Any reason a Tekpower-TP3005D-3 DC Linear power supply wouldn't be adequate for my mosfet/vfet testing needs?
https://www.amazon.com/Tekpower-TP3...id=1480099498&sr=8-6&keywords=Tekpower+linear
Purchase yet? This one gets good marks in the budget category.
BK
Already purchased 🙂. Expecting delivery Tuesday. But thank you for the pointer! The Korad looks to have a few more bells and whistles. The Tekpower is pretty much just a couple knobs and a few switches. Should still meet my simple needs, though. Hopefully.
Those PSU are excellent for amp testing and very good value for the money.
For FET/Mosfet testing I would suggest you to get a dedicated instrument like the cheap and versatile FET tester by lucky_z.......
For FET/Mosfet testing I would suggest you to get a dedicated instrument like the cheap and versatile FET tester by lucky_z.......
Hi NicMac! The locky_z intelligent curve tracer is definitely on my radar - and next on the list. Sadly, I had to pick between the bench supply and the curve tracer this time around, to not bust the budget. Couldn't get both. Aside from the vfets, i think most all my other small signal devices should be pretty well matched - having come from good sources. The jfets are all from Spencer, 1530/201s and 2013/313s were from you ( thank you 😉 ), and what fqa/fqp devices I have left were from Buzzforb. Trying to work on putting more of them to use 🙂.
Cody
Cody
Already purchased 🙂. Expecting delivery Tuesday. But thank you for the pointer! The Korad looks to have a few more bells and whistles. The Tekpower is pretty much just a couple knobs and a few switches. Should still meet my simple needs, though. Hopefully.
I don't have the KA3305P, but considered it. $159 shipped for next few days. Not too shabby! I'm sure they're both comparable.
BK
Locky_Z curve tracer tool work only on PC with Windows7 OS version.
🙂
Locky_Z's curve tracer works perfectly in Windows 10 as well as in Windows 8.x. The issue is that the serial to USB chip vendor changed their drivers so that older chips were not supported in new OSS -- trying to make a buck. You can use the older driver in the new OSs, just Google a little and you will find the answer.
Supplemental kit update:
There will be a total of 197 of these Supplemental kits to cover all the releases of the Essentials kits. They are in the final stages of production and will be available in about 3 weeks, well within schedule!
There were some still available for people on the final list for Essentials kits, but I don't know if there still are any. Not starting on the final (3rd)Essentials Kits until we get this single run of Supplemental kits done.
Will ask Jason to update here also.
There will be a total of 197 of these Supplemental kits to cover all the releases of the Essentials kits. They are in the final stages of production and will be available in about 3 weeks, well within schedule!
There were some still available for people on the final list for Essentials kits, but I don't know if there still are any. Not starting on the final (3rd)Essentials Kits until we get this single run of Supplemental kits done.
Will ask Jason to update here also.
There were some still available for people on the final list for Essentials kits, but I don't know if there still are any..
Don't understand what you are saying here. Please rephrase. Thanks.
Sneak preview, not even close to complete yet.
🙂
`````````````````
Building the Vfet amp
Schematic.
Note that Q3 is NPN the kit includes a ZTX450 for this position, Q4 is PNP and the ZTX550.
Example PSU Schematic
Please take a look at this photo -
I would like to take this opportunity to strongly suggest that you print out the schematic of the circuit and tape it to a spot where you can see it during the entire process. Does it need to be as big as shown? Well, no, but it certainly doesn’t hurt.
After printing out the appropriate schematics, build the PSU. Detailed notes are in another post in this thread. You’ll need the PSU operative for part 2 of the amp PCB test. Of course, those of you with bipolar bench PSU can use those for the testing, but most builders will need to use the amp’s PSU for that.
Begin by stuffing only the Resistors and Potentiometers.
How the PCB should appear for Testing Part 1 - Testing the resistors.
Please note, at this point the PCB has only the resistors and potentiometers, no semiconductors (including diodes) nor capacitors.
This test is very straightforward - print out the page of Nelson’s notes with the chart and measure as instructed. During this test a number of resistances are measured to verify that 1) the proper values are stuffed in the proper locations, and 2) to see if there are any gross soldering errors so far. If you see any measured values much different than on the chart, check the value of the component and check your solder joints. If everything measures incorrectly, replace the battery in your multimeter.
Did the test go well? If so, move on. If not, look it over, find the error, and correct it.
There are certain things that need to next be mounted to the PCB in conjunction with the heatsinks and the T-brackets. Let’s go over that now.
The first step is to mount the T-brackets to the heatsinks.
Apply heatsink goop to the bracket and very firmly press it into the heatsink, to spread it into the irregularities of the aluminum surfaces. On my first attempt I didn’t put nearly enough down and it looked like this.
More was applied, the surfaces pressed and smeared to get good coverage, but there were still gaps.
I realized that mere pressure wasn’t enough, so a thin layer was spread around both sides of the interface. That looks better.
Remember, there is such a thing as too much heatsink goop, it’s purpose is to fill in any air gaps, normal white goop is slightly thermally insulating, but it’s much more conductive than air… So a thin layer is better than a thick one.
However, if you have a heatsink compound that’s thermally conductive, like Arctic Silver, this is a perfect application for it. There is no electrical connection in this interface, just thermal, so use it if you have it.
Now secure the T-bracket to the heatsink, and observe the proper torque pattern below.
M3 screw, lock washer, washer.
The brackets need to be attached like a cylinder head attached to an engine block, you must start in the center and work your way out, in order to insure the bracket is as flat as possible on the heatsink. If you proceed as shown it will have the greatest likelihood of being flat. Just attaching the screws randomly will almost guarantee a gap under the T-bracket. A gap will be easy enough to see.
Start with these two screws and torque them.
Then the other two in the inside.
One set of opposite corners
And the final corners.
The Torque order shown on one photo
Please note that the mounting holes for the TO-3 package Vfet are not symmetrical. The pins (center holes) are slightly offset in one direction regarding the mounting screws. And the PCB mounts under the T-bracket. So make sure the holes in the PCB align with the holes in the bracket.
Also please see that there are no specific holes to mount the amp PCB to the T-bracket. The screws for the Mosfets and and the Vfets are sufficient to hold everything together.
Capacitors and regulators installed.
Stuff the capacitors, TO-220 package Mosfet with heatsinks, regulators, Jfets, BJT, and diodes (some of those are not shown in this photo)
The small mosfets shown are in the TO-220FP package, so no insulator is required. You do need a bit of heatsink compound, so smear a bit on and try to achieve better coverage than in this photo. If your mosfets have an exposed metal tab then you'll need a small plastic sleeve for the holes and an insulator. These sleeves are supplied in the supplemental kit along with TO-220 mica insulators which require grease on each side.
Use this hardware to attach the assembly to the board as shown below.
Attaching the power Mosfet will give sufficient hold to the PCB and the bracket.
Bend the leads down, and apply the mica insulator and goop.
Get this hardware from the parts kit,
And attach as such. The small washer is under the PCB on the bottom, and the lock washer is under the nut above the fender washer on the top.
Attach both devices
And verify that the holes for the TO-3 Vfets align in the bracket properly.
If so, now you can tighten the power Mosfet screws, and solder the pins to the PCB.
At this point all this should be stuffed on the PCB.
🙂
`````````````````
Building the Vfet amp
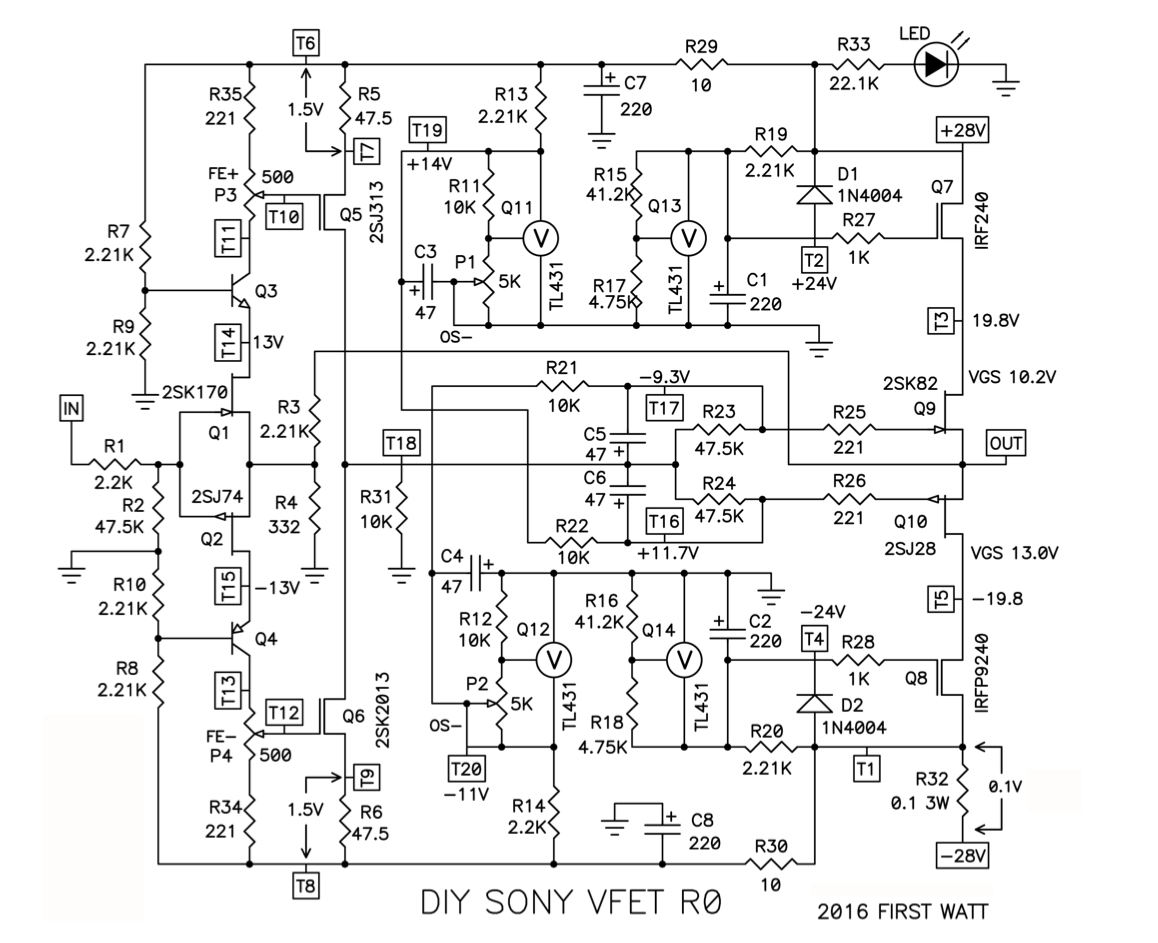
Schematic.
Note that Q3 is NPN the kit includes a ZTX450 for this position, Q4 is PNP and the ZTX550.

Example PSU Schematic
Please take a look at this photo -
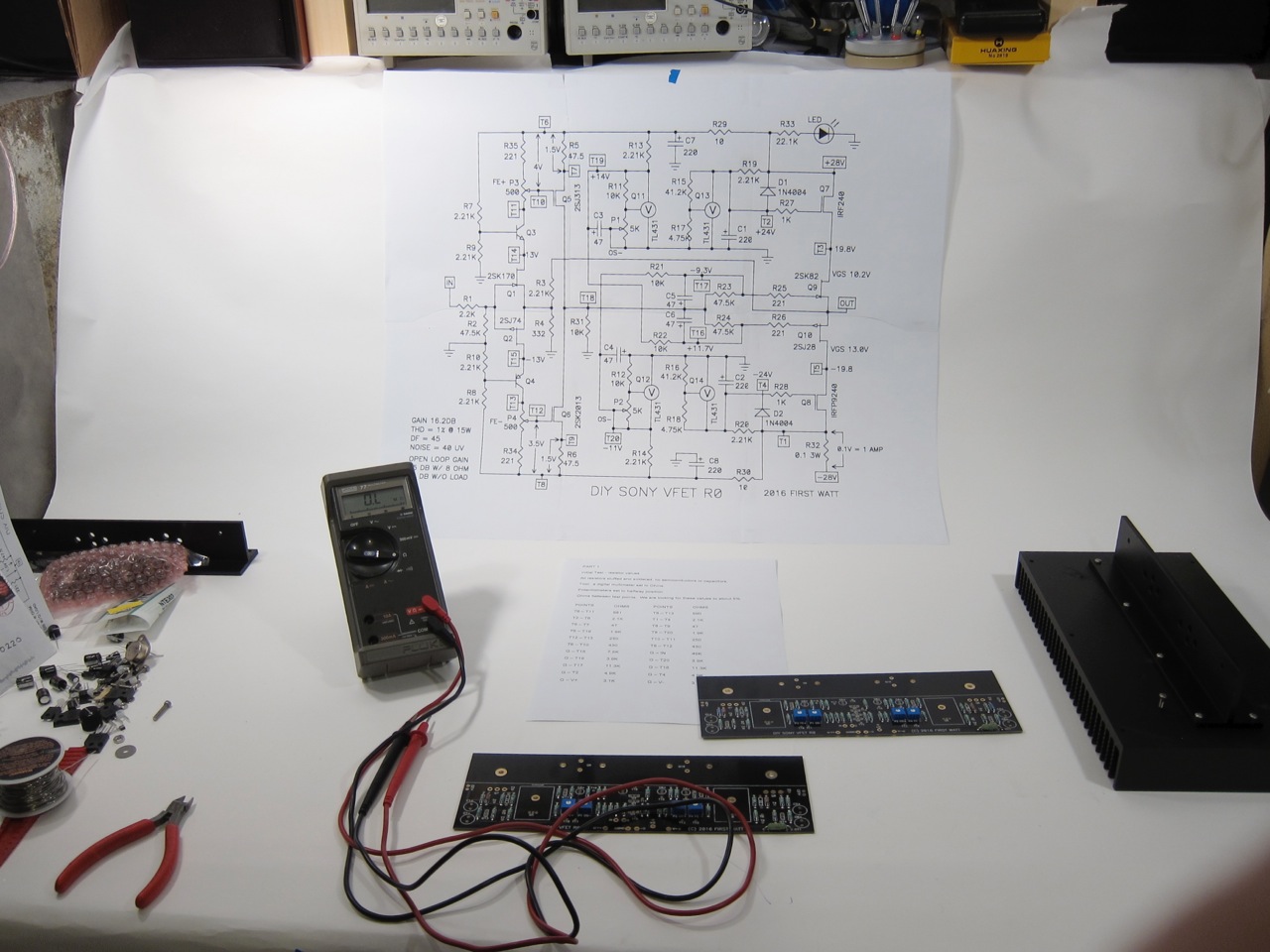
I would like to take this opportunity to strongly suggest that you print out the schematic of the circuit and tape it to a spot where you can see it during the entire process. Does it need to be as big as shown? Well, no, but it certainly doesn’t hurt.
After printing out the appropriate schematics, build the PSU. Detailed notes are in another post in this thread. You’ll need the PSU operative for part 2 of the amp PCB test. Of course, those of you with bipolar bench PSU can use those for the testing, but most builders will need to use the amp’s PSU for that.
Begin by stuffing only the Resistors and Potentiometers.

How the PCB should appear for Testing Part 1 - Testing the resistors.
Please note, at this point the PCB has only the resistors and potentiometers, no semiconductors (including diodes) nor capacitors.
This test is very straightforward - print out the page of Nelson’s notes with the chart and measure as instructed. During this test a number of resistances are measured to verify that 1) the proper values are stuffed in the proper locations, and 2) to see if there are any gross soldering errors so far. If you see any measured values much different than on the chart, check the value of the component and check your solder joints. If everything measures incorrectly, replace the battery in your multimeter.
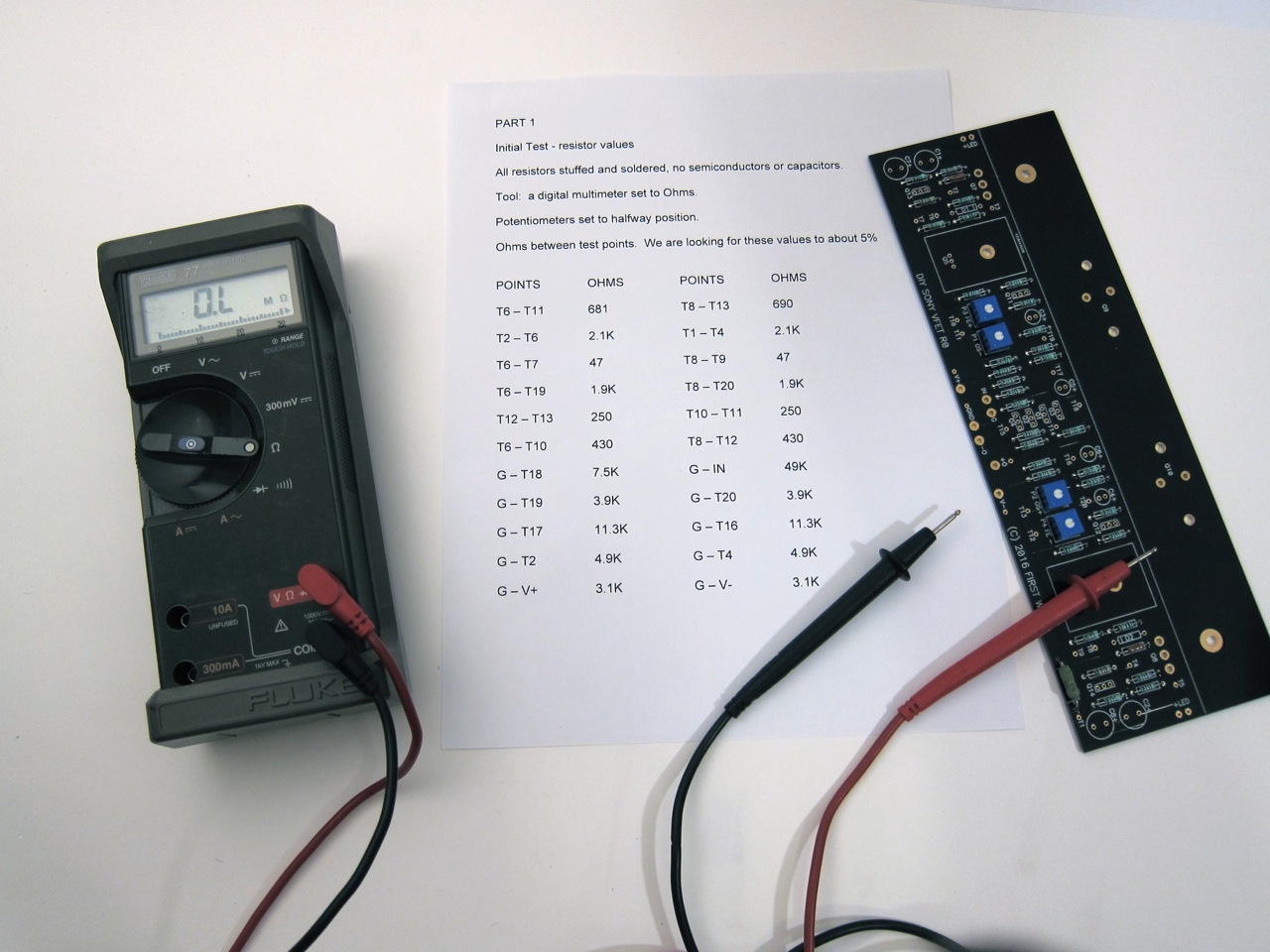
Did the test go well? If so, move on. If not, look it over, find the error, and correct it.
There are certain things that need to next be mounted to the PCB in conjunction with the heatsinks and the T-brackets. Let’s go over that now.
The first step is to mount the T-brackets to the heatsinks.
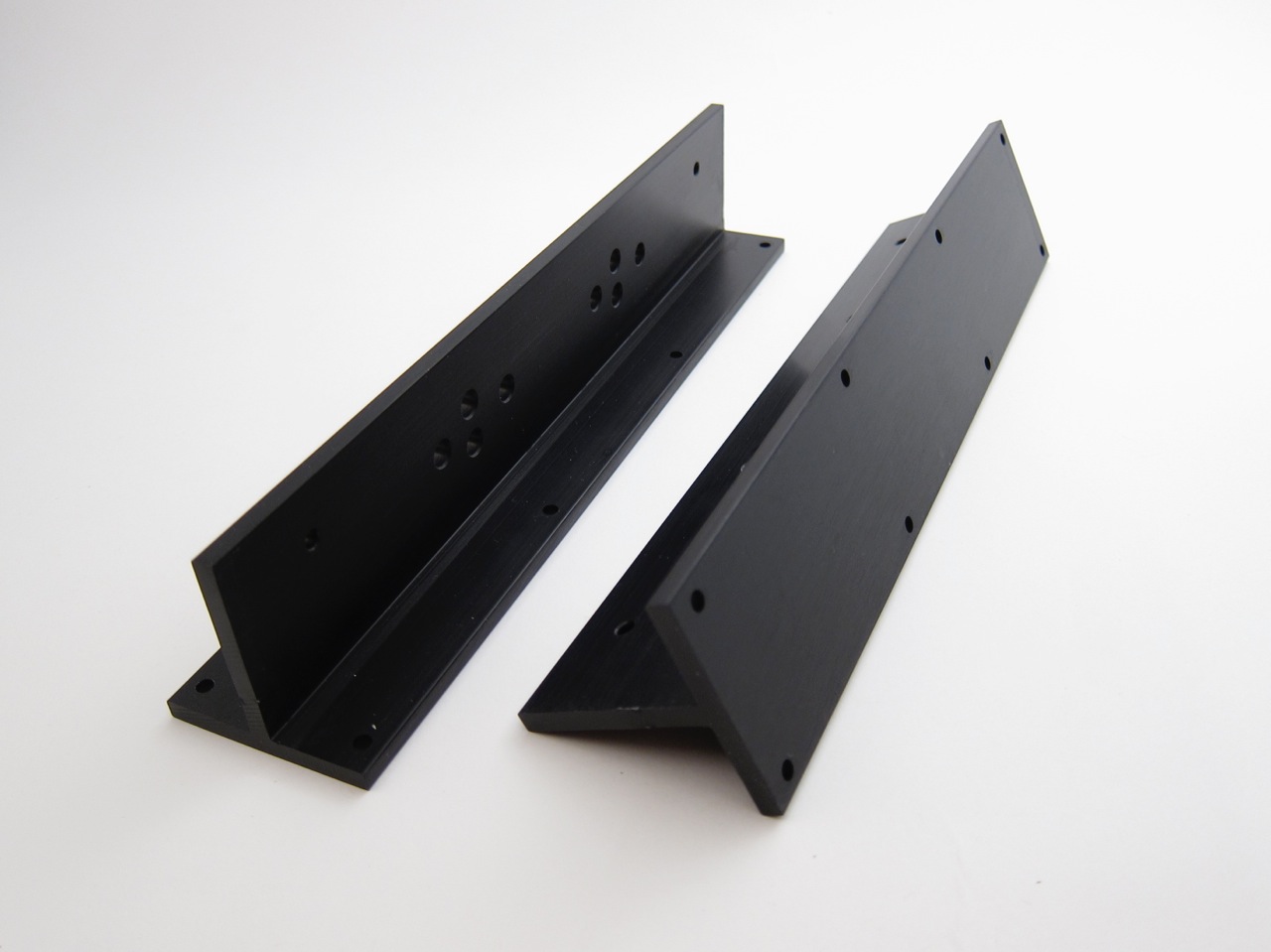
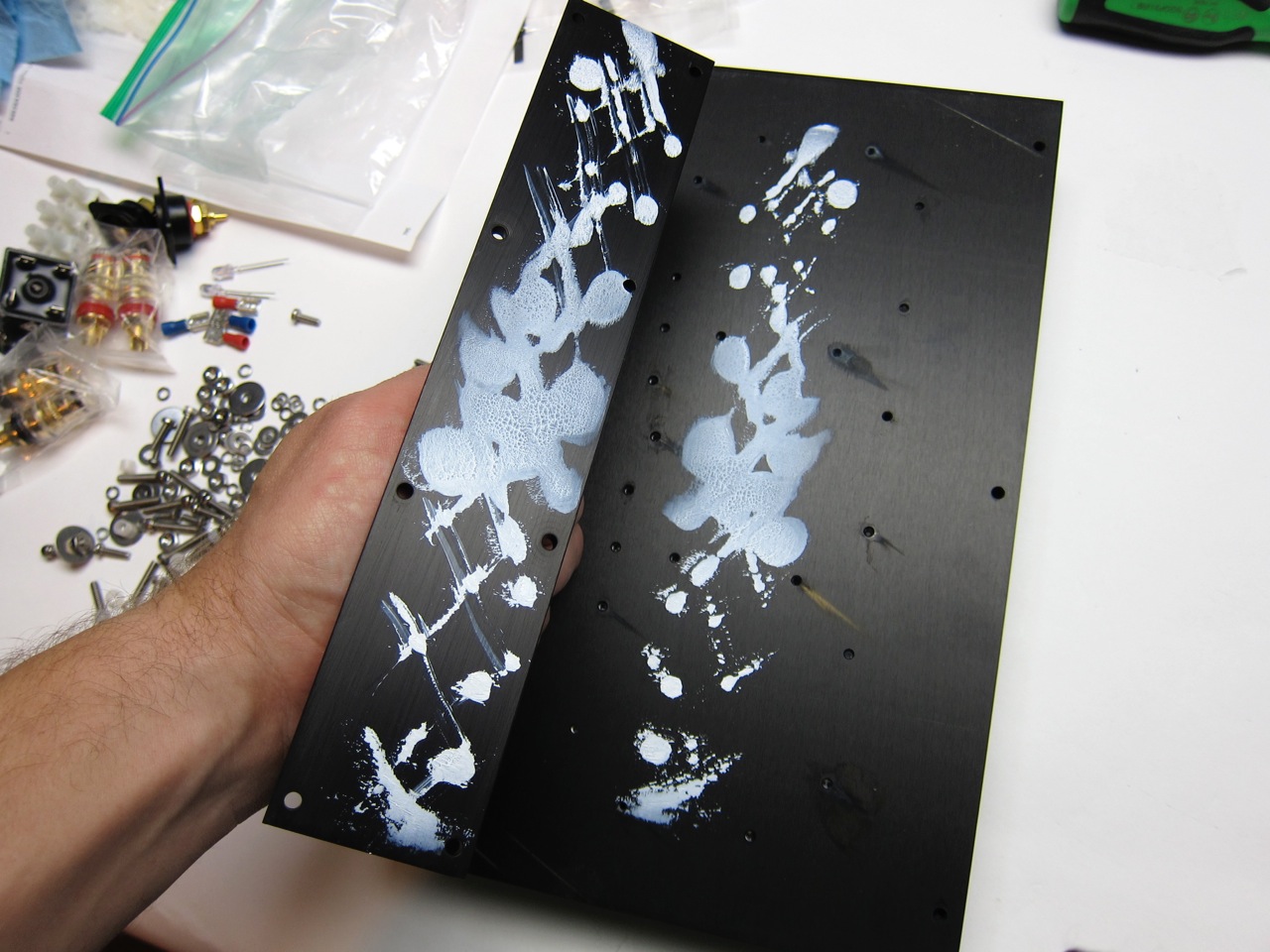
Apply heatsink goop to the bracket and very firmly press it into the heatsink, to spread it into the irregularities of the aluminum surfaces. On my first attempt I didn’t put nearly enough down and it looked like this.
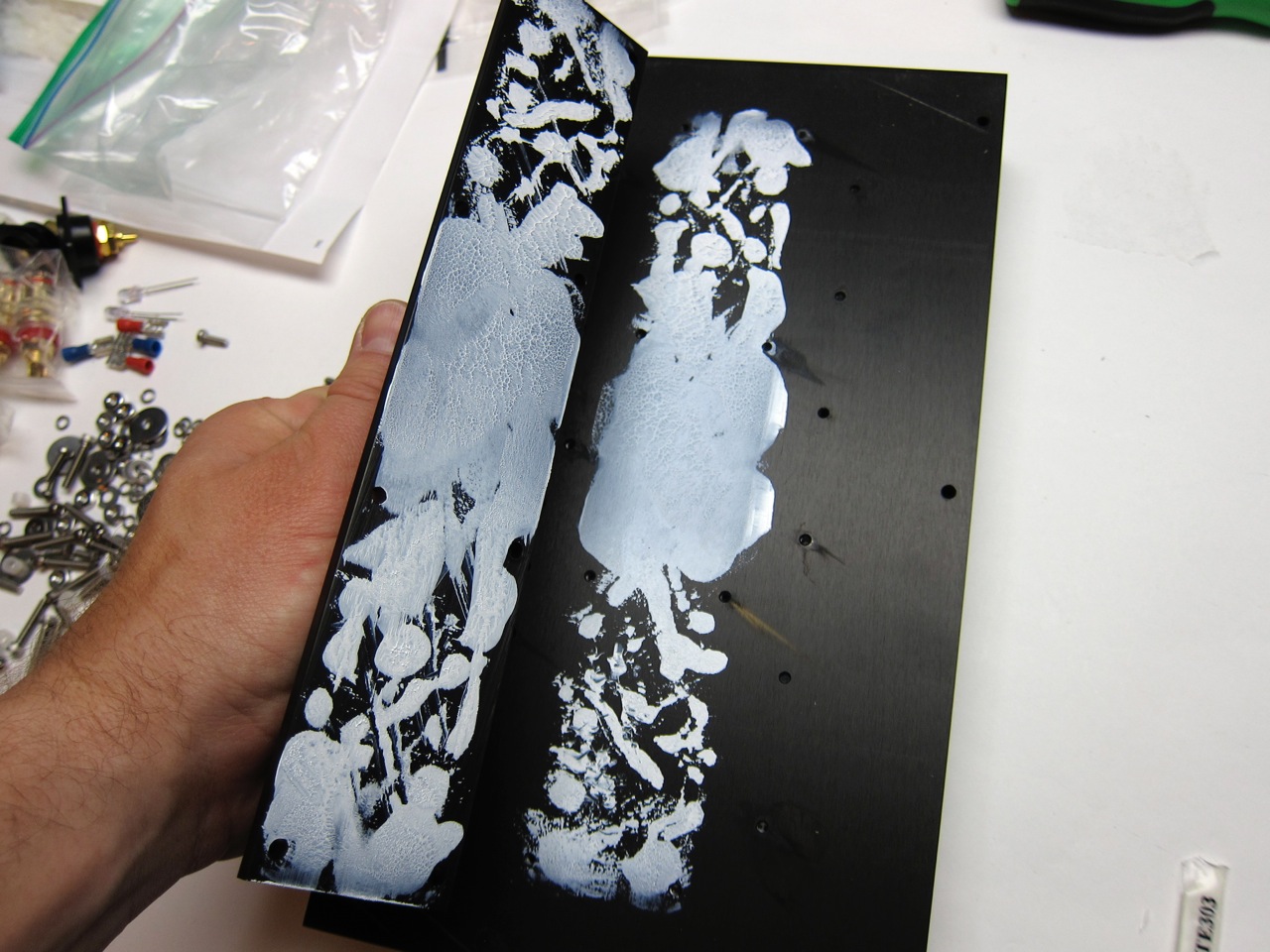
More was applied, the surfaces pressed and smeared to get good coverage, but there were still gaps.
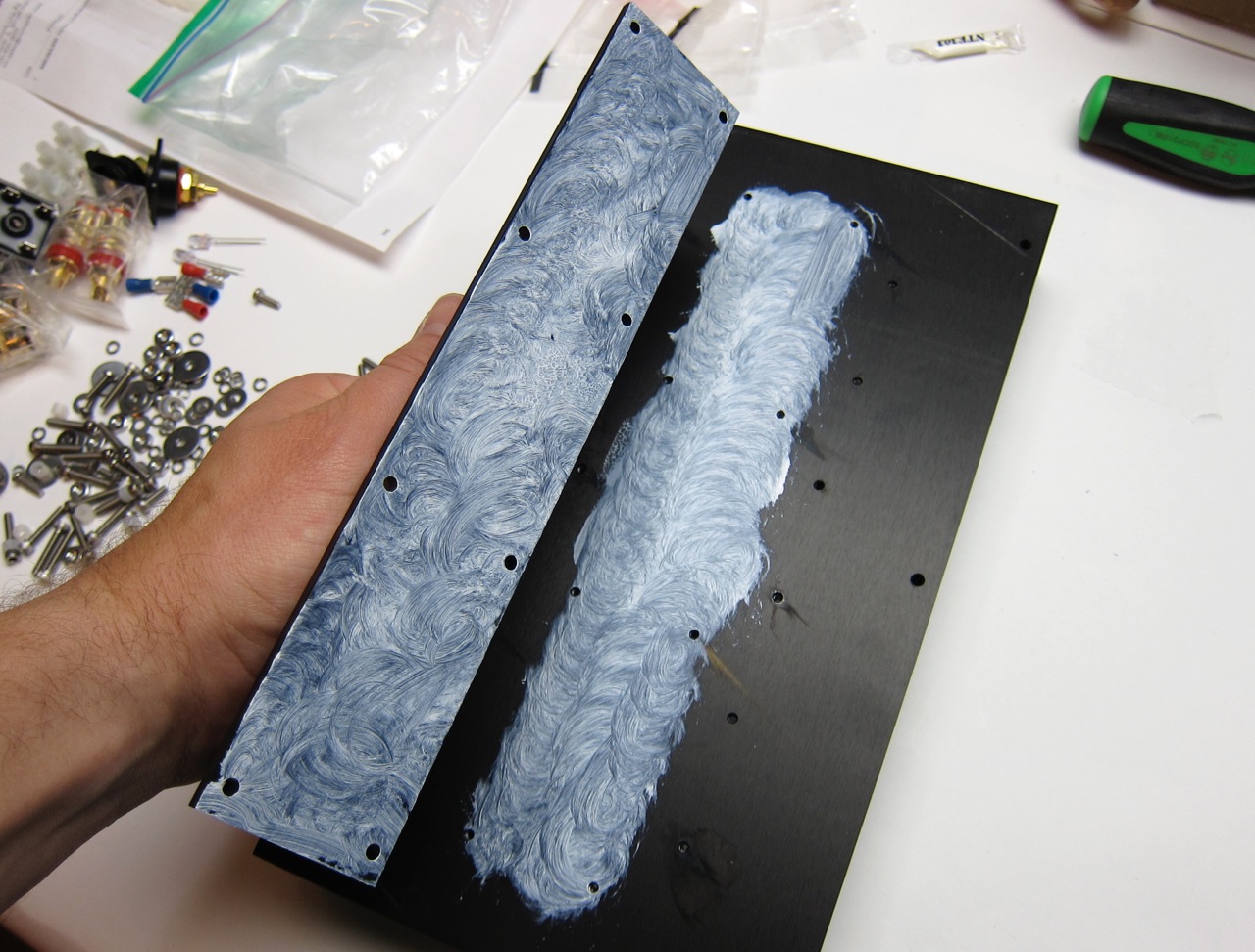
I realized that mere pressure wasn’t enough, so a thin layer was spread around both sides of the interface. That looks better.
Remember, there is such a thing as too much heatsink goop, it’s purpose is to fill in any air gaps, normal white goop is slightly thermally insulating, but it’s much more conductive than air… So a thin layer is better than a thick one.
However, if you have a heatsink compound that’s thermally conductive, like Arctic Silver, this is a perfect application for it. There is no electrical connection in this interface, just thermal, so use it if you have it.
Now secure the T-bracket to the heatsink, and observe the proper torque pattern below.
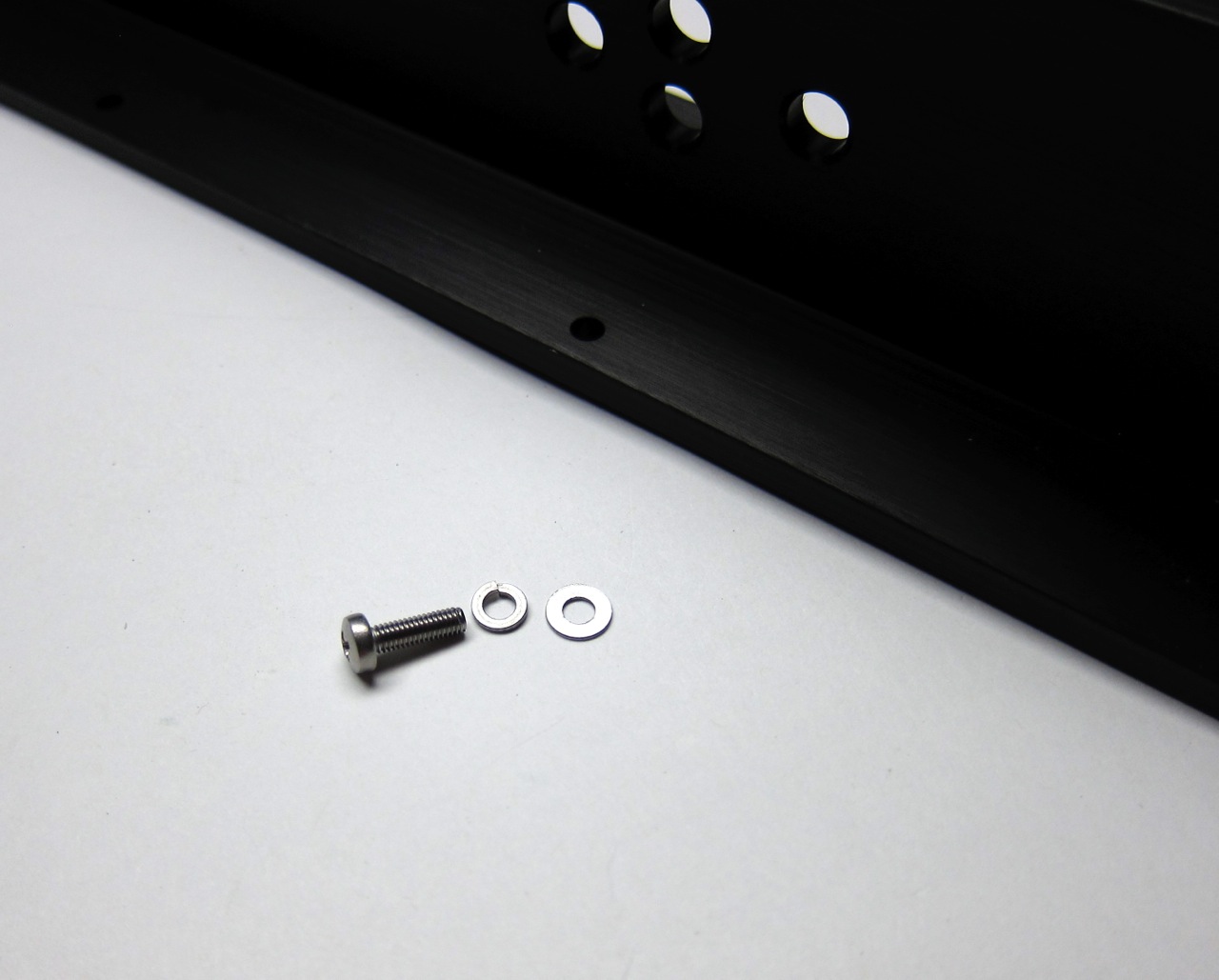
M3 screw, lock washer, washer.
The brackets need to be attached like a cylinder head attached to an engine block, you must start in the center and work your way out, in order to insure the bracket is as flat as possible on the heatsink. If you proceed as shown it will have the greatest likelihood of being flat. Just attaching the screws randomly will almost guarantee a gap under the T-bracket. A gap will be easy enough to see.

Start with these two screws and torque them.
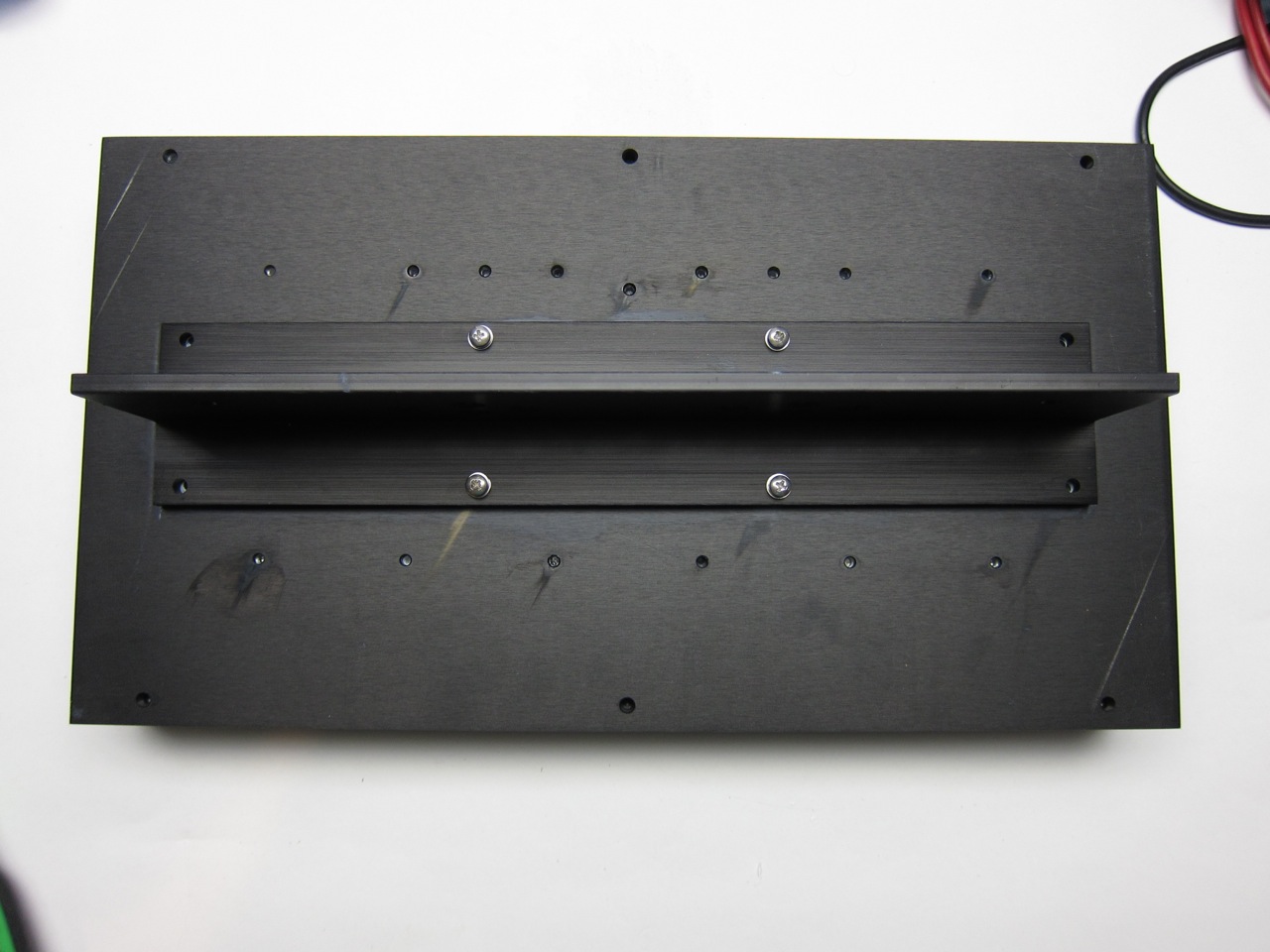
Then the other two in the inside.
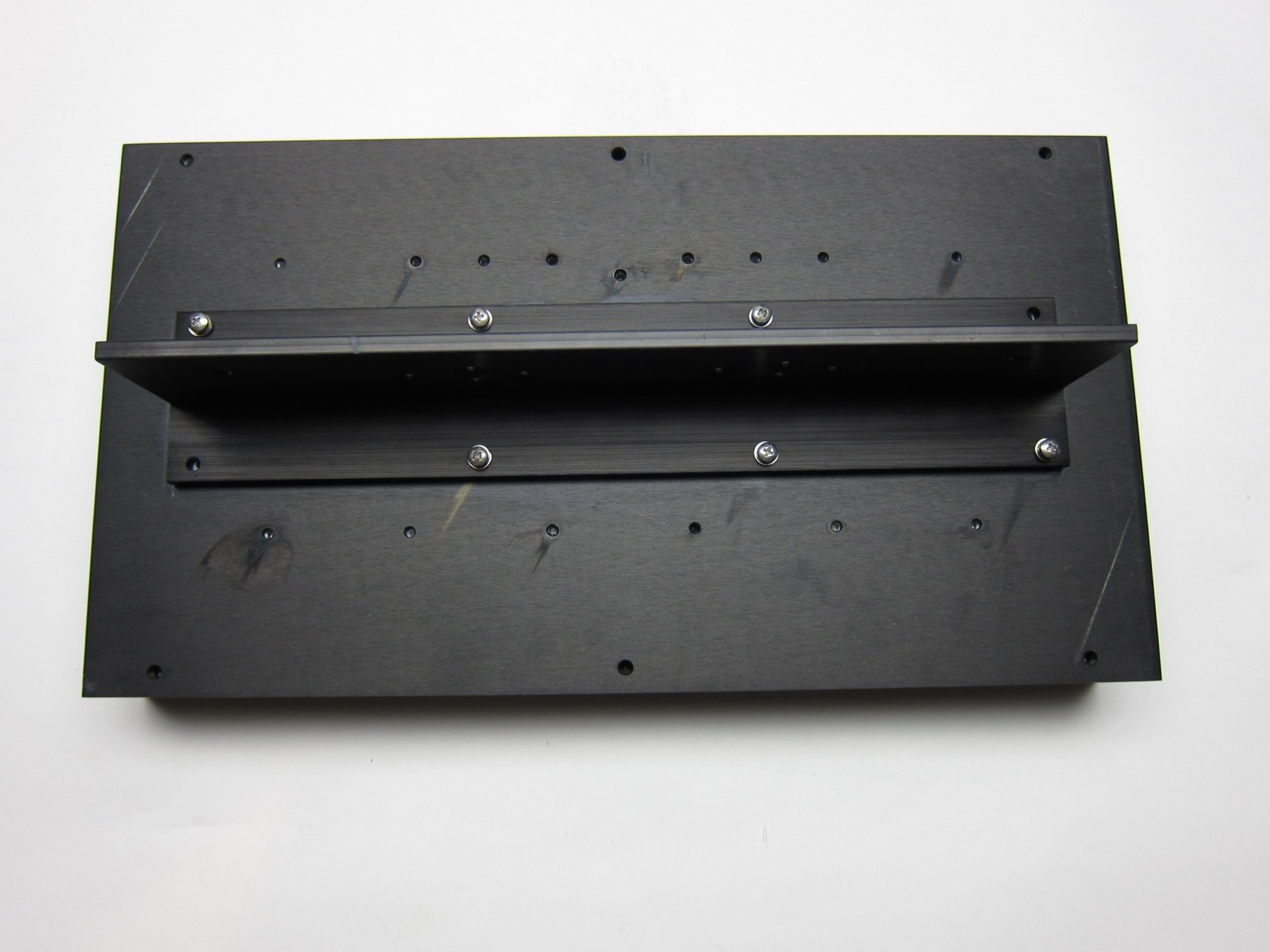
One set of opposite corners
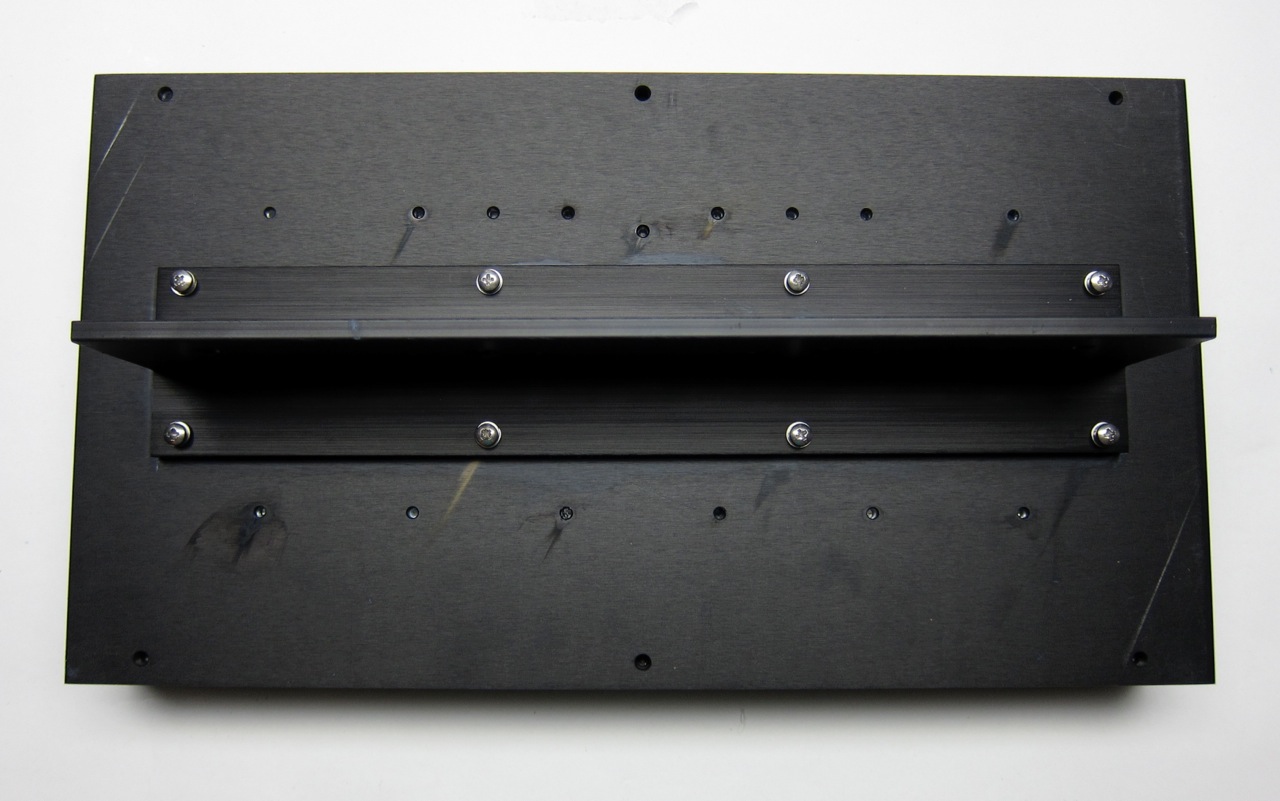
And the final corners.

The Torque order shown on one photo
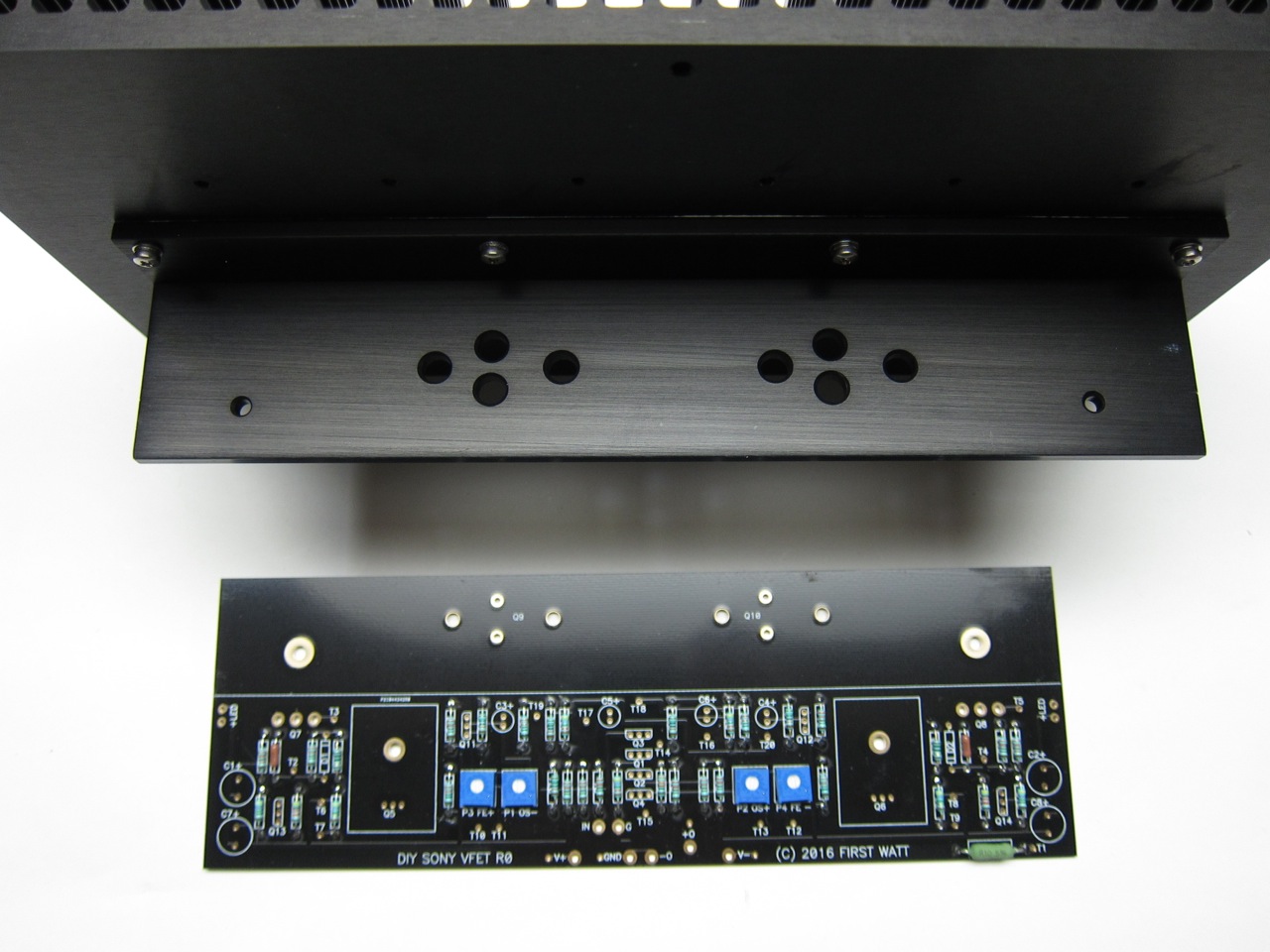
Please note that the mounting holes for the TO-3 package Vfet are not symmetrical. The pins (center holes) are slightly offset in one direction regarding the mounting screws. And the PCB mounts under the T-bracket. So make sure the holes in the PCB align with the holes in the bracket.
Also please see that there are no specific holes to mount the amp PCB to the T-bracket. The screws for the Mosfets and and the Vfets are sufficient to hold everything together.

Capacitors and regulators installed.
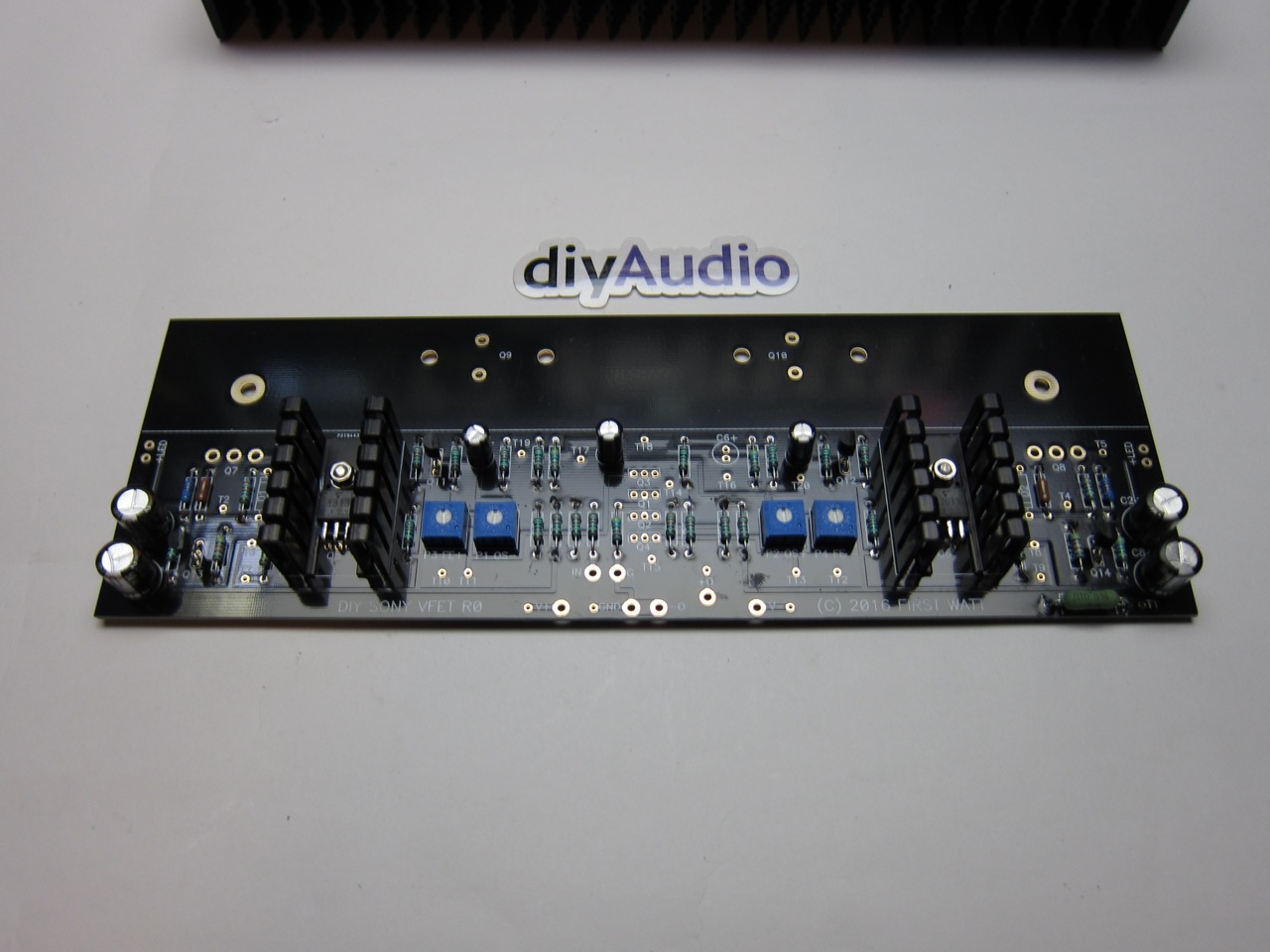
Stuff the capacitors, TO-220 package Mosfet with heatsinks, regulators, Jfets, BJT, and diodes (some of those are not shown in this photo)

The small mosfets shown are in the TO-220FP package, so no insulator is required. You do need a bit of heatsink compound, so smear a bit on and try to achieve better coverage than in this photo. If your mosfets have an exposed metal tab then you'll need a small plastic sleeve for the holes and an insulator. These sleeves are supplied in the supplemental kit along with TO-220 mica insulators which require grease on each side.
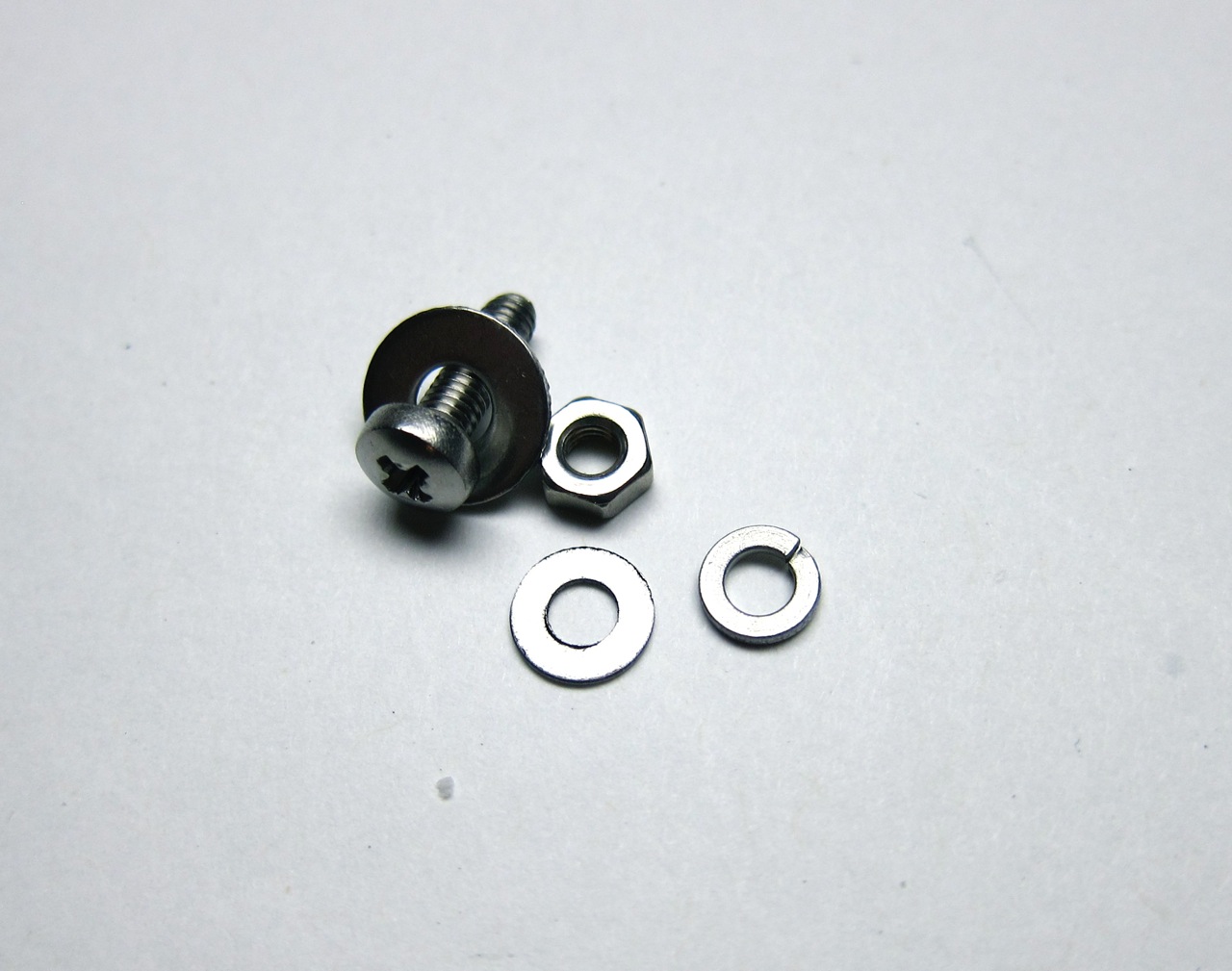
Use this hardware to attach the assembly to the board as shown below.
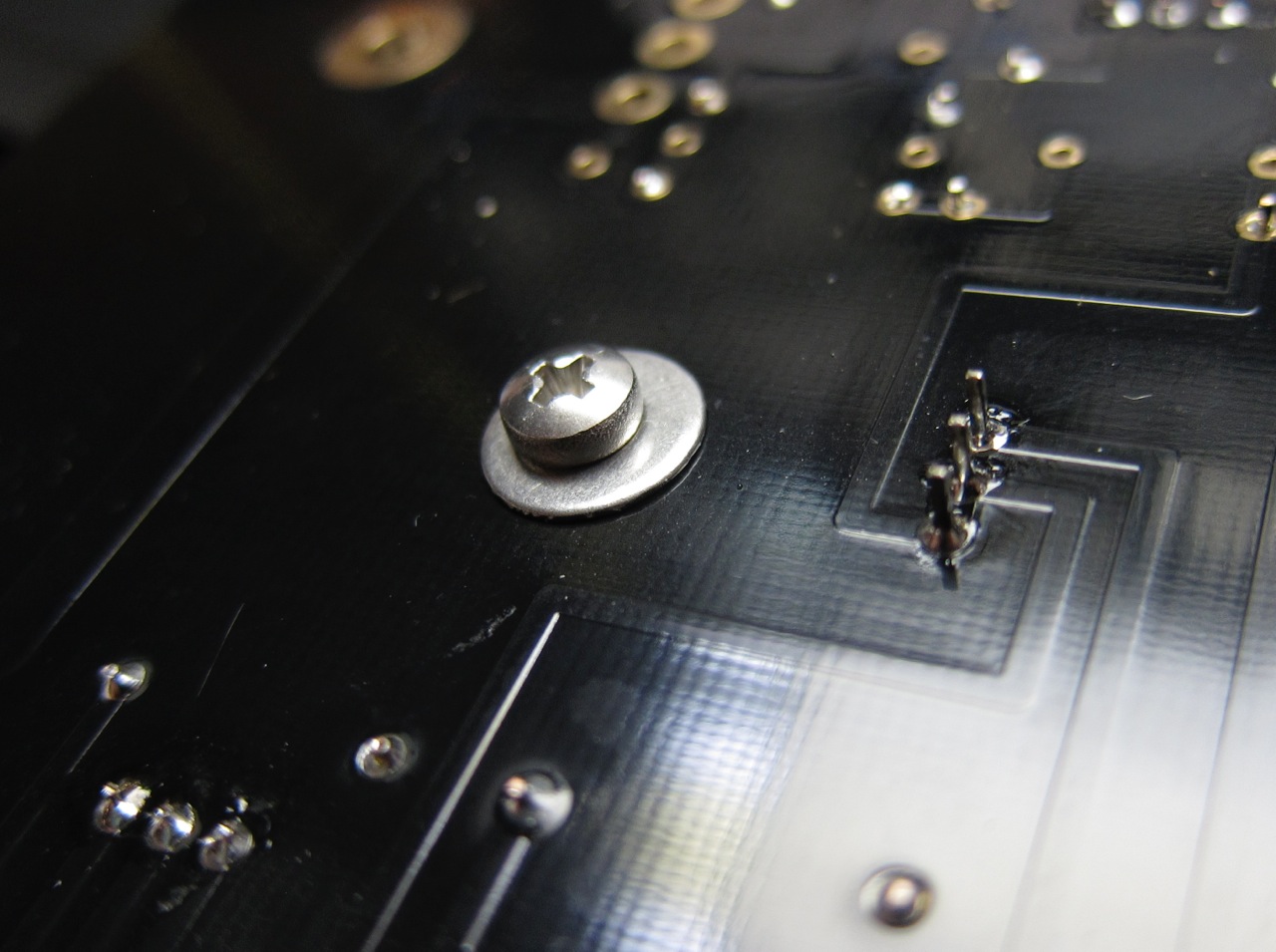
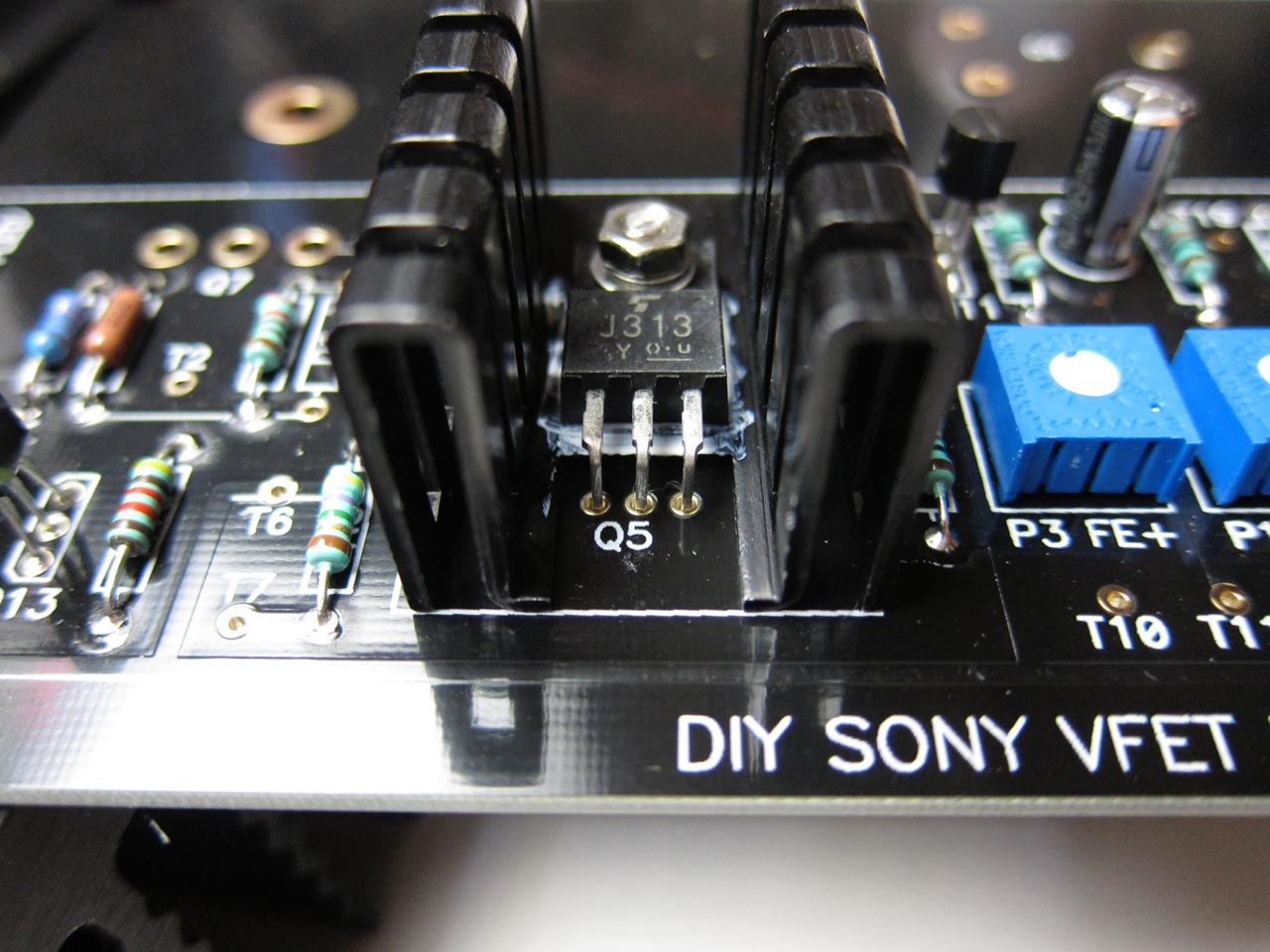
Attaching the power Mosfet will give sufficient hold to the PCB and the bracket.
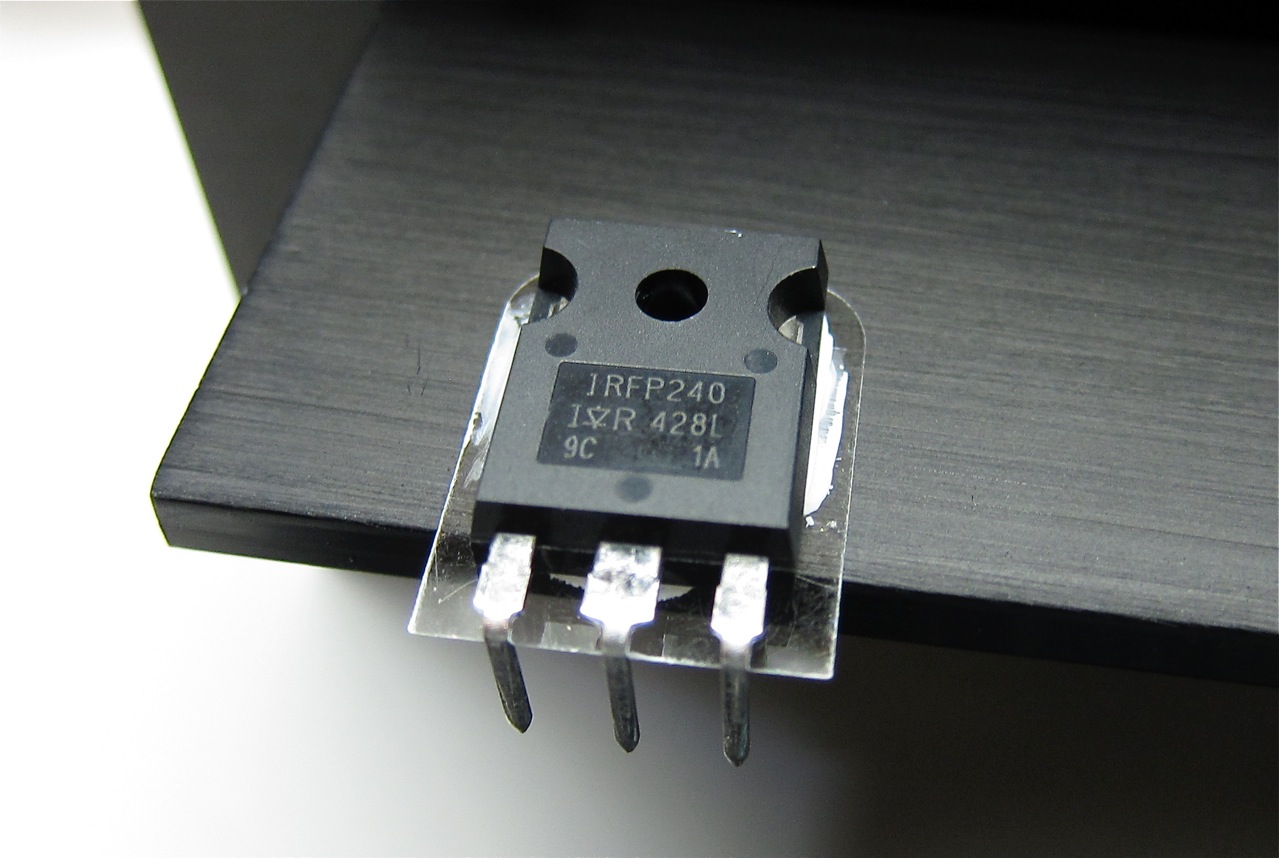
Bend the leads down, and apply the mica insulator and goop.
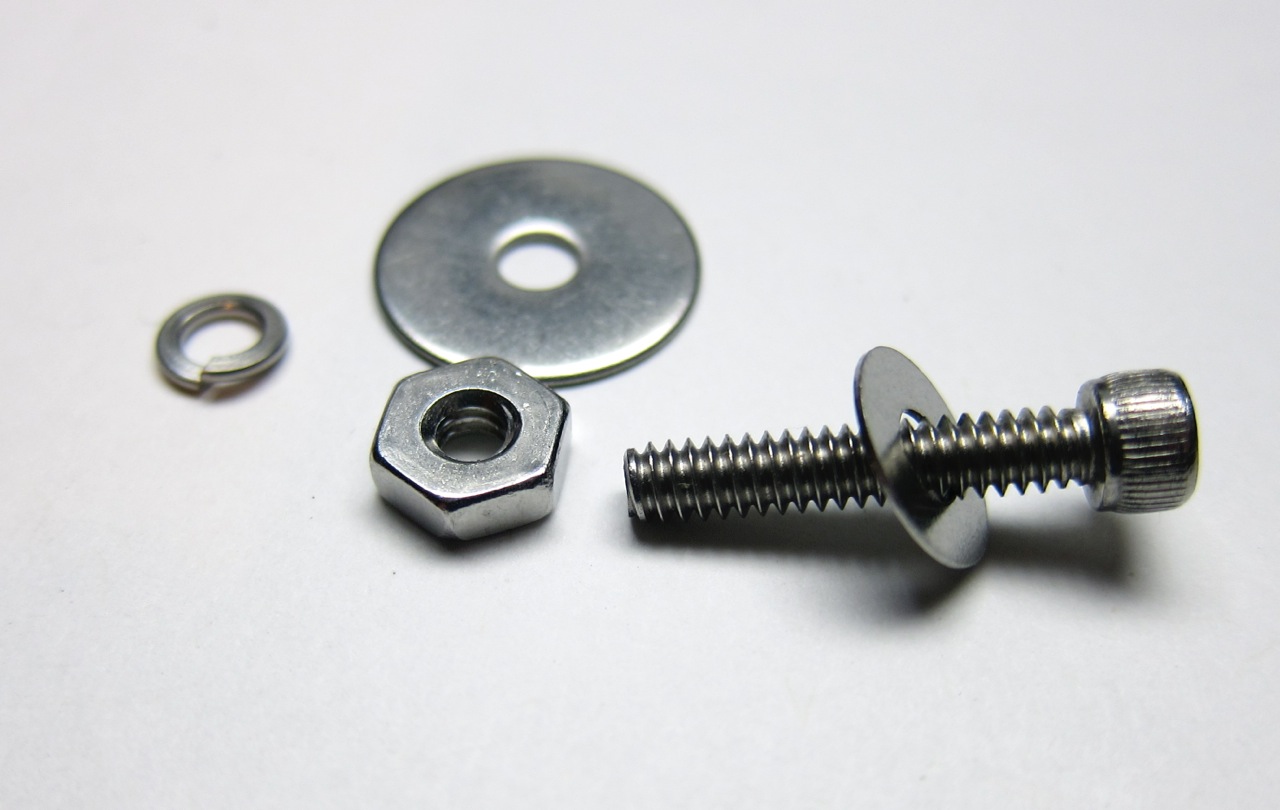
Get this hardware from the parts kit,
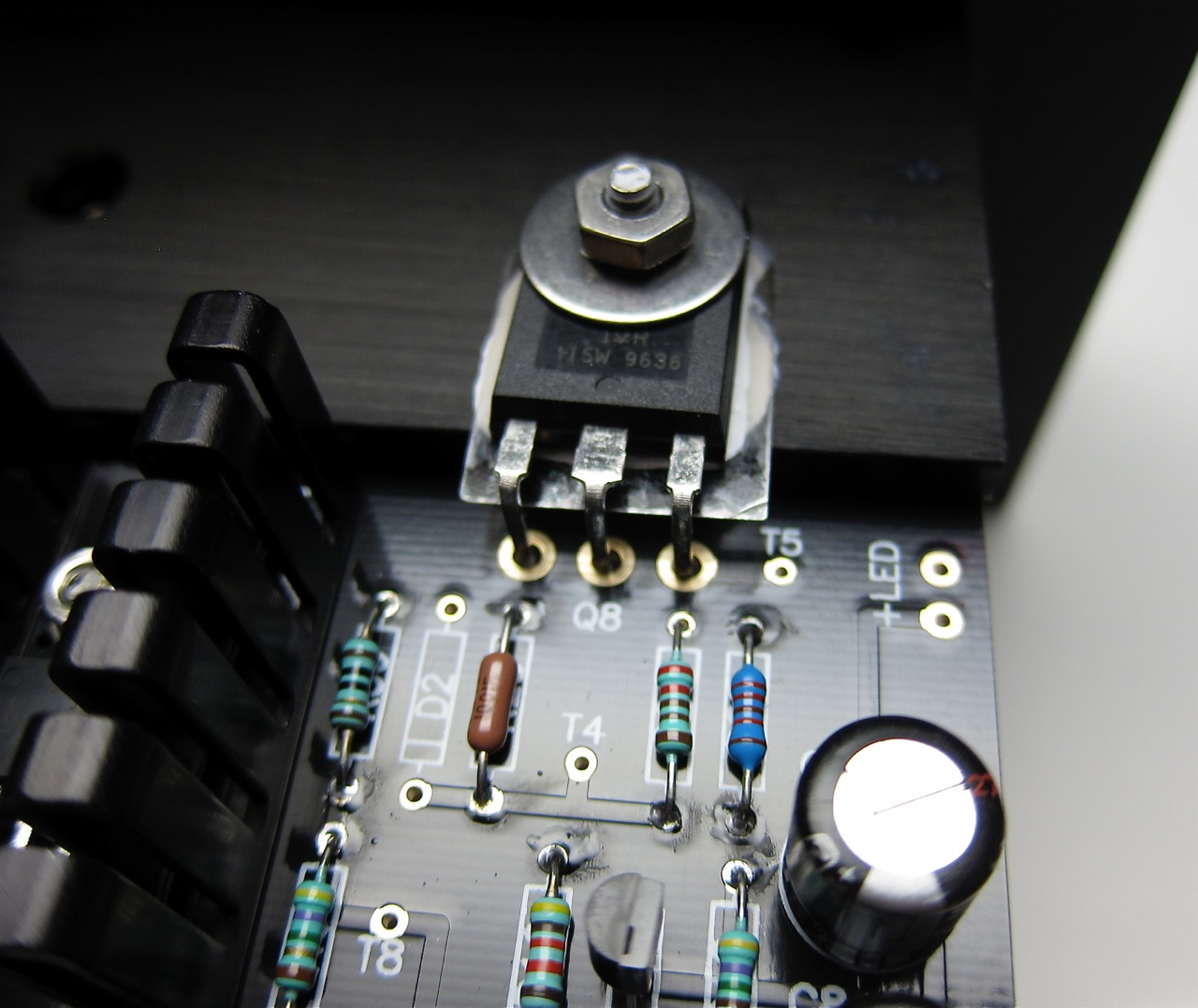
And attach as such. The small washer is under the PCB on the bottom, and the lock washer is under the nut above the fender washer on the top.
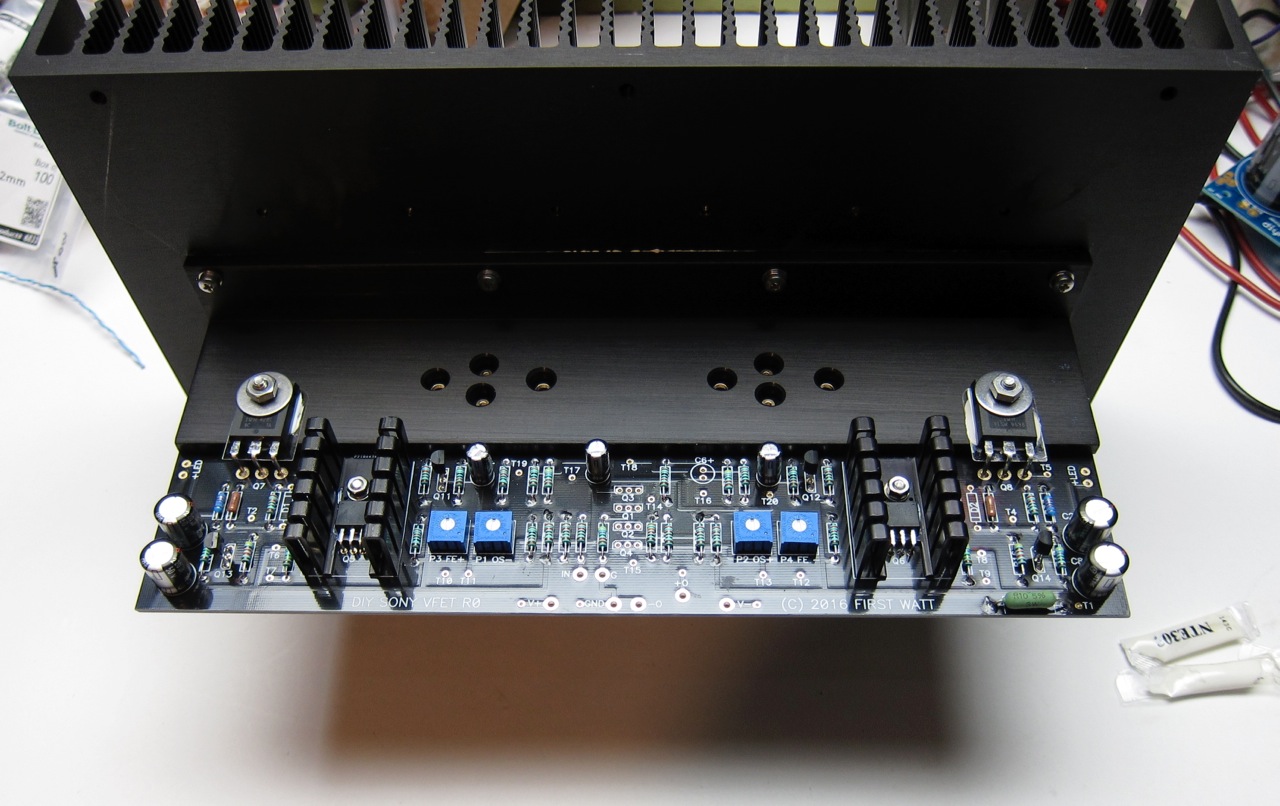
Attach both devices
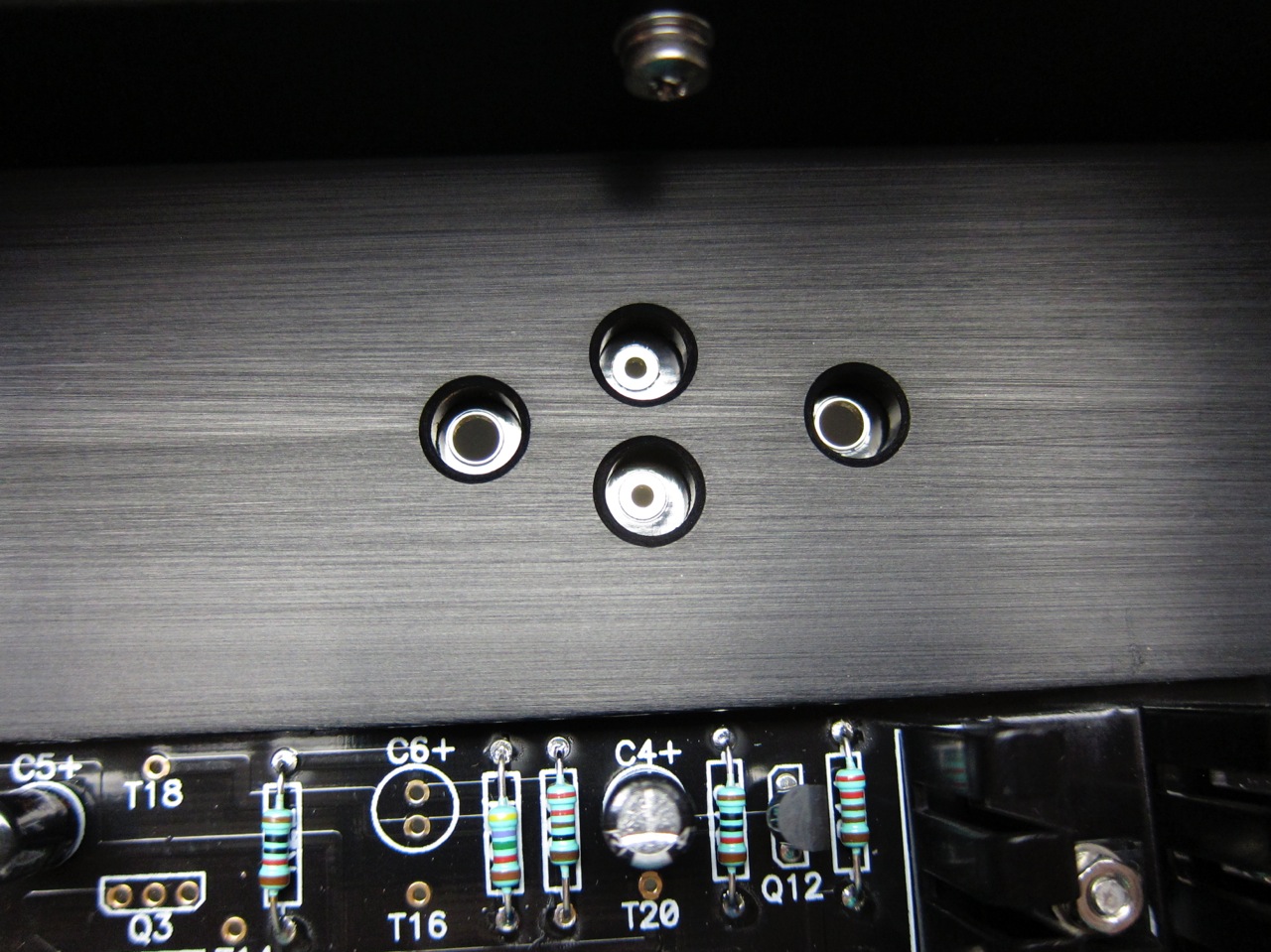
And verify that the holes for the TO-3 Vfets align in the bracket properly.
If so, now you can tighten the power Mosfet screws, and solder the pins to the PCB.
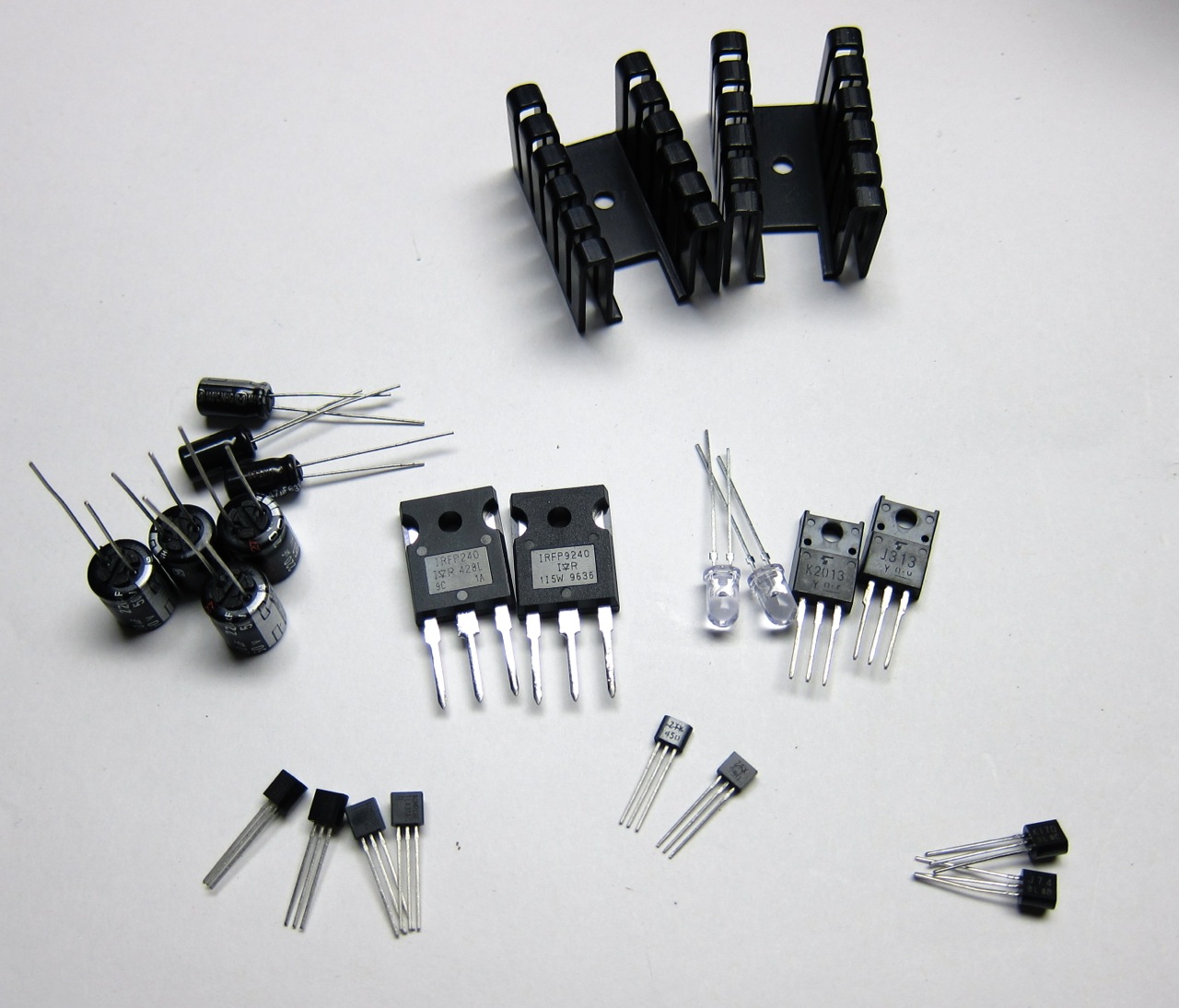
At this point all this should be stuffed on the PCB.
Last edited by a moderator:
Excellent guide! I'm especially impressed with your photos. Did you use only 1 soft box overhead?
Great work!!!
Now I'm getting really excited to receive my supplemental kit!
Great work!!!
Now I'm getting really excited to receive my supplemental kit!
*****Sneak preview, not even close to complete yet


Highly stimulate


That is an awesome writeup!
Wonder if anything is being done to the insanely big holes in the aluminum bracket?
They decrease thermal conductivity pretty much I would think.
I will anyway get another pair of PCBs, so if the brackets are improved I might as well get 2 pairs of those.
Wonder if anything is being done to the insanely big holes in the aluminum bracket?
They decrease thermal conductivity pretty much I would think.
I will anyway get another pair of PCBs, so if the brackets are improved I might as well get 2 pairs of those.
Chassis
At last doing the V2.
From reading the entire thread, I think I understand that the DeLuxe 4U is sufficient with regard to heatsinking. Both for the single and dual pair VFET. Correct?
What is the experiences with regard to space inside? It seems to also be sufficient. But if you load it up with protection circuitry, remote power on and other fancy/necessary stuff, is it still room there to change the belt for the overhead camshaft etc? 😀
/RK
At last doing the V2.
From reading the entire thread, I think I understand that the DeLuxe 4U is sufficient with regard to heatsinking. Both for the single and dual pair VFET. Correct?
What is the experiences with regard to space inside? It seems to also be sufficient. But if you load it up with protection circuitry, remote power on and other fancy/necessary stuff, is it still room there to change the belt for the overhead camshaft etc? 😀
/RK
Hi R-KAt last doing the V2.
From reading the entire thread, I think I understand that the DeLuxe 4U is sufficient with regard to heatsinking. Both for the single and dual pair VFET. Correct?
What is the experiences with regard to space inside? It seems to also be sufficient. But if you load it up with protection circuitry, remote power on and other fancy/necessary stuff, is it still room there to change the belt for the overhead camshaft etc? 😀
/RK
If heat sinks are sufficient but you need more space try psu toroid on L bracket like show by 6L6 on his build guide.
Best regards 🙂
Attachments
- Home
- Amplifiers
- Pass Labs
- Sony vFET Amplifier Part 2