For the last year or so I have been building a multi cell mid-bass horn, purchased two, used JBL 2446H drivers, along with putting together a measurement system. The horns are built, and have tested the JBL drivers
and have some data to post to inquire about interpreting some of the graphs. I have a fair driver knowledge, but lack the interpretation skills on the REW graphs
All the graphs are just the JBL driver alone, no horn. I used REW software, with a Mini DSP mic, the mic was positioned 2 inches away from the driver exit. Below are .jpeg graphs and data files
SPL + Phase
SPL + Phase.mdat
Impulse
Spectrograph
Waterfall
Impedance
Impedance.zma
Distortion
My concerns are the spectrograph and impulse graphs, along with the impedance graph with the large second spike at 1300 Hz, as this is in the mid-range being reproduced by .
Does the spectrograph look normal, or is that proof of a damaged diaphragm?
Does the Impulse file look normal, or does the graph show ringing ?
The Impedance rise at 1300Hz will need some suppression?
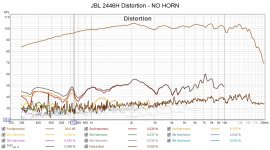
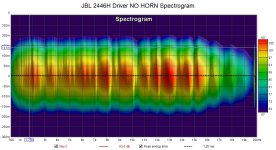
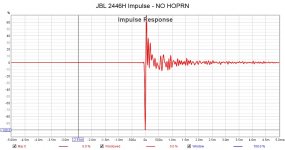
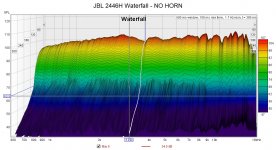
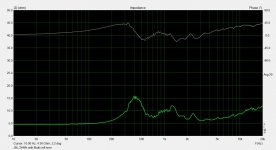
Mid-Bass horns built from this post:
Error 404 - Forum Page Missing cell-horn.html
Any help is appreciated,
Tom in Lafayette
and have some data to post to inquire about interpreting some of the graphs. I have a fair driver knowledge, but lack the interpretation skills on the REW graphs
All the graphs are just the JBL driver alone, no horn. I used REW software, with a Mini DSP mic, the mic was positioned 2 inches away from the driver exit. Below are .jpeg graphs and data files
SPL + Phase
SPL + Phase.mdat
Impulse
Spectrograph
Waterfall
Impedance
Impedance.zma
Distortion
My concerns are the spectrograph and impulse graphs, along with the impedance graph with the large second spike at 1300 Hz, as this is in the mid-range being reproduced by .
Does the spectrograph look normal, or is that proof of a damaged diaphragm?
Does the Impulse file look normal, or does the graph show ringing ?
The Impedance rise at 1300Hz will need some suppression?
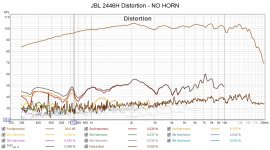
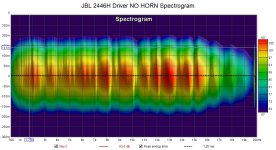
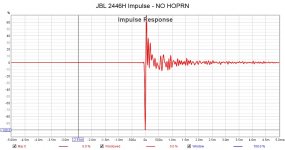
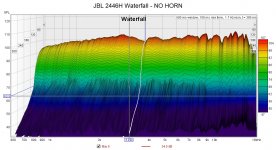
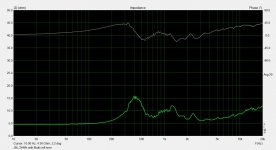
Mid-Bass horns built from this post:
Error 404 - Forum Page Missing cell-horn.html
Any help is appreciated,
Tom in Lafayette
Do both drivers measure the same?
They wont be exactly the same, but should be relatively close. Did you replace the diaphragms? If so, you might want to try to re-align them. There is a trick I read about somewhere, maybe here on DIYA, install the diaphragm, don't tighten down the screws all the way, leave them just a tiny bit loose. Play some ~500hz tones through it, very very low volume. The diaphragm will buzz a little, you can also go down to ~300hz or so, but do so carefully, and with very very very little power applied. Shift the diaphragm until the buzz goes away, and tighten down the screws.
I've done the above on my 288's, 2445's, and other compression drivers with good result. IME you wont always get rid of the buzz 100%, but typically you can eliminate most of it. This may help improve any aberrations in performance, if they're alignment related obviously.
I always check the bug screens on older drivers, sometimes they're dirty, sometimes they're really dirty. Clean them if so, carefully of course.
Obviously if you're not comfortable trying the above, don't take the risk in damaging your drivers.
Non magnetic screwdrivers can also help, in the very least it made me a bit more confident when working around the magnet and diaphragm.
Now, to the graphs you've posted, I don't see anything jumping out, though I'm not as experienced reading spectral graphs. The response, distortion and impedance look ok to me. You might spend some time looking through other threads of measured 2446's. They wont be exactly like yours of course, but should give you bit better reference.
They wont be exactly the same, but should be relatively close. Did you replace the diaphragms? If so, you might want to try to re-align them. There is a trick I read about somewhere, maybe here on DIYA, install the diaphragm, don't tighten down the screws all the way, leave them just a tiny bit loose. Play some ~500hz tones through it, very very low volume. The diaphragm will buzz a little, you can also go down to ~300hz or so, but do so carefully, and with very very very little power applied. Shift the diaphragm until the buzz goes away, and tighten down the screws.
I've done the above on my 288's, 2445's, and other compression drivers with good result. IME you wont always get rid of the buzz 100%, but typically you can eliminate most of it. This may help improve any aberrations in performance, if they're alignment related obviously.
I always check the bug screens on older drivers, sometimes they're dirty, sometimes they're really dirty. Clean them if so, carefully of course.
Obviously if you're not comfortable trying the above, don't take the risk in damaging your drivers.
Non magnetic screwdrivers can also help, in the very least it made me a bit more confident when working around the magnet and diaphragm.
Now, to the graphs you've posted, I don't see anything jumping out, though I'm not as experienced reading spectral graphs. The response, distortion and impedance look ok to me. You might spend some time looking through other threads of measured 2446's. They wont be exactly like yours of course, but should give you bit better reference.
Hello Pcgab,
Thanks for the contribution. I will give your realignment method a try. Absolutely will need a set of no-magnetic screw drivers.
After I took my original set of measurements, issues have settled out a little, due to you and others looking at the graphs and stating no major issues
I will only be using the 2446H/Horn from 500 - 4,000 Hz, so I am not worried about high frequency, at the moment.
Will report back on progress - hopefully
Tom in Lafayette
Thanks for the contribution. I will give your realignment method a try. Absolutely will need a set of no-magnetic screw drivers.
After I took my original set of measurements, issues have settled out a little, due to you and others looking at the graphs and stating no major issues
I will only be using the 2446H/Horn from 500 - 4,000 Hz, so I am not worried about high frequency, at the moment.
Will report back on progress - hopefully
Tom in Lafayette
Hello Pcgab,
Thanks for the contribution. I will give your realignment method a try. Absolutely will need a set of no-magnetic screw drivers.
After I took my original set of measurements, issues have settled out a little, due to you and others looking at the graphs and stating no major issues
I will only be using the 2446H/Horn from 500 - 4,000 Hz, so I am not worried about high frequency, at the moment.
Will report back on progress - hopefully
Tom in Lafayette
You're very welcome. I'm sure there are videos on youtube of the procedure, worth a bit of time to investigate, if nothing else, for the added bit of confidence.
I've used 2445's, and 2446's on many different mid-horns, typically from ~500-600 to as high as 5k or so. I tend to think that's the best range for those size drivers, especially with stock diaphragms. The beryllium diaphragms are a different story all together.
I went through this last year and I would like to find out more. Youtube had limited information, I think I spent some hours over a couple of days looking for procedures.
I agree that the impedance shows an effect similar to what Tom shows. Is the buzzing necessarily related to rubbing on the pole piece or also just the diaphragm not being centred?
I agree that the impedance shows an effect similar to what Tom shows. Is the buzzing necessarily related to rubbing on the pole piece or also just the diaphragm not being centred?
I went through this last year and I would like to find out more. Youtube had limited information, I think I spent some hours over a couple of days looking for procedures.
I agree that the impedance shows an effect similar to what Tom shows. Is the buzzing necessarily related to rubbing on the pole piece or also just the diaphragm not being centred?
That's a good question, I was told that it has to do with centering in the gap. I've certainly had some buzzing from rubbing as well.
Tom,Absolutely will need a set of no-magnetic screw drivers.
First things first, there is nothing that presently suggests your diaphragms need alignment, or are defective.
Non-magnetic screwdrivers won't hurt in the diaphragm installation procedure, but are not needed, the JBL diaphragm screws themselves should be stainless steel, which does not carry much magnetic attraction. The biggest potential for damage is the screw driver slipping off a screw and poking the diaphragm, which can happen with non-magnetic screw drivers as well. Use a finger to guide the driver outward, in case of slippage the driver will go harmlessly outside the screw ring.
Having aligned HF diaphragms for over four decades, I can say there is no particular frequency that is "good" to use, as often just one narrow frequency band, sometimes only a few Hz wide, may trigger the “buzz” distortion. For that reason, misalignment distortion may not be at all evident except with certain musical passages, making music, pink noise, or even specifically spaced sine wave tones near useless for alignment.
In most cases, low frequencies of several octaves below the usual pass band will make the harmonic distortion most audible. After determining a reasonable mid pass band output level, slowly sweep from 200 Hz up, listening for "buzz". Most times the range between 200 Hz to 800 Hz will reveal the "buzzing", but I have found a few diaphragms that only buzzed when driven at anywhere from 800 Hz to 5kHz or so.
The diaphragm alignment "procedure" is to first remove the driver from the horn, or stuff the horn with rags, or lay it mouth down on a rug or carpet. The horn, or even the long throats of "old school" drivers like Altec, JBL, or TAD makes the diaphragm output much louder, which masks the dragging voice coil distortion component. Next, remove the diaphragm, fully clean the magnetic gap with tape, check that the gap is symmetrical with a depth gauge which can be made from paper card stock, if not symmetrical it must be made so.
Then to align the diaphragm, re-install the diaphragm with it's screws just loose enough to not rattle, but tight enough to allow one to tap a portion of the screw ring in the direction that eliminates the buzz, then re-sweep to determine you have not caused a buzz at a different frequency, then tighten the screws fully, and test again. Lather, rinse, repeat ;^).
Even with many modern diaphragms supposedly "self aligning", they often ain't.
Art
Thank you for posting your insights Art, they are immensely helpful for those of us that don't have the expertise.
My experience has been it's a relatively easy procedure, take your time, heed Art's notes, and you'll be fine.
My experience has been it's a relatively easy procedure, take your time, heed Art's notes, and you'll be fine.
My experience is the "relatively easy procedure" of cleaning the gap may take between a few minutes or upwards of an hour, before any hope of success in the alignment process can even begin.My experience has been it's a relatively easy procedure, take your time, heed Art's notes, and you'll be fine.
An analog sweep generator definitely speeds the process compared to using stepped tone generators..
Weltersys,
Thanks you for the info. Can you provide a little more insight into your statement:
"Next, remove the diaphragm, fully clean the magnetic gap with tape, check that the gap is symmetrical with a depth gauge which can be made from paper card stock, if not symmetrical it must be made so."
I have not opened the drivers yet, so I am inexperienced at this specific procedure.
Once opened your direction should be clear, but for now a few questions:
I assume the use of tape is to clear out solid debris in the gap?
Can the gap be flushed out with contact cleaner?
If the gap is not depth symmetrical, How do I correct this issue ?
Please advise,
Tom in Lafayette
Thanks you for the info. Can you provide a little more insight into your statement:
"Next, remove the diaphragm, fully clean the magnetic gap with tape, check that the gap is symmetrical with a depth gauge which can be made from paper card stock, if not symmetrical it must be made so."
I have not opened the drivers yet, so I am inexperienced at this specific procedure.
Once opened your direction should be clear, but for now a few questions:
I assume the use of tape is to clear out solid debris in the gap?
Can the gap be flushed out with contact cleaner?
If the gap is not depth symmetrical, How do I correct this issue ?
Please advise,
Tom in Lafayette
Tom,1)"Next, remove the diaphragm, fully clean the magnetic gap with tape, check that the gap is symmetrical with a depth gauge which can be made from paper card stock, if not symmetrical it must be made so."
2)I assume the use of tape is to clear out solid debris in the gap?
3)Can the gap be flushed out with contact cleaner?
4)If the gap is not depth symmetrical, How do I correct this issue ?
I'll repeat: There is nothing that presently suggests your diaphragms need alignment, or are defective.
There is no reason to open up your drivers if you hear no buzzing when doing a slow sine sweep. Don't "fix it" if it ain't broke 😉
1) The gap can be checked for symmetry by folding over paper until it fits tightly in the gap, it will drag in tight spots if the top plate or pole piece has shifted. Until fairly clean, it is hard to tell if there is a "pinch".
2) Yes, the tape adhesive will grab magnetic particles and dust that have been attracted to the gap. If the gap is rusted, (rust expands from the surface, reducing the gap) fine sandpaper will be needed to remove the rust, which leaves even more ferrous material stuck in the gap.
3) Flushing the gap with contact cleaner won't remove magnetic particulate.
4) I brought up checking the gap width symmetry as no amount of "alignment" will fix that issue.
You probably can't fix a pinched gap without demagnitization, dissasembly of the motor, re-gluing, repositioning with shims, then remagnitization.
There is a possibility of shimming the gap, tapping the top plate back into alignment, then regluing it externally, but the success rate would be iffy, and the magnetic strength may be reduced even if the gap has been restored.
Art
- Home
- Loudspeakers
- Multi-Way
- JBL 2446H Measurement interp