scales and angles in this sketch are not determined by logic, just by the cross section images I'm mashing together).
It was not so good at either end of that decade..
The added mass required for a good connection to a dome shaped diaphragm as in your idea would probably preclude it's use for midrange or HF, and as it sits "normal" 10" drivers can beat the M4 when horn loaded in the low range, and don't require such complicated phase plugs for use from 100-1000 Hz.
When pushing the limits of reaching a decade of operation for "normal" cone drivers, phase plugs that conform to the speaker can be employed.
Attachments
I was not talking about trying to get good HF performance from a large diaphragm, I was talking BIG and low frequencies. I guess maybe the actual question is whether there would be any benefit to the sort of thing in my sketch rather than just having a cone crudely mated to a large horn throat, or through a slot/hole.
Ah -
In that case, my original comment applies then.
A front loaded horn with a cone at it's apex IS a compression driver.
You can take a front loaded horn like the labhorn, and every single element that exists in that basshorn also exists in front loaded horn with a compression driver at it's apex. And I think that's the reason you don't see a lot of compression drivers with diaphragms larger than 10cm. Once the dimensions are getting that large, the frequencies are long enough that you don't need a hyper-accurate phase plug. (Like the phase plug in that Tad that I posted a second ago.)
Once we're talking about wavelengths that are eight feet long being radiated by a cone that's half a foot long, the wavelengths are so long the phase plug no longer has to be perfect.
But it's a whole 'nother story when the wavelengths are an inch long and the radiator is four inches in diameter.
Hmm, yep, that's exactly what I meant. how 'bout that. 😀
Whatyall talkin' 'bout?
They do make mid and bass compression drivers. Not the most practical things mind you, and just slightly out of most persons range. 😀
http://www.aleacoustic.com/
They do make mid and bass compression drivers. Not the most practical things mind you, and just slightly out of most persons range. 😀
http://www.aleacoustic.com/
By now you've seen the dome in a compression driver is already turned around.Why don't they turn it around and put a conventional motor behind the dome?
Then you want the Ale drivers son! Hope your piggy bank is overflowing 'cause the last time I looked the bass comp drivers were what, about $30,000 a pop? Kinda makes a 15" woofer look pretty good about now. You can always put one in a tapped horn and get more than you'll probably need. 🙂I was talking BIG and low frequencies.
Keep in mind how big a regular front or rear horn has to be to get down low and you understand why these are not more popular. Have a look at the Ale site horns.
I meant turn the motor/VC around, but you've seen that by now 😉.By now you've seen the dome in a compression driver is already turned around.
Your drawing of the 'cone' in post 7 has the coil on the same side as a standard comp driver, but you already knew that. 😉
What am I missing here buddy?
Have you ordered the Goto drivers yet? 😀
What am I missing here buddy?
Have you ordered the Goto drivers yet? 😀
There might be some people that disagree with me, but if you're going to the trouble of making a proper phase plug, make a radial one.
http://www.nutshellhifi.com/library/Henricksen_1978_Tangerine_PP.pdf
I built some 11 slit radial phase plugs for some Faital M5N12-80 following the above AES paper from Henricksen. In a 140Hz tractrix horn they would do 180Hz to 6KHz.
http://www.nutshellhifi.com/library/Henricksen_1978_Tangerine_PP.pdf
I built some 11 slit radial phase plugs for some Faital M5N12-80 following the above AES paper from Henricksen. In a 140Hz tractrix horn they would do 180Hz to 6KHz.
I guess you're reading the drawing wrong? My drawing is, it turned out, trying to show the same thing that the JBL CMCD drivers are. The green line is the cone+VC. Here it is next to the compression driver drawing it was sloppily made from:Your drawing of the 'cone' in post 7 has the coil on the same side as a standard comp driver, but you already knew that. 😉
What am I missing here buddy?
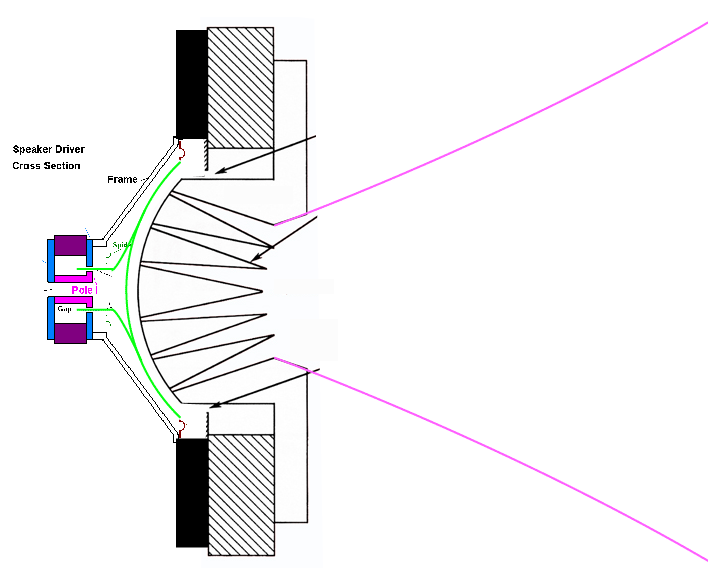

Yeah... I think I'll pass on those, but there's no CMCD stuff in my cart either. I was just wonderin'.Have you ordered the Goto drivers yet? 😀
Last edited:
- Status
- Not open for further replies.
- Home
- Loudspeakers
- Multi-Way
- Compression Driver Engineering Question