The would be careful about linearity complain. These speakers have well under 1% distortion across almost all sound band while playing quite loud. Directivity allows tune them for proper position. They are in a very small group of full range speakers that can work well in small rooms, which is a great achievement.They are seriously flawed speakers, with regard to linearity as well as directivity control.
It can be as some cabinet makers have CNC machines and can do flat packs if you supply the plans.
Lots of cabinets that a regular 3 axis CNC cannot do.
dave
The B&W 8xx enclosures appear to be bendy ply glued to formers. That sort of construction does not require any special tooling.
Well they certainly do use special tooling.
http://blog.bowers-wilkins.com/sound-lab/film-the-making-of-an-800-series-diamond-loud-speaker/
dave
Mass produced speaker systems, even the "high end" types are a compromise between the designer and the manufacturing engineer. Runs of the same design can not be tweaked individually to meet a customers demand.What sounds good to one person is poor to another, with measurements meaning nothing to the subjective listener. When we build our own we build them to what we want to hear and for the type of music we like.
Well they certainly do use special tooling.
Film: The making of an 800 Series Diamond loud-speaker | Society of Sound
dave
4 days of finish polishing 'the bulk' costs a pretty penny too.
Interesting to see what what's not inside the bigger tear-drop
Last edited:
special tooling & procedures, indeed
Whom among us wouldn't like to have even occasional access to a router capable of machining dadoes inside an elliptically curved shell, assuming we could fabricate that accurately in the first place?
Whom among us wouldn't like to have even occasional access to a router capable of machining dadoes inside an elliptically curved shell, assuming we could fabricate that accurately in the first place?
Attachments
Have you seen this? Building (2) High End Tower Speakers - Blu-ray Forum
An example of what some DIY-ers can do... Granted he had access to some nice tools but with a bit (or a lot
) of creativity there isn't much of a limit of what you actually can accomplish.
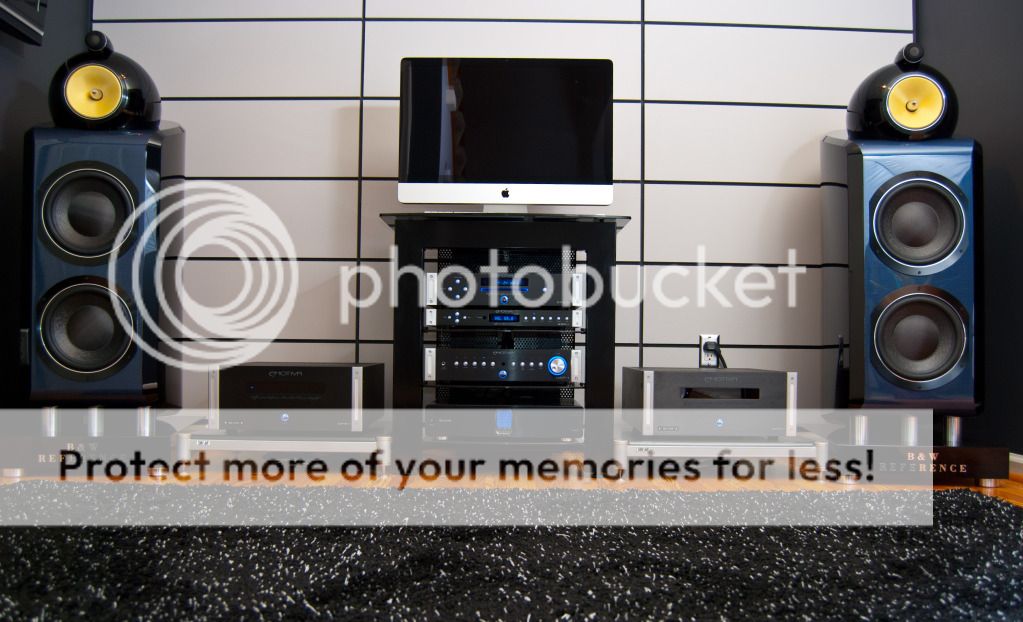
An example of what some DIY-ers can do... Granted he had access to some nice tools but with a bit (or a lot
Last edited:
Can't remember, it has been a while ago that I read it. Personally I'm not into the copying and would rather be inspired and build my own idea. Still I do admire the skills that went into making this.
Edit:
Edit:
Reference on Blu-ray.com said:I don't even remember when I started this project. I think it took me about 6 month to complete it. It was a wonderful and very challenging project.
Last edited:
Whom among us wouldn't like to have even occasional access to a router capable of machining dadoes inside an elliptically curved shell, assuming we could fabricate that accurately in the first place?
Well machining dadoes inside is a curved shell is probably out for 99.9% of DIYers, but I still maintain that this sort of shell is not that hard to make in a home garage shop or whatever.
That B&W jig is pretty cool, but not super expensive. It looks shop made to me. No cast metal parts or heated plattens, which means they are using cold set glue instead of thermosetting phenolic (etc).
The thing was probably built up out of stacked plywood patterns which were cut with a router table. That can be done in a home garage. For a home version, screw jacks or F clamps could replace the hydraulic jacks. It could be made much lighter. Most of the bulk is excessive if you are going to lay up a handful of shells instead of thousands. For quick and dirty, you could lose the female part of the form entirely, and just wrap kerfed MDF around it secured with a lot of strap clamps.
Can't remember, it has been a while ago that I read it. Personally I'm not into the copying and would rather be inspired and build my own idea. Still I do admire the skills that went into making this.
I agree.
Personally I don't care for the looks of B&W much anyway. Nice to see people go all out on stuff though.
To add to my previous post, obviously one could simply use kerfed mdf for the actual shell. I must have blocked the possibility of MDF from my brain.
BTW some bendy ply is bendy enough to get around that all in one piece just like the evil kerfed mdf.
Apparently kids don't make balsa wood airplane models anymore, or none of this would seem weird.![]()
They make RC airplanes out of foam core nowadays. Foam core can also be used to make curvy tear drop shaped speakers.
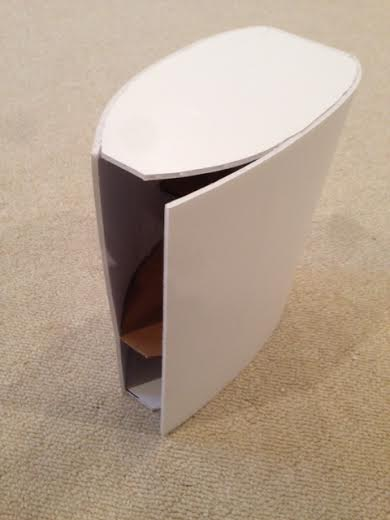
" bendy" ply hereabouts generically trade term would be "rubber" ply - approx 1/4"
Greg- that I find some shapes so aesthetically appealing to merit copying, I'll not apologize for
Have actually tried both the phenolic paper and 2 ply veneer faced "kerf-core" sheet goods in the past, and prefer the structural rigidity of 3or 4 layers of vacuum bagged rubber ply. It's certainly more work by the time you fabricate a sturdy enough form to withstand the force of approx 1 atmosphere (~ 1 ton per sq ft) but I think you get better results in the long run. Both pairs in the photo Dave referenced were made from the same form, and I'd be surprised if I didn't use it yet again. With either method, you still need to fabricate the skeleton frame around which the curved panels will be wrapped.
Greg- that I find some shapes so aesthetically appealing to merit copying, I'll not apologize for
Have actually tried both the phenolic paper and 2 ply veneer faced "kerf-core" sheet goods in the past, and prefer the structural rigidity of 3or 4 layers of vacuum bagged rubber ply. It's certainly more work by the time you fabricate a sturdy enough form to withstand the force of approx 1 atmosphere (~ 1 ton per sq ft) but I think you get better results in the long run. Both pairs in the photo Dave referenced were made from the same form, and I'd be surprised if I didn't use it yet again. With either method, you still need to fabricate the skeleton frame around which the curved panels will be wrapped.
Last edited:
… and I'd be surprised if I didn't use it yet again...
Those curvy Pensil7.x could wellbe popular… and maybe even useful for larger & smaller Pensils and similar (MTM with Silver Flute W14?).
dave
Have you seen this? Building (2) High End Tower Speakers - Blu-ray Forum
![]()
An example of what some DIY-ers can do... Granted he had access to some nice tools but with a bit (or a lot) of creativity there isn't much of a limit of what you actually can accomplish.
That is a very nice work. But if it was worth it financially? Considering it took 6 month to build. This is 26 weeks. Let's assume he spent 8 hours per week (reasonable if it was not full time job). So we have 208 hours. Now consider cheap labor rate at $50/hour. This gives us about $10K just in labor cost. You can buy original 802D for $12K and 800D for $20K. If buy 3 yeas old used, can get 40% less than that. And we are not even touching question if these speakers sound better or worth than the original B&W.
Apparently kids don't make balsa wood airplane models anymore, or none of this would seem weird.![]()
Tis a rare breed these days that douses sheet balsa with freshly piped urine and boiling water to get it to form correctly
- Status
- This old topic is closed. If you want to reopen this topic, contact a moderator using the "Report Post" button.
- Home
- Loudspeakers
- Full Range
- DIYers stay the course - much better value building your own!