I have found this thread very interesting. Last year I built some active three way sealed speakers with high quality drivers (scanspeak and SB), high quality active crossovers, and MC2 amps.
I am extremely pleased with the outcome, but am continually dismayed by the 'stethoscope test' on my cabinet walls.
They are made from 18mm MDF with substantial oak and MDF cross-bracing, and 8-12mm of bitumen/aluminum (silent coat) internal damping. Over the bitumen is a 2cm layer of high density wool felt, and finally they are densely stuffed with glass fibre.
I was hoping with a well braced, well damped, well stuffed enclosure I would be safe - but it appears resonance is hard to tame!
I have even tried external application of tiles with 'green glue' type damping adhesive, which didn't seem to achieve much. So I am left with two options:
1. Either start again with the cabinet. ( I would now probably try either 9mm ply with 12-18mm bitumen damping and minimal bracing, or a full complex CLD enclosure with chipboard/plywood.)
2. De-couple the drivers from the current cabinet.
Given the complexity of the first option and cost, I have decided to try decoupling the drivers first - particularly as this has been shown to have a massive effect on panel resonance if done properly.
To decouple the drivers I am using two techniques:
1: I am making new baffles from stabilised hardwood which will be epoxied onto the current MDF baffles - if I understand things correctly this should provide greater damping and stiffness through the use of the two different materials bonded with epoxy - ? form of CLD, as the new hardwood baffle will only be tied to the rest of the cabinet via the epoxy.
2. 3mm sorbothane gaskets for all the drivers (given results shown demonstrate that the mid and tweeter can excite just as much resonance as the woofer) which are held to the new baffle with thin countersunk head screws and rubber O-rings - to prevent the metal screw from touching the speaker frame.
I hope that with these two measures I should get a good degree of decoupling of the drivers from the cabinet.
I will report back on my success - hopefully with photos and measurements in the next few weeks!
I understand from my experience too. Sometimes what we "know" just ain't so.
A link to a paper concerning driver decoupling from Andrew Jones, Director of Engineering, TAD and designer of the TAD Reference 1. I believe he posts on this site as AndrewJ. They used EAR type E-610-1 isolation grommets in the study.
http://www.linkwitzlab.com/Driver Decoupling.doc
Bushmeister, do you know the modulus of elasticity and the damping factor of the bitumen damping material?
Is the bitumen layer stiff enough for optimum damping (modulus of elasticity)? For most effective extensional damping the damping material should be:
1) 1/2 to 1 times the thickness of the base panel, even greater thickness is more effective, (this you have done)
2) optimally, the modulus of elasticity of the damping material should be similar to the base panel (surprisingly), within +-50% is best, though 1/5th works
3) the damping factor of the damping material should be greater than 0.1, with 0.4 to 0.6 best, damping factor = 1/Q
4) the damping material should be firmly attacked to the base panel, no flexible adhesive here, you want the damping material to flex when the base panel vibrates
The isophthalic polyester resin (available at serious boat repair shops and FRP supply stores) mixed with bentonite (cat litter) is very effective. See the Qualia website.
Some informative application information on damping tile effectiveness, see the damping factor tables on the right hand side of the page"
http://www.pyroteknc.com/download/Decidamp Tile 182IP 310713.pdf
I only have REW measurements as per this thread:
http://www.diyaudio.com/forums/mult...r-anyone-spot-any-probs-before-i-start-7.html
I do have on access waterfall etc. But it all looks good. It is the stethoscope test that disappoints.
Is there any measurements I can take with rew and my umik that might assist?
Wow missed all your other posts! It is 4mm silent coat, which is one of the better butyl based car dampening products with an aluminium constrained layer.
http://www.diyaudio.com/forums/mult...r-anyone-spot-any-probs-before-i-start-7.html
I do have on access waterfall etc. But it all looks good. It is the stethoscope test that disappoints.
Is there any measurements I can take with rew and my umik that might assist?
Wow missed all your other posts! It is 4mm silent coat, which is one of the better butyl based car dampening products with an aluminium constrained layer.
Last edited:
Hey
What adhesive for CLD can be recommended considering a closed cabinet? -> So with no fumes or harmful chemical emitions like bitumen (for the suround, cone etc).
... Green Glue or other adhesive made for constrained layer damping ...
What adhesive for CLD can be recommended considering a closed cabinet? -> So with no fumes or harmful chemical emitions like bitumen (for the suround, cone etc).
Last edited:
I've already hinted you to this one: tesa® Powerbond INDOOR - Adhesive Tapes - tesa SE
Then you won't need a damping layer any more, just put them between two thin (6 mm) plates of MDF.
But if it is applicable in a closed cabinetI can't say.
Then you won't need a damping layer any more, just put them between two thin (6 mm) plates of MDF.
But if it is applicable in a closed cabinetI can't say.
Why not a simple stiff ply box, lined with this:
iKoustic Mute Board 4 | Wall Soundproofing | iKoustic
Would seem to tick all boxes in one?
iKoustic Mute Board 4 | Wall Soundproofing | iKoustic
Would seem to tick all boxes in one?
Why not a simple stiff ply box, lined with this:
iKoustic Mute Board 4 | Wall Soundproofing | iKoustic
Would seem to tick all boxes in one?
Here's a related thread, with input from Brian Ravnaas, co-developer of Green Glue.
Green Glue in my speaker?!?! - AVS | Home Theater Discussions And Reviews
A very interesting discussion. I have been following it from the beginning. Like a lot of people here I am on a similar journey.
Here is a link to a page describing one persons findings on the subject of resonance control using a double wall cabinet with CLD.
This quote from the article might be relevant here.
"The best overall choice for building cabinets is composite layer construction. The fundamental resonances are raised an average of 1-1.5 octaves and reduced by 10-15dB (based on my tests with an accelerometer), and the enclosures are *dead*, without any messy goop (that may be hazardous to driver adhesives) or roofing felt. The trick is the glue that constrains the two layers.
I recommend you try this for yourself, but I spent a month and about $30 trying various types of adhesives, and found an excellent, cheap, high-damping, aggressive adhesive that is readily available...acrylic latex caulk plus silicone. Specifically, DAP ALEX Plus. The latex caulks don't have enough bond strength to the wood, and the pure silicones have no damping whatsoever.
Rigid bonds, such as wood glue, are practically worthless in composite constructions, providing strength but no damping. Try it yourself.. .buy a tube of ALEX Plus and glue a I' square piece to another. Do the same with wood glue. Let them dry overnight, and then knock on them. The ALEX Plus is dead, but the wood glue still almost as resonant as the single thickness piece' (This is supported by accelerometer testing that I have done, and I may be able to have the data here for you to look at at some point.·..) I tried several other latex In' silicones from other manufacturers, but none of them had the right balance of adhesion, damping, curing time and viscosity (and a reasonable pH so that "acid evolution" won't destroy the bonds over a couple of years)."
Robert
Here is a link to a page describing one persons findings on the subject of resonance control using a double wall cabinet with CLD.
This quote from the article might be relevant here.
"The best overall choice for building cabinets is composite layer construction. The fundamental resonances are raised an average of 1-1.5 octaves and reduced by 10-15dB (based on my tests with an accelerometer), and the enclosures are *dead*, without any messy goop (that may be hazardous to driver adhesives) or roofing felt. The trick is the glue that constrains the two layers.
I recommend you try this for yourself, but I spent a month and about $30 trying various types of adhesives, and found an excellent, cheap, high-damping, aggressive adhesive that is readily available...acrylic latex caulk plus silicone. Specifically, DAP ALEX Plus. The latex caulks don't have enough bond strength to the wood, and the pure silicones have no damping whatsoever.
Rigid bonds, such as wood glue, are practically worthless in composite constructions, providing strength but no damping. Try it yourself.. .buy a tube of ALEX Plus and glue a I' square piece to another. Do the same with wood glue. Let them dry overnight, and then knock on them. The ALEX Plus is dead, but the wood glue still almost as resonant as the single thickness piece' (This is supported by accelerometer testing that I have done, and I may be able to have the data here for you to look at at some point.·..) I tried several other latex In' silicones from other manufacturers, but none of them had the right balance of adhesion, damping, curing time and viscosity (and a reasonable pH so that "acid evolution" won't destroy the bonds over a couple of years)."
Robert
Excellent links chaps. I love the idea of coating the inside of my current speaker with green glue then slapping wet plaster all over it...to produce a very high performance cld....
Would be achievable and I would only have to remove the current lining but no braces. More reading...
Would be achievable and I would only have to remove the current lining but no braces. More reading...
I only have REW measurements as per this thread:
http://www.diyaudio.com/forums/mult...r-anyone-spot-any-probs-before-i-start-7.html
I do have on access waterfall etc. But it all looks good. It is the stethoscope test that disappoints.
Is there any measurements I can take with rew and my umik that might assist?
Panels have several type waves. Main two are bending and longitudinal waves (there are several more). The bending waves create the most sound. With a stethoscope, I don't know which waves you hear. In other words how valid is the stethoscope test?
Accelerometer with waterfall plot or cumulative spectrum decay would be best.
It's not the perfect test, but you could try a close microphone test on the side or rear baffles with a large signal and the waterfall plot and experiment with the sample time. What is the test signal method: MLS, sweeping sine wave, other? Earlier in this thread, a link to testing with a sine wave generator while having wheat floor on the baffle to show vibration mode patterns at different frequencies. Or maybe water in a small glass on a baffle, playing sine waves.
From our own Linearray (you may want to translate to your language as you open):
http://www.dipol-audio.de/projekt-schwingungen-an-lautsprechergehaeusen.html
Last edited:
I only have REW measurements as per this thread:
http://www.diyaudio.com/forums/mult...r-anyone-spot-any-probs-before-i-start-7.html
It is 4mm silent coat, which is one of the better butyl based car dampening products with an aluminium constrained layer.
The damping products for building walls, loudspeaker enclosures, and automobile panels do not all work across the spectrum. Basically the 3 to 4mm thick damping products for automobile sheet metal (18 gauge/0.048"/1.21mm) is insufficient for loudspeaker panels of 3/4" MDF. If you are going the extensional damping route, it needs to be thicker and stiffer, 12mm or greater and stiffness close to MDF (modulus 0.45 Mpsi / 3.1 GPa). For constrained layer damping, keep the thin adhesive layer but that thin aluminum foil layer needs to be replaced with something much stiffer.
Before, when I "knew" what I was doing, I tried one of those water base slurry/paint damping layers myself. Put on numerous coats that built up to about 1/8", 3 to 4 mm. Material not too bad with a damping factor around 0.14 and somewhat stiff. Not too effective either, too thin for my 1" MDF panels, should have been 1/2" to 1" thick. Wrong damping product.
Last edited:
Excellent links chaps. I love the idea of coating the inside of my current speaker with green glue then slapping wet plaster all over it...to produce a very high performance cld....
Would be achievable and I would only have to remove the current lining but no braces. More reading...
Bushmeister, are you referring to your bass or midrange enclosure? Brian Ravnass was applying that construction to the midrange enclosure.
Robotc/Robert,
Thanks for the link and the reference to DAP ALEX Plus for a CLD adhesive.
Link to a construction of a loudspeaker with CLD:
http://www.diyaudio.com/forums/mult...e-aligned-constrained-layer-construction.html
Thanks for the link and the reference to DAP ALEX Plus for a CLD adhesive.
Link to a construction of a loudspeaker with CLD:
http://www.diyaudio.com/forums/mult...e-aligned-constrained-layer-construction.html
It's actually funny that some of you are now thinking about cutting out the cross-braces in a cabinet. 
http://www.diyaudio.com/forums/multi-way/223174-interesting-read-i-found-lossy-cabinet-designs-harbeth.html#post3234256
The simple and precise answer to building a good cabinet seems to be coming back to lightness, rigidity and damping. Low stored energy in other words.
How light? Well not tin-foil light obviously. You've got to match the mass of the driver and its forces to the mass of timber or granite in the box or whatever.
In an ideal world, we'd probably build egg-shaped ply boxes for free-standing speakers. Or build the baffles into the wall of our rooms for a less bafflestep approach.
But we are stuck with flat panels in the real world. I'd suspect some panel ratios like 1.618 or 1.414 might help to detune resonances. Where the ratios get more offkey, a brace might help. But probably of the same material as the rest of the cabinet.
http://www.diyaudio.com/forums/multi-way/223174-interesting-read-i-found-lossy-cabinet-designs-harbeth.html#post3234256
The simple and precise answer to building a good cabinet seems to be coming back to lightness, rigidity and damping. Low stored energy in other words.
How light? Well not tin-foil light obviously. You've got to match the mass of the driver and its forces to the mass of timber or granite in the box or whatever.
In an ideal world, we'd probably build egg-shaped ply boxes for free-standing speakers. Or build the baffles into the wall of our rooms for a less bafflestep approach.
But we are stuck with flat panels in the real world. I'd suspect some panel ratios like 1.618 or 1.414 might help to detune resonances. Where the ratios get more offkey, a brace might help. But probably of the same material as the rest of the cabinet.
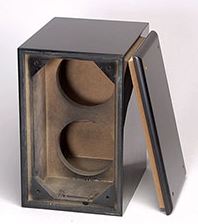
Again very interesting twinter. I will go away and see if I can get some empirical evidence regarding my stethoscope suspicions.
I guess I could clad the outside of the current boxes with some 9mm ply using a suitable adhesive. Or line the inside with pieces.
However in the link on green glue, the consensus seems to be again that the main drive for cabinet resonance is direct mechanical excitation, so decoupling the drivers should have the largest effect.
Also my silent coat layers may not be stiff enough, but they do add a high internal damping mass loading layer to the panels so should be beneficial even if not that effective extensionally.
I guess I could clad the outside of the current boxes with some 9mm ply using a suitable adhesive. Or line the inside with pieces.
However in the link on green glue, the consensus seems to be again that the main drive for cabinet resonance is direct mechanical excitation, so decoupling the drivers should have the largest effect.
Also my silent coat layers may not be stiff enough, but they do add a high internal damping mass loading layer to the panels so should be beneficial even if not that effective extensionally.
Morning
i don't know if that was the consensus:
Please excuse my english.
Regards
i don't know if that was the consensus:
But afaiu decoupeling the mid or bass driver works against the whole concept of how most drivers work. To move the membran the motor of the driver has to "push against something" or "hold on to smt". When decoupled part of the energy / force the motor "generates" is lost (whole driver "swinging back+forth") and i would guess the driver is also less "exact"....
However in the link on green glue, the consensus seems to be again that the main drive for cabinet resonance is direct mechanical excitation, so decoupling the drivers should have the largest effect. ...
Please excuse my english.
Regards
Morning i don't know if that was the censensus:
But afaiu decoupeling the mid or bass driver works against the whole concept of how most drivers work. To move the membran the motor of the driver has to "push against something" or "hold on to smt". When decoupled part of the energy / force the motor "generates" is lost (whole driver "swinging back+forth") and i would guess the driver is also less "exact".
Please excuse my english.
Regards
Hi and just to say that i agree completely.
If some of the energy from the driver is dissipated in the decoupling/cabinet that will not be transmitted to the room. It will be just wasted.
The cabinte and the mounting must be as stiff as possible.
Possible resonances must be addressed and dealt with in some other ways.
I am sure that these stiff speakers like Magico and Audio Machina they all sound louder in the room, with huge dynamic ... like an explosion of sound in the room.
All the energy from the driver is transmitted to the listening room ... and not absorded by a decoupling mounting or a lossy cabinet.
The tweeterinstead i agree it could be beneficially decoupled from the speaker baffle ... that is more reasonable.
Look here for instance ...
https://www.youtube.com/watch?v=LeRO_piB4lU
https://www.youtube.com/watch?v=IcPrJy-ihtQ
we can discuss instead about the actual drivers used ... i think there could be something better around.
Thanks and regards, gino
Last edited:
Please read links already provided in this thread with multiple measurements of drivers 'hanging free', rigidly mounted to cabinets, and de-coupled using rubber gromits = no significant difference in SPL output.
Also note comments from other members regarding laws of motion and the weight of membrane versus weight of the driver (on its own) and how the loss of energy (SPL) can be calculated to be insignificant.
There is no loss of dynamics or sound output by having a driving completely unmounted. In fact it improves resonances and ringing etc.
Please point me in the direction of any conflicting data to the already well documented stuff in this thread.
Also note highly engineered speakers such as the B&W nautilus - which you praised earlier uses decoupled drivers...
Also note comments from other members regarding laws of motion and the weight of membrane versus weight of the driver (on its own) and how the loss of energy (SPL) can be calculated to be insignificant.
There is no loss of dynamics or sound output by having a driving completely unmounted. In fact it improves resonances and ringing etc.
Please point me in the direction of any conflicting data to the already well documented stuff in this thread.
Also note highly engineered speakers such as the B&W nautilus - which you praised earlier uses decoupled drivers...
Please read links already provided in this thread with multiple measurements of drivers 'hanging free', rigidly mounted to cabinets, and de-coupled using rubber gromits = no significant difference in SPL output.Also note comments from other members regarding laws of motion and the weight of membrane versus weight of the driver (on its own) and how the loss of energy (SPL) can be calculated to be insignificant.There is no loss of dynamics or sound output by having a driving completely unmounted. In fact it improves resonances and ringing etc.
Please point me in the direction of any conflicting data to the already well documented stuff in this thread.
Also note highly engineered speakers such as the B&W nautilus - which you praised earlier uses decoupled drivers...
Hi and sorry i admit i am hard to understand ...
so speaking of B&W Matrix concept you mean that the bracing is there only to fight the panel vibrations caused by the woofer back emission ?
If it is like that i understand now ... no more question
And i know what to do.
Brace the panels and decouple the woofer from the front baffle ... quite easy to do.
Thanks again, gino
Last edited:
- Status
- This old topic is closed. If you want to reopen this topic, contact a moderator using the "Report Post" button.
- Home
- Loudspeakers
- Multi-Way
- how to brace a speaker cabinet?