The bronze valve guide and valve is an easy simple way also. Those ream easily.
Charles Altmann used this method in his DIY TT:
The Altmann DIY Turntable
Forget about VCR heads, I'm pretty sure it uses a rolling bearing element of some sort. A plain bearing is what you want to use.
BillWojo
As I said previously, it has already been done and it works very well. Folks can go through all sorts of gyrations in trying to build something, You can go the hardest route you can imagine, which is most likely the most expensive, or you can go simple and clean.
To me trying to machine something like this is way off the radar since I don't have a metal lathe nor a milling machine (much less the knowledge of how to use them if I did), so alternate routes are somewhat necessary. Having something milled...and hopefully they will actually do it correctly...can be expensive for a one off part.
Instead of dismissing something out of hand, rip one apart and give it a try. It's not like you are investing hundreds of bucks in a part or something.
My 2 cents
Thanks guys for your replies!
Now with this thread I have more solution to try for my diy turntable, and I'm pretty happy!
But I have one question more.
How is generally the Altmann spindle system compared with high end turntable bearing system?
Is it "ok", "good", "perfect" or can be compared with really high end systems?
Thanks again
Now with this thread I have more solution to try for my diy turntable, and I'm pretty happy!
But I have one question more.
How is generally the Altmann spindle system compared with high end turntable bearing system?
Is it "ok", "good", "perfect" or can be compared with really high end systems?
Thanks again
Valves are made to be strong and light and are generally small in dia. If you are making a 15 + pound platter, consider that most high end spindles are using much bigger diameters to compensate.
Goldmund uses .750" on Their best TT,s
I guess you could use the longest valve you can get, and a well balanced platter if this is your only option
Regards
David
Goldmund uses .750" on Their best TT,s
I guess you could use the longest valve you can get, and a well balanced platter if this is your only option
Regards
David
It would be nice if somebody would make some skilled comments as to what tolerance is suitable for a spindle bearing. Too tight is not good either....
And BTW - the original Teres bearing was made in to doa's .75 and .8".....
The Teres assembly instructions lists the clearance as .0002-.0003", which is pretty tight, and explains why it took so long for their bearing and platter to seat all the way.
jeff
I just looked up the old Teres assembly manual, and rightly enough, it states 2-3 ten thousands of an inch,- a factor ten better than my previous post . My bad - and my bad recollection of the fact. In another discussion about Choir audio, the tolerance is said to be " in the single digit thousands", - of an inch that is...
Still - as european, I'm used to working in mm's - 2/10.000'' equals .5/100 mm, but lets say 1/1000'' is 2,5/100 mm....... 5 times more.....
Hence my question - how much is enough???
Still - as european, I'm used to working in mm's - 2/10.000'' equals .5/100 mm, but lets say 1/1000'' is 2,5/100 mm....... 5 times more.....
Hence my question - how much is enough???
Hence my question - how much is enough???
If you use the Teres as an example, a really close running fit is worth striving for. It's a big heavy platter, sitting on an 8" long spindle, so the forces involved are more extreme than say something like a Rega, that has a relatively light platter. So, it depends on what you're going to design. At the local hifi salon, they had a turntable with a 22kg platter, which was suspended by magnets. Didn't get a look at the bearing.
jeff
Maybe I should clarify my interest in this. Several years ago, I made a bearing after the original Teres plans. I also had some mail conversation with another of the original designers, who founded another co after the Teres split.
Other things came into my way, and the bearing has been in one of my office drawers since then. There is still some polishing to do, which I'm uncertain of how to do, since I have no access to a polishing machine. I do have abrasives papers down to .1 micron, though.... on measuring with fairly standard OD and ID micrometers, I can hardly measure any difference, which suggests I'm in the vicinity of 0.01mm. However, I can still feel a slight wiggle on the dry spindle.....
Ideas for polishing without anything but a lathe and a mill is appreciated..
Other things came into my way, and the bearing has been in one of my office drawers since then. There is still some polishing to do, which I'm uncertain of how to do, since I have no access to a polishing machine. I do have abrasives papers down to .1 micron, though.... on measuring with fairly standard OD and ID micrometers, I can hardly measure any difference, which suggests I'm in the vicinity of 0.01mm. However, I can still feel a slight wiggle on the dry spindle.....
Ideas for polishing without anything but a lathe and a mill is appreciated..
Last edited:
Ideas for polishing without anything but a lathe and a mill is appreciated..![]()
Try wet sanding your spindle in the lathe with some fine paper. Use a light oil with it. It's a bit messy, but works quite well. If you want a mirror finish, you'll have to find someone with a cotton buffing wheel, and some polishing compound.
jeff
That maybe so, but still there ought to be a possibillity of concensus among otherwise intelligent persons, instead of the increasing amount of jibberish and nonsense that keep filling this forum. We are talking of discrepancy factor of roughly the here......
General dia. tolerance is also often set a percentage of diameter....
General dia. tolerance is also often set a percentage of diameter....
Last edited:
General dia. tolerance is also often set a percentage of diameter....
You're not building and engine, and it's unlikely you're going to encounter a bigger spindle than 3/4". If you can't get any closer than .0005", I wouldn't loose any sleep over it.
Ok, coffee break is over, have to go finish cutting the lawn.
jeff
Last edited:
That is a nice thread as i am thinking about my making my own spindle bearing too!
I have made some decisions about what way to go.
I have used oilite bushings and can be tailored to a good spec so i guess they're in.
But not as a single piece...probably a three piece item with free space between them.
I will add spiral oil routes on the inside of the bushings.
As for the spindle itself i will try to use a tungsten carbide rod...ultra hard for life!
The idea of a parallel oil reservoir is great but i dissagree with the steel ball (i prefer ceramic) and i would add a damping layer under the PTFE thrust plate.
And of course since you are making it yourself why not adding magnetic repulsion?
If one is striving hard to get the lowest friction why not lowering the weight imprint on the ball and thrust plate to eliminate any drag?
If you know the final weight of your platter it's easy to find the right circular neo magnets to lift your platter to the point of mere feather weight...although i find a weight of 1-2 kilos better to drain the platter vibrations...
I have made some decisions about what way to go.
I have used oilite bushings and can be tailored to a good spec so i guess they're in.
But not as a single piece...probably a three piece item with free space between them.
I will add spiral oil routes on the inside of the bushings.
As for the spindle itself i will try to use a tungsten carbide rod...ultra hard for life!
The idea of a parallel oil reservoir is great but i dissagree with the steel ball (i prefer ceramic) and i would add a damping layer under the PTFE thrust plate.
And of course since you are making it yourself why not adding magnetic repulsion?
If one is striving hard to get the lowest friction why not lowering the weight imprint on the ball and thrust plate to eliminate any drag?
If you know the final weight of your platter it's easy to find the right circular neo magnets to lift your platter to the point of mere feather weight...although i find a weight of 1-2 kilos better to drain the platter vibrations...
I think it is a great idea to have a group bearing design that has freely available documentation so everyone doesn't have to start from scratch. I've looked at the old Teres threads but there isn't enough info (or drawing) to duplicate that design. Is a a Teres drawing available anywhere? I have reasonable machining skills and I think getting a final dimension within a half thousands is not horribly difficult. Does the shaft really need to be hardened? If the ball bearing is taking all of the axial load and the sleeve is only taking the lateral load I would think that it wouldn't need to be hardened.
I lifted this picture from the Wayback Machine, but I also have the original drawings tucked away on one of my backup disks. I also had some communication with another of the Teres designers, and some new ideas. I don't want to publish the original drawings without permission Based on this, there are two dim's for the spindle diameter, .75 and .8''. The length of the spindle section is appx 2.5''. The bearing sleeve brass, appx 4.5'' total length, with a wider section turned in the middle of the inner sleeve, effectively making it a two part sleeve or bushing. The top hat of the spindleis recessed into the platter appx flush with the platter top, and a disc spindle is threaded into the top, one smooth or one threaded for a screw on disc clamp. O chose .8'' for my still not quite finished version.....
Wayback link here : Teres Turntable
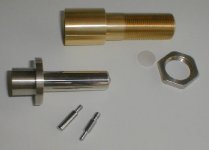
Wayback link here : Teres Turntable
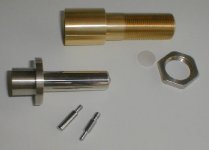
Last edited:
- Status
- This old topic is closed. If you want to reopen this topic, contact a moderator using the "Report Post" button.
- Home
- Source & Line
- Analogue Source
- DIY turntable spindle bearing tutorial