I know, I know, probably a dumb question. But.
LPs are overwhelmingly played with a 9" pivoted arm, why not cut them using the same geometry? If nothing else it would make playback alignment much simpler and accurate.
LPs are overwhelmingly played with a 9" pivoted arm, why not cut them using the same geometry? If nothing else it would make playback alignment much simpler and accurate.
Mechanical reasons.I know, I know, probably a dumb question. But.
LPs are overwhelmingly played with a 9" pivoted arm, why not cut them using the same geometry? If nothing else it would make playback alignment much simpler and accurate.
"Cutting" means you are moving a heavy powerful cutting head, you must move it with precision over a blank disk, where there are no "position references", meaning you must place it wherever needed, and toboot it´sliterally cutting surface material away against resistance.
So for precision, rigidity and mechanical resistance, let alone weight handling, that is the best structure.
In Engineering we call it "puente grúa", literally "bridge-crane", not sure about the English word but that gives you an idea.
Back in the day I learnt to design them, although never actually built one.
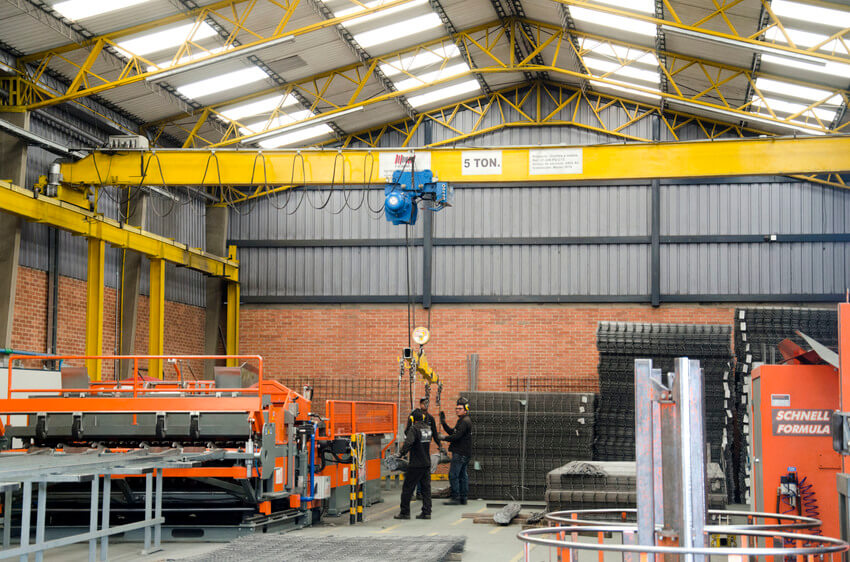
"Playing back" is the opposite: you want the lightest possible head, and it is "passive", it will go wherever the light needle pressure carries it, so the pivoted tangential arm is best.
Just think about how could a puente-grúa type cartridge head track the unpredictable record groove, real time and without adding its own position bias and flexing.
Up to the horror story of bending or tearing needle away.
There are such "arms" of course, but they need precise and swift servos to work ,,, easier said than done.
While I mainly have quite a few turntables/record changers around the house that all use the traditional pivoted tonearms, my main "serious" system has a linear-tracking direct-drive Kenwood.
As JM|Fahey pointed out, it is the way that records are "cut", and to play them back in the same way naturally results in the closest extraction of what's in those grooves.
Not to say that a good pivoted arm is inferior, they can provide satisfactory playback if set up right.
As for my Kenwood, it may be a small, almost invisible improvement in playback quality, but the unheard benefits are worth it.
No need for antiskating compensation...
Equal stylus contact on both groove walls...
Lack of any un-tangental phase differences...
Even some records that tend to skip on a pivoted arm machine do not on the Kenwood.
Unless of course, there's a major scratch or defect.
And the shortness of the linear arm changes the arguments about mass, and results in a faster-responding design when dealing with warped records.
I've got a flea market Beach Boys album with a 3/8" - 10MM quick warp that plays beautifully only on the kenwood.
As JM|Fahey pointed out, it is the way that records are "cut", and to play them back in the same way naturally results in the closest extraction of what's in those grooves.
Not to say that a good pivoted arm is inferior, they can provide satisfactory playback if set up right.
As for my Kenwood, it may be a small, almost invisible improvement in playback quality, but the unheard benefits are worth it.
No need for antiskating compensation...
Equal stylus contact on both groove walls...
Lack of any un-tangental phase differences...
Even some records that tend to skip on a pivoted arm machine do not on the Kenwood.
Unless of course, there's a major scratch or defect.
And the shortness of the linear arm changes the arguments about mass, and results in a faster-responding design when dealing with warped records.
I've got a flea market Beach Boys album with a 3/8" - 10MM quick warp that plays beautifully only on the kenwood.
Perhaps it's a question of the appropriate technology being available at the outset. Materials have improved and computer controlled servos are precise. PC hard disks/CNC machines wouldn't work without them. It's one of those situations where there's never been the impetus (read money) to try something different because vinyl is 'good enough' as it is.
I remember reading somewhere that the reason oil barrels have such an odd volume is that originally there were no barrels for oil so someone used barrels that'd been used for storing salted fish. Dunno if that's really true or not. IIRC the reason railway gauges are what they are is because it matched the wheel spacing of the horse drawn carts of the time...
I remember reading somewhere that the reason oil barrels have such an odd volume is that originally there were no barrels for oil so someone used barrels that'd been used for storing salted fish. Dunno if that's really true or not. IIRC the reason railway gauges are what they are is because it matched the wheel spacing of the horse drawn carts of the time...
Just curious: how does the cartridge follow spiral track?While I mainly have quite a few turntables/record changers around the house that all use the traditional pivoted tonearms, my main "serious" system has a linear-tracking direct-drive Kenwood.
.....
As for my Kenwood, it may be a small, almost invisible improvement in playback quality, but the unheard benefits are worth it.
No need for antiskating compensation...
Equal stylus contact on both groove walls...
Lack of any un-tangental phase differences...
Do they use some kind of sensitive servo or it´s "passive", relying on feather light roller bearings?
Of course, they have no physical groove to follow, it´s all preprogrammed coordinates there, or else.computer controlled servos are precise. PC hard disks/CNC machines wouldn't work without them.
In my Kenwood, it's basically a simple system, largely trouble-free.Just curious: how does the cartridge follow spiral track?
Do they use some kind of sensitive servo or it´s "passive", relying on feather light roller bearings?
The lateral angle (horizontal movment) of the tonearm moves a tiny flag that interrupts an LED light that is directed on a photocell.
The less light that the photocell is exposed to, the more voltage is sent to the servo IC and traverse motor.
In playing, the tiny bit of light as the arm moves results in a slow, tiny movement of the motor that drives a cord pulling the sled along its rail to center/align the arm. (maximum offset is 0.2 degrees!)
It's utterly silent in operation, smooth as butter.
A preforated disk and another LED/photocell counts the light pulses and as the disk slowly rotates, and the processor receives a count that determines just where the arm is. - similar to a printer's head as it prints.
At the end of the record, the counts trigger the arm to lift via a solenoid, activate the muting, then return to it's park position.
Same goes for starting a record - set the record size, speed, then the arm "counts" inward to the set diameter and lowers for play - muting turns off just after the stylus lands in the groove.
If a manual move and lower is done in the middle of a song track, the muting slowly (2.5 seconds) releases after the arm hits the groove.
For something made in the later 1980's, it's been trouble free except for one belt change on the arm traverse motor.
Last edited:
I've used old cutters that had pivot arms. They were meant for home use and weren't of the best quality. But it does seem odd that a high quality pivoting cutter wasn't made and used.
- Home
- Member Areas
- The Lounge
- Why are LPs cut with a parallel tracking arm?