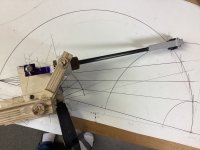
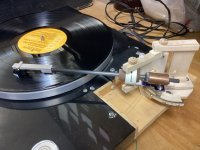
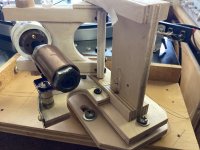
Stipulated: This is an exercise in wretched excess.
About a year ago, I built a string suspended TA which I have been using happily since. In discussions with Carlo (nocdplz), the possibility of a string suspended pivoting linear tonearm came up. I tried an experiment to see if a tensioned length of dyneema would support the weight of the arm without distorting badly. It did. I'd kinda hoped for failure.
A local hardware store carries small pieces of Baltic birch plywood for model airplane building, with excellent strength to weight characteristics, which was helpful because I can only do limited metal work in my shop.
The twin arm geometry is from several years ago and is posted in the "Angling for 90 degrees" thread. All of the pivot points are string - there are no bearings anywhere. The rear control arm is string/magnet/attractor.
The arm actually works well and seems happy with both low and medium compliance carts. It tracks accurately, doesn't skip, allows the cartridge to do its job and the resulting music is quite nice. I haven't done tests yet. The first will be for resonances, which weill narrow cart choice and also show how much difference there is between horizontal and vertical masses.
Doug
Using strings as bearings is undoubtedly inspirational. Great job! I especially like the back guiding mechanism. The only criticism is that the strings may not be easy to adjust the tensions. The Ballpoint pen is easy to install.
Last edited:
Inspirational indeed! It would be a matter of selecting the right string, I get that, but it reminds me of a part on a German clock that I bought. In that case it was a very fine wire, used as a torsion spring in which acts as the balance/timing wheel metronome IIRC. Sorry my terminology isn't going to be real good here. Anyway, this same action of torsion may be present in even a string, and that is what I would be curious about. Same idea as the tonearm leads adding a bit of torsion themselves if not dressed just right.
Though I understand the need for the rear guide wire, a different problem catches my attention, and that is horizontal friction. Perhaps as in the other choice of string, this could be compensated for by the type of string chosen. Either way, there are great possibilities here.
Ahem. Upon further inspection of the photos, I am increasingly sure that I didn't get the full impact of the design, and the idea of torsion being any issue, would likely be irrelevant given the limited amount of movement of any given string. But I want to understand another aspect more clearly. Can you explain string/magnet/attractor as used for the rear control arm? Thanks.
Though I understand the need for the rear guide wire, a different problem catches my attention, and that is horizontal friction. Perhaps as in the other choice of string, this could be compensated for by the type of string chosen. Either way, there are great possibilities here.
Ahem. Upon further inspection of the photos, I am increasingly sure that I didn't get the full impact of the design, and the idea of torsion being any issue, would likely be irrelevant given the limited amount of movement of any given string. But I want to understand another aspect more clearly. Can you explain string/magnet/attractor as used for the rear control arm? Thanks.
Last edited:
Further examining the back control mechanism, I have a suggestion for the construction of the magnet. From the picture, it seems that the bottom of the magnet touches the wooden plate under the magnet. The contact between the wooden plate and the magnet may produce unwanted friction.
It looks like the magnet is a pretty strong one. The friction between the magnet and the wooden plate may be neglectable. I would still suggest cutting a piece of half-moon-shaped plastic or metal to glue under the path of the magnet to reduce friction. Another option is to make the magnet suspend 3 mm or even higher above the wooden plate while the side of the magnet is lined up with the curved steel rail. There will be no friction between the magnet and the wooden plate.
It looks like the magnet is a pretty strong one. The friction between the magnet and the wooden plate may be neglectable. I would still suggest cutting a piece of half-moon-shaped plastic or metal to glue under the path of the magnet to reduce friction. Another option is to make the magnet suspend 3 mm or even higher above the wooden plate while the side of the magnet is lined up with the curved steel rail. There will be no friction between the magnet and the wooden plate.
Last edited:
Thank you for your thoughtful replies.
I spent almost as much time building jigs for tensioning the strings as I did building the arm. There is no way to adjust tension on this arm, but the string on the original pivot string arm has retained tension for almost a year.
Torsion has to be dealt with, but it’s not all negative - it can be used for anti-skating. I haven’t done that with this arm, but it works well on the pivot arm. I‘ve incorporated a lot I learned from that arm into this one Including making the gap between parts as close as possible so they are close coupled. That helps prevent misalignment, especially vertical. The swing arm stays level through its entire movement.
The magnet just clears both the metal attractor and the wood but not by much. There are lots of moving parts in a small space so there isn’t much room for adjustments. For instance, if the attractor was raised, it would foul the bottom of the swing arm. I used a lot of parts that were around my shop or appropriated from other uses. The magnet was available and the attractor is the lip of a coffee can that just happened to have about the right radius. There are better magnet arrangements, I’m not particularly proud of this one, but mounted the way it is means it doesn’t pull too hard and it aligns easily.
The string and magnet idea came from Frank Schroeder and I’m pleased that it works well. As the arm crosses a record, the forces on the string and magnet are a combination of outward and tangent to the attractor arc so the string is tensioned. When the arm is lifted and returned to it’s rest position, the outward force reverses, turns inward, so care is needed.
Doug
I spent almost as much time building jigs for tensioning the strings as I did building the arm. There is no way to adjust tension on this arm, but the string on the original pivot string arm has retained tension for almost a year.
Torsion has to be dealt with, but it’s not all negative - it can be used for anti-skating. I haven’t done that with this arm, but it works well on the pivot arm. I‘ve incorporated a lot I learned from that arm into this one Including making the gap between parts as close as possible so they are close coupled. That helps prevent misalignment, especially vertical. The swing arm stays level through its entire movement.
The magnet just clears both the metal attractor and the wood but not by much. There are lots of moving parts in a small space so there isn’t much room for adjustments. For instance, if the attractor was raised, it would foul the bottom of the swing arm. I used a lot of parts that were around my shop or appropriated from other uses. The magnet was available and the attractor is the lip of a coffee can that just happened to have about the right radius. There are better magnet arrangements, I’m not particularly proud of this one, but mounted the way it is means it doesn’t pull too hard and it aligns easily.
The string and magnet idea came from Frank Schroeder and I’m pleased that it works well. As the arm crosses a record, the forces on the string and magnet are a combination of outward and tangent to the attractor arc so the string is tensioned. When the arm is lifted and returned to it’s rest position, the outward force reverses, turns inward, so care is needed.
Doug
If the Dyneema gives way (and it doesn't look like it will!), a possible alternative is tungsten wire. Micro Seiki used it for their MA-505 tonearm.
Cheers,
Mike
Cheers,
Mike
Skating force follows the blue line at a Birch type tonearm.
Torsional torque is a mirror image of it, it increases proportionally to the rotation.
Torsional torque is a mirror image of it, it increases proportionally to the rotation.
What is the pivot point you use to calculate the skating force for Birch type tonearm? Or I should say virtual pivot point.Skating force follows the blue line at a Birch type tonearm.
Torsional torque is a mirror image of it, it increases proportionally to the rotation.
All Birch-type tonearms don't skate, including the one here. If it skates, it means the tower is not perfectly leveled or in other words, its two sides are not balanced.
I wonder what the mechanical resonant frequencies are of the suspension system - are they damped enough? Below the audio spectrum?
I just ran a couple of test on this arm - skating and resonances. Resonances first: The cart is a Sumiko Pearl which has a claimed compliance of 15 x 10-6cm/dyne. The tests with the HFnews test record were inconclusive because the audible and visual signs were muted, far less noticeable than on any conventional arm I’ve tested. The usual resonance dance didn’t happen. The most noticeable resonances were L = 6Hz and V = 8Hz. Working backwards with the VE resonance calculator gives EMs of approx. L = 30 gr and V = 20 gr. The lateral is about what I expected and the vertical is high. There were indications the vertical might be about 10 gr, which is closer to what I expected.
I put a stethoscope on the support frame and wand carrier while playing a record. There was no needle talk, no music. That was true with the single pivot string arm, too. I think maybe the strings just eat that energy and also damp the mechanical resonances.
I really don’t want to wade into the skating swamp, but I did Ray’s string skating test and the arm moved inward which I expected because that was true of other PLTs I’ve built. Jim, I argued with Ray for years based on the Birch virtual pivot, but then I tried a different approach: I drew lines from the inner and outer bearings of the swing arm through the stylus point. The resulting angle is the offset, which gets smaller across the record, and the skating force follows Alighiszem’s blue line. Carlo did a more complete analysis and came to the same conclusion.
I did a couple of other skating tests, made a slight - less than a quarter bubble - adjustment to the support vertical alignment, and the arm settled down.
Doug
I put a stethoscope on the support frame and wand carrier while playing a record. There was no needle talk, no music. That was true with the single pivot string arm, too. I think maybe the strings just eat that energy and also damp the mechanical resonances.
I really don’t want to wade into the skating swamp, but I did Ray’s string skating test and the arm moved inward which I expected because that was true of other PLTs I’ve built. Jim, I argued with Ray for years based on the Birch virtual pivot, but then I tried a different approach: I drew lines from the inner and outer bearings of the swing arm through the stylus point. The resulting angle is the offset, which gets smaller across the record, and the skating force follows Alighiszem’s blue line. Carlo did a more complete analysis and came to the same conclusion.
I did a couple of other skating tests, made a slight - less than a quarter bubble - adjustment to the support vertical alignment, and the arm settled down.
Doug
I don't want to drag this thread into another skating discussion thread so I will try to be as brief as I can.I really don’t want to wade into the skating swamp, but I did Ray’s string skating test and the arm moved inward which I expected because that was true of other PLTs I’ve built. Jim, I argued with Ray for years based on the Birch virtual pivot, but then I tried a different approach: I drew lines from the inner and outer bearings of the swing arm through the stylus point. The resulting angle is the offset, which gets smaller across the record, and the skating force follows Alighiszem’s blue line. Carlo did a more complete analysis and came to the same conclusion.
Again, Ray's string test is not the golden standard of testing if a tonearm skates. It is flawed. Even Ray realized that.
Here are the links.
First link
https://www.diyaudio.com/community/...g-pivoting-tonearm.373127/page-7#post-6696029
In the first link, 2wice proposed the so-called string test version 2. Ray said he liked it. However, I immediately pointed out that String Test V. 2 is not doable. It can't be performed in reality. Therefore, it is meaningless.
2nd link
https://www.diyaudio.com/community/...ngential-tracking-pivot-tonearm.373984/page-3
In the 2nd link, Ray proposed another version of his string test V 2.1. I asked Ray at once.
I have never gotten an answer from Ray. I don't think he is able to answer my question.How do you determine that your string is tangent to the groove? If it is a test, you have to actually perform such a test on a tonearm. I would like to see you actually perform such a test before we will discuss it further.
I posted these links here to remind you that even the original author recognizes the flaw of his invention.
We can't reach a consensus if the standard is flawed. In my opinion, the only correct test for skating is my blank disk test which I did it years ago, and so does Wally Tools later on. We can only reach a consensus based on a correct testing method. I would like to see you perform the blank disc test to see if your Birch-style arm skates or not.
For a Birch-style arm, the level of the tower is very critical. Frank Schroeder realized that. He added a level adjustment mechanism on his Birch style tonearm. Other manufactories may not even realize that yet. I would say their arms are problematic. I didn't realize that at the beginning of building my 6B arm. I thought a Birch-style arm will skate when I started to build my 6B arm. Now, I can't understand why you guys don't believe what they see with your own eyeballs. Even the simple fact lies in front of you, but you guys still want to trust your own believings.
If you want to perform my blank disc test, you need to adjust the level of the tower. I have spent a huge amount of time adjusting my 6B arm. If the tower leans on one side, the arm will skate to the same side. Only if the tower is perfectly balanced, the arm doesn't skate. The arm sounds the best when the tower is balanced.
Whether or not a Birch-style arm skate is structurally related. Under ideal conditions, all Birch-style arms don't skate. Skating is not embedded in Birch-style arms.
Speaking of Alighiszem’s calculation of skating force, I have asked him which pivot he used to do such a calculation. But I get no answer. For a Birch-style arm, there is the primary pivot, 2P2, secondary pivot 1P2, and virtual pivot P3, as I named it.
Which pivot did he use to calculate the skating force of a Birch-style arm? I get no answer. I don't believe his calculation is valid since he doesn't have enough understanding about Birch-style arms.
Last edited:
You got no answer because you are on my ignore list and I check your comments only ocassionally. Life is too short to argue with someone who never makes any effort to understand what I write.
"I have asked him which pivot he used to do such a calculation. But I get no answer."
I wrote for instance that the Birch tonearm rotates around the center of the Thales circle. Do you understand that? You got your answer!
The stylus is moving on the Thales circle.
The stylus of a traditional toenarm is moving on a circle too. Same rules apply.
Your "virtual pivot" is so virtual that nothing rotates around it. It is significant in only one sense: the centerline of the catridge must go through it.
The auxiliary arms with "primary" and "secondary" pivots provide just that, but they do not have any role in the play of forces on the stylus.
The forces acting on the stylus are determined only by the friction force and the fact that the stylus moves on a Thales circle. The formula for the skating force is the same as for a traditional tonearm:
"I have asked him which pivot he used to do such a calculation. But I get no answer."
I wrote for instance that the Birch tonearm rotates around the center of the Thales circle. Do you understand that? You got your answer!
The stylus is moving on the Thales circle.
The stylus of a traditional toenarm is moving on a circle too. Same rules apply.
Your "virtual pivot" is so virtual that nothing rotates around it. It is significant in only one sense: the centerline of the catridge must go through it.
The auxiliary arms with "primary" and "secondary" pivots provide just that, but they do not have any role in the play of forces on the stylus.
The forces acting on the stylus are determined only by the friction force and the fact that the stylus moves on a Thales circle. The formula for the skating force is the same as for a traditional tonearm:
Last edited:
I proved with a simulation how Birch tonearms work. They rotate simultanously around the center of the Thales circle AND the stylus.
You do not understand this as anything else I write.
You do not understand this as anything else I write.
The video is not showing Birch-style arm movements at all. It merely shows the characters of Thales circle.
If I use the regular term, the thick red lines are the effective length of a tonearm. Its length changes. It is NOT a Birch-style tonearm. If you insist to find a tonearm based on such movements, it is an early Thales tonearm.
A Birch-style tonearm is different although Birch-style tonearm utilities Thales circle as well.
Your calculation is completely based on your misunderstandings.
If I use the regular term, the thick red lines are the effective length of a tonearm. Its length changes. It is NOT a Birch-style tonearm. If you insist to find a tonearm based on such movements, it is an early Thales tonearm.
A Birch-style tonearm is different although Birch-style tonearm utilities Thales circle as well.
Your calculation is completely based on your misunderstandings.
For the interested reader:
all tonearms based on the Thales circle (e.g. the Birch arm) are characterized by
1. the Thales circle on which the stylus moves
2. the centerline of the cartridge which goes through the P3 point.
The Birch tonearm is just one realisation, several others are possible with varying precision (Thales Original, Reed 5T, Schröder LT a. o.),
All move according to my simulation, otherwise they were not follow the Thales circle or they would not be tangential.
all tonearms based on the Thales circle (e.g. the Birch arm) are characterized by
1. the Thales circle on which the stylus moves
2. the centerline of the cartridge which goes through the P3 point.
The Birch tonearm is just one realisation, several others are possible with varying precision (Thales Original, Reed 5T, Schröder LT a. o.),
All move according to my simulation, otherwise they were not follow the Thales circle or they would not be tangential.
So, what is the angle in the formula Fsk=Ffr x sin( a)?2. the centerline of the cartridge which goes through the P3 point.
Is your above statement still correct?They rotate simultanously around the center of the Thales circle AND the stylus.
- Home
- Source & Line
- Analogue Source
- Tightly Strung