Spots are beyond what we are talking about. Much simplier treatments, as discussed in this thread, can hav esignificant affect.
And yet Toole say sthat it is still not good enuff. The guy who has done some of the most saying it is still not enuff. He has HUGE credibility.
dave
And yet Toole say sthat it is still not good enuff. The guy who has done some of the most saying it is still not enuff. He has HUGE credibility.
dave
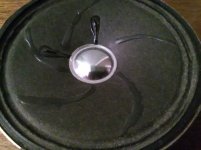
Perhaps it's not just the material used for the coating, but also the " pattern " - I did these " swirls " ( in PVA wood glue ) many years ago in an effort to dampen the ripples that go from the centre of the cone to the edge and reflected again. Unfortunately the rest of the hi fi wasn't good enough to reveal any noticeable improvement, but food for thought . Didn't the BBC ( or KEF ) coat the cones of the LS35a ?
Felt pads can do miracles, are cheap, available worldwide and even detachable. remember to take nearfield measurements before/after!
Have you ever tried with 5 or 7 felt pads ?
Regards
Charles
'Even' Troels G succeeded in measuring the differences. Your remark isn't backed up by observations.And we well know that we have yet to figure a way to measure this so measurements may show us gross changes but the important stuff does not show.
+1. Dave do you really think driver manufactures other than MarkAudio are still Wizzards &Magicians with high hats? Designers now have Klippel, PafSys, Comsol, Finecone etc.
I am certainly aware of the inherent limitatations advanced modelling still has, but the basic "raw" transducer behaviour and properties are all reasonably well mapped and thus predictable. Modelling conforms the real built to a surprisingly high degree.
I am certainly aware of the inherent limitatations advanced modelling still has, but the basic "raw" transducer behaviour and properties are all reasonably well mapped and thus predictable. Modelling conforms the real built to a surprisingly high degree.
'Even' Troels G in measuring the differences/
One can measure fixes if they cause a difference significant enuff to measure. Most of the things that these kinds of tweaks can bring are subtler than that.
An example is the damping ring at the surround/cone interface on the back of FExx6 and FFxx5wk drivers can also be measrured.
dave
What are for you the more magical FR, Planet10 ? SOme with more efficienty ? What's your favs in this more magical league, please ?
A mate would like to put a EMS-Speakers LBII, a 8" FR ib a huge horn made for some AER, Voxative, etc , is a good idea to put such FR for 300 hz to 15/20 K hz in a huge horn à la JMLC ?
A mate would like to put a EMS-Speakers LBII, a 8" FR ib a huge horn made for some AER, Voxative, etc , is a good idea to put such FR for 300 hz to 15/20 K hz in a huge horn à la JMLC ?
After reasonable FR and extension I am interested most in maximizing DDR/detail as this is the small stuff that brings a greater ability to bring “life” to instrument & voice and the information critical to a solid 3D image/soundstage (if on the software you are playing)
What driver is best is dependent on the application. And i am not afraid of mechanical fixes are the source for driver issues.
My favorite drivers are all EnABLed. I can certaiy hear the difference (proven in double blind listening tests).
A7.3, A7ms, A103/0, A11ms, CHN-110, A5.2/3, A6.2m/p, Fostex FF85wk, Visaton B200, SEAS FA22 are the favourites that comes to mind. Some are easy to work with (SEAS) and some a real challenge (B200). Both need dustcapectomy and phase plugs. B200 is unusable without them. You can see many MA but only one example of other brands.
Most notable drivers i have heard that i am not a fan of include TB1772/1808 (too coloured, too pricey) Audio Nirvana (just bad. lots of ringing in the ones i heard), Jordan (top end issues, same heard in first generation Mark Audio). JX150 i like. And a particualrily dissapointing set of Feastrex FCs. I have not heard them all. Lots of vintage drivers that are good with lots of potential, but i feel the best modern drivers have surpassed the staes of the past.
dave
What driver is best is dependent on the application. And i am not afraid of mechanical fixes are the source for driver issues.
My favorite drivers are all EnABLed. I can certaiy hear the difference (proven in double blind listening tests).
A7.3, A7ms, A103/0, A11ms, CHN-110, A5.2/3, A6.2m/p, Fostex FF85wk, Visaton B200, SEAS FA22 are the favourites that comes to mind. Some are easy to work with (SEAS) and some a real challenge (B200). Both need dustcapectomy and phase plugs. B200 is unusable without them. You can see many MA but only one example of other brands.
Most notable drivers i have heard that i am not a fan of include TB1772/1808 (too coloured, too pricey) Audio Nirvana (just bad. lots of ringing in the ones i heard), Jordan (top end issues, same heard in first generation Mark Audio). JX150 i like. And a particualrily dissapointing set of Feastrex FCs. I have not heard them all. Lots of vintage drivers that are good with lots of potential, but i feel the best modern drivers have surpassed the staes of the past.
dave
C37?
Too much can make the cone too stiff and start ringing. Smaller amounts work well on some drivers (Visaton B200/CSS FR125) but thinned PVA seems to produce very similar magnitudes of improvement but costs a minicule amount. Unlike lacquer, too much just wipes out the top end (sometimes an asset).
dave
Too much can make the cone too stiff and start ringing. Smaller amounts work well on some drivers (Visaton B200/CSS FR125) but thinned PVA seems to produce very similar magnitudes of improvement but costs a minicule amount. Unlike lacquer, too much just wipes out the top end (sometimes an asset).
dave
The higher end Scanspeak drivers use a grooved pattern along the cone surface and fill it with a dampening substance, which i think is pretty smart.
There are some drivers that use progressive thickness cones, some of which taper towards the outside diameter. This type of cone often responds negatively to uncontrolled hand application of dampening materials, mainly because you're potentially adding much more mass on the outside diameter of the cone compared to the center, which ruins the driver upper FR. This type of cone does however respond very well to dampening the cone edge to surround interface induced breakup and bell mode resonances, getting rid of most if not all the typical midrange response kink it causes in untreated form.
I'm a big proponent of weighing the amount of dampening substance before and after application to obtain consistent results between driver pairs and for the sake of repeating the results if they were favorable.
Regarding silicone compounds, they do work depending on the specific type used and not all are suited the same (or even similar) for speaker cone dampening. The Permatex flowable silicone works well for lighter weight cones and sealing cloth surrounds because it adds less mass than most PVA based compounds. It dries clear and is self leveling, plus the working time is a bit longer which is a plus when treating larger cones. It also won't warp paper cones like other thinner water based substances, plus you end up with a moisture resistant surface and its more environmentally stable in the long term. This is a big plus with urethane based foam surrounds.
PVA does work better with paper cone drivers because it has better thermo dynamic conversion properties (converting mechanical energy into heat). Thats why its used so much compared to other compounds, plus its also easier to apply and non toxic. Most dome tweeters and mids use PVA based surface treatments. Plastic and polymer cone materials usually do better with visco elastic (latex) based dampening compounds, mainly because these cone materials don't bond well with water based coatings in the long run. Most kevlar cones I've seen use latex coatings. Without them, these cone materials exhibit very harsh, high Q breakup modes simlar to metal cone drivers.
There are some drivers that use progressive thickness cones, some of which taper towards the outside diameter. This type of cone often responds negatively to uncontrolled hand application of dampening materials, mainly because you're potentially adding much more mass on the outside diameter of the cone compared to the center, which ruins the driver upper FR. This type of cone does however respond very well to dampening the cone edge to surround interface induced breakup and bell mode resonances, getting rid of most if not all the typical midrange response kink it causes in untreated form.
I'm a big proponent of weighing the amount of dampening substance before and after application to obtain consistent results between driver pairs and for the sake of repeating the results if they were favorable.
Regarding silicone compounds, they do work depending on the specific type used and not all are suited the same (or even similar) for speaker cone dampening. The Permatex flowable silicone works well for lighter weight cones and sealing cloth surrounds because it adds less mass than most PVA based compounds. It dries clear and is self leveling, plus the working time is a bit longer which is a plus when treating larger cones. It also won't warp paper cones like other thinner water based substances, plus you end up with a moisture resistant surface and its more environmentally stable in the long term. This is a big plus with urethane based foam surrounds.
PVA does work better with paper cone drivers because it has better thermo dynamic conversion properties (converting mechanical energy into heat). Thats why its used so much compared to other compounds, plus its also easier to apply and non toxic. Most dome tweeters and mids use PVA based surface treatments. Plastic and polymer cone materials usually do better with visco elastic (latex) based dampening compounds, mainly because these cone materials don't bond well with water based coatings in the long run. Most kevlar cones I've seen use latex coatings. Without them, these cone materials exhibit very harsh, high Q breakup modes simlar to metal cone drivers.
Well, musical instruments evolved by ear not by measurement. So I think the haptic approach to speakers is valid, though ideally one should make only changes that are reversible if they don't work!
I recall a very vintage (1940s) 8-inch chassis that was particularly uncoloured compared with others of similar size. This one had a DC-energised electromagnet, run warm for plenty of field, and the paper cone was multiple corrugated, very fine pattern, radially and concentrically. Sounded beautiful on all sources, no shout, no honk, topped out with a little electrostatic tweeter. Intuition told me do nothing, and I put away the lacquer can.
I recall a very vintage (1940s) 8-inch chassis that was particularly uncoloured compared with others of similar size. This one had a DC-energised electromagnet, run warm for plenty of field, and the paper cone was multiple corrugated, very fine pattern, radially and concentrically. Sounded beautiful on all sources, no shout, no honk, topped out with a little electrostatic tweeter. Intuition told me do nothing, and I put away the lacquer can.
- Home
- Loudspeakers
- Multi-Way
- damping coating substances for speakers' cones ?