Hello sq225917,[...]
Silicon oil isn't a great lubricant- that's ok in my polymer bearing....
The one thing I really love about viscous drag is that it's self correcting. If the motor should increase its speed the increased drag holds it back. If the motor drops it's speed the reduced drag helps even it out. I think it might be the only free lunch in the whole of audio.....!
My deck comes to rest from 33 in about 5 revolutions.
self correcting: i would not describe it that way. The drag does not smoothen out sudden stylus drag change very much, almost not at all. The drive motor and the motor control has to do that, preferably without delay.
With carolus' miracle bearing the only thing helping with sudden transients is the platter inertia, but the drive motor has to do a lot. On not so fast stylus drag changes, the platter inertia does not help it all and the drive motor has to counteract 100% of the drag-induce deceleration.
With bearings like yours and mine, the bearing-drag-induced base load is around 80% and the stylus drag variation happens inside the remaining 20%. Much easier for the drive control to counteract that.
Hello carolus,
my compliments for your air bearing setup!
I have one question and one suggestion for you.
Question:
how satisfied are you with your air bearing TT's low end reproduction? Do you have the feeling that the bottom octave is fully present, sonically?
Suggestion:
get yourself a decent massive resonance-impeding plinth for that TT! You will like it.
Currently, you have a Rube-Goldberg mechanism as far as ringing and resonances are concerned (just my

Best regards,
Bernhard
Hello carolus,
my compliments for your air bearing setup!
I have one question and one suggestion for you.
Question:
how satisfied are you with your air bearing TT's low end reproduction? Do you have the feeling that the bottom octave is fully present, sonically?
Suggestion:
get yourself a decent massive resonance-impeding plinth for that TT! You will like it.
Currently, you have a Rube-Goldberg mechanism as far as ringing and resonances are concerned (just my)
Best regards,
Bernhard
Hi Bernard.
FYI;
About "feelings bottom octave": this means a subjectif opinion of the entire set-up (vinyl/groove/pick-up/headshell/arm/TT/Riaa-ampl/X-over/Ten-DC-amp/Horn EV-PatricianIV).
For the horn set-up, I "measure" a strong & present 20Hz (and below) full horn.
For the arm air bearing, I use my old Firato Hi-Fi test (2) from Jan Kool & "Analogue test LP". Band 2 = Cartridge/arm resonance below 7Hz, Band 3 card/arm vert. below 6 Hz ...
Thanks for your suggestion about the "massive resonance-impeding plinth".
To day I have no special need to go further in this project with heavier mass (in the living room).
I love my WAF=10/10. ... (no heavy mass struggle & divorce).
My initial goal was to push (in dynamic mass) 200 ... 300kg ... very easy in air bearing ...
And I like "Rube-Goldberg" ... but believe me, my air bearing concept is "music", I am in (Riaa) "paradise" ... no-chi-chi-ni-tra-la-la ....
Allez, salukes ... let's play music.
The best.
Karel
Sorry, out the thread:
@ SQ225917, Thanks for your support to (RIAA) "paradise" heaven ... I apprecieted.
Hi Bernard.
FYI;
About "feelings bottom octave": this means a subjectif opinion of the entire set-up (vinyl/groove/pick-up/headshell/arm/TT/Riaa-ampl/X-over/Ten-DC-amp/Horn EV-PatricianIV). [...]
Hello Karel,
granted, all hearing is subjective. However, i cannot hear thru my measuring equipment, I have to use my ears. But that's just me.
Let me repeat/re-phrase my question:
During listening to, say, a premium recording (recording engineer e.g. Kenneth Wilkinson, Robert Fine, Lewis Layton, Louis Chase, Christopher Parker just name a few) of a big orchestra in an even bigger hall:
do you perceive the bottom octave as crisp, well-defined? Are the walls of the concert hall (and the reverberation/echo) audible? Is the space between the instruments audible?
Or is the low-end reproduction tending to be frazzled, woolly, out-of-focus?
How does the low-end reproduction compare to a TT with conventional axial platter bearing (spherical face / trust plate)?
No corrosive intention here, but ...
Plinth design. Place a the sylus on a stationary platter. Measure to - 60 dB via RIAA preamp ( speakers on helps ). Start to think what you must do. It is that easy. You will be surprised what you see. People walking up the garden path ? A soundcard analyser should do the job. A good bearing of the simple type without the motor on probably is > - 80dB weighted ( running free, pushed to speed then let to run down ). LP's I seem to remember about - 57 dB. If you use suspension like a motorcar it needs to be good from the wow and flutter point of view. As far as I know to make it stiff in the horizontal and free in the vertical is the best you can do. Linn and Thorens TD150 were not so stupid in having the springs wrongly placed. All that corrected that fault run the risk of reaction to the sylus forces, dynamic wow was the term used.
all hearing is subjective .... measuring equipment ..... I have to use my ears.
question:
... big orchestra in an even bigger hall ...
... perceive the bottom octave ..... well-defined ....
....Is the space between the instruments audible?
....Or is the low-end reproduction tending to be frazzled, woolly, out-of-focus?
... How does the low-end reproduction compare to a TT with conventional axial platter bearing (spherical face / trust plate)?
...I want to know ....
Hi Bernard.
Sorry, we are again "out of topic/thread" (it's not my style).
In a nutshell some answers:
1) I agree (with you), after the right measurements (drivers/horns alignment, pinknoise ...) a next tuning step with "two good ears" (& more out-side ears) is opportune.
Some very-fine-tuning-steps are not seeing on the graph ... but with great musical audible result (musical scene, depth, instr. localisation, coherence ....)
A never ending tuning-story .... (but, easy in actif X-over) ...
2) About your "low-end" curiosity:
(perso) Believe me, musical heaven start with 18" (& more) driver in a horn concept .... (it's my experience/comparaison since '68).
The musical impression "low-end" is the sum of the fundamental low Fr with all his harmonics (1°/2°/3° .. etc) ..... & again, all drivers/horns (from very low to high) are in the running on the musical scène ....
Bernard, you now very well the advantages (& dis-) about a good-tuned-full-horn concept ...
It's quick, présence, plenty power, clear, subtile,no fatigue, in symbiose , mit swoeng (!), .... etc,etc ...
I préfère (& respect) the perso opinion/impression from the listener ....
3°) I compared my 16" air bearing TT (& TA) with (my) two EMT930 & high-level-modified-Lenco.
The inherent produced "floor noise" (amplified back ground noise from ball-bearing, axel & -hole mismatch) from an air bearing with multi-air-nozzels is significant lower (near zero) .....
Joke; You now the hype about Roger Waters his dog in "amused to death"!
With closed eyes @ open ears I can ear (on the right hand) his tooth-scratching & growl before barking.
(I know other subtile hype-jokes ...)
It's music out heaven's cloud .... Sint Cecilia like it ... (I presume).
Bernard, let's play music ....
The best.
Servus.
Karel
(next via PM)
Hello nigel pearson,
Plinth design: very good strategy, i did similar: i made a stand for and improvised tonearm with its gymbal mounted to that stand so that i could place the stylus tip anywhere on the plinth. Excellent to locate resonances in the plinth.
-57dB: depends how you look at it. Compared to common reference level (stylus velocity of 5cm/sec @ 1kHz), the noise floor is down to -45dB for a near-pristine vintage 1st pressing (i measured this on "Vienna1908-1914" Mercury SR90316-white promo,) and it is no further down than -47dB on a perfect unplayed 180gr-re-issue. BTW, loudest level is +17dB on the most dynamic recording i ever experienced. trombones running amuck on the Mercury recording cited above.
Make the suspension free-moving in both horizontal and vertical direction but position the suspension springs at the outer perimeter of the plinth, increasing the reaction torque against the suspension spring by this. Result is a much higher frequency for rotational oscillations than for vertical/piston-like oscillations which makes the sonically detrimental rotational oscillations subside very fast (1.0 to 1.5 oscillation periods) and remaining is the vertical/piston-like oscillation. Among many other suspension configuration i have tried out, this worked best.
Suspension springs.
Metal springs show a frequency-dependent stiffness; unfortunately they are stiffest in the center of our hearing range. Between 1 and 2 kHz the do not really decouple the plinth from the ground or from the suspension chassis. Rubber springs or bladders filled with air (e.g. bicycle tubes) don't do that, that is why i prefer them.
The premium solution is what the manufacturers of optical tables use: they have a container full of compressed air and a piston holding a rolling diaphragm inside a bore; the diaphragm is holding the air. This design is free-moving in both horizontal and vertical direction, but big amplitudes only are possible in vertical direction: see Newport Pneumatic Vibration Isolator.
Plinth design: very good strategy, i did similar: i made a stand for and improvised tonearm with its gymbal mounted to that stand so that i could place the stylus tip anywhere on the plinth. Excellent to locate resonances in the plinth.
-57dB: depends how you look at it. Compared to common reference level (stylus velocity of 5cm/sec @ 1kHz), the noise floor is down to -45dB for a near-pristine vintage 1st pressing (i measured this on "Vienna1908-1914" Mercury SR90316-white promo,) and it is no further down than -47dB on a perfect unplayed 180gr-re-issue. BTW, loudest level is +17dB on the most dynamic recording i ever experienced. trombones running amuck on the Mercury recording cited above.
There is such a thing as horizontal excitement on a TT; i would not consider it desirable to let pass horizontal excitation thru into the plinth, particuarly not at higher frequencies. May i suggest another strategy?[...] As far as I know to make it stiff in the horizontal and free in the vertical is the best you can do. [...]
Make the suspension free-moving in both horizontal and vertical direction but position the suspension springs at the outer perimeter of the plinth, increasing the reaction torque against the suspension spring by this. Result is a much higher frequency for rotational oscillations than for vertical/piston-like oscillations which makes the sonically detrimental rotational oscillations subside very fast (1.0 to 1.5 oscillation periods) and remaining is the vertical/piston-like oscillation. Among many other suspension configuration i have tried out, this worked best.
Suspension springs.
Metal springs show a frequency-dependent stiffness; unfortunately they are stiffest in the center of our hearing range. Between 1 and 2 kHz the do not really decouple the plinth from the ground or from the suspension chassis. Rubber springs or bladders filled with air (e.g. bicycle tubes) don't do that, that is why i prefer them.
The premium solution is what the manufacturers of optical tables use: they have a container full of compressed air and a piston holding a rolling diaphragm inside a bore; the diaphragm is holding the air. This design is free-moving in both horizontal and vertical direction, but big amplitudes only are possible in vertical direction: see Newport Pneumatic Vibration Isolator.
The measurements help greatly. They don't need to be highly accurate as long as consistant. Ideas can be tried against things heard. I use squash balls. They still work when nearly flat due to mass killing them.
My friend Kurt who designed the recent Thorens high end turntable made an interesting point. He was asked by another German turntable maker to use a ceramic ball on a requested design. This raised the resonance of the design to 6 kHz rather than 1.5 kHz if metal. As Kurt said not really better and new problems to solve. Kurt liked the idea of a broken glass bearing to solve that. Idea was idea and not fact.
My friend Kurt who designed the recent Thorens high end turntable made an interesting point. He was asked by another German turntable maker to use a ceramic ball on a requested design. This raised the resonance of the design to 6 kHz rather than 1.5 kHz if metal. As Kurt said not really better and new problems to solve. Kurt liked the idea of a broken glass bearing to solve that. Idea was idea and not fact.
Why do bearing and spindle have to be machined as one piece?
Instead of starting a new thread, I believe this is the appropriate place to ask a question that's been baffling me: why most turntables' bearing and spindle are machined as one piece? Other than the motor the noisiest part of a turntable is the bearing and its shaft is connected all the way up to the spindle that physically touches the record so why are they machined as one piece? The only designer that I am aware of who addresses this issue is Allen Perkins from Spiral Groove who machines the two components separately as described in a Stereophile interview: "he believes that his platter bearing is very different from those used in other turntables in that the spindle and platter bearing are decoupled yet precisely aligned."
I am not a machinist but I believe it can cause noise because I noticed in one turntable is noisier when I use a clamp and quieter without it.
That suggest the common practice of machining the bearing shaft and spindle as one piece is matter of economy and ease. Again, I'm not a machinist, any comment regarding this issue is greatly welcome.
In a YouTube video, I saw the Bergmann Magne turntable having similar design, check segment starting at 1:45.
Instead of starting a new thread, I believe this is the appropriate place to ask a question that's been baffling me: why most turntables' bearing and spindle are machined as one piece? Other than the motor the noisiest part of a turntable is the bearing and its shaft is connected all the way up to the spindle that physically touches the record so why are they machined as one piece? The only designer that I am aware of who addresses this issue is Allen Perkins from Spiral Groove who machines the two components separately as described in a Stereophile interview: "he believes that his platter bearing is very different from those used in other turntables in that the spindle and platter bearing are decoupled yet precisely aligned."
I am not a machinist but I believe it can cause noise because I noticed in one turntable is noisier when I use a clamp and quieter without it.
In a Stereophile review of another Allen Perkins designed turntable, the Immedia RPM2:
A discourse on method
The point at which the belt drives the platter is important, since Perkins' bearing design more or less (ahem) revolves around it. The RPM2 uses a short bearing with very tight tolerances. If you take the belt off and spin the platter, it doesn't turn freely—it rotates only a few times. The engineering term for this kind of bearing is "class-A drag"—which means, Perkins maintains, that the bearing is less influenced by changes in the motor speed or when the belt stretches. It's a planned application of friction, which, Perkins feels, smooths the rotation.
"People object that it makes the platter harder to turn, but I don't believe that a platter has to be easy to turn," he insists. "You just need a strong enough motor to turn it. If you have a torquey motor and a resistive platter, you get a more constant speed. People assume that a lack of friction means a lack of noise, but I've found that most noise comes through the spindle. The part of our spindle that touches the record isn't even part of the bearing, which makes machining quite difficult."
That suggest the common practice of machining the bearing shaft and spindle as one piece is matter of economy and ease. Again, I'm not a machinist, any comment regarding this issue is greatly welcome.
In a YouTube video, I saw the Bergmann Magne turntable having similar design, check segment starting at 1:45.
I totally agree.
Since the bearing is a crucial point in the noise department, you have to make sure
that a) you are using a very quiet one and b) try to eliminate or damp any reisidual noise from coming up the the record level.
A two piece platter design is a good idea...provided that the two pieces are machined as one and that you are able to keep the centers inline...
Actually the best idea is to have the two "hard" layers separated by a damping one.
Since the bearing is a crucial point in the noise department, you have to make sure
that a) you are using a very quiet one and b) try to eliminate or damp any reisidual noise from coming up the the record level.
A two piece platter design is a good idea...provided that the two pieces are machined as one and that you are able to keep the centers inline...
Actually the best idea is to have the two "hard" layers separated by a damping one.
Well said. Garrard used a flat bearing. It worked very well. The experimental type I have seen is very wide ( about 1 inch ). 1/10000" to being square. That was a 1954 requirement set out in engineering notes. The bearing reference material was glass ( to calibrate the surface measuring machine ). The standard 401 bearing was measured at Germany's Audio magazine at - 79 dB weighted. Most of that noise was the motor I designed. It was Garrard type with small improvements. It makes me smile when people says things. The measurements say all. I have seen many improved Garrard bearings for sale. It is easy to see the truth of that needs questioning. One wore a very big hole in the shaft in 6 months. 50 year old 301 bearings are as new. One I serviced at the old Telstar records in Slough had run all day for 24 hours non stop since 1964 when PYE records ( I guees switched off for holidays ). It was fine ( motor also ). The Garrard bearing like the Bumble bee obviously can't work. I thought so myself.
I don't get this... ?? Most tables have bearing spindle and platter as two or even more parts...??
I did not talk about platter, only mentioned bearing shaft and spindle. There are non-detachable platters built with the bearing and spindle as one piece, such as the Empire 208. But that's not the focus here. Basically anything that touches the thrust pad will generate noise and will be transmitted to the spindle that touches the record. Having the bearing shaft and spindle separated can,I believe, decouple the noise. Why do they have to be one piece other than ease of machining and economic reason? But what baffles me is that many ultra expensive turntables use the same method, too.
To illustrate my point, the Lenco bearing shaft (#4) is the same piece as the spindle that touches the record.
An externally hosted image should be here but it was not working when we last tested it.
Or a Rega bearing that uses a subplatter. The Thorens TD-160 and Linn LP12 have the same concept.
An externally hosted image should be here but it was not working when we last tested it.
In an inverted bearing, the thrust pad is closer to the spindle and record surface and possibly more noise.
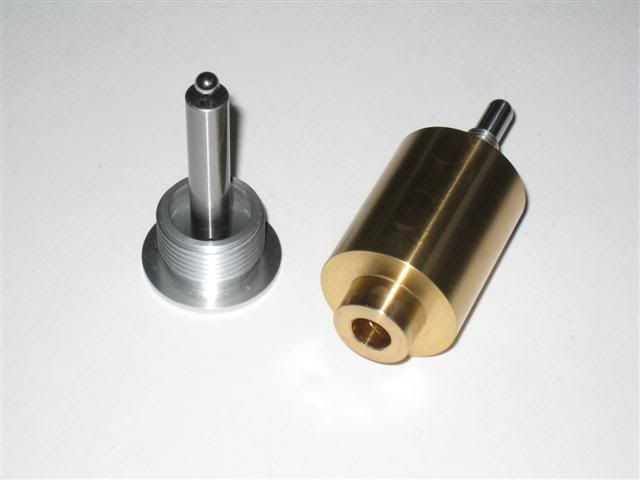
So in the end, why are we tied to the tyranny of bearing/spindle as one piece?
Last edited:
I guess the problem he has mentioned is dealing with the vinyl record having contact with anything that "beams up" (in contrat with "draining down") vibrations from the shaft/thrust plate area.
At least that is what I am thinking...
BTW AuroraB... i think it's Constantinople.
At least that is what I am thinking...
BTW AuroraB... i think it's Constantinople.
So in the end, why are we tied to the tyranny of bearing/spindle as one piece?
Why is it a tyranny?
jeff
Why is it a tyranny?
Tyranny is just an exaggerated word so don't take it too seriously and I should rephrase it: "So in the end, why are we tied to this convention of bearing/spindle as one piece?"
That approach is certainly the convention and most common. I think 95 turntables out of 100 are built that way whether that's direct-drive, idler-drive, or belt-drive. I understand that in budget tables but in those ultra high end tables they do the same thing except with thicker and shinier platter and other blink-blinks so where's the creativity?
I guess the problem he has mentioned is dealing with the vinyl record having contact with anything that "beams up" (in contrat with "draining down") vibrations from the shaft/thrust plate area.
At least that is what I am thinking...
When you put a record on the platter, the hole is slid over and touching the spindle. And the spindle is the same piece extend all the way down to the bearing tip or ball that's touching the thrust plate, the source of noise.
I don't know why it is hard to understand. Perhaps I don't explain things well. Sorry.
I understand that in budget tables but in those ultra high end tables they do the same thing except with thicker and shinier platter and other blink-blinks so where's the creativity?
Well, you certainly would have more options with a thick platter. I guess it depends on your design philosophy.
jeff
- Status
- This old topic is closed. If you want to reopen this topic, contact a moderator using the "Report Post" button.
- Home
- Source & Line
- Analogue Source
- DIY turntable spindle bearing tutorial