Well, all that can't be worse that meeting a guy at a club and trying to make it out with you.
I think you guys are better at providing information related to acoustics than recreational drug use.
Wow, John, incredible story, but from my decades of experience in China completely believable. China is, in fact, basically a lawless country where anything goes if you have the bucks. Heck the wife of Bo Shi Lai thought that murder was fine as long as she had enough money. Unlucky for her, it was a foreigner - it's not the same thing outside of China!! You can't just buy your way out of any situation in the west.
You need more bucks, the and the right people, plus the right political scheme in the west. Level of difficulty is raised, but not impossible.
You can't just buy your way out of any situation in the west.
Pretty close though. Money still talks. Compare conviction rates to income brackets and you'll see pretty clearly that enough cash can buck the justice system. Hell, plenty of lowlifes with lots of cash are ensuring that the theft they perform is legal. Remember that congress has legal insider trading. Yep, they write the laws and can benefit from picking winners. 99% crooks is perhaps understated.
I'm thinking that I chose the wrong specialty in chemistry!
Its not too late! Breaking Bad give you a perfect template for success.
Pretty close though. Money still talks. Compare conviction rates to income brackets and you'll see pretty clearly that enough cash can buck the justice system.
Agreed, but it is nowhere near the same scale as in China. In China you can look up the average bribe needed to buy a specific public office. No need to pay too much!
Bo Shi Lai had homes all over the world and his wife was trying to transport out several million dollars. This on his official salary of about $2000 a month.
*snip*
Fair enough!
*/snip*Agreed, but it is nowhere near the same scale as in China. In China you can look up the average bribe needed to buy a specific public office. No need to pay too much!
Fair enough!
Since I accidentally turned this into the 'drugs and waveguides' thread, I'll try to get things back on topic.
While working in the garage today, I figured out a way to improve the throat of a waveguide, by using hemp. (See what I did there?)
Here's some background on the problem:
At the throat of a waveguide, we want a really smooth transition from compression driver to waveguide. This is easy to do with a commercial waveguide, but when you build your own, it is very tricky.
Back when I first started building waveguides in fiberglass, I would make the throat the same size as the compression driver.
This doesn't work so great, because you always have to file down the throat, to make sure it's a perfect match. So when you file down a 1" throat, you end up with a throat that's a little too big.
The solution that I've used for the past couple years is to simply make the throat a little too small, and then I run a drill bit right down the middle. This gets you a perfectly symmetrical 1" opening.
Unfortunately, this solution isn't perfect, because you need a material for the horn that is both strong and substantial. Wood would work great, but wood isn't ideal for the complex shape of a waveguide, particularly at the throat.
Fiberglass is so so. My main gripe with fiberglass is that it takes a decent amount to build up enough thickness. Fiberglass mat works, but it isn't as strong as fabric.
Carbon fiber works great, but carbon fiber is expensive.
Ideally, I would want something like carbon fiber, but cheaper. Easier to work with would be a nice bonus.
In order to come up with a good solution, it's worthwhile to consider why carbon fiber works so well. In my opinion, carbon fiber works well because the strands are much much smaller than glass. Given a fixed amount of fiberglass or carbon fiber, the carbon fiber is going to have more strands, because the strands are smaller in diameter. ( 5–10 μm versus 9-13 μm)
Bottom line:
A throat made of carbon fiber produces a smoother finish than a throat made of fiberglass.
Here's an alternative to CF, that seems to work much better than I'd dreamed.
First, you go to a craft store and buy a ball of hemp yarn. The reason that we want hemp is because hemp is strong, and it has a lot of surface area, due to the rough microscopic nature of the strands.
Second, get yourself some gorilla glue.
At this point, we have about $12 invested. To do the same with epoxy and carbon fiber would require a trip to TAP Plastics, and about $100. (Admittedly, that'll buy you a lot of epoxy.)
Now take the hemp and run it under the faucet. We're getting it wet because moisture makes gorilla glue cure faster.
Now the messy part. Put some gloves on, put the hemp yarn into your hand, and pour some gorilla glue onto the yarn. Now really squeeze it! We want the glue to be thoroughly saturated into the yarn.
If you've made it this far, you've now created the hemp equivalent of prepreg carbon fiber. (The way that most carbon fiber is used these days is with the epoxy impregnated into the carbon fiber, to maximize strength by minimizing the amount of epoxy.)
I got the idea from Calfee bicycles. This is how Calfee bonds bamboo to bamboo. (I believe they use epoxy, not polyurethane glue.)
There's some neat advantages to gorilla glue though:
1) The huge one is getting the perfect mix every time. In my fiberglass projects I've found that the strength of fiberglass varies a lot on whether the epoxy is mixed perfectly, and the perfect mix depends on what temperature it is outside! (ugh.)
2) I was astonished at how quickly the gorilla glue cures when you add water to the hemp. What would normally take 24 hours took about one.
3) When the water/hemp/gorilla glue cures, it's hard like concrete I simply couldn't believe how strong it was. It's insane. As demonstrated by Calfee, it can take a serious beating.
4) The volume of the hemp is a lot greater than carbon fiber or glass, which is handy when you're trying to lay up something quickly. (This could also be a downside of course, if you needed a very thin layer this is not the best method.)
5) Probably one of the neatest things that you can do with this trick is to leverage loops and knots and braids. Try doing THAT with carbon fiber! This is an important advantage, as companies like Ferrari and Lamborghini have demonstrated that the orientation of carbon fiber plays a large role in it's strength. With hemp you can take this to another level, by literally tying two pieces together. (For example, if you are bonding a mounting plate to a horn, you can drill holes through the mounting plate and tie the two pieces together, prior to adding the glue.)
Basically the ideal material for the horn throat is strong, easily sanded, and produces a smooth finish. Carbon fiber fits the bill. Fiberglass less so. Bond is fairly terrible, because bondo has virtually no strength. I can't count the number of waveguides where the bondo simply delaminated from the waveguide.
Hemp works pretty darn well, and is an interesting and inexpensive alternative to carbon fiber.
While working in the garage today, I figured out a way to improve the throat of a waveguide, by using hemp. (See what I did there?)
Here's some background on the problem:

At the throat of a waveguide, we want a really smooth transition from compression driver to waveguide. This is easy to do with a commercial waveguide, but when you build your own, it is very tricky.
Back when I first started building waveguides in fiberglass, I would make the throat the same size as the compression driver.
This doesn't work so great, because you always have to file down the throat, to make sure it's a perfect match. So when you file down a 1" throat, you end up with a throat that's a little too big.
The solution that I've used for the past couple years is to simply make the throat a little too small, and then I run a drill bit right down the middle. This gets you a perfectly symmetrical 1" opening.
Unfortunately, this solution isn't perfect, because you need a material for the horn that is both strong and substantial. Wood would work great, but wood isn't ideal for the complex shape of a waveguide, particularly at the throat.
Fiberglass is so so. My main gripe with fiberglass is that it takes a decent amount to build up enough thickness. Fiberglass mat works, but it isn't as strong as fabric.
Carbon fiber works great, but carbon fiber is expensive.
Ideally, I would want something like carbon fiber, but cheaper. Easier to work with would be a nice bonus.
In order to come up with a good solution, it's worthwhile to consider why carbon fiber works so well. In my opinion, carbon fiber works well because the strands are much much smaller than glass. Given a fixed amount of fiberglass or carbon fiber, the carbon fiber is going to have more strands, because the strands are smaller in diameter. ( 5–10 μm versus 9-13 μm)
Bottom line:
A throat made of carbon fiber produces a smoother finish than a throat made of fiberglass.
Here's an alternative to CF, that seems to work much better than I'd dreamed.
First, you go to a craft store and buy a ball of hemp yarn. The reason that we want hemp is because hemp is strong, and it has a lot of surface area, due to the rough microscopic nature of the strands.
Second, get yourself some gorilla glue.
At this point, we have about $12 invested. To do the same with epoxy and carbon fiber would require a trip to TAP Plastics, and about $100. (Admittedly, that'll buy you a lot of epoxy.)
Now take the hemp and run it under the faucet. We're getting it wet because moisture makes gorilla glue cure faster.
Now the messy part. Put some gloves on, put the hemp yarn into your hand, and pour some gorilla glue onto the yarn. Now really squeeze it! We want the glue to be thoroughly saturated into the yarn.
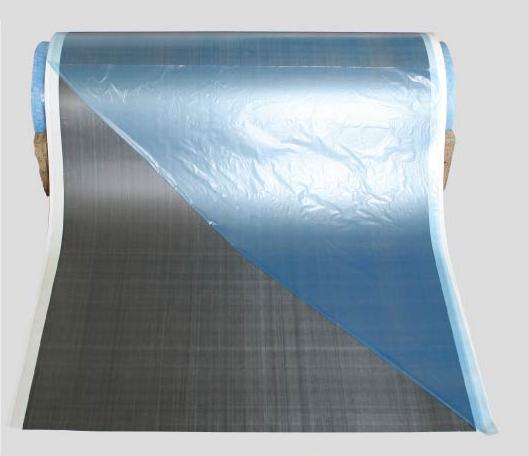
If you've made it this far, you've now created the hemp equivalent of prepreg carbon fiber. (The way that most carbon fiber is used these days is with the epoxy impregnated into the carbon fiber, to maximize strength by minimizing the amount of epoxy.)

I got the idea from Calfee bicycles. This is how Calfee bonds bamboo to bamboo. (I believe they use epoxy, not polyurethane glue.)
There's some neat advantages to gorilla glue though:
1) The huge one is getting the perfect mix every time. In my fiberglass projects I've found that the strength of fiberglass varies a lot on whether the epoxy is mixed perfectly, and the perfect mix depends on what temperature it is outside! (ugh.)
2) I was astonished at how quickly the gorilla glue cures when you add water to the hemp. What would normally take 24 hours took about one.
3) When the water/hemp/gorilla glue cures, it's hard like concrete I simply couldn't believe how strong it was. It's insane. As demonstrated by Calfee, it can take a serious beating.
4) The volume of the hemp is a lot greater than carbon fiber or glass, which is handy when you're trying to lay up something quickly. (This could also be a downside of course, if you needed a very thin layer this is not the best method.)
5) Probably one of the neatest things that you can do with this trick is to leverage loops and knots and braids. Try doing THAT with carbon fiber! This is an important advantage, as companies like Ferrari and Lamborghini have demonstrated that the orientation of carbon fiber plays a large role in it's strength. With hemp you can take this to another level, by literally tying two pieces together. (For example, if you are bonding a mounting plate to a horn, you can drill holes through the mounting plate and tie the two pieces together, prior to adding the glue.)
Basically the ideal material for the horn throat is strong, easily sanded, and produces a smooth finish. Carbon fiber fits the bill. Fiberglass less so. Bond is fairly terrible, because bondo has virtually no strength. I can't count the number of waveguides where the bondo simply delaminated from the waveguide.
Hemp works pretty darn well, and is an interesting and inexpensive alternative to carbon fiber.
Last edited:
Composite material are amazing these days. Here is one that I came across by accident. It was so hard that it wore out several sanding disks just trying to sand it down some.
I sometimes buy cheap ceiling tiles at Home depot to build up into complex shapes that are light and easy to manipulate. I needed to build up an area that was low once so I took some scrap ceiling tile that I had and soaked it in water so that it came apart. Then I added some Titebond II glue to the wet mixture to make a paste, which I smeared onto the form. Once dry this stuff was so hard that it wore out several sanding disks before I got even 1/8" taken off. I simply could not believe how hard it was. And, as you say, it was cheap!.
Polyurethane glue (Gorilla glue) is not nearly as hard as Titebond when it is dry and polyurethane tends to expand on curing which I don't like. I'd prefer a little contraction.
My cast baffles are made with several different composites that I have developed over the years.
Many people don't realize that carbon fiber does not get to its full strength unless it is autoclaved, which not many people can do. Otherwise it is just a little better than fiberglass.
I sometimes buy cheap ceiling tiles at Home depot to build up into complex shapes that are light and easy to manipulate. I needed to build up an area that was low once so I took some scrap ceiling tile that I had and soaked it in water so that it came apart. Then I added some Titebond II glue to the wet mixture to make a paste, which I smeared onto the form. Once dry this stuff was so hard that it wore out several sanding disks before I got even 1/8" taken off. I simply could not believe how hard it was. And, as you say, it was cheap!.
Polyurethane glue (Gorilla glue) is not nearly as hard as Titebond when it is dry and polyurethane tends to expand on curing which I don't like. I'd prefer a little contraction.
My cast baffles are made with several different composites that I have developed over the years.
Many people don't realize that carbon fiber does not get to its full strength unless it is autoclaved, which not many people can do. Otherwise it is just a little better than fiberglass.
Last edited:
Earl,
Coming out of aerospace and many years of composite and plastics development I can say that some of what you assume is very incorrect. Carbon fiber and fiberglass are not even close in material properties. Fiber size or what are called bundles are made in many different variation of fiber diameter. The modulus of standard carbon fiber is at least 10 times the stiffness of glass for an equivalent thickness or fiber size, night and day different in practical usage. Yes most polyurethanes can expand in some instances but this is actually the opposite of what most molded polyurethanes do in reality. They shrink as almost all organic plastic materials do after cure, this is why we always use shrinkage rates when designing these parts. To say that you have to use an autoclave to cure a carbon composite part is not correct. The real reason for using the autoclave is consolidation of the composite, a low void fraction of resin to fiber ratio. This is one of the only ways to achieve extremely dense and non porous composites that can not contain any voids where failure modes occur due to stress loading. But that has little to nothing to do with the hardness of the composite beyond that void ratio. I could go on but I will see if I can just point to a web site that will give more technical answers to what some may have about these materials.
Coming out of aerospace and many years of composite and plastics development I can say that some of what you assume is very incorrect. Carbon fiber and fiberglass are not even close in material properties. Fiber size or what are called bundles are made in many different variation of fiber diameter. The modulus of standard carbon fiber is at least 10 times the stiffness of glass for an equivalent thickness or fiber size, night and day different in practical usage. Yes most polyurethanes can expand in some instances but this is actually the opposite of what most molded polyurethanes do in reality. They shrink as almost all organic plastic materials do after cure, this is why we always use shrinkage rates when designing these parts. To say that you have to use an autoclave to cure a carbon composite part is not correct. The real reason for using the autoclave is consolidation of the composite, a low void fraction of resin to fiber ratio. This is one of the only ways to achieve extremely dense and non porous composites that can not contain any voids where failure modes occur due to stress loading. But that has little to nothing to do with the hardness of the composite beyond that void ratio. I could go on but I will see if I can just point to a web site that will give more technical answers to what some may have about these materials.
Do you think this stuff can be used to strengthen injection molded plastic waveguides ? I'm afraid it is too rigid and not enough damped.Basically the ideal material for the horn throat is strong, easily sanded, and produces a smooth finish. Carbon fiber fits the bill. Fiberglass less so. Bond is fairly terrible, because bondo has virtually no strength. I can't count the number of waveguides where the bondo simply delaminated from the waveguide.
gtb,
It has a lot to do with what type of plastic was used to produce the horn in the first place. Some plastic are very hard to bond to and others very easy. If you take a small amount of epoxy resin you can see if it will stick to the plastic without easily peeling off. If it does you should be able to reinforce the plastic horn you are talking about. I would be very careful about using any polyester resin on those plastic horns as it can attack and dissolve some plastics.
It has a lot to do with what type of plastic was used to produce the horn in the first place. Some plastic are very hard to bond to and others very easy. If you take a small amount of epoxy resin you can see if it will stick to the plastic without easily peeling off. If it does you should be able to reinforce the plastic horn you are talking about. I would be very careful about using any polyester resin on those plastic horns as it can attack and dissolve some plastics.
I tried a bi component epoxy paste and it bonded very well to the plastic. It dry very fast even with a big thickness and is very strong. But it is also very expansive and I not sure if it is damped enough to reinforce the plastic with good acoustic properties.
Earl,
The modulus of standard carbon fiber is at least 10 times the stiffness of glass for an equivalent thickness or fiber size.
this is simple not true
first google link i find - besides own practical experiences
Comparing the characteristics of Glass, Kevlar (Aramid) and Carbon Fiber
In reality you dont even utilize the Young's Modulus of carbon to get full advantage over glass because the epoxy bond is not perfect - it flexes somehow.
10 times is just BS to make 20x cost increase acceptable. Same thickness laminate is max about 2 times stiff. /with very good technology/
Using CF when you dont need lightweight is senseless overkill.
Anyway if we need stiffness - thickness is the key in composite structure
it has "on third" relationship /excuse me english/ so 2 times more thicker means 8 times stiffer construction and laminate Young's Modulus has only linear relationship so 2 better laminate is just 2 times better stiffness of construction
Given the same thickness carbon will always be much higher stiffness. Tomtom, yes stiffness goes up with thickness but this is the case for both materials and carbon will gain on a much higher rate as thickness goes up, glass will never approach what carbon/epoxy values are at equivalent thickness. I don't know where you get that epoxy does not bond well to carbon fiber that is properly processed and uses the correct sizing agents. Sizing is the word used for the treatment of a material to increase the bonding strength of the resin fiber matrix. If you are looking at tensile strength then that is another story but stiffness goes to carbon fiber by a large margin.
Do you think this stuff can be used to strengthen injection molded plastic waveguides ? I'm afraid it is too rigid and not enough damped.
Absolutely.
Based on Earl's advice, I tried doing the same composite with Titebond instead of gorilla glue.
For me, the gorilla glue worked better. The titebond composite wasn't 'tacky' enough and it was hard to get it to adhere to the fiberglass horn. (Titebond + hemp would probably work fine if the horn was wood, but this horn is glass.)
If you wanted more damping you might try subsituting liquid nails subfloor adhesive, like Earl used to use for CLD.
Burlap Fabric |Jute Fabric | Burlap Fabric Roll
One idea I had was to get some jute cloth. (I can't find hemp cloth; it's possible that the stuff I have in the garage labeled 'hemp' may be jute.)
The jute cloth is only marginally cheaper than fiberglass, but the ability to lay this stuff down without fiberglass or epoxy is pretty attractive. And something about the combination of the fibers and the polyurethane glue makes it ultra-tacky; it's almost like duct tape that dries to the consistency of concrete.
Given the same thickness carbon will always be much higher stiffness. Tomtom, yes stiffness goes up with thickness but this is the case for both materials and carbon will gain on a much higher rate as thickness goes up, glass will never approach what carbon/epoxy values are at equivalent thickness. I don't know where you get that epoxy does not bond well to carbon fiber that is properly processed and uses the correct sizing agents. Sizing is the word used for the treatment of a material to increase the bonding strength of the resin fiber matrix. If you are looking at tensile strength then that is another story but stiffness goes to carbon fiber by a large margin.
What do you think about GLARE?
I've had really good luck with it. The main problems I ran into were delamination and it's hard to find aluminum that's the right thickness.
But once you get past that, GLARE seems like a great material for loudspeakers.
I made part of a bike frame out of some DIY glare, and when you tapped on the frame it was like tapping on a block of lead. Just completely d-e-a-d.
Here's a fun video about GLARE - the good stuff starts at the 4:00 mark
http://www.youtube.com/watch?v=cYJjilw7uWg
Last edited:
Really?(I can't find hemp cloth; it's possible that the stuff I have in the garage labeled 'hemp' may be jute.)
Unprimed Linen, Hemp & Jute Canvas Rolls | SoHo Urban Artist - JerrysArtarama.com
Eco Source | The Finest Hemp Textiles On Earth
CA-H1
Hemp Canvas
Hemp Fabric - 100% Natural Fiber Hemp & Hemp Blended Fabrics
- Home
- Loudspeakers
- Multi-Way
- Geddes on Waveguides