Hello,
I can't remember if I have mentioned my DIY Tonearm here yet, but here it is:
The arm tube is made from Bamboo (£0), and the horizontal bearing is the head drum from a VHS machine (£0). The vertical bearing is of the knife-edge type, using a stanley blade (£1) resting on the edges of the head drum. There are some small grooves in the drum, cut with a staney knife, to sotp the arm moving back and forth. The counterweight and headshell are coppers (£0.33). The whole lot is stuck together with Araldite (£2.50-ish). The fingerlift is made from a steel rod from a Pioneer Midi size TT (£0), where the phono stage and wiring came from.
The arm has an AT-110E mounted on it, and is mounted on a Thorens TD150 MKII.
I suspect that the effective mass is a little high for the cart, but I don't have a test LP to try it with.
I can't remember if I have mentioned my DIY Tonearm here yet, but here it is:
The arm tube is made from Bamboo (£0), and the horizontal bearing is the head drum from a VHS machine (£0). The vertical bearing is of the knife-edge type, using a stanley blade (£1) resting on the edges of the head drum. There are some small grooves in the drum, cut with a staney knife, to sotp the arm moving back and forth. The counterweight and headshell are coppers (£0.33). The whole lot is stuck together with Araldite (£2.50-ish). The fingerlift is made from a steel rod from a Pioneer Midi size TT (£0), where the phono stage and wiring came from.
The arm has an AT-110E mounted on it, and is mounted on a Thorens TD150 MKII.
I suspect that the effective mass is a little high for the cart, but I don't have a test LP to try it with.
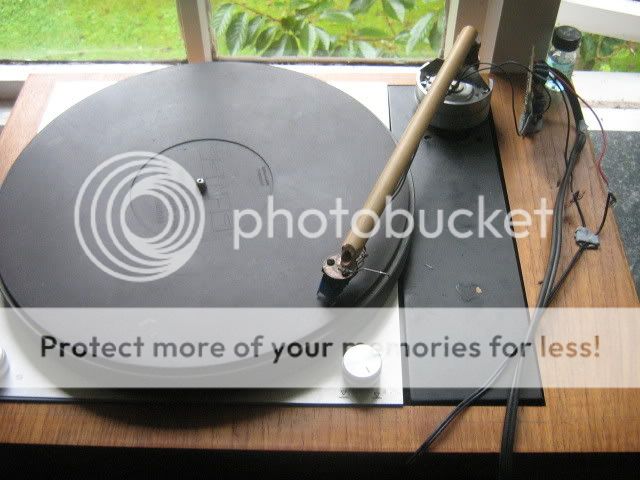
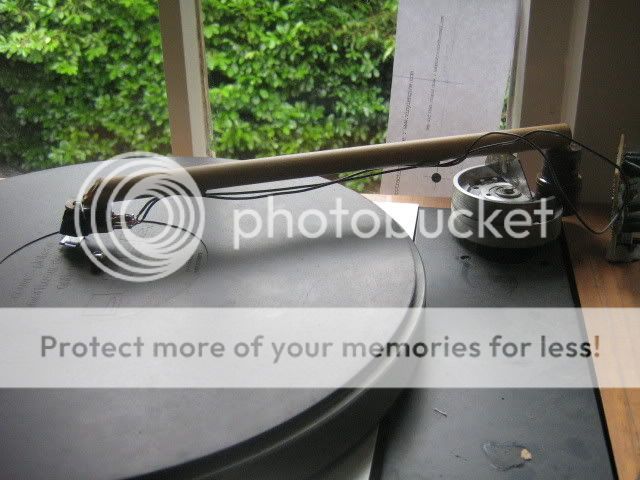
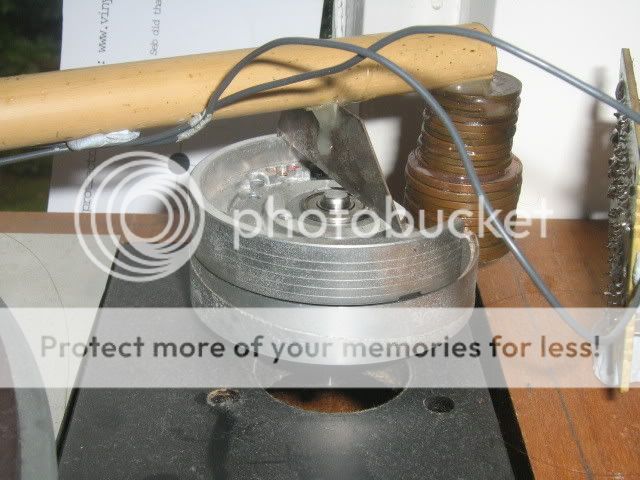
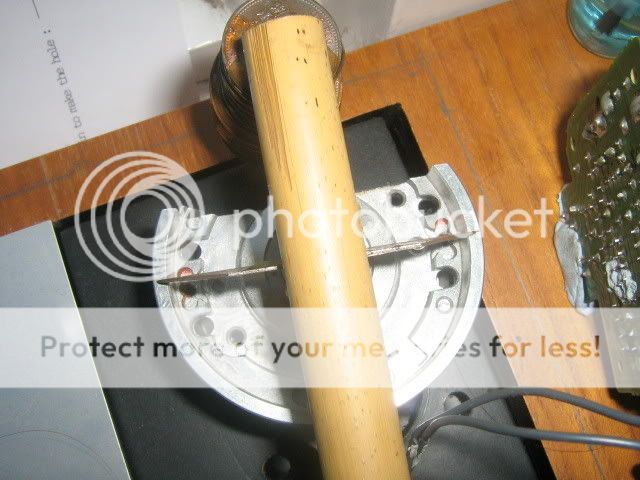
ssmith said:
1.The Altmann DIY Unipivot seems to be the one that started it all -- it's cheap'n'ugly, and allegedly sounds damn good. So anyone who's tried it and compared it with a mass market one (something like a Rega RB250?) please report here!
This is a better looking version.
ssmith
That second example reminds me; I've heard of people using an old violin bow.
That said, I don't know if violin bows are particurly cheap.
Looks like it should work quite well! You have the vertical pivot somewhere around the height platter surface, which is good.
One thing you should be aware of though - "coppers" have been made of steel (copper plated) for some years now, and they're very magnetic.
jrevillug said:The counterweight and headshell are coppers (£0.33).
One thing you should be aware of though - "coppers" have been made of steel (copper plated) for some years now, and they're very magnetic.
Sorry, Zen Mod, didn't see your reply untill just now. Thanks.
Yes, the arm cables shown there were too thick - they tended to pull the arm in either direction to a fixed point. I have now replaced the cables with wire salvaged from a BSR autochanger - thin and flexible.
I have also go a different amplifier (with a built-in phono stage), so the arm cables just go into a interconnect wire now.
James
Yes, the arm cables shown there were too thick - they tended to pull the arm in either direction to a fixed point. I have now replaced the cables with wire salvaged from a BSR autochanger - thin and flexible.
I have also go a different amplifier (with a built-in phono stage), so the arm cables just go into a interconnect wire now.
James
arm cable
Try fine gage magnet wire. I've tried anything from 40 ga. to 20 ga., and like 34ga. the best for flexability and sound. You can twist all wires togeather or just channel pairs (this sounded the best to me, MHO). Forget the wire clips, wire wrap the bare 34 ga. directly to the cartridge pins!
Try fine gage magnet wire. I've tried anything from 40 ga. to 20 ga., and like 34ga. the best for flexability and sound. You can twist all wires togeather or just channel pairs (this sounded the best to me, MHO). Forget the wire clips, wire wrap the bare 34 ga. directly to the cartridge pins!
Tonearm Wire
I have been using the Fine Silver/Teflon wire from A-M Systems. It works and sounds great! They were very easy to order from and have a great selection...
http://www.a-msystems.com/physiology/wirerod/silvertef.aspx
I have been using the Fine Silver/Teflon wire from A-M Systems. It works and sounds great! They were very easy to order from and have a great selection...
http://www.a-msystems.com/physiology/wirerod/silvertef.aspx
I like the video drum bearing idea, and the widely separated vertical pivot points. Nice. Why not make that phono stage a bit smaller and hang it off the back together with the counterweight? That way, you could use fine unscreened wires to carry the signal from the arm and reduce your friction.
That's a good idea - however, the arm has moved on a little in the last year and a half.
I'm still using it though.
The arm wires are still those from the autochanger, and go from the top of the arm above the pivot in an 'n' shape to the plinth, where it attaches directly to the phono lead. That runs to the amp as normal. The phono stage shown there has been consigned to the shelf, awaiting, in all probability, parts scavenging and disposal.
The deck, VHS head drum and the 'headshell' coin are connected together and earthed via a separate wire to the amp. I get no hum at all - just the whooshing noise of the phono stage.
I have re-mounted the armboard to move the pivot a bit closer to the spindle, to improve the alignment of the cartridge.
I also added an antiskate mechanism - just a piece of thread round the drum, over a wire hook and down to a weight (experimentally decided as needing to be 2 drawing pins).
I will put some more photos up at some point but being in the middle of exams doesn't leave much free time.
James
EDIT - I love your signature, EC8010.
I'm still using it though.
The arm wires are still those from the autochanger, and go from the top of the arm above the pivot in an 'n' shape to the plinth, where it attaches directly to the phono lead. That runs to the amp as normal. The phono stage shown there has been consigned to the shelf, awaiting, in all probability, parts scavenging and disposal.
The deck, VHS head drum and the 'headshell' coin are connected together and earthed via a separate wire to the amp. I get no hum at all - just the whooshing noise of the phono stage.
I have re-mounted the armboard to move the pivot a bit closer to the spindle, to improve the alignment of the cartridge.
I also added an antiskate mechanism - just a piece of thread round the drum, over a wire hook and down to a weight (experimentally decided as needing to be 2 drawing pins).
I will put some more photos up at some point but being in the middle of exams doesn't leave much free time.
James
EDIT - I love your signature, EC8010.
jrevillug said:I also added an antiskate mechanism - just a piece of thread round the drum, over a wire hook and down to a weight (experimentally decided as needing to be 2 drawing pins).
Blutak is great for fine adjustment of bias force. I have a beautifully machined hollow aluminium weight and just vary the amount of Blutak inside.
more & less
Hello everyone, I am not new in Diyaudio, but this is my first post, so forgive me, and my bad english (maybe you'll prefer to my good italian)
my nickname will tell you that I am an analogue addict, and the work of Altmann for me was a real revelation, at least like to discover that a set tube amp with ten components sounded better than my ipod.
I tried to make tonearms in many different ways, unipivot included, then I asked myself: one pivot alone? maybe too much.
here is the result, and it plays.
ciao - Carlo
wavy lp? throw them away, or keep them better
Hello everyone, I am not new in Diyaudio, but this is my first post, so forgive me, and my bad english (maybe you'll prefer to my good italian)
my nickname will tell you that I am an analogue addict, and the work of Altmann for me was a real revelation, at least like to discover that a set tube amp with ten components sounded better than my ipod.
I tried to make tonearms in many different ways, unipivot included, then I asked myself: one pivot alone? maybe too much.
here is the result, and it plays.
ciao - Carlo
wavy lp? throw them away, or keep them better
Attachments
more 'n less 2
I sent two "silly" realizations that seem to lack of articulation for vertical movements (like the cutting lathe..). Maybe so silly that someone can't understand my drawings, or has mercy on me.
So i've added a few words
(see attachments).
ciao Carlo
I sent two "silly" realizations that seem to lack of articulation for vertical movements (like the cutting lathe..). Maybe so silly that someone can't understand my drawings, or has mercy on me.
So i've added a few words
(see attachments).
ciao Carlo
Attachments
vertical movement
Very interesting concept, nocdplz. (Great username!) It seems in both arms the vertical movement is based on compliance, the flexing of material in the Plexiglas and piano wire. My question is that do you encounter changing tracking force when altering VTA?
And in the Plexiglas arm, during needle drop do you have to hold the armlift until you get to the playing area? How does it handle warped records, does the arm have enough flex to accommodate it without damaging the cartridge?
Thank you for your post.
--------------------------------
In production tonearms, the only design I am aware of using "flex" bearing is the extremely expensive Vertere Reference tonearm that "the unique Vertical & Horizontal pivoting motion is provided by non-rotating polymer-metal laminate films. The result is the first truly ‘noiseless’ and stiction-free tonearm bearing."
Very interesting concept, nocdplz. (Great username!) It seems in both arms the vertical movement is based on compliance, the flexing of material in the Plexiglas and piano wire. My question is that do you encounter changing tracking force when altering VTA?
And in the Plexiglas arm, during needle drop do you have to hold the armlift until you get to the playing area? How does it handle warped records, does the arm have enough flex to accommodate it without damaging the cartridge?
Thank you for your post.
--------------------------------
In production tonearms, the only design I am aware of using "flex" bearing is the extremely expensive Vertere Reference tonearm that "the unique Vertical & Horizontal pivoting motion is provided by non-rotating polymer-metal laminate films. The result is the first truly ‘noiseless’ and stiction-free tonearm bearing."


Last edited:
vertical movement
thanks Directdriver: it' an experiment more than a concept.
I made some arms from different schools trying to understand what is important and what is not (or very little, at least to my ears) and trying to reduce the variables. Lesson learned is that tonearm's (and TT) role is only to leave the cartridge in peace to do his dirty work. I also believe that, about the geometry and physics of the tonearms everything was just said in the thirties, and there's no need to lose time any more.
I try to answer to your questions: these arms are certainly not-so comfortable to use (like our tube amps), and of course the VTA is vital to set the tracking force (totally for the H arm, partially for the J). In the drawings you see an height adjustment screw, and a sort of armlift, but they are not essential. The essential point instead is the flexing material: I used 0.8 - 1 mm for steel wire, and 1- 1.2mm sheet of plexiglas or lexan, but it depends on the total weight, the height etc. The lexan is not the best because is influenced by temperature, maybe better the carbon fiber or the plywood used for model aircrafts. But i have still to find and try.
Of course at the headshell level you must get more flexing than the stylus, but risks with warped records maybe are less than that from the inertia of a heavy headshell / counterweight (not to talk of the stop&go motion of a linear tracking).
Anyway, to put together a rough version of these arms is quick and easy, and the funny thing is that they play like many others, and not the worst: which (like the Altmann Joke) gives a lot to think about the value of what someone claims and sells around
Alighiszem: thanks for the link. are there some drawinngs of that arm? i can't understand how it works
Carlo
P.S. glad to be in a so expensive company: there are so many clever minds in tonearms design (more than in potato-peelers) that there is place even for silly diyers.
thanks Directdriver: it' an experiment more than a concept.
I made some arms from different schools trying to understand what is important and what is not (or very little, at least to my ears) and trying to reduce the variables. Lesson learned is that tonearm's (and TT) role is only to leave the cartridge in peace to do his dirty work. I also believe that, about the geometry and physics of the tonearms everything was just said in the thirties, and there's no need to lose time any more.
I try to answer to your questions: these arms are certainly not-so comfortable to use (like our tube amps), and of course the VTA is vital to set the tracking force (totally for the H arm, partially for the J). In the drawings you see an height adjustment screw, and a sort of armlift, but they are not essential. The essential point instead is the flexing material: I used 0.8 - 1 mm for steel wire, and 1- 1.2mm sheet of plexiglas or lexan, but it depends on the total weight, the height etc. The lexan is not the best because is influenced by temperature, maybe better the carbon fiber or the plywood used for model aircrafts. But i have still to find and try.
Of course at the headshell level you must get more flexing than the stylus, but risks with warped records maybe are less than that from the inertia of a heavy headshell / counterweight (not to talk of the stop&go motion of a linear tracking).
Anyway, to put together a rough version of these arms is quick and easy, and the funny thing is that they play like many others, and not the worst: which (like the Altmann Joke) gives a lot to think about the value of what someone claims and sells around
Alighiszem: thanks for the link. are there some drawinngs of that arm? i can't understand how it works
Carlo
P.S. glad to be in a so expensive company: there are so many clever minds in tonearms design (more than in potato-peelers) that there is place even for silly diyers.
Vertical movement
I tried to understand something of the "similar" tonearms with elastic vertical movement that were linked. (thanks again). Not having found any drawing I make some assumptions from the photos and little information found.
Let's begin with the $ 35k technology :
Vertical movement: the shaft seems suspended (WTL like) not a to a line but to a strip of “polymer-metal laminated films” (translation for all of us = mylar?) with a SME V – REGA like angled articulation - (thus a flexible joint, not elastic)
Horizontal movement: it looks like a normal ball bearing articulation, 23 mm offset.
Balance: luxury version of a Roksan “intelligent counterweight” (no fear Humankind, counterweights will take the Power not so soon)
Construction: hand carved platinum block, hopefully
let's move on, which is better. ERA 444, much more interesting:
Vertical movement: two pairs of leaf articulation, crossed (therefore a genuine elastic articulation!)
Horizontal movement: normal articulation on ball bearings, maybe
Balance: normal counterweight + small sliding weight on the U shaft for the VTF
Construction: folded aluminum sheet and u shaft, ideal for spurious resonances. Sounds great? who knows.
Therefore: New ideas around? Keen experimenters unemployed?
Slating welcome - Carlo
I tried to understand something of the "similar" tonearms with elastic vertical movement that were linked. (thanks again). Not having found any drawing I make some assumptions from the photos and little information found.
Let's begin with the $ 35k technology :
Vertical movement: the shaft seems suspended (WTL like) not a to a line but to a strip of “polymer-metal laminated films” (translation for all of us = mylar?) with a SME V – REGA like angled articulation - (thus a flexible joint, not elastic)
Horizontal movement: it looks like a normal ball bearing articulation, 23 mm offset.
Balance: luxury version of a Roksan “intelligent counterweight” (no fear Humankind, counterweights will take the Power not so soon)
Construction: hand carved platinum block, hopefully
let's move on, which is better. ERA 444, much more interesting:
Vertical movement: two pairs of leaf articulation, crossed (therefore a genuine elastic articulation!)
Horizontal movement: normal articulation on ball bearings, maybe
Balance: normal counterweight + small sliding weight on the U shaft for the VTF
Construction: folded aluminum sheet and u shaft, ideal for spurious resonances. Sounds great? who knows.
Therefore: New ideas around? Keen experimenters unemployed?
Slating welcome - Carlo
we are not alone
I've always believed that tonearms are one of the best playgrounds for wheel reinventors. So thanks to your suggestions I have surfed the net for flat and floppy tonearms, and quickly found illustrious ancestors:
EAT, CANTUS, NAD.
The Cantus and the Eat have only traditional articulations with a flat shaft, but the NAD 5120 is almost identical to my H arm: probably I knew it, and buried into my diy unconscious: so if this arm works, honor to Mr. Janda Jiri who invented, if not shame on me that have resurrected from the hifi garbage.
carlo
the flat Nad has an interesting damped counterweight. On the wrong side?
I've always believed that tonearms are one of the best playgrounds for wheel reinventors. So thanks to your suggestions I have surfed the net for flat and floppy tonearms, and quickly found illustrious ancestors:
EAT, CANTUS, NAD.
The Cantus and the Eat have only traditional articulations with a flat shaft, but the NAD 5120 is almost identical to my H arm: probably I knew it, and buried into my diy unconscious: so if this arm works, honor to Mr. Janda Jiri who invented, if not shame on me that have resurrected from the hifi garbage.
carlo
the flat Nad has an interesting damped counterweight. On the wrong side?
Attachments
- Status
- This old topic is closed. If you want to reopen this topic, contact a moderator using the "Report Post" button.
- Home
- Source & Line
- Analogue Source
- a continuation of DIY TT bearing...But now Tonearms!