I have a final project due in the next while for my ceramics class and figured I could build a swanky set of speakers.
I haven't put much though to the particulars of the design as I only though about this yesterday. All I have so far is a general idea of the shape I want.
Essentially though, I'm curious to know if clay would function as an adequate enclosure. Specifically for a small set of horn loaded speakers.
I don't want to make a simple sealed or ported enclosure as that is much to simple for what i am required to do, and imo, would not look anywhere near as interesting.
I've attached a quick&dirty sketchup model of my basic idea.
As far as drivers are concerned, im thinking along the lines of
Tang Band W3-881SJ 3" Shielded Neodymium Driver
or
HiVi B3N 3" Aluminum Driver Round Frame
largely because I've little interest in spending large amounts of money on this.
They would likely be paired with the DTA-2 t-amp for which I would also build a fancy little box for.
Dayton Audio DTA-2 Class T Digital Audio Amplifier Module
Lastly, this is one of the rare instances where I would place form as a priority over function (I have plenty of fabulous sounding and monolithic speakers already). Having both would certainly not hurt though.
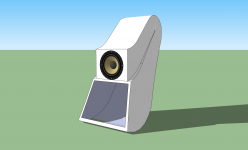
I haven't put much though to the particulars of the design as I only though about this yesterday. All I have so far is a general idea of the shape I want.
Essentially though, I'm curious to know if clay would function as an adequate enclosure. Specifically for a small set of horn loaded speakers.
I don't want to make a simple sealed or ported enclosure as that is much to simple for what i am required to do, and imo, would not look anywhere near as interesting.
I've attached a quick&dirty sketchup model of my basic idea.
As far as drivers are concerned, im thinking along the lines of
Tang Band W3-881SJ 3" Shielded Neodymium Driver
or
HiVi B3N 3" Aluminum Driver Round Frame
largely because I've little interest in spending large amounts of money on this.
They would likely be paired with the DTA-2 t-amp for which I would also build a fancy little box for.
Dayton Audio DTA-2 Class T Digital Audio Amplifier Module
Lastly, this is one of the rare instances where I would place form as a priority over function (I have plenty of fabulous sounding and monolithic speakers already). Having both would certainly not hurt though.
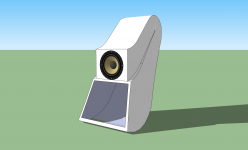
I liked the first part of your post , till you named the speakers & amps 
maybe my expectations are too high . Not sophisticated ... but a nice 8" and a tweeter 😕 Oh sorry !!!!
This is FR Forum !!

maybe my expectations are too high . Not sophisticated ... but a nice 8" and a tweeter 😕 Oh sorry !!!!

Ivan I think it's a great idea. Fired clay would be good and strong. Would you place any kind of reinforcing mat within the clay for extra rigidity, and how would you mount the driver to it? Is it called porcelain once it's fired?
I have thinked of this before , and Cal had reminded me of the oven . I knew the limitations are the measures of the oven , and also the need for some structure for not making it fluffy..Oh ..Cal got it !! A segmented structure ,made of two or three pieces , with the junctions well closed. 🙂
There are varying qualities of clay, from Stoneware (which I have a bunch of atm) to porcelain. The difference between them is largely in how the particles arrange themselves once the clay is fired. Stoneware turns more to rock, whereas porcelain turns to glass.
I'm aiming for bookshelf sized speakers so the rigidity of the clay itself would likely be enough that it wouldn't need reinforcements. If I had to though, it would be very easy to implement.
I haven't worked the details of mounting the driver, but im likely to build it in such a way that I can epoxy a piece of wood to which the driver would be attached.
The kilns(giant high temp oven) at the university are reasonably large, so I dont think that I need to make it in segments.
I'm aiming for bookshelf sized speakers so the rigidity of the clay itself would likely be enough that it wouldn't need reinforcements. If I had to though, it would be very easy to implement.
I haven't worked the details of mounting the driver, but im likely to build it in such a way that I can epoxy a piece of wood to which the driver would be attached.
The kilns(giant high temp oven) at the university are reasonably large, so I dont think that I need to make it in segments.
some terra&tubes from Serbia 🙂
An externally hosted image should be here but it was not working when we last tested it.
An externally hosted image should be here but it was not working when we last tested it.
Why not?
Working enclosures have been made from more than the 'ever popular' particle board and MDF. Cast aluminum (RS Minimus?), plastic (Gedlee), ABS/PVC (Linkwitz).....
Be sure to post the results of your creative ideas here!
(I'm thinkin' His Master's Voice doggie with open mouth, howlin'...)
😀😀
Working enclosures have been made from more than the 'ever popular' particle board and MDF. Cast aluminum (RS Minimus?), plastic (Gedlee), ABS/PVC (Linkwitz).....
Be sure to post the results of your creative ideas here!
(I'm thinkin' His Master's Voice doggie with open mouth, howlin'...)
😀😀
Clay is scary 😱
In those pics I recognize a stove or a fire or, in the first one , a fish in a meta-baroque manner 😕

One is omni ...but the trumpet ?
😀
Same for the fish'n'trumpet : where's the speaker
😱
I was to say that if clay works ,and it should ,it could be made in full scale , maybe some honeycomb pattern to help .
In those pics I recognize a stove or a fire or, in the first one , a fish in a meta-baroque manner 😕

One is omni ...but the trumpet ?
😀
Same for the fish'n'trumpet : where's the speaker
😱
I was to say that if clay works ,and it should ,it could be made in full scale , maybe some honeycomb pattern to help .
Last edited:
While not an entire enclosure, Wharfedale Airedale speakers had clay tiles placed inside the cabinet against the sidewalls, as part of the design.
Ivan, Corian or Himacs would be great for that design. You can get that shape thermoformed in 12 or 19mm white. Its very dense, a v good material for speaker builds and far superior to mdf.
how about 36-24-36 with built in beer holder??
use modeling clay and fiberglass and leave it unfired??
use modeling clay and fiberglass and leave it unfired??
Clay pots are an old favorite "found cabinet" for FR builds.
There is another thread here with custom thrown pots, likely some tips there -- they were being done by a pro.
If you can get a shape & actually build it, you will be fine with the clay.
dave
There is another thread here with custom thrown pots, likely some tips there -- they were being done by a pro.
If you can get a shape & actually build it, you will be fine with the clay.
dave
Have you considered using sculpture cement? Some simple shapes like a sphere with tapered tube can be cast with a basketball interior covered in household plastic wrap, and a plywood side profile template to rotate around the rough exterior cement. You can use chicken wire, or old copper wire to build a skeleton frame for the concrete. I no longer try to drill+tap+screw the speaker into the concrete, but just silicone adhesive midrange and tweeter drivers.
The cement that I use in this process is white portland cement. The cement is mixed with white silica sand in a ratio of about 1 part sand to 2 parts cement, and a small amount of micro fibers Fibermesh® 150, ¾ " long polypropylene multifilament fibers. Ratio of latex 1 : water 4 is added to this mixture to achieve the consistency of clay. The use of a latex additive and fibers allows for better adhesion to dried cement, helps to prevent cracking, and offsets the lack of aggregate or sand. I use a metal armature when starting my sculptures, similar to what would be used in clay or plaster. I wrap chicken wire or scrap copper wire together forming a skeleton to support the cement. Using a variety of tools which include various rasps, dremel tool bits, sand paper and sometimes even a grinder I then can begin the process of working at the cement to smooth out, correct errors and make marks that would be indicative to an original sculpture. The moisture content should remain high in the sculptures to keep the material from becoming so hard it becomes difficult to work with. This means that when a sculpture is started, it needs to be completed in a timely fashion, and wrapped in plastic when not being worked on. When the cement has time to slowly cure, and the sculpture is finished, it is then sealed with a stone sealer, or concrete paint. Clear wax can be used to help buff the finish to a low luster sheen.
The cement that I use in this process is white portland cement. The cement is mixed with white silica sand in a ratio of about 1 part sand to 2 parts cement, and a small amount of micro fibers Fibermesh® 150, ¾ " long polypropylene multifilament fibers. Ratio of latex 1 : water 4 is added to this mixture to achieve the consistency of clay. The use of a latex additive and fibers allows for better adhesion to dried cement, helps to prevent cracking, and offsets the lack of aggregate or sand. I use a metal armature when starting my sculptures, similar to what would be used in clay or plaster. I wrap chicken wire or scrap copper wire together forming a skeleton to support the cement. Using a variety of tools which include various rasps, dremel tool bits, sand paper and sometimes even a grinder I then can begin the process of working at the cement to smooth out, correct errors and make marks that would be indicative to an original sculpture. The moisture content should remain high in the sculptures to keep the material from becoming so hard it becomes difficult to work with. This means that when a sculpture is started, it needs to be completed in a timely fashion, and wrapped in plastic when not being worked on. When the cement has time to slowly cure, and the sculpture is finished, it is then sealed with a stone sealer, or concrete paint. Clear wax can be used to help buff the finish to a low luster sheen.
Im after clay specifically as this will be an art project for my ceramics class.
While more exotic materials could be nicer, I plan on spending as little money as possible.
Working with complex shapes is certainly not a problem though. One of the nice things about clay is it can take just about any shape.
I could, in theory, make just about any shape imaginable. For the moment though, I'm thinking I would like to pursue a shape similar to a nautilus shell. Having the two speakers mirror each other.
While this is still just a sketch, I'm not sure if the driver should be further forward? or if there are any other particulars I should be aware of.
While more exotic materials could be nicer, I plan on spending as little money as possible.
Working with complex shapes is certainly not a problem though. One of the nice things about clay is it can take just about any shape.
I could, in theory, make just about any shape imaginable. For the moment though, I'm thinking I would like to pursue a shape similar to a nautilus shell. Having the two speakers mirror each other.
While this is still just a sketch, I'm not sure if the driver should be further forward? or if there are any other particulars I should be aware of.
Attachments
I was going to mention in an earlier post that the earlisest sketch reminded me of these.
The Dalek -- Fostex FE166e Horn
dave

The Dalek -- Fostex FE166e Horn
dave
Ivan,
I'm assuming you are planning on hand building these (as opposed to throwing sections on the wheel)? I would be a little concerned about ringing of the large horn mouth. If you are throwing them in sections you are restricted to using clay that is plastic enough to be used on the wheel. Hand building them would certainly open up the options as far as clay mixtures go. I would recommend an open clay body as possible. In other words LOTS of grog, and possibly even a little bit of organic material, such as cornmeal. The organic material will slightly weaken the fired product, but it will really reduce the chance of the horn mouth acting as a bell.
I think you'll find most commerically mixed clays will have some ringing after they are fired.
Maybe someone fluent in Hornresp can help you out with dimensions.
It's an exciting project, keep us posted.
Joe
I'm assuming you are planning on hand building these (as opposed to throwing sections on the wheel)? I would be a little concerned about ringing of the large horn mouth. If you are throwing them in sections you are restricted to using clay that is plastic enough to be used on the wheel. Hand building them would certainly open up the options as far as clay mixtures go. I would recommend an open clay body as possible. In other words LOTS of grog, and possibly even a little bit of organic material, such as cornmeal. The organic material will slightly weaken the fired product, but it will really reduce the chance of the horn mouth acting as a bell.
I think you'll find most commerically mixed clays will have some ringing after they are fired.
Maybe someone fluent in Hornresp can help you out with dimensions.
It's an exciting project, keep us posted.
Joe
I'm after a more angular look, so yes, it will be hand built. For those familiar with clay, I plan on having a mold of the interior space and wrapping large slabs of clay to cover 3/4. Once that's, take the mold out and seal it closed. Because its slab built, I want dont want the clay to be too soft, otherwise it sags and makes it impossible to get smooth surfaces and clean corners, which are two characteristics I'm after.
@Dave, its quite possible my subconscious was influencing me in my design ideas, as those are striking looking speakers. (I prefer the monolithic look of my Saburo's though 😉)
After contemplating some more, I'm leaning once again towards my initial design idea. This just makes me realize how terribly indecisive I can be at times.
Having some feedback from someone who knows Hornresp would be fantastic. I imagine I would need more specific information though, like dimensions, driver model and the boatload of statistics that go with it.
@Dave, its quite possible my subconscious was influencing me in my design ideas, as those are striking looking speakers. (I prefer the monolithic look of my Saburo's though 😉)
After contemplating some more, I'm leaning once again towards my initial design idea. This just makes me realize how terribly indecisive I can be at times.
Having some feedback from someone who knows Hornresp would be fantastic. I imagine I would need more specific information though, like dimensions, driver model and the boatload of statistics that go with it.
Ivan, Corian or Himacs would be great for that design. You can get that shape thermoformed in 12 or 19mm white. Its very dense, a v good material for speaker builds and far superior to mdf.
Be aware that not all acrylic or polyester solid surface materials are created equal, or have "ideal" thermo-forming characteristics. The chemistry of specific binder resins and the quantity and size of aggregates/fillers used to achieve some of the gorgeous textures and 3D effects seriously affect the ability to safely bend to more than very large radii - more so with thicker stocks. Some brands with even very fine particles fracture very easily.
Material and fabrication costs aside, as to being a good material for speaker builds (of any design), or preferable to MDF, let's agree that we're not all on the same wavelength.
- Status
- Not open for further replies.
- Home
- Loudspeakers
- Full Range
- Clay as speaker enclosure?