Sorry if I'm questioning the obvious but regarding tonearm bearings I wonder why the following :
If the stylus has moved in response to the groove and via the mechanics of the cartridge sent a signal down the wires , then all the vibratory /resonance problems are due to reflected vibrations coming back from the bearing / counterweight or within the armtube.
If this is so , why aren't highly absorbant bearings the norm rather than extremely solid ones ? And absorbant counterweights rather than brass or other solids?
Perhaps there is a site explaining these things that I have yet to find , if so , could someone point me to it (& stop me posting dumb questions!).
Thanks
If the stylus has moved in response to the groove and via the mechanics of the cartridge sent a signal down the wires , then all the vibratory /resonance problems are due to reflected vibrations coming back from the bearing / counterweight or within the armtube.
If this is so , why aren't highly absorbant bearings the norm rather than extremely solid ones ? And absorbant counterweights rather than brass or other solids?
Perhaps there is a site explaining these things that I have yet to find , if so , could someone point me to it (& stop me posting dumb questions!).
Thanks
It's not a silly question and there isn't a web site that answers (any better than this one) these kinds of questions. Most (though not all) arm designs work on the principle that mechanical energy produced from the stylus is communicated via the cartridge body, into the arm and through the bearings to be dealt with by the chassis of the turntable. However, some arms like the Well Tempered do seek to terminate this energy at the bearing point. Designers of rigid bearing arms would probably suggest that your suggestion would result in increased colouration as energy would not pass through the bearing but be reflected back to the cartridge and stylus.
Hi,
The acoustic (as oppposed to mechanical) design of generic tonearms
is very limited, they are built to look like they do a job, and anything
radical generally goes straight into the niche market bucket.
The bearings have several jobs to do and they are in fact a very
poor point to try and absorb / dissapate energy in most arms.
A "well tempered arm" clone with a proper tube and headshell
would be one way of addressing the issue, the "Townshend trough"
is another.
🙂/sreten.
The acoustic (as oppposed to mechanical) design of generic tonearms
is very limited, they are built to look like they do a job, and anything
radical generally goes straight into the niche market bucket.
The bearings have several jobs to do and they are in fact a very
poor point to try and absorb / dissapate energy in most arms.
A "well tempered arm" clone with a proper tube and headshell
would be one way of addressing the issue, the "Townshend trough"
is another.
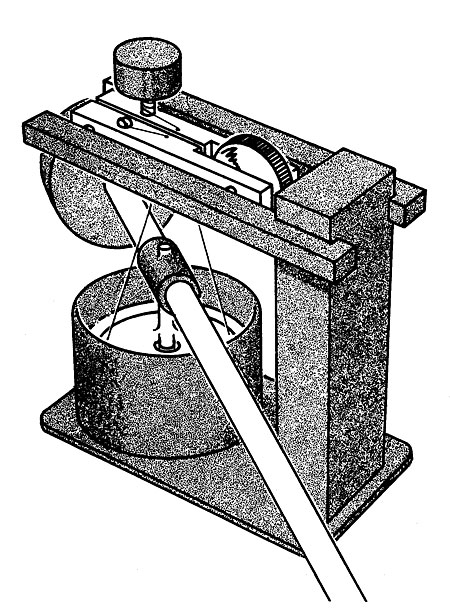
An externally hosted image should be here but it was not working when we last tested it.
🙂/sreten.
Another example is the Mayware Formula IV unipovot with silicone grease damping at the bearing pin.
I am glad allears brought up this nebulous subject which has been vexing me ever since I started making my own tonearms!
YNWOAN, I have come across this argument before, that the best way to "drain" tonearm energy is through a mechanically sound and solid connection. On the other hand, I have also read about "recoil" mechanism where I imagine the vibrational energy is reflected back to the source as it hits a solid obstacle (analogous perhaps to a ball hitting a solid wall). My interpretation might not be correct, a little elucidation will be greatly appreciated.
sreten, I would also appreciate if you could expand on your statement that bearings are a poor point to absorb/dissipate energy in most arms.
At the moment I am doing work on wood tonearms specifically to address this issue. Wood has a very high internal damping and seems to work quite well in taming unwanted energy. Excess energy is also more efficiently "drained" to the plinth through use of like materials in order to enhance conduction. This necessitated the use (of course) of a unipivot bearing made of wood!
All I can safely say is that I am so much in the dark here. Air bearings, unipivots, string bearings, magnetic bearings, knife edge, etc,etc! Some of them seem to work on diametrically opposite principles yet put out magnificent performances. Black Magic?
YNWOAN, I have come across this argument before, that the best way to "drain" tonearm energy is through a mechanically sound and solid connection. On the other hand, I have also read about "recoil" mechanism where I imagine the vibrational energy is reflected back to the source as it hits a solid obstacle (analogous perhaps to a ball hitting a solid wall). My interpretation might not be correct, a little elucidation will be greatly appreciated.
sreten, I would also appreciate if you could expand on your statement that bearings are a poor point to absorb/dissipate energy in most arms.
At the moment I am doing work on wood tonearms specifically to address this issue. Wood has a very high internal damping and seems to work quite well in taming unwanted energy. Excess energy is also more efficiently "drained" to the plinth through use of like materials in order to enhance conduction. This necessitated the use (of course) of a unipivot bearing made of wood!
All I can safely say is that I am so much in the dark here. Air bearings, unipivots, string bearings, magnetic bearings, knife edge, etc,etc! Some of them seem to work on diametrically opposite principles yet put out magnificent performances. Black Magic?
I have not (yet) experimented with tonearm design so all my knowledge is hypothesis (on my behalf) or the thoughts of others. I do know that supporters of gimbal bearing arms often believe that this solution provides a broad band mechanical link between the arm base and the arm tube. Detractors of gimgal bearings suggest that the nature of ball races means that they are not absolutely tight (or they would not rotate) and this causes bearing 'rattle' at certain frequencies, or that the construction of this type of bearing creates an impedance mis-match which means that certain frequencies pass through the bearing whilst others are reflected or only partially attenuated. Often detractors suggest that a unipivot is the answer. Supporters of unipivots point to their inherently low friction levels and claim that mechanical 'connection' is greater than with ball races citing that surface pressure is proportional to surface area. Detractors claim that unipivots are unstable and lack geometric accuracy - they also claim the exact opposite of unipivot supporters, and believe that unipivots suffer from bearing 'chatter' and lack rigidity. Somewhere amongst these clashing belief structures and divergent interpretations of the relevant forces, some truth must lie.
I haven't made a gimballed arm, but I have made unipivots. There are various ways of making unipivots, and it is possible to make one that chatters. Oddly, I find that a slightly lossy bearing works well - I use a ballpoint pen in PTFE as my bearing. I also use viscous damping elsewhere. There is no reason why the geometry of a unipivot need be anything less than perfect.
mandym said:I
sreten, I would also appreciate if you could expand on your statement
that bearings are a poor point to absorb/dissipate energy in most arms.
Hi,
My point is that given the job they have to do in practise if they do
this well you will find it difficult to disippate energy at that point.
🙂/sreten.
Hmm , interestingly diverse ways of looking at this business of vibration. I think it's going to come down to finding the right compromises , the ones that work musically , and that there will be no more "wrong" ways than there are wrong ways of making a musical instrument- if it sings it sings. I'm going to have to get some trial and error under my belt before I try to post again on this subject I think , but there is one more question regarding tonearm vibration that I'll put up as a new thread.
As soon as you make an "Absorbent" bearing, the vertical inertia will go up (Kiss of death). I'm not sure what you mean by absorbent bearing. Could you give an example?
My gimbaled arm uses a cup and cone arrangement, and the cups appear to have a white plastic insert. I know that if the bearings are slop free, even if the arm moves freely for all intents and purposes, the sound suffers. Loosening the pivots ever so slightly, so the bearings have some noticeable looseness, improves the sound greatly. IMO, reducing friction may be more important than coupling energy into the arm support- possibly the arm itself needs enough internal losses to deal with that issue, as we don't want arms that ring.
Ahh Haa! Now we're talking the same lingo (pardon the Pun on the Linn Power Supply!). You could probably lose the plastic insert. I frequently pry out the metal rings from so-called sealed bearings, which cause stiction. Then I flush out the heavy grease packed in there. Then use Tri-Flu, RemOil, or some other low viscosity synthetic lube. Some people swear by Dextron II ATF fluid. Here's what's happening when you loosen the bearings up. As the groove pulls on the stylus, the whole tonearm wants to move forward, which racks the cone pivot or axle against the balls nearest the forward end of the armtube. Towards the barrel of the rifle, not the butt. So when the balls are up against the wall, all slack is taken out of the system, and the cone is most likely only in contact with two of two of the balls. A very low friction condition, with a minumum of vertical inertia. Most of the inertia is probable due to the mass of the counterweight. One oof the commercial tonearms uses a system that only has three balls, and a cone. Clever. Another one has the counterweight suspended on a cable (very thin) to reduce the inertial forces, and to allow it too swing in response to the warps in the disc. As the stylus goes up the hill, the weight swingss back, reducing down force, preventing the cartridge suspension from bottoming out. The reverse happens when the cartridge crests the hill and starts its downward journey to sea level. Sorry for the prolix answer, but better to get a lot out there than responding four times to the nearly obvious follow up questions.
Thanks for your interesting responses , I think I just have to experiment so I can start to hear the physics happening so to speak. Otherwise , when I asked about absorbent bearings and counterweights it was just from thinking about my experience with musical instruments , in that with those one is trying to maximise resonance , whereas in a tonearm the opposite is true . So a big lump of brass in a guitar bridge will increase the resonance , a big lump of blu-tack will deaden it . So I wondered why the former was used for counterweights rather than something like blu-tack (only more rigid and massier of course , like a stiff blu-tack with bits of lead in it). And then looking at the Schroeder tonarms which have only a thread connecting the arm mechanically , so not draining the energy through a fixed bearing but with magnetic damping going on , I suppose I wondered what was wrong with trying to work with that "soft" bearing idea in the hope that it will offer a resonance-free arm at the expense of some rigidity, rather than a rigid arm that has to be damped . And then I keep coming across suggestions from highly-regarded designers that some element of "tuning" is involved in a good arm , that it is not after all completely different from a musical instrument , and it is in fact more of a case of choosing which frequencies need allowing and which need killing to make the music work.
So , I think onward and into the workshop is the way forward !
So , I think onward and into the workshop is the way forward !
makinson1 said
"As soon as you make an "Absorbent" bearing, the vertical inertia will go up (Kiss of death). I'm not sure what you mean by absorbent bearing. Could you give an example?"
Can you elaborate please? How is the inertia affected if you don't know "what it means" ?
sp
"As soon as you make an "Absorbent" bearing, the vertical inertia will go up (Kiss of death). I'm not sure what you mean by absorbent bearing. Could you give an example?"
Can you elaborate please? How is the inertia affected if you don't know "what it means" ?
sp
Think of what the heavy brass bridge does. It acts as a sink for the string vibration and releases the stored energy over time increasing the sustain, reflecting the sound over time. The tonearm counterweight does the same thing, so that the vibration from the cartridge is delayed and attenuated before it reflects back down the arm tube. Anything of substantial mass will store that energy preventing it from being reflected immediately back to the cartridge which would result in a smearing of the sound. So we look for counterweights, arm posts, and tonearm sound boards which have a low acoustical impedance at the frequencies in question. But high impedance under 20 Hz to filter out rumble and low frequency noise.
makinson1 said:Think of what the heavy brass bridge does. It acts as a sink for the string vibration and releases the stored energy over time increasing the sustain, reflecting the sound over time. The tonearm counterweight does the same thing, so that the vibration from the cartridge is delayed and attenuated before it reflects back down the arm tube. Anything of substantial mass will store that energy preventing it from being reflected immediately back to the cartridge which would result in a smearing of the sound. So we look for counterweights, arm posts, and tonearm sound boards which have a low acoustical impedance at the frequencies in question. But high impedance under 20 Hz to filter out rumble and low frequency noise.
Now I'm more confused as ever


I better stay out of this🙂
Mandym, coming from the land of Manny Pacquiao,
you should know that you don't have to actually get in the ring to enjoy the fight. The physics of the tonearm can only be understood by taking it in small bites. Start with some basic articles such as this one at TNT:
http://www.tnt-audio.com/sorgenti/armdesign_e.html
Then progress up to some in-depth reviews of tonearms that focus on the mechanics of the arm rather than the subjective listening tests. Check out the Theory and Design paragraphs of this one for instance:
http://www.tnt-audio.com/sorgenti/belladonna3_e.html
you should know that you don't have to actually get in the ring to enjoy the fight. The physics of the tonearm can only be understood by taking it in small bites. Start with some basic articles such as this one at TNT:
http://www.tnt-audio.com/sorgenti/armdesign_e.html
Then progress up to some in-depth reviews of tonearms that focus on the mechanics of the arm rather than the subjective listening tests. Check out the Theory and Design paragraphs of this one for instance:
http://www.tnt-audio.com/sorgenti/belladonna3_e.html
Attachments
Ah yes, I enjoy boxing specially if my man is winning. I wish though that I knew more about the sport so I can enjoy it better.
Thanks much for the instructional links you provided. I briefly glanced at it and it seems I'll have to do some wading in deeper waters but I am sure (I hope) I can learn something from it. From Paquiaoland, thanks again Makinson1.
Thanks much for the instructional links you provided. I briefly glanced at it and it seems I'll have to do some wading in deeper waters but I am sure (I hope) I can learn something from it. From Paquiaoland, thanks again Makinson1.
- Status
- Not open for further replies.
- Home
- Source & Line
- Analogue Source
- tonearm absorbant bearings?