petervv said:I made these in '97...
Peter,
I must have run into those very shortly after you did them... they were really inspiring (despite their imagined -- now somewhat confirmed -- shortcomings).
dave
petervv said:Worth the effort? I actually don't think so, the sphere was a great idea, but I think the parallel sides completely ruin the positive effect of the smooth horn extension.
I'm not that surprised -parallel walls mean that smoothing in the other plain only gets you so far. Look nice though. 🙂
hi xiphmont,
>Peter: I've been looking for a photo of those forever! Pics of your speakers were one of the first fullrange horns I ever ran across years and years ago and I'd been looking for them again ever since.
>Do you have a gallery?
I don't have a gallery or website, you can find some more photo's at the bottom of http://www.audiocraftersguild.com/Xtreme/xtreme.htm
hi Dave,
>I must have run into those very shortly after you did them... they were really inspiring (despite their imagined -- now somewhat confirmed -- shortcomings).
thanks for the kind words, your website and work is an inspiration for all fullrangers!
hi Scottmoose
>I'm not that surprised -parallel walls mean that smoothing in the other plain only gets you so far. Look nice though.
I also liked the looks, I made this second (red) set for a dutch tube audio store (Rik Stoet), they were in his demo room for a while.
I sold the first brownish-yellow set to a friend of mine, last time I saw him he asked if I wanted them back but I don't have the space for them, anyone interested? Local (Netherlands) pickup only.
regards, Peter
>Peter: I've been looking for a photo of those forever! Pics of your speakers were one of the first fullrange horns I ever ran across years and years ago and I'd been looking for them again ever since.
>Do you have a gallery?
I don't have a gallery or website, you can find some more photo's at the bottom of http://www.audiocraftersguild.com/Xtreme/xtreme.htm
hi Dave,
>I must have run into those very shortly after you did them... they were really inspiring (despite their imagined -- now somewhat confirmed -- shortcomings).
thanks for the kind words, your website and work is an inspiration for all fullrangers!
hi Scottmoose
>I'm not that surprised -parallel walls mean that smoothing in the other plain only gets you so far. Look nice though.
I also liked the looks, I made this second (red) set for a dutch tube audio store (Rik Stoet), they were in his demo room for a while.
I sold the first brownish-yellow set to a friend of mine, last time I saw him he asked if I wanted them back but I don't have the space for them, anyone interested? Local (Netherlands) pickup only.
regards, Peter
Saw this image in another thread. That looks like a cool way to build a speakers in layers like that. If you didn't have a lot of precise tools, it might actually be easy to build one template and then use a router to but the final shape of each strip.
Anyone know of any plans online for an enclosure like that?
An externally hosted image should be here but it was not working when we last tested it.
Yeah. this is my build, and is done by hands, with vertical saw, layer by layer ...
Took me 3 months to fave all finished, while i was on Florida ....
CNC can do this in no time ...
Sure a CNC could blast out parts for a set of these in short order - but aside from the almost criminally low material yield on even tightly nested parts, is there any test data - for those so inclined - or subjective listening tests that validates any sonic benefits to be accrued from the effort, as opposed to using conventional flat panels?
" ...The Less-Compromised Horn Project by Andrew Pearce (Drew P)
(That great woodworking pastime of the somewhat insane.) "OK, so I've built a regular small two way, a D'Appollito Vifa floor-standing two way, a couple of Audax carbon and HDA based subwoofers so what now? I know, I'll design and build a horn from scratch!" No doubt some of you folks know this story or one similar. The saner of you out there will have found a copy of someone else's plans for a design that had straight internal panels and given a couple of weeks effort had a completed pair of functional horns using a Fostex FE83 or similar. Wise of you.
Let me tell you my story...... Firstly, I did the usual hifi thing and gradually upgraded from my parents crappy 3 in 1 to a medium fi Monitor Audio, Sugden Optima, Arcam Alpha 5, VdH system. Of course, the next step up from this starts to get into silly money and like many of you I’d heard cheap systems offering elusive glimpses of fantastic sound and systems worth more than my house that left me completely unmoved. Hey, I’m sorry but when I walk into a room where U.S.$50K system is playing I feel ripped off if my jaw doesn’t hit the floor and I want to stay lost listening for a week or so. This being the case, I started out on my DIY career. Project one (and my wife’s favourite to date) a pair of open baffle 20mm thick mahogany cabinets (more backless than open baffle I guess) using a single Audax 100ZO HDA 90mmcone. 300 Hz to 6K, some of the sweetest and fastest midrange you are ever likely to hear, great imaging. Aint exactly fullrange but if it sounds nice… Projects 2 – 7 were for friends who found someone who would build subs and speakers for them and are of no interest to us fullrangers really. Just setting the record straight that I’ve been guilty of multi-way dalliances in the past.
Bringing me to today (or if you ask my wife and friends about 2 years ago).
Having built and loved the immediacy of the single driver Audax’s I was looking for more of the same. I’ve listened to big floor-standers, small micros, panels, ribbons and pretty much anything in between except for backloaded single driver horns and electrostatics. People have raved about the realism, image, dynamics and so on of horns ad nauseum so I won’t bore you all repeating it. Let’s just say that I was interested enough to want to give it a go. Research and Theory
So we look at all the literature we can find from the Radiotron Designers Handbook and original Voigt Patents through to Ketil Parow’s Big Fun horn. Stop and admire the Bravura Virtuosos, Lowthers and Living Voices Air Partners along the way. My reading told me that:
Everyone wants low bass to 35-40 Hz Everyone wants a smallish cabinet To achieve 1 and 2, Everyone sticks their horn in the corner at 1/8 of calculated mouth area and truncates the bugger as much as theoretically allowable (and usually a bit more)
Almost everyone uses flat panels inside, constant width, aspect ratios of up to 20:1 and 3 or 4 180 degree beds in their horn path. Most people get a reasonable sound but lumpy restrained bass
I decided to approach the problem from a different direction Horn to be floor not corner loaded (1/4 of calculated mouth) Fc 60Hz, rather have higher cutoff than lumpy bloated bass Tractrix contour 90 degree bends only Shaped internal corners with curves not angled plates Aspect ratio of 3.75:1 maximum and 2:1 or less for majority of horn OK, here I come clean and say I did still truncate my horn design and chopped off the last 40 cm of mouth. My horn area reduction method was also a little different to the standard. Most people calculate the horn at full area (mouth radius 90cm or 160 x 160cm for 60Hz cutoff!) then divide that area by 4 for floor loading giving a mouth 80cm x 80cm. They then run back along the calculations till they reach this area, discard the rest of the distance to the mouth and keep 80 x 80 back to the size of the throat. Usually in an attempt to reduce mouth area further they’ll chop off more of the mouth back beyond 80 x 80 anyhow.
No No No!!! In my opinion, this results in a long, thin horn with a mouth that is no where near opening out to a full termination, you’re lucky if it is opening out at 30 degrees. My design method is to take the entire list of calculations, divide all the areas by 4 then discard the stuff that’s too small to fit your desired throat. Result, smaller area as per the standard method but shorter horn and a mouth that’s still at 90 degree termination.
So then I was bad and did that 40cm of mouth end chopping, wrote down an list of areas, grabbed a ream of photocopy paper and disappeared for about 6 months drawing obscure line drawings that my wife and friends could look blankly at, nod and smile.
Next step: Purchase your drive units. In my case the best I could afford was a pair of Fostex FE168 Sigmas. The graphs for upper response looked flat, they didn’t need equalisation like the 208’s and they were 95dB for 1 watt with a smooth impedance curve.
Now to get the wood. Hangs head in shame and admits to the use of MDF not Baltic birch ply in the construction of a horn speaker. So shoot me! Hard to find, hard to afford and as this is my first horn design I don’t want to fork out my life savings for something that might not work. Hooray!! At last he gets to…
Listening tests:
Bass:
The test tones say there’s precious little below 70Hz. Fortunately I spend about 20 minutes a decade listening to test tones so I don’t particularly care. I don’t listen to organ music. Yes, orchestral timpanis are restrained as are the lowest of kick drums. Bass guitar sounds great, techno and dance bass sounds great, jazz double bass sounds great, grand piano sounds like a grand piano for the first time in ages. (Listen to the Tori Amos cover of Leonard Cohen’s "Famous Blue Raincoat" of the "Tower of Song" tributes album.) There are panel resonances in the low mid upper bass which will reduce once the base plates are fitted. At present the bottom front edge of the side panels is free to flap in the breeze and does so. I may install a 25mm dowel across the centre of the mouth later if the resonances are still bothering me. Treble: Fostex FE168 Sigma units are directional. They drop treble output substantially off axis. My wife complains that if you sit to one side it sounds like you have cotton wool in your ears. True. Yes, the highest treble is restrained and is not as shimmeringly stunning as it could be. Imaging is fabulous. The single driver Fostex units image pinsharp and the bass horn seems to lend piano drumskin hits and bass a sense of palpable scale that I just haven't heard in standard box speakers. I’d say these give apinpoint precise but live scale image. They can pull apart the different singing voices in a harmony and give a sense of stage depth like no other speaker I’ve heard I can now understand what people say about the "They are here" rather than the "You are there" aspect of horns. Dynamics are great, real drum skin smack and guitar attack. One thing I have noticed is that these backhorns are astoundingly level dependant. They drive the room so well that if you play too loud it’s just a bloated overkill, too quiet and things just don’t sound right. W hen you get the level right W OW ! It sounds sad but I’m seriously considering taking to my CD collection with a felt tip pen and marking down the right level for each track. In the past music has been too loud or too quiet. Now it’s just right or wrong. I’m very happy with the result for my first attempt, no doubt once things are run in, the cavity volume is tweaked, the panel resonances reduced and the cosmetics completed I’ll be even happier. These beasties still have much work to do. I wrote my initial appraisal (above) with the glow of a listenable project clouding my vision a little. I have a fair number of colourations to kill. The enclosed volume that isn't part of the horn contour (the bit forward of the rear contour but behind the mouth curves) is singing along and I think could do with sand filling. (What!! More weight!! At least no-one is goingto steal these as happened with my Monitor Audios!) I need to glue on the base plates which should stop the sidewalls from flapping as much. I think the 25mm dowell across the centre of the mouth height about 150mm back might help too. Ahh, tweaking, tweaking, tweaking. Stop reading this! Go design and build your own pair of horns! ... "
(That great woodworking pastime of the somewhat insane.) "OK, so I've built a regular small two way, a D'Appollito Vifa floor-standing two way, a couple of Audax carbon and HDA based subwoofers so what now? I know, I'll design and build a horn from scratch!" No doubt some of you folks know this story or one similar. The saner of you out there will have found a copy of someone else's plans for a design that had straight internal panels and given a couple of weeks effort had a completed pair of functional horns using a Fostex FE83 or similar. Wise of you.
Let me tell you my story...... Firstly, I did the usual hifi thing and gradually upgraded from my parents crappy 3 in 1 to a medium fi Monitor Audio, Sugden Optima, Arcam Alpha 5, VdH system. Of course, the next step up from this starts to get into silly money and like many of you I’d heard cheap systems offering elusive glimpses of fantastic sound and systems worth more than my house that left me completely unmoved. Hey, I’m sorry but when I walk into a room where U.S.$50K system is playing I feel ripped off if my jaw doesn’t hit the floor and I want to stay lost listening for a week or so. This being the case, I started out on my DIY career. Project one (and my wife’s favourite to date) a pair of open baffle 20mm thick mahogany cabinets (more backless than open baffle I guess) using a single Audax 100ZO HDA 90mmcone. 300 Hz to 6K, some of the sweetest and fastest midrange you are ever likely to hear, great imaging. Aint exactly fullrange but if it sounds nice… Projects 2 – 7 were for friends who found someone who would build subs and speakers for them and are of no interest to us fullrangers really. Just setting the record straight that I’ve been guilty of multi-way dalliances in the past.
Bringing me to today (or if you ask my wife and friends about 2 years ago).
Having built and loved the immediacy of the single driver Audax’s I was looking for more of the same. I’ve listened to big floor-standers, small micros, panels, ribbons and pretty much anything in between except for backloaded single driver horns and electrostatics. People have raved about the realism, image, dynamics and so on of horns ad nauseum so I won’t bore you all repeating it. Let’s just say that I was interested enough to want to give it a go. Research and Theory
So we look at all the literature we can find from the Radiotron Designers Handbook and original Voigt Patents through to Ketil Parow’s Big Fun horn. Stop and admire the Bravura Virtuosos, Lowthers and Living Voices Air Partners along the way. My reading told me that:
Everyone wants low bass to 35-40 Hz Everyone wants a smallish cabinet To achieve 1 and 2, Everyone sticks their horn in the corner at 1/8 of calculated mouth area and truncates the bugger as much as theoretically allowable (and usually a bit more)
Almost everyone uses flat panels inside, constant width, aspect ratios of up to 20:1 and 3 or 4 180 degree beds in their horn path. Most people get a reasonable sound but lumpy restrained bass
I decided to approach the problem from a different direction Horn to be floor not corner loaded (1/4 of calculated mouth) Fc 60Hz, rather have higher cutoff than lumpy bloated bass Tractrix contour 90 degree bends only Shaped internal corners with curves not angled plates Aspect ratio of 3.75:1 maximum and 2:1 or less for majority of horn OK, here I come clean and say I did still truncate my horn design and chopped off the last 40 cm of mouth. My horn area reduction method was also a little different to the standard. Most people calculate the horn at full area (mouth radius 90cm or 160 x 160cm for 60Hz cutoff!) then divide that area by 4 for floor loading giving a mouth 80cm x 80cm. They then run back along the calculations till they reach this area, discard the rest of the distance to the mouth and keep 80 x 80 back to the size of the throat. Usually in an attempt to reduce mouth area further they’ll chop off more of the mouth back beyond 80 x 80 anyhow.
No No No!!! In my opinion, this results in a long, thin horn with a mouth that is no where near opening out to a full termination, you’re lucky if it is opening out at 30 degrees. My design method is to take the entire list of calculations, divide all the areas by 4 then discard the stuff that’s too small to fit your desired throat. Result, smaller area as per the standard method but shorter horn and a mouth that’s still at 90 degree termination.
So then I was bad and did that 40cm of mouth end chopping, wrote down an list of areas, grabbed a ream of photocopy paper and disappeared for about 6 months drawing obscure line drawings that my wife and friends could look blankly at, nod and smile.
Next step: Purchase your drive units. In my case the best I could afford was a pair of Fostex FE168 Sigmas. The graphs for upper response looked flat, they didn’t need equalisation like the 208’s and they were 95dB for 1 watt with a smooth impedance curve.
Now to get the wood. Hangs head in shame and admits to the use of MDF not Baltic birch ply in the construction of a horn speaker. So shoot me! Hard to find, hard to afford and as this is my first horn design I don’t want to fork out my life savings for something that might not work. Hooray!! At last he gets to…
Listening tests:
Bass:
The test tones say there’s precious little below 70Hz. Fortunately I spend about 20 minutes a decade listening to test tones so I don’t particularly care. I don’t listen to organ music. Yes, orchestral timpanis are restrained as are the lowest of kick drums. Bass guitar sounds great, techno and dance bass sounds great, jazz double bass sounds great, grand piano sounds like a grand piano for the first time in ages. (Listen to the Tori Amos cover of Leonard Cohen’s "Famous Blue Raincoat" of the "Tower of Song" tributes album.) There are panel resonances in the low mid upper bass which will reduce once the base plates are fitted. At present the bottom front edge of the side panels is free to flap in the breeze and does so. I may install a 25mm dowel across the centre of the mouth later if the resonances are still bothering me. Treble: Fostex FE168 Sigma units are directional. They drop treble output substantially off axis. My wife complains that if you sit to one side it sounds like you have cotton wool in your ears. True. Yes, the highest treble is restrained and is not as shimmeringly stunning as it could be. Imaging is fabulous. The single driver Fostex units image pinsharp and the bass horn seems to lend piano drumskin hits and bass a sense of palpable scale that I just haven't heard in standard box speakers. I’d say these give apinpoint precise but live scale image. They can pull apart the different singing voices in a harmony and give a sense of stage depth like no other speaker I’ve heard I can now understand what people say about the "They are here" rather than the "You are there" aspect of horns. Dynamics are great, real drum skin smack and guitar attack. One thing I have noticed is that these backhorns are astoundingly level dependant. They drive the room so well that if you play too loud it’s just a bloated overkill, too quiet and things just don’t sound right. W hen you get the level right W OW ! It sounds sad but I’m seriously considering taking to my CD collection with a felt tip pen and marking down the right level for each track. In the past music has been too loud or too quiet. Now it’s just right or wrong. I’m very happy with the result for my first attempt, no doubt once things are run in, the cavity volume is tweaked, the panel resonances reduced and the cosmetics completed I’ll be even happier. These beasties still have much work to do. I wrote my initial appraisal (above) with the glow of a listenable project clouding my vision a little. I have a fair number of colourations to kill. The enclosed volume that isn't part of the horn contour (the bit forward of the rear contour but behind the mouth curves) is singing along and I think could do with sand filling. (What!! More weight!! At least no-one is goingto steal these as happened with my Monitor Audios!) I need to glue on the base plates which should stop the sidewalls from flapping as much. I think the 25mm dowell across the centre of the mouth height about 150mm back might help too. Ahh, tweaking, tweaking, tweaking. Stop reading this! Go design and build your own pair of horns! ... "
One point, if you're making layered enclosures in the style under discussion, you should consider making the side panels out of perspex so the "sculpture" can be seen. Otherwise it's a bit like wetting your pants in a dark suit... it gives you a warm feeling but no-one notices.
One point, if you're making layered enclosures in the style under discussion, you should consider making the side panels out of perspex so the "sculpture" can be seen. Otherwise it's a bit like wetting your pants in a dark suit... it gives you a warm feeling but no-one notices.
Do you have any idea what is the price of 4 panels of 3/8" 2x4' perspex or polycarbonate or anything similar ?
Yes, I do. Seems a shame to cheap out after all that expensive CNC work. You could use glass instead.
TelaVox - Hasehiro Back Loaded Horn Speakers
TelaVox - Hasehiro Back Loaded Horn Speakers
Yes, I do. Seems a shame to cheap out after all that expensive CNC work. You could use glass instead.
TelaVox - Hasehiro Back Loaded Horn Speakers
OK, I am kinda tired of arguing with people who just start flaming thread with no reason ....
Lemme tell you something ...
First read my post:
.Yeah. this is my build, and is done by hands, with vertical saw, layer by layer ...
Took me 3 months to fave all finished, while i was on Florida ....
CNC can do this in no time ..
Second ... Find a reason why i "cheap out" :
Plexiglass Acrylic Sheets in Clear
... and you "already know" to "cheap out" price is over $700 for 4 panels - delivered !
Andd also you posted link for 110(W)X350(H)X195(D)mm Weight:/ about 4.5kg each to "show me how this should be done"
Third, i build those in 2005 while i was on Florida - for 2 year before i move back to Germany ... soon will be 10 years, and 4 years before you even join this forum ... And text i posted: "The Less-Compromised Horn Project by Andrew Pearce" is from Web site Single Driver Website"
... but - You wont know that, web site is closed ...
BTW, where is picture your build ????
Out and unscribed ....
It canThat said, it is one of the very few practical ways of getting certain shapes, like horns, without a great deal of time and skill.
Rather than buildup with layers, foam core or other semi-flexible materials like bendy plywood or mdf can also be used to make very accurate complex curved horns that sound great. Here is a tractrix horn done with foam core. Use of constrained layer damping really reduces resonances and gets very clean HD levels.
http://www.diyaudio.com/forums/full-range/261427-presenting-trynergy-full-range-tractrix-synergy.html
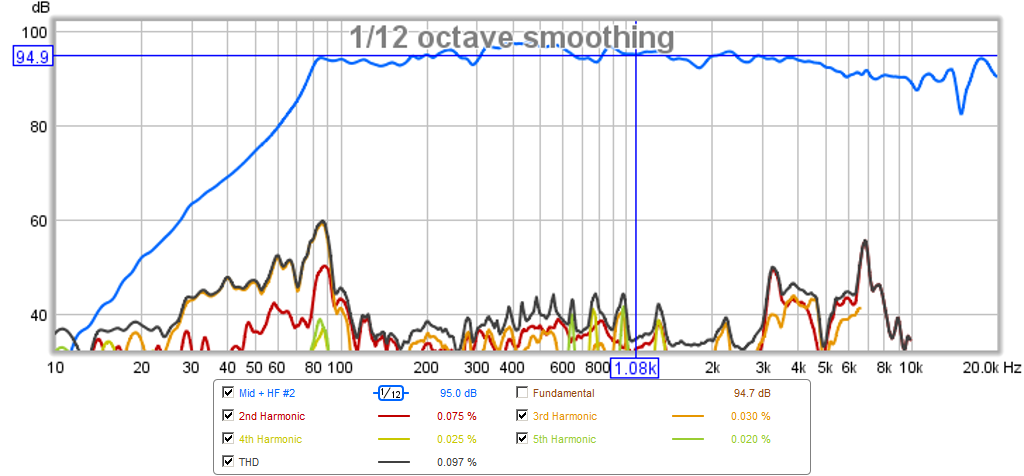
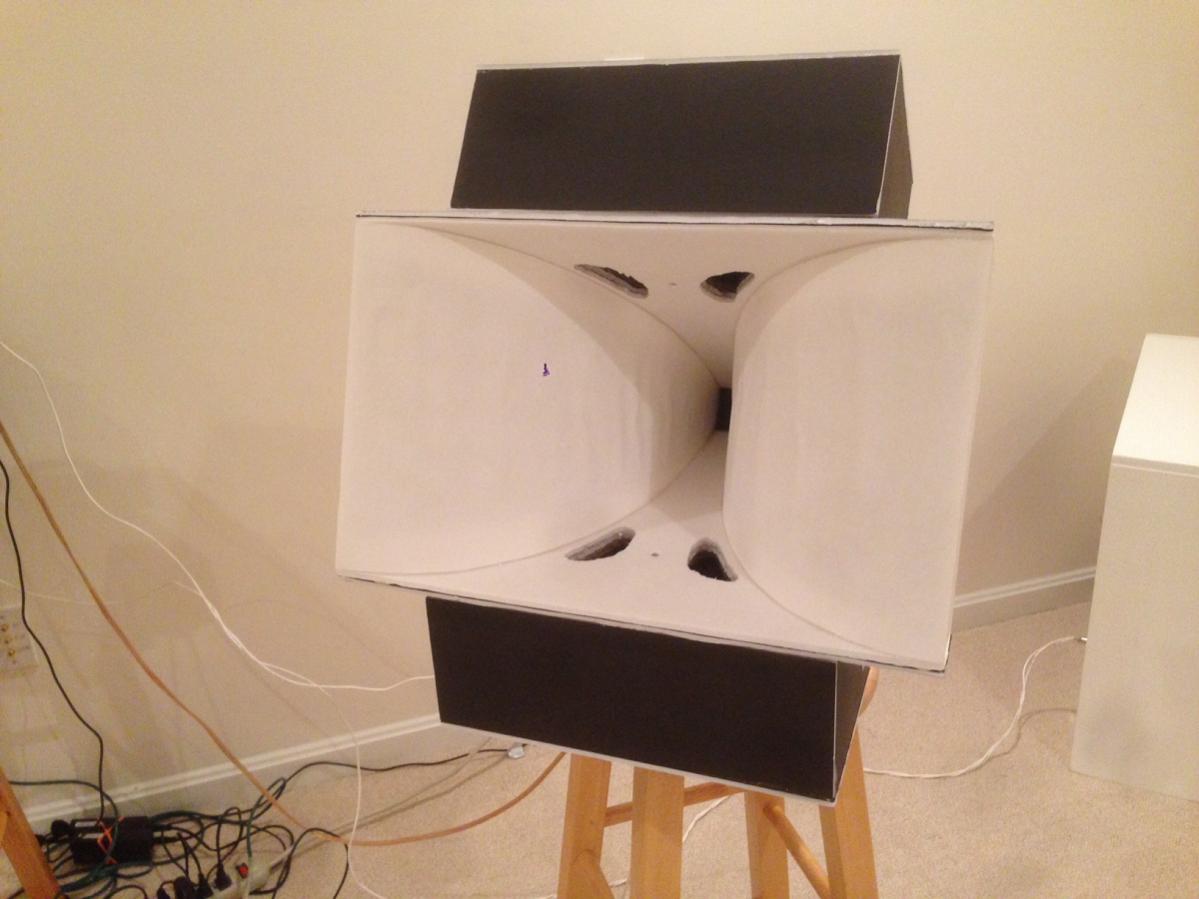
A similar technique could be used to form the curved walls in a BLH. I am now wondering how a tractrix loaded back horn can work. I have noticed that the impedance matching of the tractrix to the driver is very good - almost ideal. I get 23um of cone motion for 90dB SPL at 1m - which leads to very low distortion from such small excursions.
Here is predicted excursion for 90dB SPL (green curve is the full range driver):
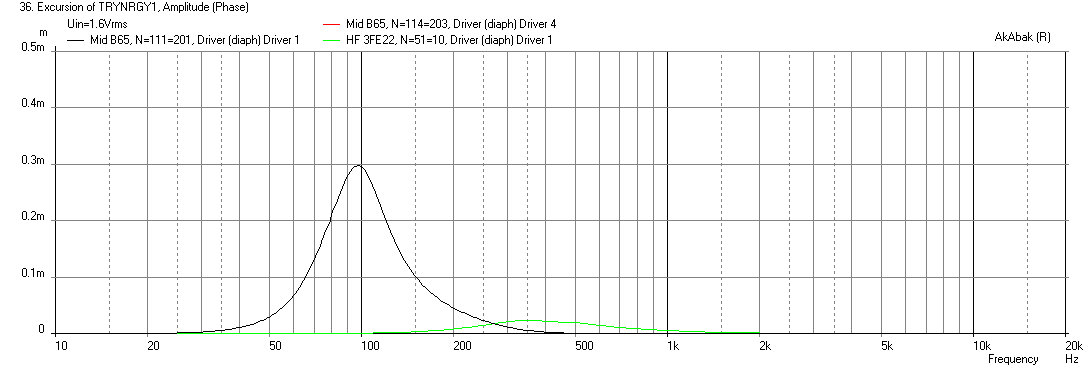
Here is corresponding freq response:
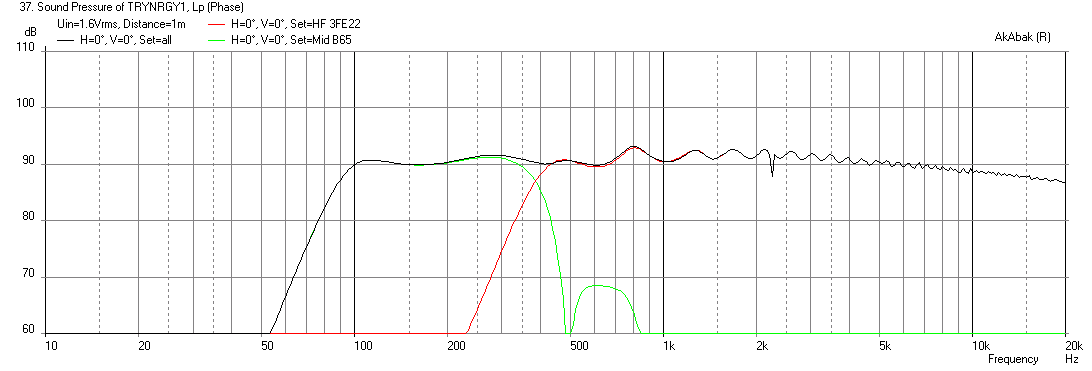
OK, I am kinda tired of arguing with people who just start flaming thread with no reason ....
...
BTW, where is picture your build ????
I apologise for upsetting you, it was not my intention. But who is flaming here? I said it would look nicer with clear sides. You can disagree without losing your temper.
As for my build, I followed this thread because I'm working out what to do with a stack of perspex sheets that's bigger and heavier than I am. It cost me about US$40. It is offcuts from a manufacturer of retail display stands. I have enough to build a couple of cabinets completely out of laminated perspex sheets. They would look spectacular, but I would need to finalise a design before starting because there is a lot of work involved, as you have pointed out.
Saw this image in another thread. That looks like a cool way to build a speakers in layers like that. If you didn't have a lot of precise tools, it might actually be easy to build one template and then use a router to but the final shape of each strip.
Anyone know of any plans online for an enclosure like that?
An externally hosted image should be here but it was not working when we last tested it.
I am thinking about building backloaded horn on different way ....
There is some wood panels easy to shape ...
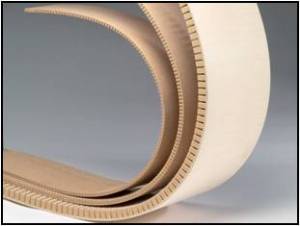
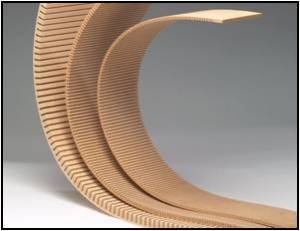
After creating shape you want, fill unused space with builders foam, something like that:

Still working on this project, and will post final 3D design, with material and dimensions ...
My problem is getting right driver, cuz i want ONE speaker inside horn and one tweeter on the top - but to get decent bass without sub ... I am Bass Head ... I dont have too much $$$ @ the moment, just added mortgage to monthly expenses, but will get there, i am thinking about Lowther units, but there is no cheap one .. LoL
Will see, winter is long 🙂
I am thinking about building backloaded horn on different way ....
With a backloaded horn, you really are at a disadvantage if you make it smooth. The pointof smooth is toincrease the high frequency performance... something that you don't want in a BLH.
dave
With a backloaded horn, you really are at a disadvantage if you make it smooth. The pointof smooth is toincrease the high frequency performance... something that you don't want in a BLH.
dave
Hi,
You talking about smooth corners or smooth finish .. ?
Thanx !
You talking about smooth corners or smooth finish .. ?
Smooth corners.
dave
Smooth corners.
dave
OK, but some dampening material gonna help with smooth corners ?
As I understand it, the purpose of (multiple) 90 dg corners on designs such as the Olson- Nagaoka labyrinths, and those that followed is to act as low pass filters for the back wave - and while such manifold designs may use more net material - before waste - speaking from experience, they can be a helluva lot easier to build, and certainly the few pairs I have built sound just fine.
No, you don't want to smooth the curves on a BLH - probably doesn't help all that much on a TL either - but let's throw that one out for debate😀
See ya later kids
No, you don't want to smooth the curves on a BLH - probably doesn't help all that much on a TL either - but let's throw that one out for debate😀
See ya later kids
Last edited:
OK, but some dampening material gonna help with smooth corners ?
The damping will reduce HF, but also LF. Better tonot smooth it and ue less or no damping.
dave
As I understand it, the purpose of (multiple) 90 dg corners on designs such as the Olson- Nagaoka labyrinths, and those that followed is to act as low pass filters for the back wave - and while such manifold designs may use more net material - before waste - speaking from experience, they can be a helluva lot easier to build, and certainly the few pairs I have built sound just fine.
No, you don't want to smooth the curves on a BLH - probably doesn't help all that much on a TL either - but let's throw that one out for debate😀
See ya later kids
Hum, OK ....
- Status
- Not open for further replies.
- Home
- Loudspeakers
- Full Range
- Cabinet in layers