Bracing doesn't have to be complicated at all. You can buy wooden dowels for quick and easy cross bracing. You don't even need power tools. Just a saw and a miter gauge to cut perfect right angles.
Also keep in mind that every time you add a brace, you're creating an anti-node which will either cancel out the even order or odd order harmonic vibration of a panel length. You are also taking away from internal volume, and pushing the resonant frequency higher.


Also keep in mind that every time you add a brace, you're creating an anti-node which will either cancel out the even order or odd order harmonic vibration of a panel length. You are also taking away from internal volume, and pushing the resonant frequency higher.
Last edited:
Working and sounding mighty fine!
Decided to defer the finish until a later time. Probably some nice veneer. The Baltic birch doesn't look half bad, but this was turning into the never ending project as is and Zia was harassing me.
BK
Nice work!
Also keep in mind that every time you add a brace, you're creating an anti-node which will either cancel out the even order or odd order harmonic vibration of a panel length. You are also taking away from internal volume, and pushing the resonant frequency higher.
That sounds complicated and I don't know that i understand the math and whether this will be beneficial or detrimental. i guess the advice is to not mess with it?
That sounds complicated and I don't know that i understand the math and whether this will be beneficial or detrimental. i guess the advice is to not mess with it?
Unfortunately it actually isn't that complicated- yet it is hard to measure and there is almost zero information out there on this. I only know of one website which has posted experiments on bracing/panel width/ and cabinet vibrations.
Basically there are three things you'll see businesses or hobbiests do. #1 is the most common. Just follow the status quo and construct cabinets out of 3/4" MDF or Plywood. Most hobbiests turn to Plywood after their first experience with MDF. Long story short MDF is a mess and the MDF dust is pretty terrible to inhale for your health. Then they add bracing if they feel like it.
The second group believes that the best enclosure is an infinitely rigid one. An enclosure that will not flex at all. You'll see normal 3/4"+ MDF/Ply with lots of bracing for people in this group OR exotic materials like granite. The theory is that if you make an enclosure rigid enough, cabinet vibrations will not be audible.
The third group of belief goes to people who think that an infinitely rigid enclosure is impractical or detrimental. The basis for this is that no enclosure no matter how rigid will still vibrate. People in this group go the other way and construct cabinets with relatively thin material that will vibrate, usually 1/2" Ply or MDF, then cover the interior of the cabinet with a damping material (a material that converts vibration into heat). This is completely different from sound absorption which converts sound in the air into heat, where as damping actually attenuates (decreases) the sound/vibration energy in the enclosure walls. The benefit of this route is that the sound energy that is radiated from enclosure walls is lower in frequency- where the ear is less sensitive. This is how Harbeth design's their enclosures.
The last unmentioned group says screw enclosures and all the problems acclimated with enclosure resonances
What I was talking about with nodes and anti nodes is as follows. If you take a length of material and affix it at both ends- such as a guitar string- it will vibrate if you excite it (picking it for a guitar string). It will vibrate at the fundamental frequency. The same goes for enclosure walls. Now if you take that guitar string and hold it down exactly half the distance of the entire string (or put bracing in a cabinet in the center of a panel) you now have the string playing a frequency at double the fundamental with zero of the odd order harmonics of the original fundamental frequency of the string. This is because you have created a node (the part where there is zero vibration) which is exactly where all the anti-nodes of odd harmonics of the fundamental would be. Although, now each side of the string could be seen as a seperate string with it's own fundamental and own group of harmonics. Add more bracing, and the more complicated it gets.
An externally hosted image should be here but it was not working when we last tested it.
In short, Audio reproduction- speakers, amps, etc. is an extremely complicated acoustic/electrical/mechanical/phychoacoustics engineering problem. I don't know of another product that has so many different types of engineering problems in a single product. That's why a perfect speaker has not been invented and probably never will. In engineering there is no best, just a balance of pros and cons. The Seas A26 kit is an incredible engineering feat which attains an on axis frequency response of +/- 2.5dB with a minimum of crossover parts.
If you did add bracing, I would recommend only adding bracing to where the point of bracing is the length of the panel divided by an even number. This is ofcourse my opinion, and is based purely on theory. In practice it might be no better or worse than randomly placed bracing.
Last edited:
Xaborus, an incredibly interesting post that I enjoyed. Thank goodness someone has got a grip on this.
I agree with you that all our efforts in search of the perfect loudspeaker are in vain.
Let me give you an example in Audio Genius Steen Duelund, well one of my heroes anyway. This guy worked out that a three-way is just a variation on a two way. A spectrum of mathematical solutions.
He also had an incredibly interesting view of the speaker box versus the room. You can just play with the relative sizes. You can equally apply cabinet damping to the inside of the box as the outside. Amazingly creative.
And then, we come to Quantum Mechanics and Dick Feynman, which IMO is a much harder problem than loudspeakers. But diffraction rules in both. But perhaps not the Quantum.
BTW, bk856er, LOVELY work:
Wish I could do stuff like that.
I agree with you that all our efforts in search of the perfect loudspeaker are in vain.
Let me give you an example in Audio Genius Steen Duelund, well one of my heroes anyway. This guy worked out that a three-way is just a variation on a two way. A spectrum of mathematical solutions.
He also had an incredibly interesting view of the speaker box versus the room. You can just play with the relative sizes. You can equally apply cabinet damping to the inside of the box as the outside. Amazingly creative.
And then, we come to Quantum Mechanics and Dick Feynman, which IMO is a much harder problem than loudspeakers. But diffraction rules in both. But perhaps not the Quantum.
BTW, bk856er, LOVELY work:
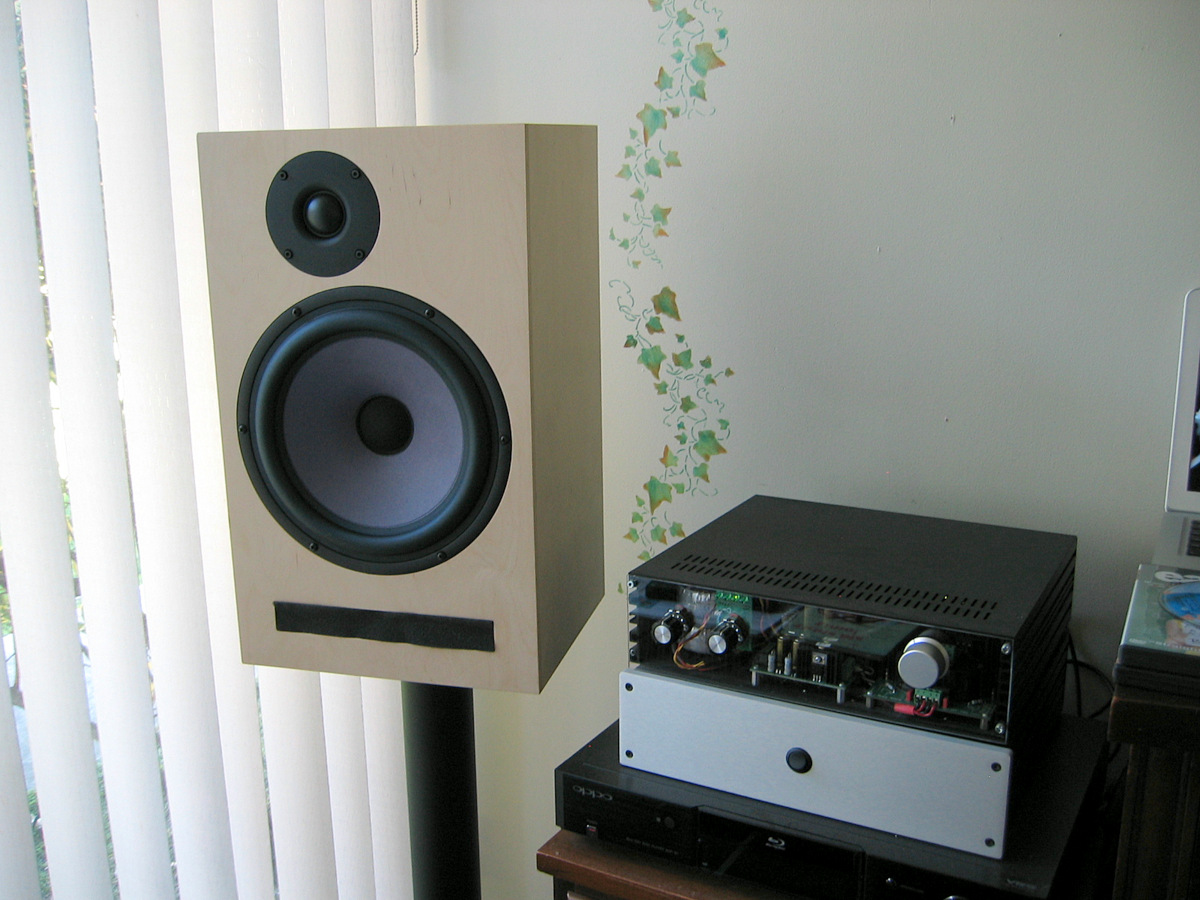
Wish I could do stuff like that.
Attachments
Thanks for the comments, guys! It's really gratifying to finish a project like this and have it exceed your (listening) expectations.
On bracing. I can't say if the A26 benefits or not, or if my implementation was optimal. This project was a tune-up for something more complicated, so I used it as an opportunity to learn my tools and develop my techniques. Perhaps someday I can audition my version with other versions. I can say that I'm super happy with the outcome. When I look back at the hours spent and the tools purchased, the Madisound cabinets are a real bargain!
On finish. Need to stare at these for some time before I make a decision to veneer or not. Need to learn their personality - like a newborn. There is something simple and elegant about the raw BB look (a la Troels masterpieces). I'd seal them now, but my preferred veneer attachment is heatlock glue, which works best on a porous surface. I brought the wood home in early October 2016, so I don't think it'll mind waiting a while longer. Besides, my workspace is now reconfigured for amp building!
BK
On bracing. I can't say if the A26 benefits or not, or if my implementation was optimal. This project was a tune-up for something more complicated, so I used it as an opportunity to learn my tools and develop my techniques. Perhaps someday I can audition my version with other versions. I can say that I'm super happy with the outcome. When I look back at the hours spent and the tools purchased, the Madisound cabinets are a real bargain!
On finish. Need to stare at these for some time before I make a decision to veneer or not. Need to learn their personality - like a newborn. There is something simple and elegant about the raw BB look (a la Troels masterpieces). I'd seal them now, but my preferred veneer attachment is heatlock glue, which works best on a porous surface. I brought the wood home in early October 2016, so I don't think it'll mind waiting a while longer. Besides, my workspace is now reconfigured for amp building!
BK
Thanks for the reply system7! I'll look into those interesting topics you discussed. 
Bk856er, my comments on bracing wasn't directed at you, so please take no offense
. Just some educational material for Stella blues. You're enclosures look fantastic! The attention to detail on the inside was bar-none! I also agree that BB ply is an absolutely wonderful wood to look at. My favorite ply by far.
If you decide to go the shellac route take a look into French polishing if you hate sanding like I do. It's a pretty long process but you're guaranteed a perfect mirror finish that you can be proud of.
Also, in case you're looking to color the wood but still want to check out the grain, check out "aniline" dyes (which to my understanding aren't really aniline these days). I know TransTint is a pretty popular example. It's what they use to dye curly and flame maple on guitars. I also believe it's how Devore Audio gets the "transparent black" on their O/96 Orangutang.
Bk856er, my comments on bracing wasn't directed at you, so please take no offense
If you decide to go the shellac route take a look into French polishing if you hate sanding like I do. It's a pretty long process but you're guaranteed a perfect mirror finish that you can be proud of.
Also, in case you're looking to color the wood but still want to check out the grain, check out "aniline" dyes (which to my understanding aren't really aniline these days). I know TransTint is a pretty popular example. It's what they use to dye curly and flame maple on guitars. I also believe it's how Devore Audio gets the "transparent black" on their O/96 Orangutang.
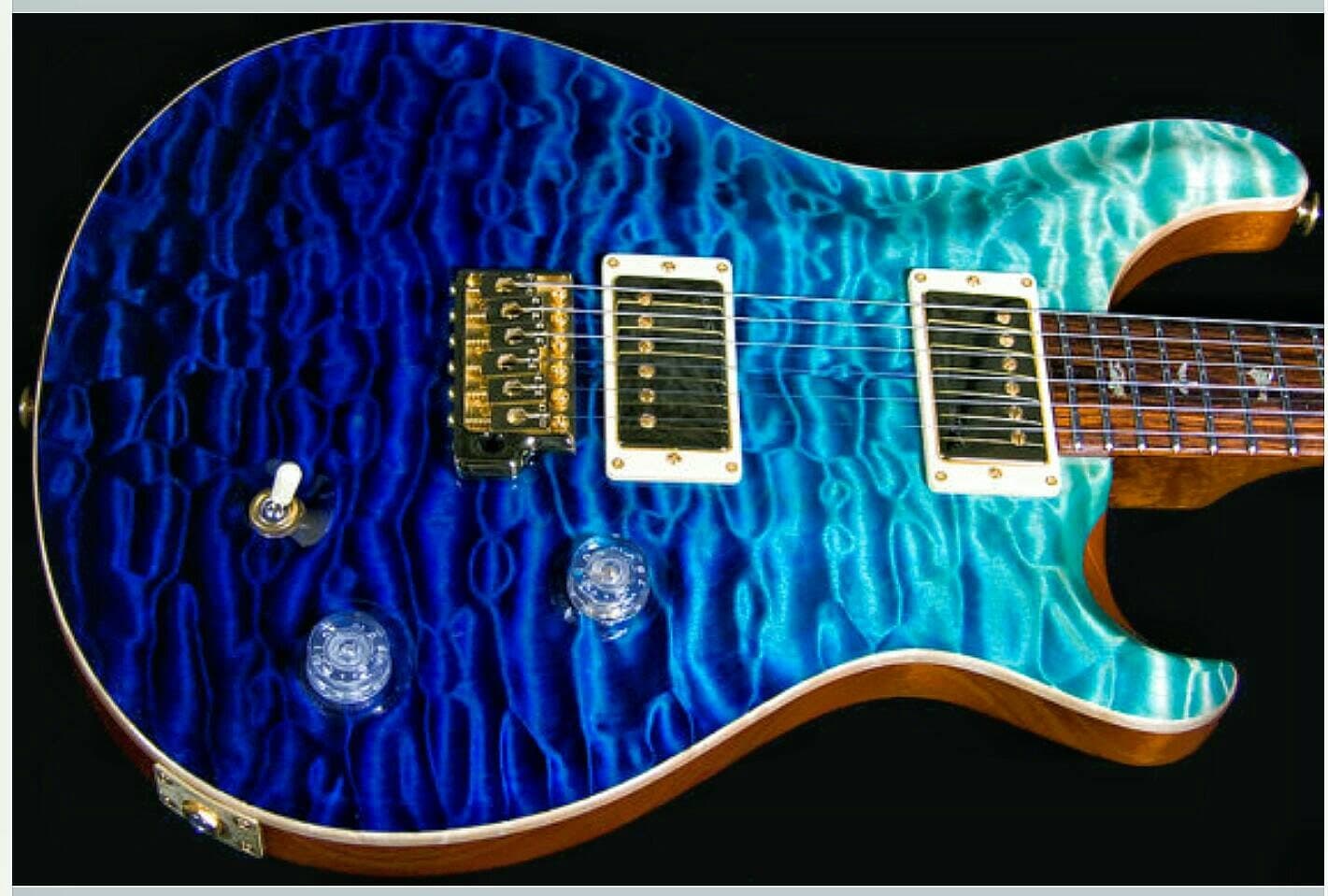
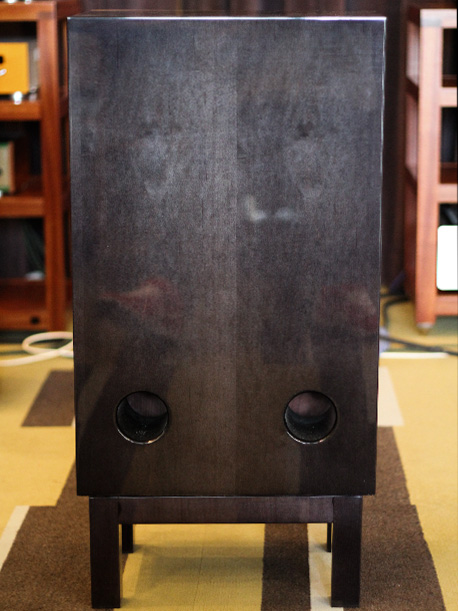
Last edited:
Xaborus not to worry - no offense taken and very happy to read your informative post. That's the beauty of diy - make it how you want and be in charge. Then make it again if you want to try it a different way. Get valuable input along the way from helpful folks who've been around the block a time or two.
Dig that transparent black look. So many options.
BK
Dig that transparent black look. So many options.
BK
Any weekend listening updates so far?![]()
Too early for meaningful impressions - still adapting and haven't cycled in other amps yet. There was definitely a change in the first 2 days and right now I would not call it warm at all. Think I will need to try the 12ohm resistor and stuffing quantity. Will say that I turned it up to 11 last night to show it off for some youngsters and it certainly does impress at high volumes!
BK
Too early for meaningful impressions - still adapting and haven't cycled in other amps yet. There was definitely a change in the first 2 days and right now I would not call it warm at all. Think I will need to try the 12ohm resistor and stuffing quantity. Will say that I turned it up to 11 last night to show it off for some youngsters and it certainly does impress at high volumes!
BK
Does this first impression mean its good but not great so far?
Does this first impression mean its good but not great so far?
I think they're beyond good and maybe even great. But I want to spend more time getting to know them with various configurations. Changed the amp tonight and I'm getting some new character. For sure, the mid/tweet is a star.
BK
Part of the reason the A26 design works with such a low Crossover and such a simple one is the use of a 1.5 inch tweeter. They have the right acoustic output where you need it. The only one I could suggest other than the Seas is the Audax TWO34 XO 1.3 dome.
I say don't mess with it. The simple elegance of the design is part of its appeal.
I say don't mess with it. The simple elegance of the design is part of its appeal.
Last edited:
How about an update on impressions?![]()
They keep getting better
Been using them daily since I hooked them up and the initial build euphoria has not worn off at all. Still need to connect up some key amps and torture test. The larger A26 is blocking vertical growth of my tower of diy electronics, so need to shuffle things around. One thing I find particularly impressive is the quality when the volume knob is twisted to the right - and this from a humble Wiener Pro. Super smooth and non-fatiguing.
More when I can, driven by Pass designed M2 clone and VFET, and hopefully also even an F6.
BK
- Home
- Loudspeakers
- Multi-Way
- SEAS A26 build