Also try US composites at http://www.shopmaninc.com
I've used the spray version with great success. You have to use it over a well waxed form.
I've used the spray version with great success. You have to use it over a well waxed form.
Re: I haven't tried it....
After making cabinets in composites for years I'm giving up and going to wood. Its just a lot cheaper and easier to deal with. The composites are great, but push the product price too high to be justified in terms of performance. They look great though.
chrismercurio said:but Marten Design uses monocoque construction in their Coltrane line of loudspeakers. I'm sure once the prototyping is over and the design kinks are worked out it is an easy way to build a cabinet....but getting there must be quite a journey.
Chris
After making cabinets in composites for years I'm giving up and going to wood. Its just a lot cheaper and easier to deal with. The composites are great, but push the product price too high to be justified in terms of performance. They look great though.
gedlee said:...Isolating the speaker from the enclousre is a bad idea from a number of perspectives, so I don't consider that a solution.
I would have to listen to these: Fuji Eclipse TD712; reviewed at Stereophile.com, before I came to any conclusion about that notion...
critofur said:
I would have to listen to these: Fuji Eclipse TD712; reviewed at Stereophile.com, before I came to any conclusion about that notion...
You should read these reviews of mine then:
http://www.diyaudio.com/forums/showthread.php?postid=1507485#post1507485
And
http://www.diyaudio.com/forums/showthread.php?postid=1520192#post1520192
Real reviews, not Stereophile reviews.
critofur said:
I would have to listen to these: Fuji Eclipse TD712; reviewed at Stereophile.com, before I came to any conclusion about that notion...
I agree. As I said earlier, isolating the driver from the cabinet should be the goal, and this is one way to achieve that.
That Fujitsu company also makes a subwoofer with opposing drivers connected by an aluminum shaft. Brilliant!
Here's a pdf of the brochure. I'd think it was marketing B.S., if I already didn't understand the theory behind it. These speakers go for thousands of USD, but could be made for much less than that DIY.
Here's a pdf of the brochure. I'd think it was marketing B.S., if I already didn't understand the theory behind it. These speakers go for thousands of USD, but could be made for much less than that DIY.
gedlee said:Real reviews, not Stereophile reviews.
I read the reviews.
Your system seems to be a custom made system where the subs are designed specifically for the transfer function of your room. Right?
The tightness of the bass comes from the fact that the main speakers operate down to 50Hz with the BP subs only providing a foundation. Right?
Are the BP subs configured to play at much lower levels than the main speakers. I ask this because BP subs are known to be very effcient in the quantity of the bass they deliver.
I once built BP subs (in stereo) each sub using 2 10" Peerless (831727) woofers in a 3 chambered box (center chamber was vented) for a Dynaudio Gemini kit. The "visceral kick" these subs provided was appreciated but I began to suspect that they lacked fine definition. After reading your reviews I now assume the errors made were that I did not provide any over lap between the subs and Geminis and that the subs were about the same level as the Gemini.
The reviews your system has got as atlesat got me looking at BP as an option again. Any guidance in this matter would be much appreciated. I live in India and coming to the US to listen to your system is not a convienient option.
I have 4 12" Audio Concpets woofers that I can use to experiment.
navin said:Your system seems to be a custom made system where the subs are designed specifically for the transfer function of your room. Right?
No not at all, its just a generic design.
The tightness of the bass comes from the fact that the main speakers operate down to 50Hz with the BP subs only providing a foundation. Right?
The bass quality comes from the fact that there are multiple LF sources spread throughout the room (some of them are the mains and some are subs) thus flattening the spatial and spectral variations found in most LF systems.
gedlee said:The bass quality comes from the fact that there are multiple LF sources spread throughout the room (some of them are the mains and some are subs) thus flattening the spatial and spectral variations found in most LF systems.
how WAF friendly is this process?
Most of us are lucky if we are allowed to get a pair of floorstanders.
I was considering bandpass becuase I believe that for it's size it can produce the most bass. What about goig isobarik with bandpass using 2 woofers in push-pull config? This would be even more compact.
I fear we have gone terribly Off Topic! Sorry.
I'm using epoxy for special parts of loudspeaker cabinets and difficult shapes, like this phase plug (for a 15"):Most of you have probably seen this two-component epoxy resin material. It's very dense, although it scratches quite easily. Wouldn't it be neat to create a "monocoque" speaker cabinet? One would have to construct a mold, and then simply fill the mould with the epoxy resin. Has anyone here considered this type of approach or heard of it being done?


This is mostly polyester/ fibreglass (4/5" thick), glued with epoxy/chalk, filled with polyurethane 2-comp. foam and painted with a 2-comp PU-paint. It's not quite finished yet but unfortunately it went down the line of priorities 😉
A bit more info why reinforcement materials such as aramide, glass fibre and carbon have such great benefits in combination with polyester and epoxy can be derived from the next table (translated to the best of my knowledge): Especially loudspeaker enclosures would benefit from these fibres added. Carbon fibre in special, as it acts against vibrations.
As you can see the resins are primarily strong upon being pressed together were as the fibres offer strength against being pulled apart.
The strongest composite I made up to date from epoxy and chopped glass strands was a bit thougher/harder than 13-laminate void free Baltic birch but quite more dense and expensive. The latter is the main reason I only use it for smaller and extraordinary/ difficult objects.
No problems with only using wax occurred up till now. 5 layers of wax were sufficient for removal from a variety of moulds. However epoxy shrinks a little (up to 5%), polyester shrinks quite a bit (up to 10%) so it can wrap itself around a mould, or creating forces making it nasty or impossible to separate. The phase plug as above shrunk itself on the inner PU-foam core. More filler or fibre added = less shrink.Wax alone will NOT work
Can’t find the quote but I've tried adding wood dust but only small quantities could be added before it turned into a paste (about 20-25% MDF dust). edit- other non-fibre fillers can be used in larger percentages resulting in lower cost and possible better performance -edit-
Regards Johan
And here epoxy with chalk (calciumcarbonate)(1:1 ratio) to cover up an experimental internal bracing to make thin yet very stiff enclosures:
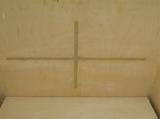
About the MDF router dust.
Regards Johan
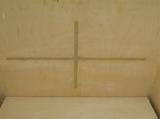
About the MDF router dust.
4 parts epoxy mixture, 1 part MDF saw/router dust (parts by weight): The ratio in volume was about 3 parts epoxy mixture to 2 parts MDF dust. Which was just enough to make all the dust wet with the epoxy. It's good for getting pressed into medium or larger templates. At smaller gaps (smaller than a square inch) it might be easier to work with the following.
5 parts epoxy mixture, 1 part MDF saw/router dust (parts by weight): It pretty much has the consistency of a tinnish peanut butter and it looks like it as well (in use and after hardening). Actually, from 2 ft away I probably couldn't tell the difference, except for the slightly present, distinct smell.
It doesn't however give a perfect finish, it's finish looks and feels pretty much like a slight textured finish, as Trimite, Warnex and alike.
Regards Johan
JL Audio uses many layers of fiberglass and epoxy to make their subwoofer enclosures (Gotham + Fathom).
Pretty impressive stuff and it is just solid epoxy and fiberglass.
The rest of the pics are here...
JL Audio Tour
Pretty impressive stuff and it is just solid epoxy and fiberglass.
An externally hosted image should be here but it was not working when we last tested it.
An externally hosted image should be here but it was not working when we last tested it.
An externally hosted image should be here but it was not working when we last tested it.
An externally hosted image should be here but it was not working when we last tested it.
The rest of the pics are here...
JL Audio Tour
!
I am very new to this, but I auditioned some Wilson Audio Alexandria's yesterday and they were incredible. I looked at them pretty closely and it looks like they are made of an epoxy style composite. The speakers were very heavy as well.
Thanks for the great thread!
Gene
I am very new to this, but I auditioned some Wilson Audio Alexandria's yesterday and they were incredible. I looked at them pretty closely and it looks like they are made of an epoxy style composite. The speakers were very heavy as well.
Thanks for the great thread!
Gene
Wilson speakers used to be made out of phenolic laminate sheets and mdf sheets.....depending on if it was "x" material or "m" material. Their crossovers are potted (read hidden) in epoxy.
Chris
Chris
- Status
- Not open for further replies.
- Home
- Loudspeakers
- Multi-Way
- Anyone ever try using epoxy resin for cabinet material?