woodturner-fran: "Any part number on that?"
Right below the barcode is "801.498.46" ( www.ikea.com/us/en/catalog/products/80149846 ) and is made in Taiwan. There's a sticker on the tube itself and under the brand Komplement is "PGR" in small print and then "14606" in larger print.
Nanook: "KOMPLEMENT. it may be called something else in Europe. It is a "wardrobe" accessory. directdriver: thanks for the link. Is it hollow or solid?"
It is hollow, indeed, just like a glass tube but it's made of plastic. Outside diameter is 3/4" (19mm) and inside diameter is 9/16" (14mm)
I don't know how well it will work but for $5 I can't complain! If nothing else, I will at least have an accessory for my wardrobe!
Maybe one can order something like this:
Acrylic Tube Plexiglass Clear and Colored Extruded Acrylic Tubing Piping Cylinder
.
Hi Guys
I can not say I have tried that many carts at my Cantus, but I Bo suggested ZYX R100H would be a suitable choice, so that is what I use, and I think it works fine.
Some of my friends use Benz Micro ACE L (Red) MC carts, at their Cantus/Continous, which also seems to be a fair choice.
I have tried adding different weights on top of the cart, with a small brass tubes.
Slightly different, but not sure if it was for the better, so later it was removed
Regards
Pix
Sweden
I can not say I have tried that many carts at my Cantus, but I Bo suggested ZYX R100H would be a suitable choice, so that is what I use, and I think it works fine.
Some of my friends use Benz Micro ACE L (Red) MC carts, at their Cantus/Continous, which also seems to be a fair choice.
I have tried adding different weights on top of the cart, with a small brass tubes.
Slightly different, but not sure if it was for the better, so later it was removed
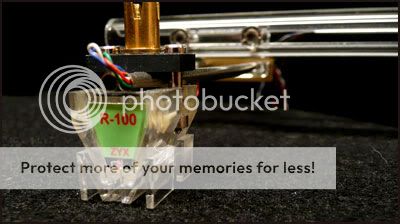
Regards
Pix
Sweden
Thanks for posting the cartridge info as there has been some interest in what cartridges work well with a Cantus. Have you experimented with any other arm or table mods? I should think that packing the arm tubes with powder would probably help things a fair bit. A member here did so on a long WBT clone (17 inches long) he used coffee creamer which is one of the favorite damping powders for arrow shaft damping. Suppose you could also use talc powder or similar. Not too much added mass but plenty of extra damping to the tubes. Frank suggested silicone shrink tube as being good for the tubes. suppose one could do both without too much trouble. Drilling a few holes in the plastic arm mounting plate would more than offset the added mass. This would require re routing the tonearm wires outside of the tube so a foil shield could be added easily. A shrink wrap to the main glass tube might also tidy things up some.
Has anybody tried adding a regulated 24 volt supply to run the motor? I should think that would also yield substantial benefit. Looking forward to more comments from the home crowd who own Cantus Continuo combinations. I have a Cantus/Continuo set on the way to me now. Should take delivery next week.
Has anybody tried adding a regulated 24 volt supply to run the motor? I should think that would also yield substantial benefit. Looking forward to more comments from the home crowd who own Cantus Continuo combinations. I have a Cantus/Continuo set on the way to me now. Should take delivery next week.
Last edited:
Thanks for posting the cartridge info as there has been some interest in what cartridges work well with a Cantus. Have you experimented with any other arm or table mods? I should think that packing the arm tubes with powder would probably help things a fair bit. A member here did so on a long WBT clone (17 inches long) he used coffee creamer which is one of the favorite damping powders for arrow shaft damping. Suppose you could also use talc powder or similar. Not too much added mass but plenty of extra damping to the tubes. Frank suggested silicone shrink tube as being good for the tubes. suppose one could do both without too much trouble. Drilling a few holes in the plastic arm mounting plate would more than offset the added mass. This would require re routing the tonearm wires outside of the tube so a foil shield could be added easily. A shrink wrap to the main glass tube might also tidy things up some.
Has anybody tried adding a regulated 24 volt supply to run the motor? I should think that would also yield substantial benefit. Looking forward to more comments from the home crowd who own Cantus Continuo combinations. I have a Cantus/Continuo set on the way to me now. Should take delivery next week.
Hi Moray
No. In my mind the Cantus/Continuo is very well designed as it is, for its purpose. Tweaks and changes often end up being degenerations.
I sometimes wish for a VTA adjustment wheel (to be used on the fly). But adding such means added complexity which should be avoided
The simplicity of this TT is its strength
The Cantus horizontal alignment is crucial though, and a good waterlevel is a must.
But ones setup, the hole TT will run for years without further adjustments
The extra damping of the arm tube sounds interesting though, and could be worth testing some rainy day
Regards
Pix
Sweden
I was at IKEA today and found this glass looking pole with hook made of "polystyrene-acrylic plastic" and cost only $5 USD. It's about 3/4" diameter and 37" long. And that's enough to make about 4 tubes for the Cantus experiment. Since it's not glass so it shouldn't be too hard to cut. And when I finger flick it, there's no ringing, pretty inert. Good sign. I might to try to slice it with a Dremel kit.
.
![]()
.
There is no reason to IKEA shopping.These things are every where.
Btw.I don't see why a U shaped channel of glass or plexi,mounted on a grooved piece of wood or something else ,that would improve the solidity of the tonearm,cannot function properly.
Cantus,no doubt,wanted to make it less easy,for the copiers.
As for the dust,it will be easier to keep it clean with a simple make -up brush.
As long as,it is open,slitted or U, dust will creep in.
Or simply,use a cover.
B.L.
Pix:I agree that the Cantus is deceptively simple and a very deliberate design. Modifications that may add to performance yet be easily reversed it not successful are what I had in mind.
BL: a "V" shaped glass track as already been built and yes a "U" channel could also be used. Both will require a cover of some sort and both will have to be open enough for arm motion. When all is said and done the tube with a slot is an excellent compromise.
A hard material for the track will reduce friction and here again the glass tube is a fine compromise with a hardness of 6.5 on the Mohs Scale, Tungsten Carbide and gemstones (other than diamond) will be about 9.5 - 10 on the Mohs Scale. Diamond is 11 on the Mohs Scale and machine steel or aluminum will be softer than glass.
I don't think Bo was concerned with copy cat products when he designed the Cantus and he is not now even though the design has been commercially copied. The Cantus would appear to be a very well executed engineering design which holds its own twenty years after the fact. There is not much to change without fear of degrading the design in some way. Should win an award for "Done Right The First Time". To do so much with so little is quite an achievement.
BL: a "V" shaped glass track as already been built and yes a "U" channel could also be used. Both will require a cover of some sort and both will have to be open enough for arm motion. When all is said and done the tube with a slot is an excellent compromise.
A hard material for the track will reduce friction and here again the glass tube is a fine compromise with a hardness of 6.5 on the Mohs Scale, Tungsten Carbide and gemstones (other than diamond) will be about 9.5 - 10 on the Mohs Scale. Diamond is 11 on the Mohs Scale and machine steel or aluminum will be softer than glass.
I don't think Bo was concerned with copy cat products when he designed the Cantus and he is not now even though the design has been commercially copied. The Cantus would appear to be a very well executed engineering design which holds its own twenty years after the fact. There is not much to change without fear of degrading the design in some way. Should win an award for "Done Right The First Time". To do so much with so little is quite an achievement.
Some pictures on a Clearaudio Tangent. Not sure about having V-grooved rollers on a string. Not rigid enough! A blade would work better, I think.
___________________________________________
It appears the Japanese DIYer is inspired by the Cantus.
.
An externally hosted image should be here but it was not working when we last tested it.
___________________________________________
It appears the Japanese DIYer is inspired by the Cantus.
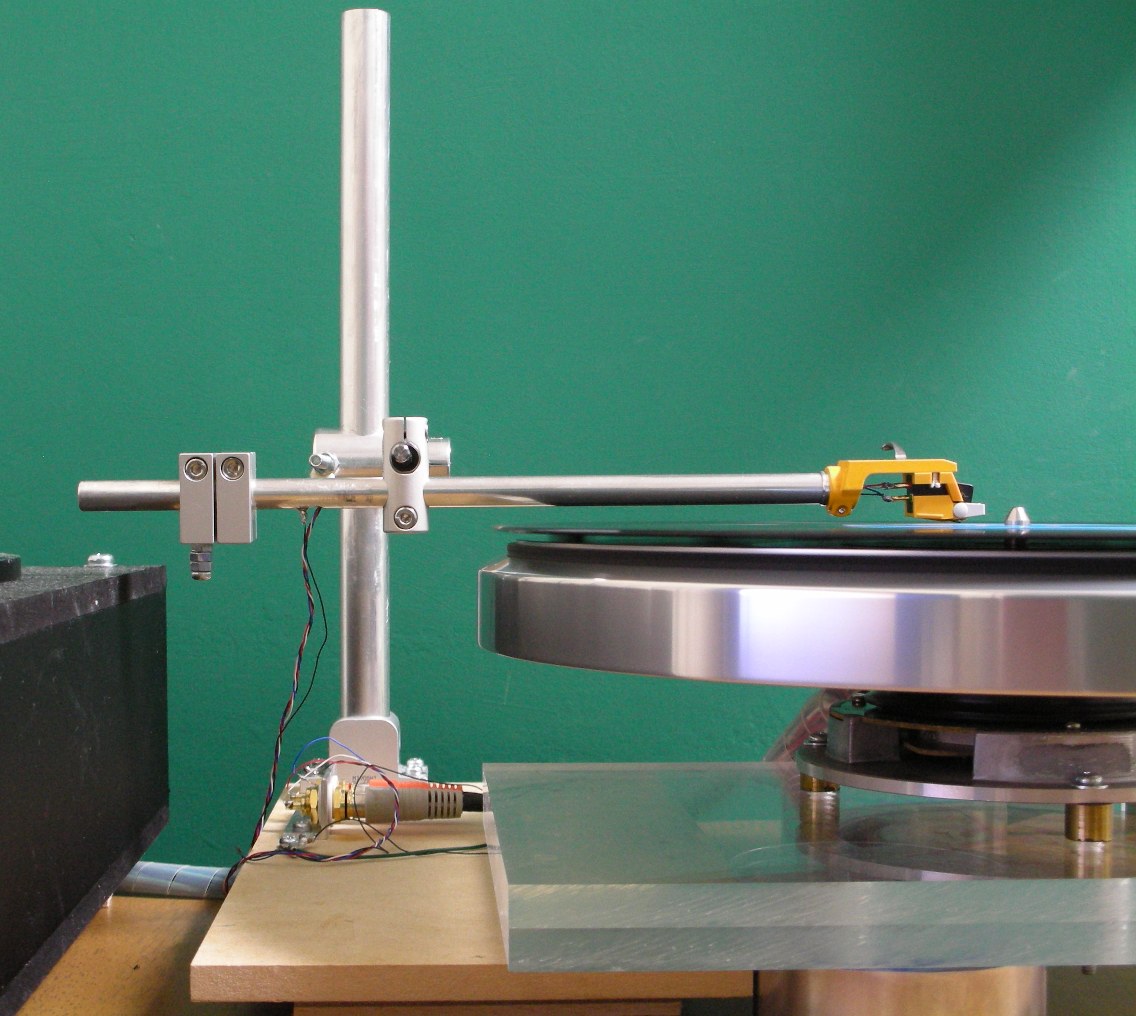
.
Last edited:
IKEA tube
Hi All,
A few comments from the guy that built the glass V track. I have my linear tracker on hold for right now, but have experienced good success with the parallel hardened ground and polished stainless steel rods from a DEC line printer. I also have experienced the degree of cleanliness and polish and surface smoothness needed to make the parallel rod track really work well. So I'm very interested in seeing how well the acrylic tube works especially where it is intended for a home maker application. The slotted tube sure is attractive from the keep the dust and dirt out as well as the aesthetics. It looks great. What I feel could be the best compromise is to use the acrylic tube, slotted of course, but use it as the holder for the glass V track. Note that the angle of the v will have to be fairly shallow to allow adequate vertical motion of the arm wand, and to allow the choice of a reasonably sized ball bearing. Also the diameter of the bearing support rods, and the inner diameter of the bearing will have to be chosen correctly to eliminate interference between the bottom edge of the acrylic tube slot and the bearing support rods. On my 2 rod rail model I had to file semicircular clearance grooves in the bearing support rods. This is all pretty easy but it is something to be aware of at the outset.
Good luck, I'm watching with great interest,
BillG
Pix:I agree that the Cantus is deceptively simple and a very deliberate design. Modifications that may add to performance yet be easily reversed it not successful are what I had in mind.
BL: a "V" shaped glass track as already been built and yes a "U" channel could also be used. Both will require a cover of some sort and both will have to be open enough for arm motion. When all is said and done the tube with a slot is an excellent compromise.
A hard material for the track will reduce friction and here again the glass tube is a fine compromise with a hardness of 6.5 on the Mohs Scale, Tungsten Carbide and gemstones (other than diamond) will be about 9.5 - 10 on the Mohs Scale. Diamond is 11 on the Mohs Scale and machine steel or aluminum will be softer than glass.
I don't think Bo was concerned with copy cat products when he designed the Cantus and he is not now even though the design has been commercially copied. The Cantus would appear to be a very well executed engineering design which holds its own twenty years after the fact. There is not much to change without fear of degrading the design in some way. Should win an award for "Done Right The First Time". To do so much with so little is quite an achievement.
Hi All,
A few comments from the guy that built the glass V track. I have my linear tracker on hold for right now, but have experienced good success with the parallel hardened ground and polished stainless steel rods from a DEC line printer. I also have experienced the degree of cleanliness and polish and surface smoothness needed to make the parallel rod track really work well. So I'm very interested in seeing how well the acrylic tube works especially where it is intended for a home maker application. The slotted tube sure is attractive from the keep the dust and dirt out as well as the aesthetics. It looks great. What I feel could be the best compromise is to use the acrylic tube, slotted of course, but use it as the holder for the glass V track. Note that the angle of the v will have to be fairly shallow to allow adequate vertical motion of the arm wand, and to allow the choice of a reasonably sized ball bearing. Also the diameter of the bearing support rods, and the inner diameter of the bearing will have to be chosen correctly to eliminate interference between the bottom edge of the acrylic tube slot and the bearing support rods. On my 2 rod rail model I had to file semicircular clearance grooves in the bearing support rods. This is all pretty easy but it is something to be aware of at the outset.
Good luck, I'm watching with great interest,
BillG
Youtube videos of "linear arm on glass tube"
youtube.com/watch?v=1At1hS16O6s _____ Video #1 of Linear Arm On Glass Tube
youtube.com/watch?v=ukM-rumeqVM ____ Video #2 of Linear Arm On Glass Tube
youtube.com/watch?v=npUeDaOgBdo ____ Video #3 of Linear Arm On Glass Tube
http://aboyhome.blogspot.com Google Translated from Thai
.
youtube.com/watch?v=1At1hS16O6s _____ Video #1 of Linear Arm On Glass Tube
youtube.com/watch?v=ukM-rumeqVM ____ Video #2 of Linear Arm On Glass Tube
youtube.com/watch?v=npUeDaOgBdo ____ Video #3 of Linear Arm On Glass Tube
http://aboyhome.blogspot.com Google Translated from Thai
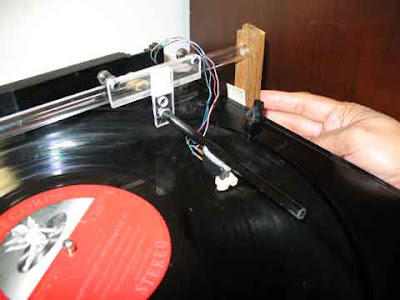
.
Last edited:
Comments from the designer of the Opus 3 Cantus...
This is an interesting letter I received from Bo Hansson in response to some questions that I asked about the Continuo turntable. Since Bo's first language is Swedish I have adjusted the grammar where necessary so that there would be minimal confusion without changing the meaning of his words.
Dear Moray James
There is two sayings which are a kind of leading guide for me. One comes from Ingvar Kamprad, the founder of IKEA : "Complex expensive solutions does not comes from the most bright designers" and the other is from one of my friends who found it somewhere " There is nothing quite so complicated as simplicity". I try to use these as guiding words in my designs.
Traditionally most of record player designers proudly show nicely machined parts, but does not pay much attention to function. A platter bearing of 7-9 mm is definitely to small to take care of the moment on the platter during play.
One turntable maker bought part from our production, and send the part for chroming (?) before assembling. On my question why chroming non visible parts, he meant it's satisfying to know it's chromed even not visible. Well we have different sights on it.
I'm music lower, use my time for relaxation with music, mainly all from early music to Romantic era with organ music. I don't listen to electronic music and seldom music from the 50ies and later, which is the most common.
Continuo project started as I needed a better record player for evaluation, my music production. Most of record players at that time sounded very different from my master tapes, especially suspended sub chassis types sound weak in the midrange and have bumpy bass, which does not work for my favorite organ music. There are some players with less of this problem Nakamichi 1000 and Thorens Reference, a beast of 90 kgs. The (my) goal was to make one record player for my own use, but shortly after mine was in use there was a que of people who also wanted one.
Some technical. I use a standard bearing from SKF a Swedish maker and the one who invented the roller bearing. As being 18 mm shaft the tolerance is bigger than if you use a 7 mm shaft, but by making an inverted bearing it doesn't make any sense. You can have up to -55 dB signal to noise ratio on the best made vinyl records. on a lacquer you can reach -60 dB sometimes - 65dB. our measurements on Continuo with a Thorens measurement tools shows better than - 77dB, we can't measure better as there is no way to do it. This means the S/N ration is more than 100 times better than the best lacquer you can play and more than 1000 times better than a good record, on a record players still in an affordable price for music lovers.
Of course there is things that can be improved, and I'm working on it, at the same time I ask my self, is that "improvement" only of cosmetic art or does it make a better record player for people who love music.
Best regards
Bo Hansson
This is an interesting letter I received from Bo Hansson in response to some questions that I asked about the Continuo turntable. Since Bo's first language is Swedish I have adjusted the grammar where necessary so that there would be minimal confusion without changing the meaning of his words.
Dear Moray James
There is two sayings which are a kind of leading guide for me. One comes from Ingvar Kamprad, the founder of IKEA : "Complex expensive solutions does not comes from the most bright designers" and the other is from one of my friends who found it somewhere " There is nothing quite so complicated as simplicity". I try to use these as guiding words in my designs.
Traditionally most of record player designers proudly show nicely machined parts, but does not pay much attention to function. A platter bearing of 7-9 mm is definitely to small to take care of the moment on the platter during play.
One turntable maker bought part from our production, and send the part for chroming (?) before assembling. On my question why chroming non visible parts, he meant it's satisfying to know it's chromed even not visible. Well we have different sights on it.
I'm music lower, use my time for relaxation with music, mainly all from early music to Romantic era with organ music. I don't listen to electronic music and seldom music from the 50ies and later, which is the most common.
Continuo project started as I needed a better record player for evaluation, my music production. Most of record players at that time sounded very different from my master tapes, especially suspended sub chassis types sound weak in the midrange and have bumpy bass, which does not work for my favorite organ music. There are some players with less of this problem Nakamichi 1000 and Thorens Reference, a beast of 90 kgs. The (my) goal was to make one record player for my own use, but shortly after mine was in use there was a que of people who also wanted one.
Some technical. I use a standard bearing from SKF a Swedish maker and the one who invented the roller bearing. As being 18 mm shaft the tolerance is bigger than if you use a 7 mm shaft, but by making an inverted bearing it doesn't make any sense. You can have up to -55 dB signal to noise ratio on the best made vinyl records. on a lacquer you can reach -60 dB sometimes - 65dB. our measurements on Continuo with a Thorens measurement tools shows better than - 77dB, we can't measure better as there is no way to do it. This means the S/N ration is more than 100 times better than the best lacquer you can play and more than 1000 times better than a good record, on a record players still in an affordable price for music lovers.
Of course there is things that can be improved, and I'm working on it, at the same time I ask my self, is that "improvement" only of cosmetic art or does it make a better record player for people who love music.
Best regards
Bo Hansson
Hi all
Just noticed this thread and thought to show some pics with one of my own DIY tangent arms. This one was inspired by Souther/Clearaudio/Opus3 passive tangent arms.
I managed to make the arm to weight only 22 grams without cartridge and weight/counterweight. One of the problems was to make the arm very light but to have high dynamic mass to complement the very low compliance of the Denon DL103.
The arm itself (the wood part and wiring) is still not the final version but as it is, it successfully passes the tracking ability tests, tracks 6,7,8 side 1 HI-FI NEWS Analogue test LP and the Analogue Productions test LP track 1 side 2.
Also it does very well at the low frequency resonance tests. Lateral low freq resonance is 11Hz and vertical resonance is 9Hz.
Before this I built some other variations including one based on linear bearings. Later discovered that a guy from Japan did the same thing and posted some videos on youtube.
In my opinion this new version (the Opus3 inspired) is a better one, it tracks impeccable and do not skip at all if the turntable is properly adjusted (level)
http://img.photobucket.com/albums/v292/chrissugar/TURNTABLE/TANGENT-01.jpg
http://img.photobucket.com/albums/v292/chrissugar/TURNTABLE/TANGENT-02.jpg
http://img.photobucket.com/albums/v292/chrissugar/TURNTABLE/TANGENT-03.jpg
http://img.photobucket.com/albums/v292/chrissugar/TURNTABLE/TANGENT-04.jpg
http://img.photobucket.com/albums/v292/chrissugar/TURNTABLE/TANGENT-06.jpg
http://img.photobucket.com/albums/v292/chrissugar/TURNTABLE/TANGENT-07.jpg
chrissugar
Just noticed this thread and thought to show some pics with one of my own DIY tangent arms. This one was inspired by Souther/Clearaudio/Opus3 passive tangent arms.
I managed to make the arm to weight only 22 grams without cartridge and weight/counterweight. One of the problems was to make the arm very light but to have high dynamic mass to complement the very low compliance of the Denon DL103.
The arm itself (the wood part and wiring) is still not the final version but as it is, it successfully passes the tracking ability tests, tracks 6,7,8 side 1 HI-FI NEWS Analogue test LP and the Analogue Productions test LP track 1 side 2.
Also it does very well at the low frequency resonance tests. Lateral low freq resonance is 11Hz and vertical resonance is 9Hz.
Before this I built some other variations including one based on linear bearings. Later discovered that a guy from Japan did the same thing and posted some videos on youtube.
In my opinion this new version (the Opus3 inspired) is a better one, it tracks impeccable and do not skip at all if the turntable is properly adjusted (level)
An externally hosted image should be here but it was not working when we last tested it.
http://img.photobucket.com/albums/v292/chrissugar/TURNTABLE/TANGENT-01.jpg
http://img.photobucket.com/albums/v292/chrissugar/TURNTABLE/TANGENT-02.jpg
http://img.photobucket.com/albums/v292/chrissugar/TURNTABLE/TANGENT-03.jpg
http://img.photobucket.com/albums/v292/chrissugar/TURNTABLE/TANGENT-04.jpg
http://img.photobucket.com/albums/v292/chrissugar/TURNTABLE/TANGENT-06.jpg
http://img.photobucket.com/albums/v292/chrissugar/TURNTABLE/TANGENT-07.jpg
chrissugar
Thanks for the great pictures. Beautiful work. I am sure that others will want to know how you fared cutting the slot in the glass tube. Did you use a standard carbide glass cutter? Did yo experiment much with bearings and what did you end up using? Your deck looks nice is there a story to tell there as well?
Thank you all for the kind words
believe it or not it was the first time in my life I did something like this (I mean cutting glass) but I used my intuition and it worked from the first try.
I bought the glass tube from a medical accessories shop (have no idea what is the correct name in english for this kind of shop). External diameter 14mm, internal 11mm.
All I used to cut the tube was:
1-MICRO compound table KT 70 to mount the tube and advance it by rotating the handwheel.
PROXXON - KT 70
2-Mill/drill unit MICROMOT 50/E
PROXXON - MICROMOT 50 and 50/E
3-Universal holder UHZ for mounting the mill/drill unit
PROXXON - UHZ
4-Diamond cutting disc NO 28 840
PROXXON - Cutting discs
You need alot of patience to cut the glass. I advanced the tube 1milimeter per 15 seconds (very slow). If you make the calculus you need an hour to cut one row, two hours for two rows (the complete slot). Diamon disc should be almost tangent to tube to avoid breaking it.
I used different bearing before but this one suited best my specific project. It is a 10mm diameter Japanese SKF bearing.
I bought them from RS-COMPONENTS Welcome to rswww.com
part number 285-0790
The only treatment I apply is after I mount the bearings I use high presure air spray to make them spin fast and blow out any dust particle.
Here are some pics with my DIY turntable (a 45 kilogram monster). Unfortunately I do not have pics of the complete table with this new tangent arm.
In these older pics you will see the old linear bearing arm mount (without the arm) and a Technics arm.
The latest version has this new tangent arm and a Rega RB250 Origin Live arm.
I hope soon to make some photos with the new complete machine and will post them here.
http://img.photobucket.com/albums/v292/chrissugar/TURNTABLE/08.jpg
http://img.photobucket.com/albums/v292/chrissugar/TURNTABLE/09.jpg
http://img.photobucket.com/albums/v292/chrissugar/TURNTABLE/10.jpg
http://img.photobucket.com/albums/v292/chrissugar/TURNTABLE/04.jpg
chrissugar
believe it or not it was the first time in my life I did something like this (I mean cutting glass) but I used my intuition and it worked from the first try.
I bought the glass tube from a medical accessories shop (have no idea what is the correct name in english for this kind of shop). External diameter 14mm, internal 11mm.
All I used to cut the tube was:
1-MICRO compound table KT 70 to mount the tube and advance it by rotating the handwheel.
PROXXON - KT 70
2-Mill/drill unit MICROMOT 50/E
PROXXON - MICROMOT 50 and 50/E
3-Universal holder UHZ for mounting the mill/drill unit
PROXXON - UHZ
4-Diamond cutting disc NO 28 840
PROXXON - Cutting discs
You need alot of patience to cut the glass. I advanced the tube 1milimeter per 15 seconds (very slow). If you make the calculus you need an hour to cut one row, two hours for two rows (the complete slot). Diamon disc should be almost tangent to tube to avoid breaking it.
...
2. What is the bearing (part number if you can)
3. Did you do any treatment on the bearing (remove seal, flush out grease, run in on a drill etc)
I used different bearing before but this one suited best my specific project. It is a 10mm diameter Japanese SKF bearing.
I bought them from RS-COMPONENTS Welcome to rswww.com
part number 285-0790
The only treatment I apply is after I mount the bearings I use high presure air spray to make them spin fast and blow out any dust particle.
Here are some pics with my DIY turntable (a 45 kilogram monster). Unfortunately I do not have pics of the complete table with this new tangent arm.
In these older pics you will see the old linear bearing arm mount (without the arm) and a Technics arm.
The latest version has this new tangent arm and a Rega RB250 Origin Live arm.
I hope soon to make some photos with the new complete machine and will post them here.
http://img.photobucket.com/albums/v292/chrissugar/TURNTABLE/08.jpg
http://img.photobucket.com/albums/v292/chrissugar/TURNTABLE/09.jpg
http://img.photobucket.com/albums/v292/chrissugar/TURNTABLE/10.jpg
http://img.photobucket.com/albums/v292/chrissugar/TURNTABLE/04.jpg
chrissugar
chrissugar: "Here are some pics with my DIY turntable (a 45 kilogram monster). In these older pics you will see the old linear bearing arm mount (without the arm) and a Technics arm."
Great tonearm project! I really admire your craftsmanship.
Judging from your pictures, it appears to me the platter and Technics tonearm came from the Technics SL-Q2. Am I correct? I used to have that and butchered it and retained the platter for future belt-drive experiment but I abandoned it because I later found the SL-M3 and SL-M2 to be better and I also use them as motor to tape-drive a platter.
Do you have pictures of the motor and electronics and can you tell us how you modified the table? Sorry to be off topic as this thread is about tonearms.

- Status
- This old topic is closed. If you want to reopen this topic, contact a moderator using the "Report Post" button.
- Home
- Source & Line
- Analogue Source
- Opus 3 Cantus parallel tracking arm