And the cars are a little... massive for many I have found. (so heavy and gas more needed and the low price of gas encourage that, though progress were made since on the motors side, hybridation, electric for those who can)Yes, most live too far away, and public transportation is poor except in a larger city.
For a comparison.
A pair of Hifi2000 monblock chassis would cost me 824.50€, including VAT and shipping. About NZD1500 at todays exchange rate.
Obviously they are a much nicer chassis than what I can make and include heatsinks but still. More than 5x the price of what I made myself.
If I had the budget I would gladly fork out for the gorgeous Italian metal. Maybe when I am a grown up.....
Right now I am 38, 4 years into a mortage with 2 kids. So I either do it the lowest cost way possible or I can't really do it.
My entire DIY budget for a year is $520. My wife and I allow ourselves $10 per week in pocket money.
I use a lot of scrap components in my builds for this reason: transformers, heatsinks, the odd scrap chassis etc.
Recently I have been on a bit of an organisation binge trying to tidy up my work space.
I came up with this brilliant method of making containers for sorting my tools:
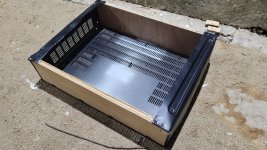
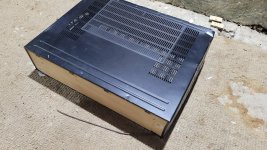
An almost zero cost tool container from the lid of a salvaged AV receiver, 2 bits of scrap would and some nails.
The receiver cost me $1 and its power transformer and heatsink will either find their way into a project or be sold off 2nd hand when I get around to it.
A pair of Hifi2000 monblock chassis would cost me 824.50€, including VAT and shipping. About NZD1500 at todays exchange rate.
Obviously they are a much nicer chassis than what I can make and include heatsinks but still. More than 5x the price of what I made myself.
If I had the budget I would gladly fork out for the gorgeous Italian metal. Maybe when I am a grown up.....
Right now I am 38, 4 years into a mortage with 2 kids. So I either do it the lowest cost way possible or I can't really do it.
My entire DIY budget for a year is $520. My wife and I allow ourselves $10 per week in pocket money.
I use a lot of scrap components in my builds for this reason: transformers, heatsinks, the odd scrap chassis etc.
Recently I have been on a bit of an organisation binge trying to tidy up my work space.
I came up with this brilliant method of making containers for sorting my tools:
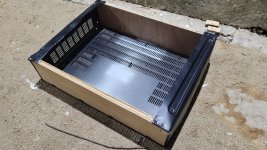
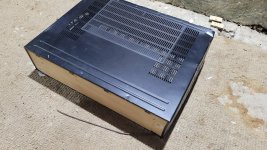
An almost zero cost tool container from the lid of a salvaged AV receiver, 2 bits of scrap would and some nails.
The receiver cost me $1 and its power transformer and heatsink will either find their way into a project or be sold off 2nd hand when I get around to it.
And this is an almost zero cost amplifier build for my basement. Deliberately ugly as sin for my amusment:
-Chassis from some broken old yamaha I got for free.
-Power transformer and heatsink from some broken AV receiver or another, virtually free.
-Electronics salvaged from some of my first projects getting into the hobby
-salvaged speaker jacks, relays etc.
Assuming everything else was past its service life and therefore free. The most expensive part was the Ali express bluetooth board.
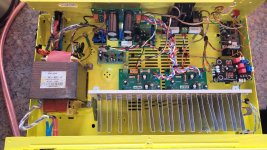
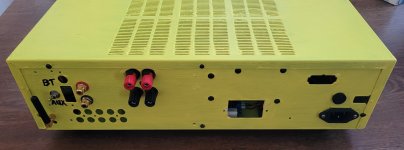
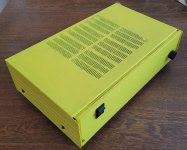
Sweet basement listening while I make stuff:
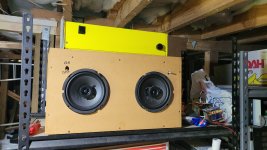
-Chassis from some broken old yamaha I got for free.
-Power transformer and heatsink from some broken AV receiver or another, virtually free.
-Electronics salvaged from some of my first projects getting into the hobby
-salvaged speaker jacks, relays etc.
Assuming everything else was past its service life and therefore free. The most expensive part was the Ali express bluetooth board.
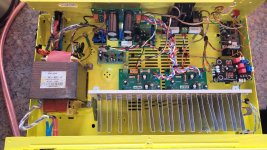
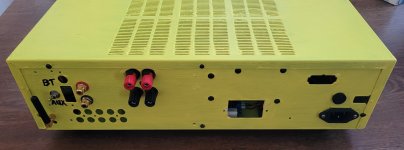
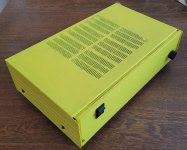
Sweet basement listening while I make stuff:
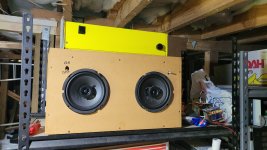
that's really inspiring Sadface, plus with kids at home you need to make your DIY safe from their hands 🙂
I always wondered about giving up this hobby because of the cost of it and the acumulation syndrom it creates.
Well if you ask me hifi 2000 is riduculous high price for what it is, it is a little an italian disease to make almost everything expensive because of design (looking). I prefer to pay for their real good goods.
I always wondered about giving up this hobby because of the cost of it and the acumulation syndrom it creates.
Well if you ask me hifi 2000 is riduculous high price for what it is, it is a little an italian disease to make almost everything expensive because of design (looking). I prefer to pay for their real good goods.
Last edited:
Off you go then!
I've found aluminium up to about 18 gauge is easy to bend over the corner of a desk for right angle bends. It doesn't need a bender like 1.2mm steel does.
You might want a rivet nut gun for fasteners. Cut the sheet however you like. Jigsaw, angle grinder etc.
Old white ware can be a good source of sheet metal if you don't mind steel. Thinner steel can be done over a desk. <1mm.
Dish washers seem to have thicker steel around the back and sides. Washing machines seem to use pretty thin stuff.
The good thing about using folded edges is that the edges of the sheet don't need to be perfect as that is not what is seen.
Except the top and bottom of course. A bit more care is needed with those as those faces are seen.
I think flanges of about 15mm are probably ideal. I used 10mm on my last build which was too short. I used 25mm on the build before that which was annoyingly big.
Too big: 25mm got in the way of putting things into the chassis.
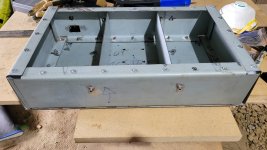
Also, way to many fasteners. It just makes it more difficult than it needs to be.
Too small: 10mm caused problems with hole accuracy around the bended edge
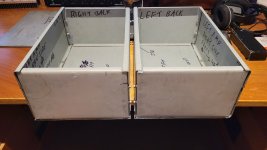
Make sure you account for the bend radius if you want specific dimensions. You could look this up. Or just do some tests folds with scrap to figure it out.
If you're not too concerned then simply make sure you are consistent.
Ali express is actually quite good for fasteners. I've been using a lot of Ali express stainless hex head bolts and rivet nuts recently. They don't seem to suffer from low quality and are much cheaper than what I can find on the ground in New Zealand. Presumably in EU too with its protectionist policies.
I've found aluminium up to about 18 gauge is easy to bend over the corner of a desk for right angle bends. It doesn't need a bender like 1.2mm steel does.
You might want a rivet nut gun for fasteners. Cut the sheet however you like. Jigsaw, angle grinder etc.
Old white ware can be a good source of sheet metal if you don't mind steel. Thinner steel can be done over a desk. <1mm.
Dish washers seem to have thicker steel around the back and sides. Washing machines seem to use pretty thin stuff.
The good thing about using folded edges is that the edges of the sheet don't need to be perfect as that is not what is seen.
Except the top and bottom of course. A bit more care is needed with those as those faces are seen.
I think flanges of about 15mm are probably ideal. I used 10mm on my last build which was too short. I used 25mm on the build before that which was annoyingly big.
Too big: 25mm got in the way of putting things into the chassis.
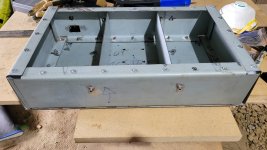
Also, way to many fasteners. It just makes it more difficult than it needs to be.
Too small: 10mm caused problems with hole accuracy around the bended edge
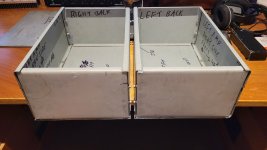
Make sure you account for the bend radius if you want specific dimensions. You could look this up. Or just do some tests folds with scrap to figure it out.
If you're not too concerned then simply make sure you are consistent.
Ali express is actually quite good for fasteners. I've been using a lot of Ali express stainless hex head bolts and rivet nuts recently. They don't seem to suffer from low quality and are much cheaper than what I can find on the ground in New Zealand. Presumably in EU too with its protectionist policies.
good tips, thanks.
I try to avoid AliX for some reasons, distance not being the last. I try to make my modest part to figth the G. Warming. I try too to limit myself on the number of projects, loudspeakers, etc. Both for monney and sanity. You know the story of the Kangugru and the Humming bird ?!
I try to avoid AliX for some reasons, distance not being the last. I try to make my modest part to figth the G. Warming. I try too to limit myself on the number of projects, loudspeakers, etc. Both for monney and sanity. You know the story of the Kangugru and the Humming bird ?!
Last edited:
This was made from a scrap-yard aluminium installation trunking, 190x90mm cross section, already anodised.
Two end pieces in 16mm solid acacia offcuts.
So cost me nothing, just work.
https://www.diyaudio.com/community/...rdell-distortion-analyser.154260/post-1966575
You can get pre-anodised aluminium 2mm bent to any dimensions you want online in Germany.
2 pieces of 90° angle 330x240x90mm will cost ~40€ + postage.
Two pieces of wood, 4 rubber feet, and you can have a very decent DAC case.
Patrick
Attachments
A Quad 405 empty.case can be had for $94
Makes a very quiet housing for a project amp or multi channel class d
Makes a very quiet housing for a project amp or multi channel class d
jealous of your craftmanship skills...
Practice makes perfect.
Patrick
A Quad 405 empty.case can be had for $94
Those from BRZHIFI ?
You still need to add tax and shipment on top.
I can't find anything less than 100USD for original Quad 405's.
Often much more.
Patrick
Another idea, not from me.
A U channel same as post #88 costs only 25€ + postage.
But mounting electronics on a piece of wood is , for me, rather tricky.
Patrick
A U channel same as post #88 costs only 25€ + postage.
But mounting electronics on a piece of wood is , for me, rather tricky.
Patrick
Last edited:
This is a good strategy.I think the cheapest way to go would be to buy a low-cost or faulty AV receiver and slap on a new front and back panel using some sheet aluminium. You may also be able to use some other bits in it, but I wouldn't count on it.
However depending on the chassis, it can be a nightmare.
Most AV receivers have various stuff stamped into the bottom for mounting things. This can make it a real pain in the backside to work around.
I have abandoned more than 1 attempt at salvaging a case for this reason.
The other downside is that most don't have any metal behind the front which reduces the effective shielding.
It can certainly be done however. This is one I did for a friend a few years back:
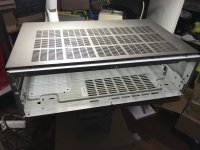
Notice the hole in the front
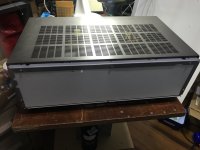
Filled with some scrap steel.
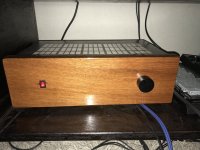
A good work around I have found was to select an AV receiver that you like the "grill" on. In other words the look of the vent holes in the top and either fabricate the rest around it so that you have fresh sheet metal.
I did this recently with the lid from a Pioneer VSX-3300. I liked the top but threw out the rest and fabricated a new botton, front and back to use the nice top:
Base:
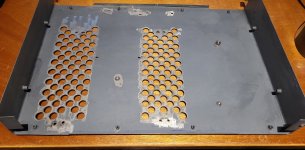
Front:
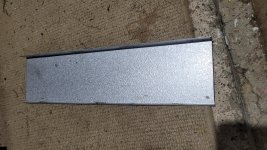
Finished:
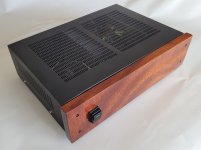
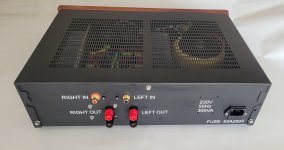
The steel for this was donated by the 20 year old dishwasher that came with my house. The gosh darned thing decided to die on the day we bought my firstborn home.
Good steel though.....
Or, get a local sheet metal shop to make a simple box to go underneath it. I did this the first time round when trying to salvage a lid. Cost me about USD60 to have it made by a local sheet metal guy out of 1.2mm electrogalv steel.
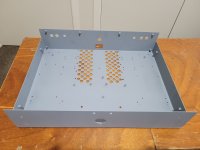
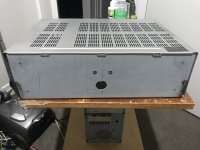
I then accidentally threw out the lid it was designed around in a scrap run. So I then had to get the guy to make me a lid to fit....
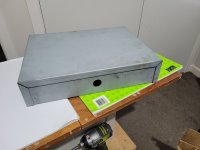
Much cheaper than getting something in from overseas and made to the right dimensions. Of course still a lot of work required to get to this:
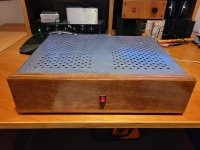
It was this experiment that convinced me to invest in some tools and steel. I expect to make a few chassis' over the coming decade or two so the tools will pay themselves off pretty quickly. I think they already have.
Projects I have accumulated some, most or all of the parts for include:
Wolverine (monos of course)
Iron Pre
Miro 1862 Dac
Aikido Preamp
Tokin SITs (monos of course)
ACA Mini (probably monos)
The occasional commission for a friend.
probably some others I am forgetting
I probably have enough salvaged power transformers and heatsinks around to complete all of them for minimal cost on the heavy bits.
Pro tip: get a step drill bit.
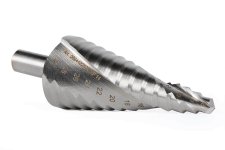
Mine isn't the cheapest, but is far from the most expensive. At this stage it has done thousands of holes and still cuts through sheet nicely.
How did you add the labelling?This was made from a scrap-yard aluminium installation trunking, 190x90mm cross section, already anodised.
Hi Patrick,any link for pre anodized aluminum;View attachment 1361760
This was made from a scrap-yard aluminium installation trunking, 190x90mm cross section, already anodised.
Two end pieces in 16mm solid acacia offcuts.
So cost me nothing, just work.
https://www.diyaudio.com/community/...rdell-distortion-analyser.154260/post-1966575
You can get pre-anodised aluminium 2mm bent to any dimensions you want online in Germany.
2 pieces of 90° angle 330x240x90mm will cost ~40€ + postage.
Two pieces of wood, 4 rubber feet, and you can have a very decent DAC case.
Patrick
https://bleche-nach-mass.de/kantteile/18-l-blech#001-0404
https://blechprofi24.de/blechkantteile/14/l-profil?c=5
(Have NOT used them before)
You need someone in Germany to order and re-ship to you.
But I think you should look for a local shop first.
Patrick
https://blechprofi24.de/blechkantteile/14/l-profil?c=5
(Have NOT used them before)
You need someone in Germany to order and re-ship to you.
But I think you should look for a local shop first.
Patrick
Patrick makes perfect ? 😎Practice makes perfect.
Patrick
- Home
- Member Areas
- The Lounge
- Casing, why so expensive?