Already looking good![]()
Thanks!
Much more stable design than the first one due to the head design which will hold its alignment and not twist when bumped. Needle aligns perfectly with shaft still.
Took three goes to get a strong arm (Tasmanian oak) hence it changed colour, also grounding was achieved using woven shielding out of some old coax.
Base is really well isolated with some nice gold feet underneath as an extra bit of bling!
Next job is the arm lift.
KISS is the way to good SQ. Strive from the path for any reason and it will be more expensive to keep the SQ. I do understand the wish to make money outta anything audio but the two dollar 19 cents is very, very hard to beat! If my builds wasn't so ugly I rather used it over my Mayware V as it sounds as good or better. Then again - I have arms that are more impressive and fits better for my heavier carts. But for carts like the Sonus Blue Gold the 2.19 and MaywareV are about equal given that the Mayware has more ways to be controlled. Wow, I managed to give my view something that passed the bridge a while ago. Well, I believe my view stands for itself in this thread.
Last edited:
Thanks!
Much more stable design than the first one due to the head design which will hold its alignment and not twist when bumped. Needle aligns perfectly with shaft still.
Took three goes to get a strong arm (Tasmanian oak) hence it changed colour, also grounding was achieved using woven shielding out of some old coax.
Base is really well isolated with some nice gold feet underneath as an extra bit of bling!
Next job is the arm lift.
Not a nanook but it might be very good for heavier carts! Nice work!
Dan.
looks good...but strictly speaking not a Nanook![]()
Don't know
Still got a pen at its heart and fixed head shell like your original except its angled and set back to take into account later comments in this thread about keeping it in line with the streight arm. Only deviation is away from the arrow, cause these are the materials i had knocking around the house. Cost was a couple of extra brass plumbing fittings!!
Yes i did make it for a heavier cart... Osawa os301 moving iron, sounds grown up against the at120e mounted in my original; which has been continually horrible to align
So made some necessary modifications including antiskate which was a must on this arm otherwise it jumped.
Notice the main weight leans to the right of the picture perfectly counteracting the pull of the antiskate keeping the arm very stable.
Interestingly this was not needed on my original arm so I removed it.
However my original arm sounds terrible in comparison due to distortion from poor head shell design.
I've temporarily dampened it with bluetac, but will replace it with a wooden head using the same configuration less the washers as I plan to countersink the bolt heads in so it can sit ridgidly against the arm.
I'll still argue my new arm is in the spirit of the Nanook as it not only borrows much of the design, and was made from junk! It is however not as light an arm and favours a mid to low compliance cartridge.
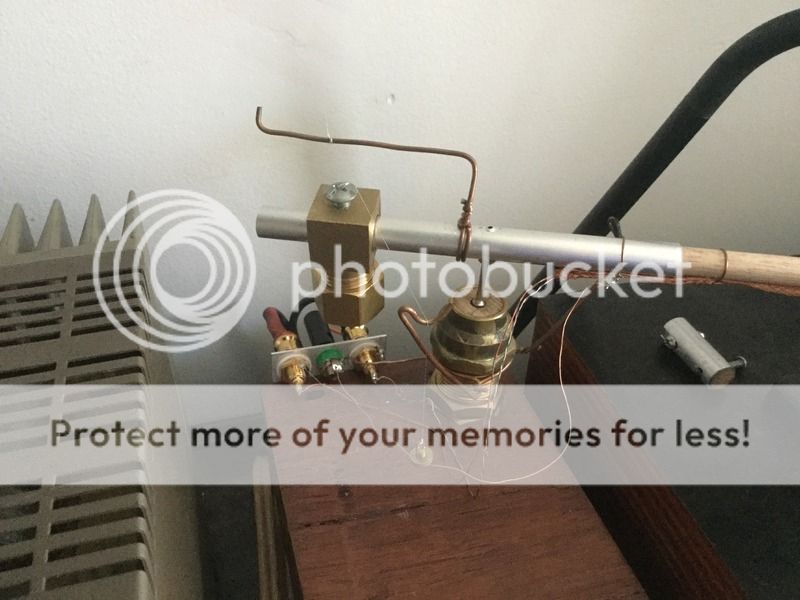
Notice the main weight leans to the right of the picture perfectly counteracting the pull of the antiskate keeping the arm very stable.
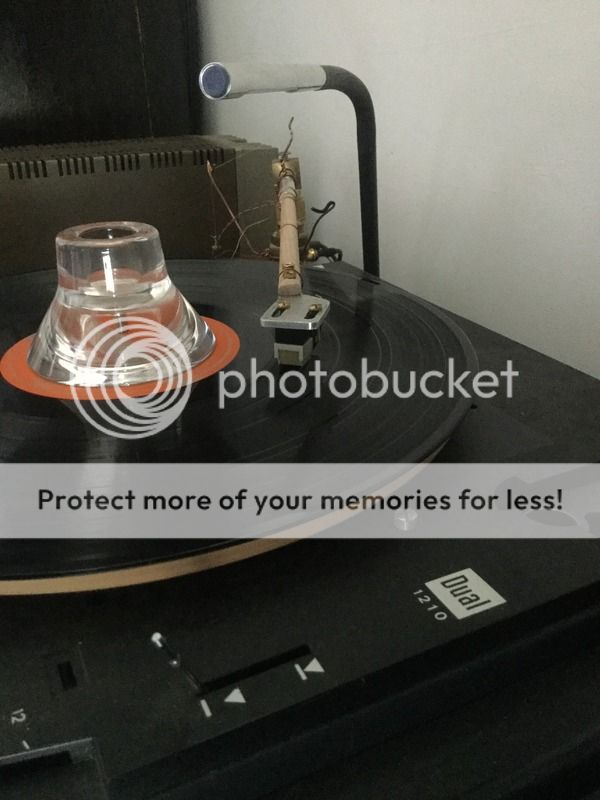
Interestingly this was not needed on my original arm so I removed it.
However my original arm sounds terrible in comparison due to distortion from poor head shell design.
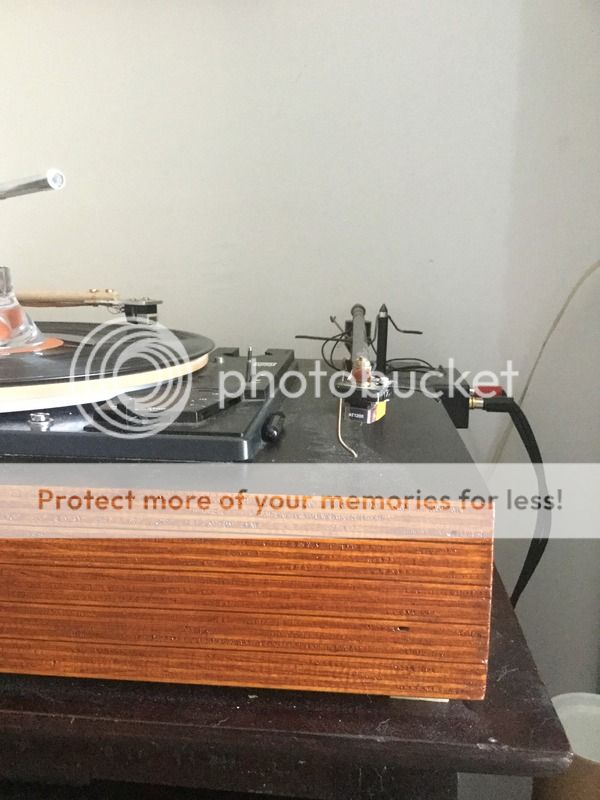
I've temporarily dampened it with bluetac, but will replace it with a wooden head using the same configuration less the washers as I plan to countersink the bolt heads in so it can sit ridgidly against the arm.
I'll still argue my new arm is in the spirit of the Nanook as it not only borrows much of the design, and was made from junk! It is however not as light an arm and favours a mid to low compliance cartridge.
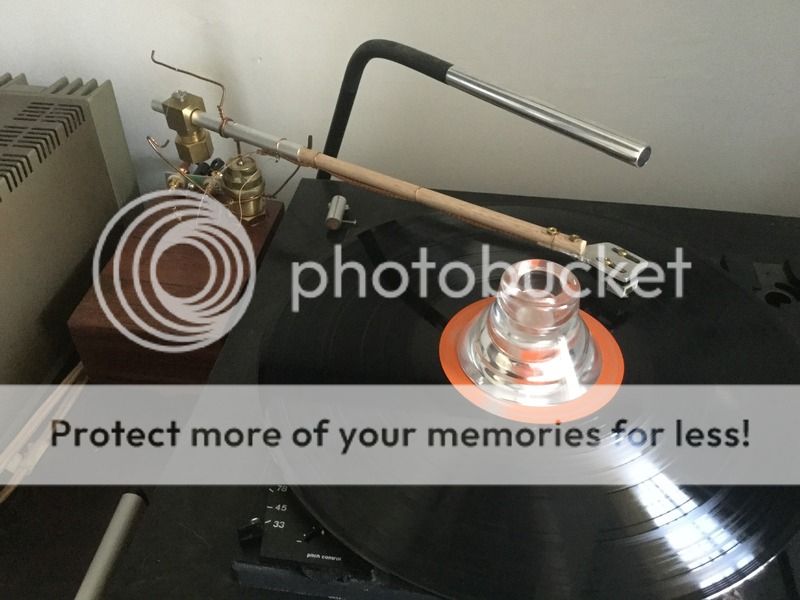
Love it Dan,
It definitely is in the 'Spirit' & plumbing fittings are great for All kinds of things I made a 'Nanook' & then later a Golf Ball WTA from them as well.
& you learn so much from doing this kind of thing....
Thanks

I'd love to see them!
In the 'Spirit" of...
All:
I'm not trying to beat anybody up here at all, so even though I've stated some of these arms are not a "nanook" (strictly speaking) they are certainly in the spirit of it, and could sound better than mine. In most cases, they do look better than some of the arms I've made.
ecodan and jay: I'd love to see others' arms and ideas as well. I followed the diyWTA and the diyScheu discussions for some time, but decided against them. I also have looked at diy linear trackers, etc. One arm I'd love to improve or 're-imagine' would be the Garrard "zero" arms, but using better bearings (etc) with less slop.Or perhaps a Thales arm. Both intrigue me.
Thanks
I'd love to see them!
All:
I'm not trying to beat anybody up here at all, so even though I've stated some of these arms are not a "nanook" (strictly speaking) they are certainly in the spirit of it, and could sound better than mine. In most cases, they do look better than some of the arms I've made.
ecodan and jay: I'd love to see others' arms and ideas as well. I followed the diyWTA and the diyScheu discussions for some time, but decided against them. I also have looked at diy linear trackers, etc. One arm I'd love to improve or 're-imagine' would be the Garrard "zero" arms, but using better bearings (etc) with less slop.Or perhaps a Thales arm. Both intrigue me.
that's the way for me too, Nanook: simple things are smarter than complicated ones.
After a century and 1500 types of tonearms on the market, maybe is difficult for us DIYers not to reinvent the wheel. And even more to build something better than serious manufacturers, using a chinese minilathe at most.
Our big advantage is to make mistakes without making others pay for them, learning step by step from our failures. This means to achieve the results just with a minimum of means (nanook / KISS style) to make errors clearly identifiable, as in any serious experiment.
This also calls to be really honest with ourselves, because it is so easy to fool our ears (especially after a lot of money or a lot of time ). For years I read about the sound of cables, of capacitors, NOS valves and so on, but never met someone complaining that his right channel sounded different from the left. Although there is no speaker (or none of the hundreds of components of the audio chain) identical to the other.
Certainly to listen to a 2.19 arm sounding like a $$$$ arm can be fascinating for someone, and frustrating for many others.
ciao - Carlo
Some time ago I sent a couple of - KISS style - experiments on your "a continuarion of diy....." posts 53 - 54. But very few there seemed interested to discuss the real role of the vertical movement (+ - 1 ° for a badly warped LP!)
After a century and 1500 types of tonearms on the market, maybe is difficult for us DIYers not to reinvent the wheel. And even more to build something better than serious manufacturers, using a chinese minilathe at most.
Our big advantage is to make mistakes without making others pay for them, learning step by step from our failures. This means to achieve the results just with a minimum of means (nanook / KISS style) to make errors clearly identifiable, as in any serious experiment.
This also calls to be really honest with ourselves, because it is so easy to fool our ears (especially after a lot of money or a lot of time ). For years I read about the sound of cables, of capacitors, NOS valves and so on, but never met someone complaining that his right channel sounded different from the left. Although there is no speaker (or none of the hundreds of components of the audio chain) identical to the other.
Certainly to listen to a 2.19 arm sounding like a $$$$ arm can be fascinating for someone, and frustrating for many others.
ciao - Carlo
Some time ago I sent a couple of - KISS style - experiments on your "a continuarion of diy....." posts 53 - 54. But very few there seemed interested to discuss the real role of the vertical movement (+ - 1 ° for a badly warped LP!)
good comments...
nocdplz:
Have you built a "nanook", and if so, what are your impressions?
True regarding that there is no identical sounding piece of audio equipment, but that is the reality of the cost of audio equipment. Yes, speaker cables (capacitors, etc.,) make a difference. All components have some resistance, capacitance and inductance. So every passive component acts as some sort of filter. It is just that the larger the signal, the more apparent they are.
nocdplz:
Have you built a "nanook", and if so, what are your impressions?
Not necessarily, but for something like a mechanical device I think so.that's the way for me too, Nanook: simple things are smarter than complicated ones.
I disagree with this point. The Chinese may have the technical skills but some lack the understanding. An example: years ago I had to rework a couple of Chinese tables for Ian Grant. The Chinese maker had the basic concept correct, but it was in the execution of the design that showed a clear lack of understanding (and this was a turntable manufacturer).After a century and 1500 types of tonearms on the market, maybe is difficult for us DIYers not to reinvent the wheel. And even more to build something better than serious manufacturers, using a chinese minilathe at most.
TO me (thankfully) I don't see too many mistakes or errors in the "nanook 219". I have made slow refinements (I have added a "safety" cup to help keep the arm on the pivot if mishandled which serves as a point to mount an arm for anti-skating adjustment) but the arm is essentially the same as my original one.Our big advantage is to make mistakes without making others pay for them, learning step by step from our failures. This means to achieve the results just with a minimum of means (nanook / KISS style) to make errors clearly identifiable, as in any serious experiment.
I know we (as humans) often have a self bias about what we might make, build or purchase. That's why I rely on friends (whose ears I trust) to make comments and be as critical as possible.This also calls to be really honest with ourselves, because it is so easy to fool our ears (especially after a lot of money or a lot of time ). For years I read about the sound of cables, of capacitors, NOS valves and so on, but never met someone complaining that his right channel sounded different from the left. Although there is no speaker (or none of the hundreds of components of the audio chain) identical to the other.
True regarding that there is no identical sounding piece of audio equipment, but that is the reality of the cost of audio equipment. Yes, speaker cables (capacitors, etc.,) make a difference. All components have some resistance, capacitance and inductance. So every passive component acts as some sort of filter. It is just that the larger the signal, the more apparent they are.
For me the frustration was/is the cost of admission for a reasonable tonearm. Turntables are around and are often offered for purchase at reasonable pricing, but good arms seem to maintain their value. I believe the cost of a new tonearm is what keeps many from trying vinyl. In my case I thought to try a concept (after actually designing in my parameters from the start) that was based on Altman's "joke tonearm" concept, except using better materials that were easy to find and purchase. To my astonishment it played in the same range as my (CAD) $2600 SME 309. There were/are pluses and minuses to both arms when directly compared, but overall the "219" is competitive with the 309.Certainly to listen to a 2.19 arm sounding like a $$$$ arm can be fascinating for someone, and frustrating for many others.
Sorry to have not read them (I gave up on some threads), but I will now. I look forward to gaining from your insight.Some time ago I sent a couple of - KISS style - experiments on your "a continuarion of diy....." posts 53 - 54. But very few there seemed interested to discuss the real role of the vertical movement (+ - 1 ° for a badly warped LP!)
Thanks for your reply, Nanook. Fully agree, although my bad English often causes some misunderstandings.
During a decade or more I've ended 5 or 6 different tonearms (with one Chinese 9x20 lathe; now the Chinese manufacture the most advanced smartphones, but minilathes did not improve as much as we need - e.g. for a platter spindle).
I tried to explore the different types (gimbal, unipivot, suspended etc) starting from the most mechanically complex and simplifying step by step, trying to understand what was important and what was not. The latter made are the two posted on your other thread (with a premise that I liked, to talk about direct experience and not hearsay) that sound correctly (even for "not so friends"), as much as my microseiki and others well known. Along this path I also made a "Nanook style" that opened my eyes, and ears: nothing to add, nothing to substract, just a ton of experiences behind, like in a racing bicycle.
Those efforts make me think that it's important to focus on what really matters* instead of accumulating unnecessary complications that often lead to more problems than they take away (linears, parallelograms and so on): for me the tonearm should be a tool, not an expensive, ornamental gadget.
Carlo
*just to talk: force vectors: hor. & vert. geometry - azimuth: tracking & skating problems - resonances: tolerances, matching, damping, and so on. Beginning from the cantilever back to the plinth, not forgetting the variable of the cartridge loading
During a decade or more I've ended 5 or 6 different tonearms (with one Chinese 9x20 lathe; now the Chinese manufacture the most advanced smartphones, but minilathes did not improve as much as we need - e.g. for a platter spindle).
I tried to explore the different types (gimbal, unipivot, suspended etc) starting from the most mechanically complex and simplifying step by step, trying to understand what was important and what was not. The latter made are the two posted on your other thread (with a premise that I liked, to talk about direct experience and not hearsay) that sound correctly (even for "not so friends"), as much as my microseiki and others well known. Along this path I also made a "Nanook style" that opened my eyes, and ears: nothing to add, nothing to substract, just a ton of experiences behind, like in a racing bicycle.
Those efforts make me think that it's important to focus on what really matters* instead of accumulating unnecessary complications that often lead to more problems than they take away (linears, parallelograms and so on): for me the tonearm should be a tool, not an expensive, ornamental gadget.
Carlo
*just to talk: force vectors: hor. & vert. geometry - azimuth: tracking & skating problems - resonances: tolerances, matching, damping, and so on. Beginning from the cantilever back to the plinth, not forgetting the variable of the cartridge loading
Hey there,
sachin recommended this thread ( and Tone-Arm) as a great read and addition to my lenco.
i am wondering how hard it is to set up for a noob, i am building a plinth for a 12" Arm with a mounting distance of 290 / 295mm.
By going through the almost 100 pages here i stumbled upon some use of Sapphire Vee Jewel Bearings and i found one locally here for quite cheap.
its tiny though,its probably too small to use for this application, especially with a ball pen-male?
maybe a bigger female? It seems worthwhile to focus on the Uni-pivot bit of the arm since it is the only bearing here
maybe one could use a needle of a compass (the one for drawing, i might be missing a word here) in a small drill chuck. still all second hand stuff or really cheap to get.
Thanks guys!
i like the stuff you come up with here
cheers!
Juergen
sachin recommended this thread ( and Tone-Arm) as a great read and addition to my lenco.
i am wondering how hard it is to set up for a noob, i am building a plinth for a 12" Arm with a mounting distance of 290 / 295mm.
By going through the almost 100 pages here i stumbled upon some use of Sapphire Vee Jewel Bearings and i found one locally here for quite cheap.
its tiny though,its probably too small to use for this application, especially with a ball pen-male?
maybe a bigger female? It seems worthwhile to focus on the Uni-pivot bit of the arm since it is the only bearing here
maybe one could use a needle of a compass (the one for drawing, i might be missing a word here) in a small drill chuck. still all second hand stuff or really cheap to get.
Thanks guys!
i like the stuff you come up with here
cheers!
Juergen
Attachments
Last edited:
yurgs, welcome to the frenzy...(well not really a frenzy)
sachin: is pretty good guy and is smart as well. If he suggested this thread to you (does he know you personally?) there must be something here to glean from this (somewhat) long thread.
I've stated so many times that any variance from the "recipe" I've provided for the 219 tonearm results in an arm of unknown quality and character. I'm not saying these variances are bad ... just that there are so many that I can't comment on what the sound might be like.
I did think of using jewel Vee bearings as a further refinement. I'm not sure what the sound would be like though. The use of a sharp steel phonograph needle (replaceable types like this ) would be very good I think and perhaps easier to get and hard enough without being too hard.
sachin: is pretty good guy and is smart as well. If he suggested this thread to you (does he know you personally?) there must be something here to glean from this (somewhat) long thread.
I've stated so many times that any variance from the "recipe" I've provided for the 219 tonearm results in an arm of unknown quality and character. I'm not saying these variances are bad ... just that there are so many that I can't comment on what the sound might be like.
I did think of using jewel Vee bearings as a further refinement. I'm not sure what the sound would be like though. The use of a sharp steel phonograph needle (replaceable types like this ) would be very good I think and perhaps easier to get and hard enough without being too hard.
- Status
- This old topic is closed. If you want to reopen this topic, contact a moderator using the "Report Post" button.
- Home
- Source & Line
- Analogue Source
- my latest iteration of "Nanook's 219 tonearm"..