go in small steps with a router. deep as possibly with long straight bit.
from both sides.
Then drill multiple holes and finish center with Sawzall or handsaw.
or just a 4x8 ply sheet and some 2x4 make a large open baffle.
or just cut a hole in a wall.
from both sides.
Then drill multiple holes and finish center with Sawzall or handsaw.
or just a 4x8 ply sheet and some 2x4 make a large open baffle.
or just cut a hole in a wall.
I don't have a router, alas, just hand tools and a 220W drill press. Tiny workshop, so I can only do small jobs.
I'm a fan of Piega and Magico aluminium speakers and want to create a very small and humble example in aluminium. One of the enclosures is 150x150x508mm box aluminium, 3mm thick, as shown. This is an available part.
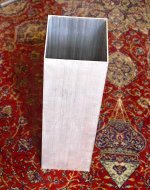
I'm a fan of Piega and Magico aluminium speakers and want to create a very small and humble example in aluminium. One of the enclosures is 150x150x508mm box aluminium, 3mm thick, as shown. This is an available part.
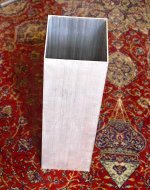
Have you checked into fly cutters? These are used on a drill press and consist of an arm with a cutter on it, and the cutter's position on the arm can be adjusted for different diameter holes.Boring a large hole has come up for me in my latest projects, which use aluminium for the cabinets and/or faceplates. Faced with a 121mm hole to bore for the mid-bass I started with a hole saw. That failed in my 550W Bosch hand drill - too much friction despite lube. Haven't tried it in my 220W drill press yet. Tried the hole saw in my hand brace, but no better. I have a tank cutter coming - that's a kind of fly cutter. Maybe that will work. Last resort would be drilling multiple holes round the circumference.
All advice welcome!!!
Ether chain drilling, or go straight in with a band saw, cut the centre out, and glue the slot left by the band saw blade.
I tried some speakers with the backs removed, and they sounded terrible because of the waves, I shoved a bit of foam where the backs were, and they were totally transformed. Half way between an open pipe, and a closed pipe.
I tried some speakers with the backs removed, and they sounded terrible because of the waves, I shoved a bit of foam where the backs were, and they were totally transformed. Half way between an open pipe, and a closed pipe.
Can you get blades for a coping saw that will cut metal? I could drill one hole, insert the blade and start cutting.
I would use a hole saw and a powerful drill. Cut in sections of an inch or so depth increments. Chisel out the material inside the cut circumference. Repeat, until reaching desired depth.
Or use a small 2" hole saw to hog it out. After making the large circular cuts. Thats actually better and a lot faster than a chisel would be.
I know the saws come in 6" size. If 7" doesn't exist, try a Milwaukee hole tool. They can cut a 7" diameter but they cost a bit more.
https://www.atlas-machinery.com/mil...1K1Ld0KaOoVhXkI_UkNgMGveFHkm0U4YaAgFPEALw_wcB
Or use a small 2" hole saw to hog it out. After making the large circular cuts. Thats actually better and a lot faster than a chisel would be.
I know the saws come in 6" size. If 7" doesn't exist, try a Milwaukee hole tool. They can cut a 7" diameter but they cost a bit more.
https://www.atlas-machinery.com/mil...1K1Ld0KaOoVhXkI_UkNgMGveFHkm0U4YaAgFPEALw_wcB
Last edited:
That's an idea - several holes with smaller hole saws. That can be done - I have plenty.
Yes exactly. Many within one.
Its just about time to get twentieth century on it.
If you use the 6 you could always chisel the remaining 1".
Its just about time to get twentieth century on it.
If you use the 6 you could always chisel the remaining 1".
If you are not used to machining aluminum sections, bear in mind the stuff tends to stick to the tool.
Use proper cutting fluid as well.
Fly cutter will be best, as the section may distort with multiple holes.
As for wood, I would consider an alternate method, cut it into thick slabs / planks, and use those to make a box.
The more experienced members will tell you if that is a good idea or a bad one, though it will defeat the solid block approach.
You can make a cavity using a ball nose cutter or an end mill, doing that with a 220W 1/4 HP machine will be a lengthy process.
That is best done on a milling machine.
Look around, see if you can get it done outside at a reasonable price, most shops here do not like wood chips in their machines.
I do know a wooden (casting) pattern maker with multiple gantry type milling machines with CNC, that will work.
Handling a heavy piece of wood is also an issue.
Think about my suggestions, and tell me your opinion.
Use proper cutting fluid as well.
Fly cutter will be best, as the section may distort with multiple holes.
As for wood, I would consider an alternate method, cut it into thick slabs / planks, and use those to make a box.
The more experienced members will tell you if that is a good idea or a bad one, though it will defeat the solid block approach.
You can make a cavity using a ball nose cutter or an end mill, doing that with a 220W 1/4 HP machine will be a lengthy process.
That is best done on a milling machine.
Look around, see if you can get it done outside at a reasonable price, most shops here do not like wood chips in their machines.
I do know a wooden (casting) pattern maker with multiple gantry type milling machines with CNC, that will work.
Handling a heavy piece of wood is also an issue.
Think about my suggestions, and tell me your opinion.
Last edited:
You can get coping saw blades for metal, and jigsaw blades as well, I cut out frames in 4 mm stainless steel with a jigsaw, lubed the blade with soap and water. I wouldn't want to do it again though, it was noisy and took a while but it got the job done.
If there is a auto repair machine shop in your area, or a large machine shop, ask for it to be done on a line boring machine, those are used for making holes for bearings in gear boxes, and also engine blocks.
There are shops here with machines for rebuilding engines and gear boxes, they bore the blocks out, put sleeves if needed and so on...they might do it.
That is safer and quicker than finding a large lathe.
Should not take more than two hours.
Provided of course, you need a through hole, which is my impression, I could be wrong.
There are shops here with machines for rebuilding engines and gear boxes, they bore the blocks out, put sleeves if needed and so on...they might do it.
That is safer and quicker than finding a large lathe.
Should not take more than two hours.
Provided of course, you need a through hole, which is my impression, I could be wrong.
A big block chev 454ci hardly exceeds a 4" bore. A 572 has a bore of 4.375. Even boring it for sleeves wouldn't exceed 4.50" so still a ways off. If the stock could be mounted and it were possible the shop would have to be willing.
A manual lathe set up for wood working would be better.
Our forefathers could hook it up. They were used to working with stock that large and had the hand tools for it.
A manual lathe set up for wood working would be better.
Our forefathers could hook it up. They were used to working with stock that large and had the hand tools for it.
Stay safe! Hand routers are the most dangerous tool, but so is a drill, as I learned yesterday when I got a metal piece in my belly and scraped up my skin. I was just going to drill a 8 mm hole, and the drill bit was dull. The other drill bits went into the aluminium so smoothly but the last drill bit was not sharp enough and got stuck and the drill went flying into the room. Luckily my belly stopped it. 😛
The line boring machines here have single point tools held between centers, the job is fixed to the table.
And I said truck, which in India means a vehicle used to carry a load of more than 3 tons, or a freight carrier / lorry. They tend to have larger engines than cars.
Americans and Australians refer to vehicles which are called pick-up vehicles here as trucks, that could be the cause of the confusion.
We in India use cylindrical grinders then hone on sleeves, the cylinder boring machines also are having multi point tools, similar to a the adjustable reamers.
What you will use depends on what facility is available in your area, and that will decide your working method.
You can spend days with hammer and chisel, or get it machined.
Circular saws have their own limitations, particularly a 6" saw will need a powerful motor, a 220W motor may fall short in that department.
And I said truck, which in India means a vehicle used to carry a load of more than 3 tons, or a freight carrier / lorry. They tend to have larger engines than cars.
Americans and Australians refer to vehicles which are called pick-up vehicles here as trucks, that could be the cause of the confusion.
We in India use cylindrical grinders then hone on sleeves, the cylinder boring machines also are having multi point tools, similar to a the adjustable reamers.
What you will use depends on what facility is available in your area, and that will decide your working method.
You can spend days with hammer and chisel, or get it machined.
Circular saws have their own limitations, particularly a 6" saw will need a powerful motor, a 220W motor may fall short in that department.
Never catch the drill bit on loose clothing. Even at low rpms its smarts.Stay safe! Hand routers are the most dangerous tool, but so is a drill, as I learned yesterday when I got a metal piece in my belly and scraped up my skin. I was just going to drill a 8 mm hole, and the drill bit was dull. The other drill bits went into the aluminium so smoothly but the last drill bit was not sharp enough and got stuck and the drill went flying into the room. Luckily my belly stopped it. 😛
BTW if those are considered dangerous (wich most power tools can be) then an angle grinder is down right wicked. Especially to the unsuspecting. If you dont respect an innocent appearing an angle grinder they will quickly teach you. In many cases its not maybe. There's very little to no room for error with those before a trip to a plastic surgeon.
Last edited:
As they say in Norway - "you cannot come to the mountain top by a flat road"....Stay safe! Hand routers are the most dangerous tool, but so is a drill, as I learned yesterday when I got a metal piece in my belly and scraped up my skin. I was just going to drill a 8 mm hole, and the drill bit was dull. The other drill bits went into the aluminium so smoothly but the last drill bit was not sharp enough and got stuck and the drill went flying into the room. Luckily my belly stopped it. 😛
Where are you? A Woodcraft or equivalent woodworking store that does classes, etc. would probably have a lathe that would handle that block (you might have to accept some mounting holes). A vocational college (some high schools) might have one as well.
For doing it here in the garage (where I don't have a lathe that big), I would probably use a 1"-1-1/4" auger bit or the like to cut the holes out rather than hole saws (they also come in handy running wire, pipe, etc.).
... edit, in case the context didn't come through. You can bore with auger bits by hand although it's a pain...
If you have access to a drill press, mount it on a base with a center pivot so you can turn/spin the block to drill the holes tangent to each other and the desired circle (without a lot of intermediate set-up/precision issues).
Then I would rough it out with a gouge if you have them, a chisel if not.
I probably would try to find/make something to clean it up nice like an automobile cylinder honing device, possibly a sanding flapper if you are "good" (I am not "good" and it that would end up lopsided like the joke about trimming the Christmas tree).
For doing it here in the garage (where I don't have a lathe that big), I would probably use a 1"-1-1/4" auger bit or the like to cut the holes out rather than hole saws (they also come in handy running wire, pipe, etc.).
... edit, in case the context didn't come through. You can bore with auger bits by hand although it's a pain...
If you have access to a drill press, mount it on a base with a center pivot so you can turn/spin the block to drill the holes tangent to each other and the desired circle (without a lot of intermediate set-up/precision issues).
Then I would rough it out with a gouge if you have them, a chisel if not.
I probably would try to find/make something to clean it up nice like an automobile cylinder honing device, possibly a sanding flapper if you are "good" (I am not "good" and it that would end up lopsided like the joke about trimming the Christmas tree).
Last edited:
Well, I've tried the tank cutter and that was useless in a hand brace. Don't know in a drill press. I managed to gouge out half of the cut with the hole saw in my 550W hand drill. I then finished the hole off with a coping saw and a file. It was VERY TEDIOUS and time consuming in 4mm alu. So for any future builds I'm pretty convinced it has to be the hole saw in something that has enough power to turn it. The rest is just wasting time and effort. The only alternative I can see is a jigsaw. That would be a pretty rough cut, so again it would need a file which would be very tedious. As I said before I don't have a router and no room for one. Smallish apartment in London.
I'd really like to find a proper workshop close by. I'm in fairly central London after all.
I'd really like to find a proper workshop close by. I'm in fairly central London after all.
Oh, sugar. I was responding to the original post about a hole in wood, sorry.
Machine shop.
But at home, my first thought is same idea with turn-table and drill press. But, depending on the size of the box and press, it will block drilling some portion of the arc. If it fits, I just would just use 1/8 or 1/4 bits and drill a lot of holes. You will be filing for a while.
Then clean it up (depending on the depth) with a wood form (cone or if you can get it precise, a cylinder) with sandpaper in a drill or the press.
Machine shop.
But at home, my first thought is same idea with turn-table and drill press. But, depending on the size of the box and press, it will block drilling some portion of the arc. If it fits, I just would just use 1/8 or 1/4 bits and drill a lot of holes. You will be filing for a while.
Then clean it up (depending on the depth) with a wood form (cone or if you can get it precise, a cylinder) with sandpaper in a drill or the press.
- Home
- Design & Build
- Construction Tips
- Boring Large Hole