He is right, I would think. Use the full output voltage swing to get best signal-to-noise/distortion ratio.
I should have missed something... isn't he saying that the pull range should be kept as low as possible?
Dario,
I'm not sure I'm right at all, but I interpreted Thorsten's comment as you should have the lowest gain possible on the servo amp that will correct the DC offset. Having a high value resistor feeding the servo opamp will require a higher gain on the opamp for the same DC correction. Is there more to Thorsten's comments? Maybe we can understand better with more background.
Jac
I'm not sure I'm right at all, but I interpreted Thorsten's comment as you should have the lowest gain possible on the servo amp that will correct the DC offset. Having a high value resistor feeding the servo opamp will require a higher gain on the opamp for the same DC correction. Is there more to Thorsten's comments? Maybe we can understand better with more background.
Jac
Are you confusing Input offset with output offset?.......................Nevertheless according Klaus' calculations we should need a much lower (less than 160mV) than 2V range, correct?
I was going to ask in my last post if you had read Gootee's contributions........................ how can we determine when it's slow (or fast) enough?
It looks like you haven't.
simulate the LF distortion with different Fc with and without the added filter.
And also change the filter.
There may be an optimum that minimises the distortion and gives fast enough response.
I think what ThorstenL is saying is that you should increase the resistor value between servo-out and amp-in. Forcing the servo opamp to increase its output voltage for the same amount of correction.
In the AndrewT example there is a maximum output offset correction of +/- 2 volts (at the output of the amp) which seems far to much if there is only a 20mV offset to start with. A maximum offset correction of 150 mV seems better but could still be to high.
1. Design the servo to give the desired maximum injection voltage at a maximum servo output.
2. Maximum offset correction = maximum expected uncorrected offset.
3. Improvements that will reduce the uncorrected offset.
In the AndrewT example there is a maximum output offset correction of +/- 2 volts (at the output of the amp) which seems far to much if there is only a 20mV offset to start with. A maximum offset correction of 150 mV seems better but could still be to high.
1. Design the servo to give the desired maximum injection voltage at a maximum servo output.
2. Maximum offset correction = maximum expected uncorrected offset.
3. Improvements that will reduce the uncorrected offset.
ensure the servo opamp does not invert when the output is driven to near the supply rail...............
1. Design the servo to give the desired maximum injection voltage at a maximum servo output. ......
The servo adjustment range MUST be bigger than the DC detection threshold.
If not then the servo could hit it's limit and the DC detection would not recognise this and do nothing, even though there is a DC fault.
A window comparator on the servo output could be an extra trigger for the DC detect.
An input mute could also be activated when the servo runs out of range.
An inverting servo can be made with Zener clamps to prevent going open-loop or even phase reverse (like old TL072's) when overdriven, and with wrapping a diode bridge around it you can series an Optocoupler with the Zener to trigger DC protection.
For the bridge+Zener clamp, see OPA627 datasheet, fig.5.
Higher order servos are tricky, notably those with passive post-filtering before resistively feeding the injection point at the -IN node because that alters the signal gain vs freq as well if not perfectly trimmed. See below the effect of a set of post filter time constants after a 100k+1u Servo into a signal gain of about 30dB, non-optimized pull-range (not needed for the effect to demo), just simple 10:1 split of R10, with the post filter as an equal valued T-filter (gives the lowest Fc for a given cap).
Only one time constant is correct and gives a flat response, higher values leads to overshoot (danger of oscillaition), lower give a gain drop at LF (amount depends on the split ratio).
For the bridge+Zener clamp, see OPA627 datasheet, fig.5.
Higher order servos are tricky, notably those with passive post-filtering before resistively feeding the injection point at the -IN node because that alters the signal gain vs freq as well if not perfectly trimmed. See below the effect of a set of post filter time constants after a 100k+1u Servo into a signal gain of about 30dB, non-optimized pull-range (not needed for the effect to demo), just simple 10:1 split of R10, with the post filter as an equal valued T-filter (gives the lowest Fc for a given cap).
Only one time constant is correct and gives a flat response, higher values leads to overshoot (danger of oscillaition), lower give a gain drop at LF (amount depends on the split ratio).
Attachments
Last edited:
Made a mistake, the equal leg T is not a good idea, it kills the 2nd order slope of the servo's transfer. Better working with low value input leg and high valued output leg, needing a bigger cap of course.
For a servo with a 0.3Hz Fc and with a +-300mV output catch range (for +-10V integrator output voltage), I arrived at 22k+1u integrator feeding a 10k+1u post filter, injection via 330k.
EDIT: The post filter kicks in at ~20Hz (if going lower a higher passband ripple, some gain at LF, start to emerge)
For a servo with a 0.3Hz Fc and with a +-300mV output catch range (for +-10V integrator output voltage), I arrived at 22k+1u integrator feeding a 10k+1u post filter, injection via 330k.
EDIT: The post filter kicks in at ~20Hz (if going lower a higher passband ripple, some gain at LF, start to emerge)
Last edited:
Agreed.Add to post 65.
4. Add the servo opamp output to the speaker protection circuit (or other warning) Preventing or warning if the amp is functioning beyond the servo opamp range.
And even more important if the amplifier becomes DC coupled.
i.e. omitting the Input and NFB DC blocking capacitors.
For a servo with a 0.3Hz Fc and with a +-300mV output catch range (for +-10V integrator output voltage), I arrived at 22k+1u integrator feeding a 10k+1u post filter, injection via 330k.
Close enough to my first-guess post-filter of 10k-3.3uF-100k. The Rs can be decreased if the pull-range is to be increased. 3.3uF was my first choice for completely unrelated reasons - it's the largest value in Wima MKS2XL that's still reasonably compact (5mm pitch) and relatively inexpensive (it would help to keep the cost of the servo lower than the Black Gate that it will replace).
I think you need a much larger RC for the integrator, though - I was looking at 1M-470nF.
Last edited:
It seems this thread is going through an interesting path... 
It's all in the thread I've linked... BTW the more interesting posts:
http://www.diyaudio.com/forums/parts/190231-dc-servo-no-compromise-opamp.html#post2596215
http://www.diyaudio.com/forums/parts/190231-dc-servo-no-compromise-opamp.html#post2596247
http://www.diyaudio.com/forums/parts/190231-dc-servo-no-compromise-opamp.html#post2597150
http://www.diyaudio.com/forums/parts/190231-dc-servo-no-compromise-opamp.html#post2597597
http://www.diyaudio.com/forums/parts/190231-dc-servo-no-compromise-opamp.html#post2599457
Is there more to Thorsten's comments? Maybe we can understand better with more background.
It's all in the thread I've linked... BTW the more interesting posts:
http://www.diyaudio.com/forums/parts/190231-dc-servo-no-compromise-opamp.html#post2596215
http://www.diyaudio.com/forums/parts/190231-dc-servo-no-compromise-opamp.html#post2596247
http://www.diyaudio.com/forums/parts/190231-dc-servo-no-compromise-opamp.html#post2597150
http://www.diyaudio.com/forums/parts/190231-dc-servo-no-compromise-opamp.html#post2597597
http://www.diyaudio.com/forums/parts/190231-dc-servo-no-compromise-opamp.html#post2599457
Are you confusing Input offset with output offset?
I've taken those data from this post:
http://www.diyaudio.com/forums/chip...ollaborative-dc-servo-design.html#post3952979
I've misanderstood?
I was going to ask in my last post if you had read Gootee's contributions.
It looks like you haven't.
I've read it but not all posts were simple enough for my electronics knowledge level.
A configuration where the offset is reduced by a percentage of the offset per unit of time.
example:
Initial Offset 200 with a 50% reduction per second.
Perhaps something like this:
Add an extra resistor between the servo opamp input and ground leaving only a percentage of the total offset signal at the opamp input. Then slow down the output so it will take a full second to accomplish that partial reduction.
example:
Initial Offset 200 with a 50% reduction per second.
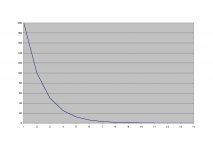
Perhaps something like this:
Add an extra resistor between the servo opamp input and ground leaving only a percentage of the total offset signal at the opamp input. Then slow down the output so it will take a full second to accomplish that partial reduction.
4.5seconds to get a start up offset of 200mV (output?) down to 20mV.
I would interpret that as slow enough to need a 5second delay on the speaker protection relay.
I suggested a different servo set up.
The output offset should be set for zero mVdc when cold and just starting.
Any drift from that starting value as the amplifier warms up is then corrected by the DC servo. That way the initial offset is low and the variation can be controlled by a slowish servo.
If there is a start up pulse on the output that is independant of output offset, then the speaker protection relay should delay connection until after that pulse is passed. i.e a 100ms pulse, then a 150ms delay for speaker connect.
I would interpret that as slow enough to need a 5second delay on the speaker protection relay.
I suggested a different servo set up.
The output offset should be set for zero mVdc when cold and just starting.
Any drift from that starting value as the amplifier warms up is then corrected by the DC servo. That way the initial offset is low and the variation can be controlled by a slowish servo.
If there is a start up pulse on the output that is independant of output offset, then the speaker protection relay should delay connection until after that pulse is passed. i.e a 100ms pulse, then a 150ms delay for speaker connect.
This design has the advantage of being extremely stable and low noise. If the offset is only 0.01 mV, the servo would only correct it by 0.005 mV over a period of one second.
How high is the initial offset? How sensitive is the speaker protection? Will it activate at only 200mV ?
What I see as a possible problem is that at power up the LM3886 is in mute state and the loop is broken. This already causes the LM318 into open loop operation. What will it do to the servo? Is this another reason to limit the offset correction to a few 100 mV?
Good idea AndrewT. To shorten the initial start-up time, the servo could have a 100% input regulation until near zero then switch to a lower percentage of regulation.
How high is the initial offset? How sensitive is the speaker protection? Will it activate at only 200mV ?
What I see as a possible problem is that at power up the LM3886 is in mute state and the loop is broken. This already causes the LM318 into open loop operation. What will it do to the servo? Is this another reason to limit the offset correction to a few 100 mV?
Good idea AndrewT. To shorten the initial start-up time, the servo could have a 100% input regulation until near zero then switch to a lower percentage of regulation.
Capacitance multiplier instead of C9-R10 branch
Hello,
one crazy idea: is there any experience of using of a capacitance multiplier in the audio signal path? It could be used instead of the branch C9-R10. Some advantages:
1. a relatively small good quality cap (1-2uF) can be used that can be easily be seen as a 220uF or even larger cap (smaller cut-off frequency then).
2. the equivalent impedance of a capacitance multiplier is still a RC branch, with R and C tunable to the desired values.
3. the quality cap and the performances of a suitable op-amp should improve the performance from the THD point of view (it was established that C9 electrolitic character can give distortion in the audio range. That's the reason why the cutoff frequency must be as low as possible and, then, C9 of high value.
4. more important: to change just the C9-R10 branch from "passive" to "active" would not change (in principle!) any other behavior of the amplifier. This means that we do not have to tune again any compensation network, input network, etc.
5. then we would have the advantage of a DC-servo like circuit, without the drawback of strong interactions with the rest of the circuit.
Sorry if the idea is too crazy...
About this, I asked to the magazine "Costruire HIFI" the permit to publish just one scheme. Let's wait for the reply.
Daniele
Hello,
one crazy idea: is there any experience of using of a capacitance multiplier in the audio signal path? It could be used instead of the branch C9-R10. Some advantages:
1. a relatively small good quality cap (1-2uF) can be used that can be easily be seen as a 220uF or even larger cap (smaller cut-off frequency then).
2. the equivalent impedance of a capacitance multiplier is still a RC branch, with R and C tunable to the desired values.
3. the quality cap and the performances of a suitable op-amp should improve the performance from the THD point of view (it was established that C9 electrolitic character can give distortion in the audio range. That's the reason why the cutoff frequency must be as low as possible and, then, C9 of high value.
4. more important: to change just the C9-R10 branch from "passive" to "active" would not change (in principle!) any other behavior of the amplifier. This means that we do not have to tune again any compensation network, input network, etc.
5. then we would have the advantage of a DC-servo like circuit, without the drawback of strong interactions with the rest of the circuit.
Sorry if the idea is too crazy...
Actually, the copyright belongs to the magazine, but fair-use exemptions should allow a small excerpt to be posted here with attribution (without violating copyright). That can, for instance, be the image of the schematic that was published.
About this, I asked to the magazine "Costruire HIFI" the permit to publish just one scheme. Let's wait for the reply.
Daniele
- Status
- This old topic is closed. If you want to reopen this topic, contact a moderator using the "Report Post" button.
- Home
- Amplifiers
- Chip Amps
- My_Ref Fremen Edition - Collaborative DC-Servo design