To all accomplished woodworkers
I haven't started my speaker build yet, but have tried build some shop cabinets as a practice run.
I've had a hard time in getting the cabinet square. I've used dowel joints.
I'm thinking of using a rabbet or half lap joint instead with my router.
Is this method more likely to give better results?
Thanks
I haven't started my speaker build yet, but have tried build some shop cabinets as a practice run.
I've had a hard time in getting the cabinet square. I've used dowel joints.
I'm thinking of using a rabbet or half lap joint instead with my router.
Is this method more likely to give better results?
Thanks
I would make a jig. There are only two things you need.
First you need an accurate way to measure. Not a big deal a tape measure is easy to obtain. Be sure not to bend the sliding tip. Next you can make a square corner jig.
This is just a board the has two pieces of wood on one edge. One piece should be as close as you can make it to 12" and the other 16". Have the edges just touch at the inside edge. The open edges should be exactly 20" apart. This is a 3, 4, 5 triangle which gives you a 90 degree angle.
Screw or nail and glue the pieces in place. Once dried use your router to open the inner corner.
Now you can use this corner to make 3 dimension corner box edges. These can be used to clamp your boxes to square.
Of course you should line these reference corners with wood pads so the edges are also open. That way you can route oversize dadoes and then sand the boxes to perfect corners.
Once you have your corner sets you should wax the corner board and corner pieces to keep glue from sticking.
Obviously to test for square you measure the diagonals to be sure they match.
Now to clamp things you use wedges. Just use a scrap with parallel faces cut on a diaganol.
The other thing you might want to get is a piece of ground steel 36" long by 2" wide and a 1/4" thick. This will be not only a real straight edge but also a method to check your tape measure edge hasn't bent.
Now if you get a compass and plum bob you can layout almost anything.
First you need an accurate way to measure. Not a big deal a tape measure is easy to obtain. Be sure not to bend the sliding tip. Next you can make a square corner jig.
This is just a board the has two pieces of wood on one edge. One piece should be as close as you can make it to 12" and the other 16". Have the edges just touch at the inside edge. The open edges should be exactly 20" apart. This is a 3, 4, 5 triangle which gives you a 90 degree angle.
Screw or nail and glue the pieces in place. Once dried use your router to open the inner corner.
Now you can use this corner to make 3 dimension corner box edges. These can be used to clamp your boxes to square.
Of course you should line these reference corners with wood pads so the edges are also open. That way you can route oversize dadoes and then sand the boxes to perfect corners.
Once you have your corner sets you should wax the corner board and corner pieces to keep glue from sticking.
Obviously to test for square you measure the diagonals to be sure they match.
Now to clamp things you use wedges. Just use a scrap with parallel faces cut on a diaganol.
The other thing you might want to get is a piece of ground steel 36" long by 2" wide and a 1/4" thick. This will be not only a real straight edge but also a method to check your tape measure edge hasn't bent.
Now if you get a compass and plum bob you can layout almost anything.
Last edited:
Installing internal braces helps to make it square.
You must just decide in which order panels are attached. I don't remember every case but at least once I left other side panel last. It also depends on how corners are done, I make them straight and overlapping a little.
Screws prevents sliding when bands and clamps are tightened. I unscrew them later on and fill holes.
You must just decide in which order panels are attached. I don't remember every case but at least once I left other side panel last. It also depends on how corners are done, I make them straight and overlapping a little.
Screws prevents sliding when bands and clamps are tightened. I unscrew them later on and fill holes.
go to a builders merchant and buy a cheap framing/roofers square eg- ( Fisher - Steel Framing Square 16" x 24": Amazon.co.uk: DIY & Tools ), use your new square and some scrap ply to check that your 45' mitre cut is set correct on your track saw, then when your sure the saw is set exactly correct cut all of your panels in one go. even if your not not quite 45' the glue and some filler will no doubt hide your inaccuracies. 
I've used a picture framing clamp for ages and done over 50 sets of speakers with it. If it's a little out just a tap in the right place to correct.
This was used mainly with butt joints but have done a few mitred as well with the assistance of masking tape.
The assembly is only as good as the square cuts and I use a home made saw table. A good quality square is a must and also measure across the diagonal corners. If they are both the same, then it's square. A good flat work surface is also a must.
This was used mainly with butt joints but have done a few mitred as well with the assistance of masking tape.
The assembly is only as good as the square cuts and I use a home made saw table. A good quality square is a must and also measure across the diagonal corners. If they are both the same, then it's square. A good flat work surface is also a must.
Attachments
Last edited:
One thing you might look into is something called a "miter lock" bit. They're big and require a beefy router to run (I wouldn't dare use a handheld- use a router table), but they work great. I just wish I could find a miter-lock cutter for the shaper. They're really helpful for tricky cabinets, and they're great for drawers where dovetails aren't necessary. They lock together, which makes the hardest part (glue-up) much less tricky. I'm surprised that more people don't use them for speaker cabinets.
If you want to be really crazy, you could do dovetails. Probably more work than it's worth for a speaker cabinet though, and most people don't have the setup to do them.
Another great solution is a finger joint. You can cut these by hand with a good dovetail saw (it takes some skill, but the results are quite nice), but very few people cut them by hand these days. It's a fairly simple setup on a tablesaw (you do generally need a dado blade for this), and the results are quite good. Just a warning, small finger joints over long distances are extremely difficult and your setup needs to be almost perfect.
If you want to be really crazy, you could do dovetails. Probably more work than it's worth for a speaker cabinet though, and most people don't have the setup to do them.
Another great solution is a finger joint. You can cut these by hand with a good dovetail saw (it takes some skill, but the results are quite nice), but very few people cut them by hand these days. It's a fairly simple setup on a tablesaw (you do generally need a dado blade for this), and the results are quite good. Just a warning, small finger joints over long distances are extremely difficult and your setup needs to be almost perfect.
I just use a few oldskool carpenter squares and clamps and measure twise before i lock everything tight. IT seems to wok very well for me, even with my limited carpenter skills.
But the cutting is mostly done on a cnc machine of a carpenter i know by him, just like i solder his crossovers (as he can't solder). He helps me with the woodwork, i help him with the electronics...
But the cutting is mostly done on a cnc machine of a carpenter i know by him, just like i solder his crossovers (as he can't solder). He helps me with the woodwork, i help him with the electronics...
it can be done with basic tools
i made this a few months ago. i decided on a "tetrahedron" shape so that it would fit into the corner of my living room, and so that internally no panel was parallel to the waves exiting the back of the speaker. i used 1" structural ply, screwed and glued. it has 2 15" rockford subs wired in series.
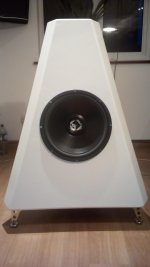
i made this a few months ago. i decided on a "tetrahedron" shape so that it would fit into the corner of my living room, and so that internally no panel was parallel to the waves exiting the back of the speaker. i used 1" structural ply, screwed and glued. it has 2 15" rockford subs wired in series.
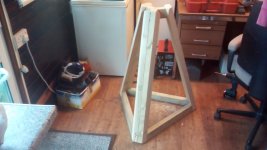
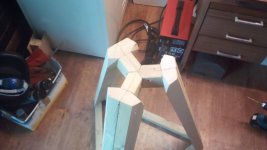
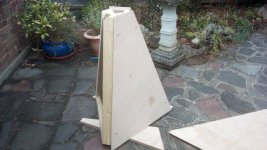

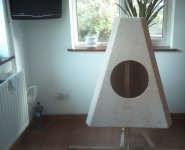
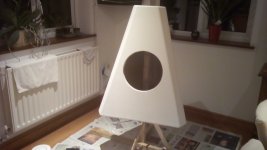
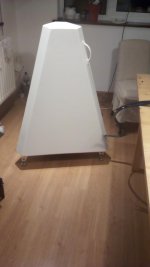
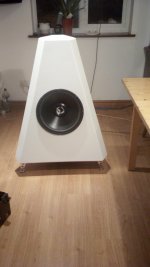
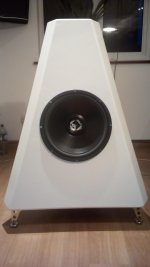
- Status
- This old topic is closed. If you want to reopen this topic, contact a moderator using the "Report Post" button.
- Home
- Design & Build
- Construction Tips
- What are some of the best methods for getting loudspeaker box square