a small correction john,the height of the platter is adjusted more so the magnets are centered in relation to the motor windings rather than the speed detector heads.
Good Man Jamie,
Any thoughts on the Tolerance for the Height Setting +/- ??
Am I correct with my suggestion to be exact as the factory setting.
Any thoughts on the Tolerance for the Height Setting +/- ??
Am I correct with my suggestion to be exact as the factory setting.
that i couldn't tell you as our mutual friend assembled my motor unit in your chassis and then gave me it back as a ready to go item
Guys, you are talking in riddles - so let me ask: is there a source available where parts to "upgrade" the bearing can be obtained?
I did not post that with no thought --a major incident occurred to many engineers in the UK and was highly reported at the time in EW a long time ago.
The interest centered on a now long dead electronic design engineer but a person who now has worldwide fame in the electronic field as relating to the UK, his life story and films/plays were made about him and he is in the history books . I would rather not say his name but the information gathered from many engineers caused a certain person to become rich.
The interest centered on a now long dead electronic design engineer but a person who now has worldwide fame in the electronic field as relating to the UK, his life story and films/plays were made about him and he is in the history books . I would rather not say his name but the information gathered from many engineers caused a certain person to become rich.
The Individual who has produced the Parts being used by Jamie, is as off Two weeks ago willing to produce the Materials for a Couple of Bearings.
One is my TT that is in their possession and I also believe one that is based in Germany.
The Engineer is retired and has a busy schedule with their other interests in Tonearms and TT's.
It was my curiosity about the TTS 8000 Bearing Housing Issues that got this Person Pondering the issue.
I supplied a Donor TT and hence the Parts have been produced, as seen with the method now in use on Jamie's TT.
Myself and the Engineer have discussed a Design for the TTS 8000's Entirety of the Bearing Assembly.
The works completed to date and in use are a proportion of the works that are to be undertaken.
It was also during the time that my TTS 8000 has been serving as a Donor, that the Platter was identified by the Engineer as being unstable when seated on the Platter Spindle.
There is a Method being looked into to overcome this Problem, and this will be one further measure to be added to the outstanding methods to be produced.
It is not possible to offer any answers, as to whether there will be Parts made available.
This will need to be taken up with the Engineer, which I can do to see how the request is received.
As a Side my TT is with the Engineer and Jamie's Bearing Housing was with the Engineer, as I had seen it on a visit.
It is not known if a TTS 8000 Bearing Housing and Spindle will be required to be made available to the Engineer ??
In my mind there are potentially more TTS 8000's that have the condition being discussed within this Thread.
This Thread is solely about offering a opportunity to identify if a TTS 8000 is with the condition, and hopefully various Methods to overcome the concerning condition will be made known.
When it comes to the TTS 8000 the method now in use with Jamie, might be unfamiliar to this model of TT, but it incorporates Modern Materials to produce a version of the methods being used for successfully improving other Vintage TT's.
I am not sure where the notion of a Book being produced is coming from, or who is the suspected author.
One is my TT that is in their possession and I also believe one that is based in Germany.
The Engineer is retired and has a busy schedule with their other interests in Tonearms and TT's.
It was my curiosity about the TTS 8000 Bearing Housing Issues that got this Person Pondering the issue.
I supplied a Donor TT and hence the Parts have been produced, as seen with the method now in use on Jamie's TT.
Myself and the Engineer have discussed a Design for the TTS 8000's Entirety of the Bearing Assembly.
The works completed to date and in use are a proportion of the works that are to be undertaken.
It was also during the time that my TTS 8000 has been serving as a Donor, that the Platter was identified by the Engineer as being unstable when seated on the Platter Spindle.
There is a Method being looked into to overcome this Problem, and this will be one further measure to be added to the outstanding methods to be produced.
It is not possible to offer any answers, as to whether there will be Parts made available.
This will need to be taken up with the Engineer, which I can do to see how the request is received.
As a Side my TT is with the Engineer and Jamie's Bearing Housing was with the Engineer, as I had seen it on a visit.
It is not known if a TTS 8000 Bearing Housing and Spindle will be required to be made available to the Engineer ??
In my mind there are potentially more TTS 8000's that have the condition being discussed within this Thread.
This Thread is solely about offering a opportunity to identify if a TTS 8000 is with the condition, and hopefully various Methods to overcome the concerning condition will be made known.
When it comes to the TTS 8000 the method now in use with Jamie, might be unfamiliar to this model of TT, but it incorporates Modern Materials to produce a version of the methods being used for successfully improving other Vintage TT's.
I am not sure where the notion of a Book being produced is coming from, or who is the suspected author.
Chapter 2. 🙂
So today i inspected my other TTS and found the same symptom they all suffer from. The oil leak!
I cleaned all the parts and re oiled them and put them back together to see where it had failed.
No leak through the freshly thread sealed thrust pad but lots in the bottom of the housing.
The rubber seal had given in. It measures ID 16mm x OD 23mm x 3.75 mm thick.
I think 4mm thick would be more the right size and allow it to seal better.
There doesn't seemed to be much on the web so it may be a case of having some made or cutting one out from sheet stock.
Its made from a hard rubber type material but what that is is anyone's guess.
So today i inspected my other TTS and found the same symptom they all suffer from. The oil leak!
I cleaned all the parts and re oiled them and put them back together to see where it had failed.
No leak through the freshly thread sealed thrust pad but lots in the bottom of the housing.
The rubber seal had given in. It measures ID 16mm x OD 23mm x 3.75 mm thick.
I think 4mm thick would be more the right size and allow it to seal better.
There doesn't seemed to be much on the web so it may be a case of having some made or cutting one out from sheet stock.
Its made from a hard rubber type material but what that is is anyone's guess.
What the seal is made from is down to the PSI (pressure ) it has to contain plus the rotational value .
While the revolutions on a record deck aren't fast filling it up with oil and then expecting an ordinary rated seal of zero PSI will not keep the oil in , so using oil to make up for a worn bearing is a waste of time.
Low friction NBR/Nitrile /FKM/Viton etc are the materials to use .
Nitrile is=acrylonitrile and butadiene obviously synthetic --not "rubber " in the general sense of --tapped of a tree somewhere .
While the revolutions on a record deck aren't fast filling it up with oil and then expecting an ordinary rated seal of zero PSI will not keep the oil in , so using oil to make up for a worn bearing is a waste of time.
Low friction NBR/Nitrile /FKM/Viton etc are the materials to use .
Nitrile is=acrylonitrile and butadiene obviously synthetic --not "rubber " in the general sense of --tapped of a tree somewhere .
plus the rotational value .
Not that type of seal. It's literally a rubber washer between the bearing housing and the outer casing.
you may have a point there,in fact it does make me wonder considering that oilites were used from the factory if they ever put oi in them originally. perhaps just a lite coat on the spindle and thats all.
when topped up with oil the spindle takes ages to sink down to the thrust washer so perhaps its no wonder the seal just gives up.
by the way duncan the seal is not in contact with the spindle like a traditional oil seal,its just a flat washer that is sandwiched between the 2 components.
when topped up with oil the spindle takes ages to sink down to the thrust washer so perhaps its no wonder the seal just gives up.
by the way duncan the seal is not in contact with the spindle like a traditional oil seal,its just a flat washer that is sandwiched between the 2 components.
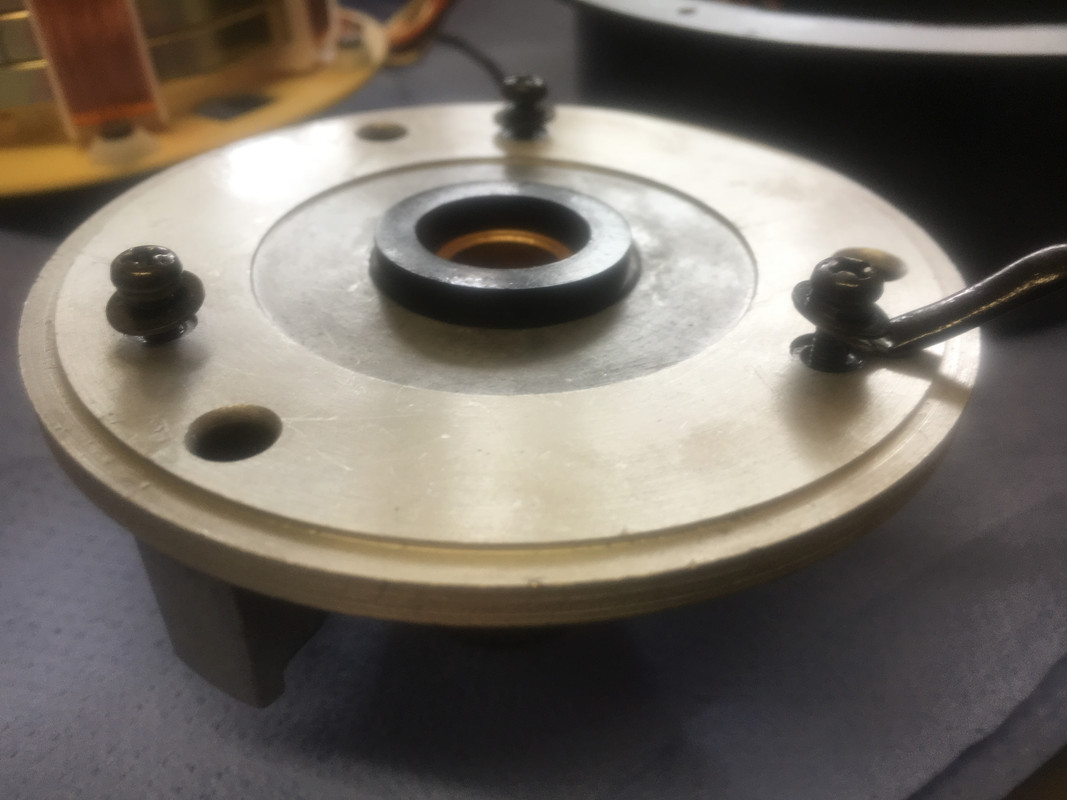
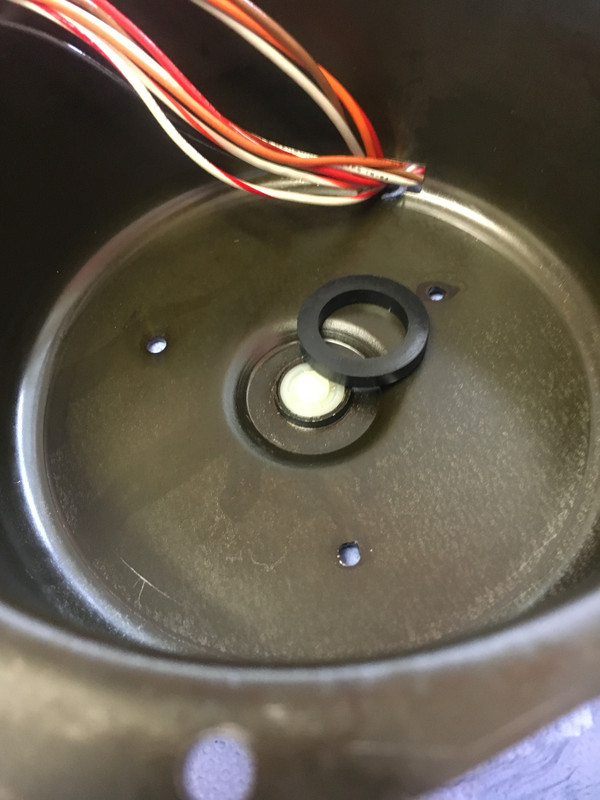
Thanks Jamie and John, now we are cooking...and good to know the size of the befamed 0-ring, so I dont have to rip the table apart for measurement.
So we have to be patient or find some other skilled person to do the job, unfortunately I dont know such person.
To make things clear for the ones who are not owners of a TTS8000, in this link you can see how it is all put together:
https://www.lencoheaven.net/forum/index.php?topic=32526.15
So it sits between the black bowl and the bearing assembly, only pressed together with 3 smallish screws. Maybe a common 0 ring would do the trick if thick enough, maybe even 4.5mm if soft enough to give a little under pressure.
I remember from my Lenco experiments that even a worn bearing could be brought back to silent life when the bearing was sealed and completely filled with oil.
Still i would prefer new bushings with less play.
So we have to be patient or find some other skilled person to do the job, unfortunately I dont know such person.
To make things clear for the ones who are not owners of a TTS8000, in this link you can see how it is all put together:
https://www.lencoheaven.net/forum/index.php?topic=32526.15
So it sits between the black bowl and the bearing assembly, only pressed together with 3 smallish screws. Maybe a common 0 ring would do the trick if thick enough, maybe even 4.5mm if soft enough to give a little under pressure.
I remember from my Lenco experiments that even a worn bearing could be brought back to silent life when the bearing was sealed and completely filled with oil.
Still i would prefer new bushings with less play.
you may have a point there,in fact it does make me wonder considering that oilites were used from the factory if they ever put oi in them originally. perhaps just a lite coat on the spindle and thats all.
when topped up with oil the spindle takes ages to sink down to the thrust washer so perhaps its no wonder the seal just gives up.
by the way duncan the seal is not in contact with the spindle like a traditional oil seal,its just a flat washer that is sandwiched between the 2 components.
Yes it depends on the material the seal is made out of normal cheap seals are zero pressure ,if you want pressurized seals they have to be a certain synthetic material and yes topped up with oil hydraulic action slows down the insertion rate but it will leak even if its not part of the rotation of the spindle as rotation is just an additional factor to take into consideration and made out of rubber.
Rubber and synthetic seals are usually made at the same factory but a big difference in price if you want it to resist hydraulic pressure --watch out when you are on Alibaba and a Chinese advert says "seals for sale".
If the guys on this thread really are taking this seriously then buy from a well known industrial manufacturing firm there are plenty of them I checked .
A thought on the Square Walled O Ring, it looks like the most Simple Solution would be to trial with a Modern Seal Ring.
The Link is to a suppliers product descriptions of the Materials referred to by duncan2 .
An alternative Option, and slightly more complex one.
Is one that I was putting on Paper in the earliest investigations, which based towards having the New Used O Rings Housed in a Purpose Produced Machined Metal Part.
It can be 'almost identical' in the Dimensions of the Existing Square Walled O Ring.
The goal at this time was to attempt to create a Improved Seal on the Sumps Side Wall,
but as importantly keep the 'suspected condition' to remain in place, where the contact between the Bearing Housing and Bowl is separated with a Rubber Part as the Interface.
The roughed out design was for the Metal Parts Top and Bottom Surfaces to be machined to receive O Rings.
The faces can be rebated to have Two O Rings with a Cross Section of Approx' 2mm Seated in the rebates.
The Two O Rings will produce Two Lines of Defence against a Leeching Lubricant.
Using Jamie's supplied Dimensions, the Outer O Ring could have a OD of approx' 20mm , the Inner O Ring could have a ID of approx' 18mm.
A Juggle with the OD Diameter of the Machined Part and the O Rings Diameters and Cross Section might just produce a Part that offers a Two Lined Defence that proves to have the wanted affect.
I never quite completed this as a Design to be presented to the Engineer for their consideration, as another option to overcome my concerns came to mind that would serve to improve on a Variety of issues being pondered.
When these were discussed with the Engineer in their entirety with the Design Ideas, they were seen as worthy of producing the Necessary Parts to achieve the Working Prototype.
As a side: I have for quite some time had a query in keeping with the above?
It relates to the Square Walled O Ring Interface.
I have a design on Paper to overcome my concerns, whether these are proven or unproven, I will be looking to have my design materialise, as it has other wanted properties to be incorporated into the overall redesign for the TT.
The Square Walled O Ring from recollection is quite a Hard Material, and it is oversized to the Spacing it is housed in, I feel it is correct to suggest it is intended to be a compressed part, at the time of Attaching and fastening the Bearing Housing to the Pressed Bowl.
I have viewed this Rubber Part as having Two Purposes, one is to serve the Purpose as the Side Wall within the Sump and retain a Lubricant.
The other is more of a Conjecture, in being that it has served as a Damping and had a influence on the SQ.
The idea of it being a Damper and the Harness of the Part, leads to the possibility that the Square Walled O Ring does not compress to the condition that will allow the Metal to Metal Contact between the Bearing Housing Base and Bowl to be achieved, and a Void my be present between the Two Metal Parts.
As said this is conjecture, but if the suspicion is proved to be the case, the Bearing Housing is seated on a Rubber Mount and the Bearing Housing has not got a Base Mounting that is rigid, it can yield when being met with the Forces Applied through the TT's Operation.
The idea of the use of Shim Packing in a Void 'if present' would be to produce a Rigid Mount for the Bearing Housing.
The risk in using a Shim Packing in this place, is that the Sonic Signature of the TT, might change as the Damping influence is possibly being lessened or even eliminated.
Any investigation undertaken and if need be methods incorporated to ensure the Bearing Housing is adequately coupled at the Base to the Support.
Would then only leave the Pressed Bowl as the most likely Part to Yield when the TT is operational.
When investigating the Pressed Bowl Material and the method of attachment to the Chassis it does not take a lot to see that this is a serious area to raise a concern.
As said before the Pressed Bowl on the TTS 8000 is without doubt looking to be the Thinnest Gauge of Metal I have witnessed when recollecting the other Bowl Materials of TT's with a Similar Bowl Design.
Viton / FKM vs Nitrile: Which material is right for your application?
The Link is to a suppliers product descriptions of the Materials referred to by duncan2 .
An alternative Option, and slightly more complex one.
Is one that I was putting on Paper in the earliest investigations, which based towards having the New Used O Rings Housed in a Purpose Produced Machined Metal Part.
It can be 'almost identical' in the Dimensions of the Existing Square Walled O Ring.
The goal at this time was to attempt to create a Improved Seal on the Sumps Side Wall,
but as importantly keep the 'suspected condition' to remain in place, where the contact between the Bearing Housing and Bowl is separated with a Rubber Part as the Interface.
The roughed out design was for the Metal Parts Top and Bottom Surfaces to be machined to receive O Rings.
The faces can be rebated to have Two O Rings with a Cross Section of Approx' 2mm Seated in the rebates.
The Two O Rings will produce Two Lines of Defence against a Leeching Lubricant.
Using Jamie's supplied Dimensions, the Outer O Ring could have a OD of approx' 20mm , the Inner O Ring could have a ID of approx' 18mm.
A Juggle with the OD Diameter of the Machined Part and the O Rings Diameters and Cross Section might just produce a Part that offers a Two Lined Defence that proves to have the wanted affect.
I never quite completed this as a Design to be presented to the Engineer for their consideration, as another option to overcome my concerns came to mind that would serve to improve on a Variety of issues being pondered.
When these were discussed with the Engineer in their entirety with the Design Ideas, they were seen as worthy of producing the Necessary Parts to achieve the Working Prototype.
As a side: I have for quite some time had a query in keeping with the above?
It relates to the Square Walled O Ring Interface.
I have a design on Paper to overcome my concerns, whether these are proven or unproven, I will be looking to have my design materialise, as it has other wanted properties to be incorporated into the overall redesign for the TT.
The Square Walled O Ring from recollection is quite a Hard Material, and it is oversized to the Spacing it is housed in, I feel it is correct to suggest it is intended to be a compressed part, at the time of Attaching and fastening the Bearing Housing to the Pressed Bowl.
I have viewed this Rubber Part as having Two Purposes, one is to serve the Purpose as the Side Wall within the Sump and retain a Lubricant.
The other is more of a Conjecture, in being that it has served as a Damping and had a influence on the SQ.
The idea of it being a Damper and the Harness of the Part, leads to the possibility that the Square Walled O Ring does not compress to the condition that will allow the Metal to Metal Contact between the Bearing Housing Base and Bowl to be achieved, and a Void my be present between the Two Metal Parts.
As said this is conjecture, but if the suspicion is proved to be the case, the Bearing Housing is seated on a Rubber Mount and the Bearing Housing has not got a Base Mounting that is rigid, it can yield when being met with the Forces Applied through the TT's Operation.
The idea of the use of Shim Packing in a Void 'if present' would be to produce a Rigid Mount for the Bearing Housing.
The risk in using a Shim Packing in this place, is that the Sonic Signature of the TT, might change as the Damping influence is possibly being lessened or even eliminated.
Any investigation undertaken and if need be methods incorporated to ensure the Bearing Housing is adequately coupled at the Base to the Support.
Would then only leave the Pressed Bowl as the most likely Part to Yield when the TT is operational.
When investigating the Pressed Bowl Material and the method of attachment to the Chassis it does not take a lot to see that this is a serious area to raise a concern.
As said before the Pressed Bowl on the TTS 8000 is without doubt looking to be the Thinnest Gauge of Metal I have witnessed when recollecting the other Bowl Materials of TT's with a Similar Bowl Design.
Viton / FKM vs Nitrile: Which material is right for your application?
In relation to the Group Buy request for replacement Bearing Parts.
The Inquiry that I have made has been met with an offer to Produce 10 Pairs of Bushes made from the Torlon Material.
These will be machined to be match the Two TT's that have been worked with,
so hence a OD of 16mm to fit the Bearing Housing, and machined to work with a 11mm Spindle.
The Torlon Bushes will be offered as a Push Fit Exchange for the existing bushes.
When the Torlon Bushes are set in the Bearing Housing, an additional DIY Treatment using a 11mm reamer will be need the be carried out, to complete the fitting process.
The added treatment is required, as the ID of the Torlon Bush will decrease slightly once the Push Fit has happened.
I have been informed a Hand Reamer will be a good enough Tool to use, and that I could be entrusted to carry out the additional treatment, which indirectly has the meaning, that using a Hand Reamer does not require a honed skill set.
A 11mm Hand Reamer as the most basic tool, does not seem to have too much of a cost attached to it.
It would be great if the Group Buy could meet the Order for the Production of Ten Torlon Bush Pairs, as this is the requested quantity for a Group Buy from the Engineer.
The supplied Ball Park Figure for the Cost of the Parts minus Shipping is very fair and I am sure will be easily accepted.
The final cost can be made known for the Pairs of Torlon Bushes if a Group Buy of Ten Pairs is achieved.
Can any queries on this option, or the interest in this option be made known ?
The Inquiry that I have made has been met with an offer to Produce 10 Pairs of Bushes made from the Torlon Material.
These will be machined to be match the Two TT's that have been worked with,
so hence a OD of 16mm to fit the Bearing Housing, and machined to work with a 11mm Spindle.
The Torlon Bushes will be offered as a Push Fit Exchange for the existing bushes.
When the Torlon Bushes are set in the Bearing Housing, an additional DIY Treatment using a 11mm reamer will be need the be carried out, to complete the fitting process.
The added treatment is required, as the ID of the Torlon Bush will decrease slightly once the Push Fit has happened.
I have been informed a Hand Reamer will be a good enough Tool to use, and that I could be entrusted to carry out the additional treatment, which indirectly has the meaning, that using a Hand Reamer does not require a honed skill set.
A 11mm Hand Reamer as the most basic tool, does not seem to have too much of a cost attached to it.
It would be great if the Group Buy could meet the Order for the Production of Ten Torlon Bush Pairs, as this is the requested quantity for a Group Buy from the Engineer.
The supplied Ball Park Figure for the Cost of the Parts minus Shipping is very fair and I am sure will be easily accepted.
The final cost can be made known for the Pairs of Torlon Bushes if a Group Buy of Ten Pairs is achieved.
Can any queries on this option, or the interest in this option be made known ?
John, that's great news! I would be in for one pair for sure.
Also interesting what you said about the rubber ring. It didn't cross my mind that it could act as a decoupling device to avoid direct contact between the two metal surfaces.
Although it is still coupled with those 3 screws at the bottom of the black bowl.
This ring of course should have an impact on sound quality, so its material matters as John said
Some strange engineering there from Sony...
Also interesting what you said about the rubber ring. It didn't cross my mind that it could act as a decoupling device to avoid direct contact between the two metal surfaces.
Although it is still coupled with those 3 screws at the bottom of the black bowl.
This ring of course should have an impact on sound quality, so its material matters as John said
Some strange engineering there from Sony...
- Home
- Source & Line
- Analogue Source
- Sony TTS 8000 (All in Discussion)