Thanks all for the comments and suggestions! Since this is my first non-tube amp build all info is appreciated.
My use of a fan is mainly to keep the interior of the chassis cool. By spacing out the center aluminum support between the upper and lower heatsinks and using that "slot" for the discharge is a bonus. I would imagine that half speed of the fan will be plenty. But this is an idea only in my head! So about time to experiment.
Dazed2 has roughly the same square area of heatsink as I do and is able to achieve about 150wpc. His sinks do have longer fins though. I'm hoping that by splitting my sinks and discharging the air between them, I can overcome the shorter fins and interior case cooling and reach close to the same output. The F5t has 32 devices mounted to the heatsink, each of my devices is mounted to its own 4.25" x 5" heatsink.
Am I in the ballpark with my plan?
My use of a fan is mainly to keep the interior of the chassis cool. By spacing out the center aluminum support between the upper and lower heatsinks and using that "slot" for the discharge is a bonus. I would imagine that half speed of the fan will be plenty. But this is an idea only in my head! So about time to experiment.
Dazed2 has roughly the same square area of heatsink as I do and is able to achieve about 150wpc. His sinks do have longer fins though. I'm hoping that by splitting my sinks and discharging the air between them, I can overcome the shorter fins and interior case cooling and reach close to the same output. The F5t has 32 devices mounted to the heatsink, each of my devices is mounted to its own 4.25" x 5" heatsink.
Am I in the ballpark with my plan?
The low noise fan is a good idea to keep the interior cool. especially in a build such as yours. IF you are intent on biasing it high.
However, take note, my build has almost nothing on the inside of the amp case. its pretty much empty. After a day and half of it being on, the heat sink temp is hotter than the inside of the amp case. (probably 10C hotter). In your build where everything is inside that amp, its going to get hot!
Has anyone ever measured if these fans output any electrical noise back into the power feed? Will it affect the work you do in smoothing out the DC in the PSU?
As far as the build I did, I'm able to bias all the way up to 162W with about 20C above ambient. (Yeah I went back and biased it even higher now
) I'm already biased up to 0.39V across the source R and I'm afraid to go any more, as per NP's article of thermal runaway at about 0.4V due to the diodes.
However I think I should be able to go more.... That graph for those diodes is not the best and I should be able to push close to 0.45V based on the temp of the heat sink
. But I'm only a FAB to a point 
However, take note, my build has almost nothing on the inside of the amp case. its pretty much empty. After a day and half of it being on, the heat sink temp is hotter than the inside of the amp case. (probably 10C hotter). In your build where everything is inside that amp, its going to get hot!
Has anyone ever measured if these fans output any electrical noise back into the power feed? Will it affect the work you do in smoothing out the DC in the PSU?
As far as the build I did, I'm able to bias all the way up to 162W with about 20C above ambient. (Yeah I went back and biased it even higher now
However I think I should be able to go more.... That graph for those diodes is not the best and I should be able to push close to 0.45V based on the temp of the heat sink
Last edited:
If possible, try to keep the leads as short as possible. in fact if you can swing it, I would recommend that you attach the mosfet leads directly to the board and not extend it at all and ionly if necessary extend the leads of the diodes.
That way the thermistor doesn't have to be extended.
That way the thermistor doesn't have to be extended.
Remember that the idea of cooling the inside compared to the outside is dependent on what needs cooling first.
Since you are coupling the outputs to the outside sinks, the transfer depends more on the outside fins than the inside.
Trying to cool just the plate and output pins inside, really doesn't,t amount to much compared to the outside.
Since you have decided to seperate the rows, you have increased spreading resistance of the sinks and at the same time the pressure created from the fan that will wrap around the small plate will cause the air to cancel itself and push straight out from the sides instead of going down and over the sinks.
A fan is a good idea, but I don,t think it will give the cooling you expect.
You can always turn the bias down to compensate
Looks like your to far along to change anything now, and if it's any help I might be wrong
Regards
David
Since you are coupling the outputs to the outside sinks, the transfer depends more on the outside fins than the inside.
Trying to cool just the plate and output pins inside, really doesn't,t amount to much compared to the outside.
Since you have decided to seperate the rows, you have increased spreading resistance of the sinks and at the same time the pressure created from the fan that will wrap around the small plate will cause the air to cancel itself and push straight out from the sides instead of going down and over the sinks.
A fan is a good idea, but I don,t think it will give the cooling you expect.
You can always turn the bias down to compensate
Looks like your to far along to change anything now, and if it's any help I might be wrong
Regards
David
Dazed2, dthanks for answering. Due to the 3/4" gap I have between the sinks the devices have to be extended. It's not much maybe 1 "- 1 1/2". But the thermistor needs to be touching, I guess I can rig up a clip.If possible, try to keep the leads as short as possible. in fact if you can swing it, I would recommend that you attach the mosfet leads directly to the board and not extend it at all and ionly if necessary extend the leads of the diodes.
That way the thermistor doesn't have to be extended.
On your previous post, you have run your amp for a day and a half! Must have been a good party😳
What are you using for a timer for your slow charge to bypass the thermistors? How long of a delay? I found this today, might make for an easy way to control the contactor.
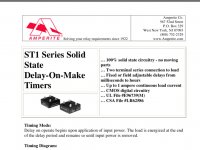
Remember that the idea of cooling the inside compared to the outside is dependent on what needs cooling first.
Since you are coupling the outputs to the outside sinks, the transfer depends more on the outside fins than the inside.
Trying to cool just the plate and output pins inside, really doesn't,t amount to much compared to the outside.
Since you have decided to seperate the rows, you have increased spreading resistance of the sinks and at the same time the pressure created from the fan that will wrap around the small plate will cause the air to cancel itself and push straight out from the sides instead of going down and over the sinks.
A fan is a good idea, but I don,t think it will give the cooling you expect.
You can always turn the bias down to compensate
Looks like your to far along to change anything now, and if it's any help I might be wrong
Regards
David
David,
Thanks for the advice.
Since the chassis will have no other openings and no way to naturally ventilate like a typical chassis with openings on top and bottom, I had to use a fan to cool the interior. That is the primary reason for the fan.
Since the air has to be discharged somewhere, and since my cosmetic reason required the splitting of the heatsinks, the space between was the logical place for the exhaust.
It shouldn't matter what direction the air discharges, as any air movement above the lower sink will create a vacuum and draw fresh air up through the sink.
I believe that it has been discussed that a 10" high sink is only about 25% or so more effiecent than a 5" high sink. By splitting my sinks and injecting any air should get get me a lot more efficentcy.
And of course, I could be wrong😊
this is back to front.10" high sink is only about 25% or so more effiecent than a 5" high sink.
the 10" heatsink is less efficient than the 5" heatsink.
The 10" uses double the resources but only achieves ~sqrt(10/5) more heat dissipation.
That makes it 30% LESS efficient.
True.
But no passive part makes a much difference as the proper adjustment of P3.
So how do you like to set P3?
this is back to front.
the 10" heatsink is less efficient than the 5" heatsink.
The 10" uses double the resources but only achieves ~sqrt(10/5) more heat dissipation.
That makes it 30% LESS efficient.
effective should have been the word. not efficient.
Thanks all for sharing, and great video 6l6.
BigE. We don't have any heating in any room😜 But the A/C will get a workout when the music is playing!
Finished stuffing the N and P boards last night
Starting on the FE boards tonight. My Toroidy transformers have shipped, but my Mundorf caps won't ship till the first week of November from PartsConnexion.
BigE. We don't have any heating in any room😜 But the A/C will get a workout when the music is playing!
Finished stuffing the N and P boards last night

Starting on the FE boards tonight. My Toroidy transformers have shipped, but my Mundorf caps won't ship till the first week of November from PartsConnexion.
THANKS for your opinion on the best sounding distortion. ( That did not come out right....)
Remember, that's what I think sounds best, you may not...
Try it with everything set for minimum distortion (the 2nd nulled out) It's worth a listen, at least for reference.
As Nelson and others say, I'm all for 2nd harmonic dominant, so when looking at the FFT from your QA400, at the 1W level, make sure the 2nd harmonic spike is taller than the third.
What are you using for a timer for your slow charge to bypass the thermistors? How long of a delay? I found this today, might make for an easy way to control the contactor.
View attachment 444475
I don't think those will work. it says a max continuous load of 1A.
From your rails biasing to 50W will already take you up to a 1A draw!
In my case I used a very simple RC timing circuit to control two relays to switch the thermistors out after about 18 secs.
Its crude, but it works.
However I would use something like what BigE designed. Its safer and disconnects the relays as soon as power is switched out.
http://www.diyaudio.com/forums/powe...it-design-other-psu-issues-4.html#post4029746 (post 39)
BTW. Just saw your secondary boards. What size resistors are you using for source resistors?
The heatsinks on the amp are at 49-50 degrees C, less than 30 deg rise, and the amp is pushing 88 watts RMS into 8 ohms. It is the only source of heat in my basement at the moment, not counting the water heater and lighting.
Class A is awesome!!!
![]()
![]()
PICS in the pics thread! or it aint true!
- Status
- This old topic is closed. If you want to reopen this topic, contact a moderator using the "Report Post" button.
- Home
- Amplifiers
- Pass Labs
- Aloha F5 v3 Monoblock build