Hello everyone! I've been planning a dedicated 2-channel audio system, I've been gathering components and planning, getting back into speaker building after 15 years. I'm in that "obsessive, all you can think about, walking around Home Depot wanting to make subwoofers out of flower pots, sewer pipe and laminated shelving" sort of mental state, so bear with me as I have a lot of thoughts and they're starting to settle in a somewhat organized manner
Background
Sort of like an addict who doesn't want to tempt their sobriety with one small drink, I have stayed out of Audio for the better part of 15 years. I'm not the kind of person to dabble a little in anything when I do, so it was really for the best as I've been extremely busy growing a company and family during that time.
However this past Christmas I decided to get a new TV, a 70 inch for our "living" room, and that act lubricated what was once a flat, slope-less hobby that I had in audio. Now with this nice new big TV, why not get a $500 home theater amp and hook up the pre-installed in-wall speakers and a set of 2-way Vifa bookshelf speakers I had in storage (with a corresponding Vifa 8" dual voice coil subwoofer). So I picked up a $600 Onkyo receiver on sale after Christmas and got things hooked up. Big mistake, pretty soon the wheels started turning and the rationalizations began breaking through my resolve like a crumbling, eroding dam.
"You know, it could use more bass, why don't you buy a pre-fab sub box and put something bigger in", and "while you're at it the front channel would sound so much better running off that old Adcom GFA-545II you have in storage but this pesky Onkyo doesn't have any audio outputs"...one thing lead to another and pretty soon once I was on Parts Express, Madisound and some other old sites I used to frequent, the poor villagers 15 miles down the valley never knew what hit them.
I'll save you the additional neurotic and gory details between then and what is now a pretty firmed up Speaker Building project, so here we go!
Overall Concept
I don't think I would call myself a true audiophile (simple because I know what that is), I'm not sure what I am is called but best I could summarize it would be that I like speakers that are loud, clear, detailed and distortion free. Though I can certainly appreciate the artfully built and tuned full range or book shelf system, I just need and want more if it was really an option.
I've build my fair share of passive crossover networks over the years but I've decided to take advantage of all technology has brought us since the 90's and go fully digital with a miniDSP 4x10. Part of the fun of this 2 channel system will be tweaking and tuning it, and a DSP based system like this will give me all the tweaking my heart could ever desire. In addition I have a collection of Adcom components that I'd like to put to good use.
After considering a nauseating # of speaker configurations and options over the past month, I finally arrived at a 4-way system consisting of two "towers" with separate tweeter, midrange, mid-bass and sub-bass sections. Again, loud, clear, detailed, powerful, that is the goal (OH yes, and well, I am married with 4-kids under 10yrs old, so they'll need to be relatively compact considering).
A final reality - previous to this I have no woodworking shop, I barely have had a set of screw drivers at home despite owing a company that has extensive metal fabrication, manufacturing and engineering resources. However I wanted to use this opportunity to build up a collection of tools (router, saber saw, sanders, circular saw, etc) but decided early on that a table say wouldn't be in the mix at this time.
Electronic Componentry
As stated earlier I have a bunch of Adcom components and will be acquiring a mini DSP to bring it all together.
Adcom Components
- GFA-545II - 150w x 2 in 4ohms - Mid-bass Section
- GFA-555 - 325w x 2 in 4ohms - Subwoofer Section
- GFA-2535 - 90w x 4 in 4ohms - Midrange and Tweeter Section
- GFP-565 - Preamp
- GCD-600 - 5-disc CD Changer
miniDSP 4x10 - 2 analog RCA inputs and 4 out, all the bells and whistles to equalize and cross over the speaker system.
An externally hosted image should be here but it was not working when we last tested it.
Background
Sort of like an addict who doesn't want to tempt their sobriety with one small drink, I have stayed out of Audio for the better part of 15 years. I'm not the kind of person to dabble a little in anything when I do, so it was really for the best as I've been extremely busy growing a company and family during that time.
However this past Christmas I decided to get a new TV, a 70 inch for our "living" room, and that act lubricated what was once a flat, slope-less hobby that I had in audio. Now with this nice new big TV, why not get a $500 home theater amp and hook up the pre-installed in-wall speakers and a set of 2-way Vifa bookshelf speakers I had in storage (with a corresponding Vifa 8" dual voice coil subwoofer). So I picked up a $600 Onkyo receiver on sale after Christmas and got things hooked up. Big mistake, pretty soon the wheels started turning and the rationalizations began breaking through my resolve like a crumbling, eroding dam.
"You know, it could use more bass, why don't you buy a pre-fab sub box and put something bigger in", and "while you're at it the front channel would sound so much better running off that old Adcom GFA-545II you have in storage but this pesky Onkyo doesn't have any audio outputs"...one thing lead to another and pretty soon once I was on Parts Express, Madisound and some other old sites I used to frequent, the poor villagers 15 miles down the valley never knew what hit them.
I'll save you the additional neurotic and gory details between then and what is now a pretty firmed up Speaker Building project, so here we go!
Overall Concept
I don't think I would call myself a true audiophile (simple because I know what that is), I'm not sure what I am is called but best I could summarize it would be that I like speakers that are loud, clear, detailed and distortion free. Though I can certainly appreciate the artfully built and tuned full range or book shelf system, I just need and want more if it was really an option.
I've build my fair share of passive crossover networks over the years but I've decided to take advantage of all technology has brought us since the 90's and go fully digital with a miniDSP 4x10. Part of the fun of this 2 channel system will be tweaking and tuning it, and a DSP based system like this will give me all the tweaking my heart could ever desire. In addition I have a collection of Adcom components that I'd like to put to good use.
After considering a nauseating # of speaker configurations and options over the past month, I finally arrived at a 4-way system consisting of two "towers" with separate tweeter, midrange, mid-bass and sub-bass sections. Again, loud, clear, detailed, powerful, that is the goal (OH yes, and well, I am married with 4-kids under 10yrs old, so they'll need to be relatively compact considering).
A final reality - previous to this I have no woodworking shop, I barely have had a set of screw drivers at home despite owing a company that has extensive metal fabrication, manufacturing and engineering resources. However I wanted to use this opportunity to build up a collection of tools (router, saber saw, sanders, circular saw, etc) but decided early on that a table say wouldn't be in the mix at this time.
Electronic Componentry
As stated earlier I have a bunch of Adcom components and will be acquiring a mini DSP to bring it all together.
Adcom Components
- GFA-545II - 150w x 2 in 4ohms - Mid-bass Section
- GFA-555 - 325w x 2 in 4ohms - Subwoofer Section
- GFA-2535 - 90w x 4 in 4ohms - Midrange and Tweeter Section
- GFP-565 - Preamp
- GCD-600 - 5-disc CD Changer
miniDSP 4x10 - 2 analog RCA inputs and 4 out, all the bells and whistles to equalize and cross over the speaker system.
Last edited:
The RS4 Speakers
I'm going to dub these speakers the RS4s, apparently Infinity has a discontinued speaker called the RS-4, oh well I've got a good lawyer, gonna roll the dice
RS4 hearkens to two things, the first is that I'll be using mostly Dayton Reference Series drivers and it's a 4-way system, the second is that I am an Audi tuner by trade and the RS line of vehicles represent dynamically precisely what I'd like to achieve with these speakers acoustically.
The components I've chosen were based on many reviews and research I did, as well as considering this is my first set of speakers in 15 years, you gotta start somewhere right?
I don't know what these are technically classified as, but they are basically an MTM with an added mid-bass 8" and a 10" subwoofer. Since I talked the wife into giving me the Dining Room I realized the potential to make something bigger and not limited size wise, so at that point I stopped planning a separate subwoofer and decided to integrate the sub-bass into the towers.
Tweeter
XT25TG30-04

I am a die hard Vifa fan from way back, obviously they've gone through some changes but I at least really wanted to try the newer tweeters they came out with. I chose these for a few reasons:
- Visually they match the rest of the RS drivers with their phase plug (I know...)
- They are 4ohms and have very high power handling, I want these to get loud and am really hoping these tweeters keep up. I was seriously considering two 8ohm tweeters in parallel but after researching the lobing issues, decided against it.
- Very well rated and used in some very high end commercial speakers
Crossover will start in the 3500kHz range
Midrange
RS100-8

Since I was committed to the RS line so it was a matter of picking one of the options, I wanted to spread the audio load over multiple drivers whenever possible and the midrange posed the best opportunity. Was interested in the RS52 and will try them for a future project. The RS100 were very well rated, had the right power handling, impedance, etc. I was also intrigued with playing these drivers high frequency capabilities given the digital setup I'd have, will be fun to experiment bringing these in with the tweeter as well as seeing how they sound w/o it.
These will have about .08 ft3 of space, I'm considering crossing them over in the 400-3500 range.
Mid-Bass
RS225-4

Something I really appreciate in a speaker is punchy mid-bass in that 100-300Hz range, I toyed with the idea of doing multiple 6.5" options per cabinet (was very intrigued with the Tang Bang 6.5" W6 at one point) but ultimately decided one 8" per cabinet would do nicely. This is obviously a very well rated woofer and I'm looking forward to using it.
This will live in about .45 ft3, sealed, cross over in the 150-400 range.
Subwoofer
RSS265HF-4

This driver was the most excruciating to make a decision on. The ride you go on when choosing a subwoofer driver isn't one you are in control of, you are simply along for the ride as your brain is tortured with a decision that really cannot ever be made, the decision simply wears you down until your spirit is broken.
The RSS265HF ultimately met all the criteria including DNA, price and rating. I went back and forth a lot on enclosure style and ultimately decided that for simplicity and space sake, I'd stick to a sealed enclosure. Also with the very powerful DSP and amplification I had available, I figured I could make up for any loss of low end easily. Also this isn't an HT setup so really I'm looking for fast, precise and powerful bass, not looking to simulate death star explosions, more the resonant impact of Sting's bass string.
I am a tech geek and I love the look of a cast basket subwoofer so I am strongly considering mounting these magnet out, more details below, still not 100%, will see what it looks like as things get further with the enclosure. I'm excited by the potential mix of industrial and finely crafted wood look, we'll see.
This driver will get about .8 ft3 and play between about 25-150Hz
More about the enclosure below..
I'm going to dub these speakers the RS4s, apparently Infinity has a discontinued speaker called the RS-4, oh well I've got a good lawyer, gonna roll the dice
An externally hosted image should be here but it was not working when we last tested it.
RS4 hearkens to two things, the first is that I'll be using mostly Dayton Reference Series drivers and it's a 4-way system, the second is that I am an Audi tuner by trade and the RS line of vehicles represent dynamically precisely what I'd like to achieve with these speakers acoustically.
The components I've chosen were based on many reviews and research I did, as well as considering this is my first set of speakers in 15 years, you gotta start somewhere right?
I don't know what these are technically classified as, but they are basically an MTM with an added mid-bass 8" and a 10" subwoofer. Since I talked the wife into giving me the Dining Room I realized the potential to make something bigger and not limited size wise, so at that point I stopped planning a separate subwoofer and decided to integrate the sub-bass into the towers.
Tweeter
XT25TG30-04
I am a die hard Vifa fan from way back, obviously they've gone through some changes but I at least really wanted to try the newer tweeters they came out with. I chose these for a few reasons:
- Visually they match the rest of the RS drivers with their phase plug (I know...)
- They are 4ohms and have very high power handling, I want these to get loud and am really hoping these tweeters keep up. I was seriously considering two 8ohm tweeters in parallel but after researching the lobing issues, decided against it.
- Very well rated and used in some very high end commercial speakers
Crossover will start in the 3500kHz range
Midrange
RS100-8
Since I was committed to the RS line so it was a matter of picking one of the options, I wanted to spread the audio load over multiple drivers whenever possible and the midrange posed the best opportunity. Was interested in the RS52 and will try them for a future project. The RS100 were very well rated, had the right power handling, impedance, etc. I was also intrigued with playing these drivers high frequency capabilities given the digital setup I'd have, will be fun to experiment bringing these in with the tweeter as well as seeing how they sound w/o it.
These will have about .08 ft3 of space, I'm considering crossing them over in the 400-3500 range.
Mid-Bass
RS225-4
Something I really appreciate in a speaker is punchy mid-bass in that 100-300Hz range, I toyed with the idea of doing multiple 6.5" options per cabinet (was very intrigued with the Tang Bang 6.5" W6 at one point) but ultimately decided one 8" per cabinet would do nicely. This is obviously a very well rated woofer and I'm looking forward to using it.
This will live in about .45 ft3, sealed, cross over in the 150-400 range.
Subwoofer
RSS265HF-4
This driver was the most excruciating to make a decision on. The ride you go on when choosing a subwoofer driver isn't one you are in control of, you are simply along for the ride as your brain is tortured with a decision that really cannot ever be made, the decision simply wears you down until your spirit is broken.
An externally hosted image should be here but it was not working when we last tested it.
The RSS265HF ultimately met all the criteria including DNA, price and rating. I went back and forth a lot on enclosure style and ultimately decided that for simplicity and space sake, I'd stick to a sealed enclosure. Also with the very powerful DSP and amplification I had available, I figured I could make up for any loss of low end easily. Also this isn't an HT setup so really I'm looking for fast, precise and powerful bass, not looking to simulate death star explosions, more the resonant impact of Sting's bass string.
I am a tech geek and I love the look of a cast basket subwoofer so I am strongly considering mounting these magnet out, more details below, still not 100%, will see what it looks like as things get further with the enclosure. I'm excited by the potential mix of industrial and finely crafted wood look, we'll see.
This driver will get about .8 ft3 and play between about 25-150Hz
More about the enclosure below..
The Enclosures
I just started making saw dust today so I'm very excited that these are coming along! However it was a good month of thinking and planning before I felt comfortable moving forward with them.
As stated in the intro, I didn't have much in the way of tools at my house so that initially led me on the path I'm on. A few other things influenced me as well, one is that we use a lot of 3D printing tech at my company and it gave me an idea which turns out isn't very original - Laminated Construction. I was all excited that I'd thought of something original but Google snapped me back to reality, like they say "every idea under the Sun". Many use transverse lamination but I decided on Longitudinal simply due to the fewer pieces I'd have to construct.
The main thing that drove me to this construction technique, for one, is my unique hallmark desire to be different (
Tools
Some tools I've acquired over the past month:
-Bosch Jig/Saber saw
-Makita Circular Saw
-Makita 1/2" chuck cordless drill
-Bosch 16/17 plunge router
-Dewalt variable speed orbital sander
-Bora Clamp edge (this thing is amazing!)

-Some Saw Horses for a makeshift work bench
-Assortment of bar clamps
-Assortment of router bits, circle jig, router guide, etc.
-Bunch of other drill bits and wood working hand tools that I'll likely need.
Planning
Back in the late 90's I was what most would consider a very good wood worker, but after a 15-year hiatus I was feeling a little nervous especially with the resources at hand. My current "work shop" is on the side of the house and with the rain I have to break it down every night, but so far so good.
In the spirit of keeping things simpler (as several other aspects of this project were clustering out of control by many standards) I decided to plan these the old fashioned way and use some pencil and graph paper.
Basic quick sketch of internal volumes, I've modified this since but it gives you an idea of the layout I chose for drivers.
Front and side view of the speakers, side view shows the reduced size of mid/tweeter section of the enclosure, both views show the side firing subwoofer (which may get mounted inside out).
Some more sketching just trying to wrap my brain around what I'd end up needing for lamination layers to create the shape and volume I was looking for.
Long. Lam Construction
What I'll end up with is 14 layers in each enclosure:
- 4 inner panels that will create the very center of the enclosure as well as the volume for the mid/tweeter section. ID of this enclosure will be .75x 4 or 3"
- 2 outer/inner panels to create the sides of the mid/tweeter section as well as additional inner layers for the lower part of the enclosure.
- 4 inner/lower panels that will add more space for the lower part of the woofer/sub enclosure.
- 4 outer/lower panels that will cap the woofer/sub enclosure and create a 1.5" wall thickness for the outside.
All enclosures will have 1.5" wall thickness except for the mid/tweeter section which will have 1.5" wall top, back and bottom, but .75 on the sides.
I will play around with bracing as I get more into it, either incorporating it into the layers, or adding additional 1" dowels that will be glued in from side to side and capped underneath the outer layer so they won't be visible.
Of the two different inner and outer panels, the first one of each that I create will act as the pattern for additional units and layers. That way every layer is the same and I don't have to worry about not having a table say to make accurate cuts with. My plan is to create the first inner piece, then glue additional oversized panes to that and flush router each additional layer that is added and work from the inside out.
All in all I'll need almost 5 full sheets of plywood, I have chosen Maple as it was the only option at Home Depot that was actually .75" thick, and I need all the thickness I can get for this!
Speaker Baffle
Partially for visual appeal, but also partially for ease of driver mounting, I will be mounting all mid/tweeter/woofer to a structural as well as decorative baffle, this way I can just router out over-sized holes in the front of the long. Lam cabinet and attach this baffle to the front of that.
Started cutting wood, more to come!
I just started making saw dust today so I'm very excited that these are coming along! However it was a good month of thinking and planning before I felt comfortable moving forward with them.
As stated in the intro, I didn't have much in the way of tools at my house so that initially led me on the path I'm on. A few other things influenced me as well, one is that we use a lot of 3D printing tech at my company and it gave me an idea which turns out isn't very original - Laminated Construction. I was all excited that I'd thought of something original but Google snapped me back to reality, like they say "every idea under the Sun". Many use transverse lamination but I decided on Longitudinal simply due to the fewer pieces I'd have to construct.
The main thing that drove me to this construction technique, for one, is my unique hallmark desire to be different (
An externally hosted image should be here but it was not working when we last tested it.
) but also since I had decided that I wasn't going to use a table saw to build these, this construction technique lended itself well to using a router to create accurate final shapes.Tools
Some tools I've acquired over the past month:
-Bosch Jig/Saber saw
-Makita Circular Saw
-Makita 1/2" chuck cordless drill
-Bosch 16/17 plunge router
-Dewalt variable speed orbital sander
-Bora Clamp edge (this thing is amazing!)
-Some Saw Horses for a makeshift work bench
-Assortment of bar clamps
-Assortment of router bits, circle jig, router guide, etc.
-Bunch of other drill bits and wood working hand tools that I'll likely need.
Planning
Back in the late 90's I was what most would consider a very good wood worker, but after a 15-year hiatus I was feeling a little nervous especially with the resources at hand. My current "work shop" is on the side of the house and with the rain I have to break it down every night, but so far so good.
In the spirit of keeping things simpler (as several other aspects of this project were clustering out of control by many standards) I decided to plan these the old fashioned way and use some pencil and graph paper.
Basic quick sketch of internal volumes, I've modified this since but it gives you an idea of the layout I chose for drivers.
Front and side view of the speakers, side view shows the reduced size of mid/tweeter section of the enclosure, both views show the side firing subwoofer (which may get mounted inside out).
Some more sketching just trying to wrap my brain around what I'd end up needing for lamination layers to create the shape and volume I was looking for.
Long. Lam Construction
What I'll end up with is 14 layers in each enclosure:
- 4 inner panels that will create the very center of the enclosure as well as the volume for the mid/tweeter section. ID of this enclosure will be .75x 4 or 3"
- 2 outer/inner panels to create the sides of the mid/tweeter section as well as additional inner layers for the lower part of the enclosure.
- 4 inner/lower panels that will add more space for the lower part of the woofer/sub enclosure.
- 4 outer/lower panels that will cap the woofer/sub enclosure and create a 1.5" wall thickness for the outside.
All enclosures will have 1.5" wall thickness except for the mid/tweeter section which will have 1.5" wall top, back and bottom, but .75 on the sides.
I will play around with bracing as I get more into it, either incorporating it into the layers, or adding additional 1" dowels that will be glued in from side to side and capped underneath the outer layer so they won't be visible.
Of the two different inner and outer panels, the first one of each that I create will act as the pattern for additional units and layers. That way every layer is the same and I don't have to worry about not having a table say to make accurate cuts with. My plan is to create the first inner piece, then glue additional oversized panes to that and flush router each additional layer that is added and work from the inside out.
All in all I'll need almost 5 full sheets of plywood, I have chosen Maple as it was the only option at Home Depot that was actually .75" thick, and I need all the thickness I can get for this!
Speaker Baffle
Partially for visual appeal, but also partially for ease of driver mounting, I will be mounting all mid/tweeter/woofer to a structural as well as decorative baffle, this way I can just router out over-sized holes in the front of the long. Lam cabinet and attach this baffle to the front of that.
Started cutting wood, more to come!
Last edited:
Time to start cutting wood! Today I loaded up the minivan with 5 sheets of .75" thick maple plywood and rough cut them into ~16" wide pieces that were the full 48" long.
Then I started working on getting my first inner center panel laid out to see what it would look like. After I got it all traced on the first sheet I started squaring up the panel with the Bora clamp edge and circular saw. I picked up high tooth count, fine finish 7.25" blade and was really happy how it cut through the plywood and didn't chew up the edge (which I was really worried about).
The Bora edge is a life saver! I doesn't square itself up but you clamp it down along a line or measurement you take and it won't budge from there. The distance from my circular saw blade to the edge of it's base is 1.4" so it was just a matter of setting the Bora edge that distance from the actual cut I wanted to make
Getting the dimensions laid out on the first piece.
And after a few hours of work I was left with this progress which I'm very proud of!
Tomorrow I have planned to cut out the initial enclosure cavity provisions and use that piece as a template, more to come!
Then I started working on getting my first inner center panel laid out to see what it would look like. After I got it all traced on the first sheet I started squaring up the panel with the Bora clamp edge and circular saw. I picked up high tooth count, fine finish 7.25" blade and was really happy how it cut through the plywood and didn't chew up the edge (which I was really worried about).
The Bora edge is a life saver! I doesn't square itself up but you clamp it down along a line or measurement you take and it won't budge from there. The distance from my circular saw blade to the edge of it's base is 1.4" so it was just a matter of setting the Bora edge that distance from the actual cut I wanted to make
Getting the dimensions laid out on the first piece.
And after a few hours of work I was left with this progress which I'm very proud of!
Tomorrow I have planned to cut out the initial enclosure cavity provisions and use that piece as a template, more to come!
Last edited:
Very nice!
I just spent an hour cutting tweeter flanges into panels in my closet. I had forgotten how much sawdust a router can make in an instant. I envy your space to work in.
What about the room? Bass traps? Diffusers? Absorbers? Should be at least 25% of your spend in the room compared to speakers. Otherwise there's not much of a point in adding a lot of inches and watts.
Best,
Erik
I just spent an hour cutting tweeter flanges into panels in my closet. I had forgotten how much sawdust a router can make in an instant. I envy your space to work in.
What about the room? Bass traps? Diffusers? Absorbers? Should be at least 25% of your spend in the room compared to speakers. Otherwise there's not much of a point in adding a lot of inches and watts.
Best,
Erik
Thanks Erik! Yes very good point about the room, will address that as a sequential project once I have all the heavy lifting done on the base system, looking forward to tweaking and tuning!
Sent from my iPhone using Tapatalk
Sent from my iPhone using Tapatalk
Thanks Erik! Yes very good point about the room, will address that as a sequential project once I have all the heavy lifting done on the base system, looking forward to tweaking and tuning!
Sent from my iPhone using Tapatalk
I like products from GIK Acoustics. Great price/performance and attractive too. My only worry was for you not to spend all your budget on your speakers/electronics. If you are one of the "This Old Mansion" types, then that's not an issue. 🙂
Also though, your priorities change. Good acoustics make such a difference in bass performance that those of us on budgets may no longer see having 4 x 15" subs as needed. 🙂
Good luck, let us see how your work progresses.
Best,
Erik
Had a productive day today and things are starting to come together in wood
Where I left off yesterday was the last picture, I was about half done with the first layer and ultimate template for every other layer. The outside of the template came out how I wanted it to, using the edge guide and some careful circular saw work I was able to get nice straight cuts, didn't splinter the plywood at all (got a really nice fine finish blade, the edge doesn't even need sanding after the cut), etc. The inside would be trickier but at the same time not quite as important to get perfect visually.
I marked out the inner walls to match the volumes I had calculated, I also put a 3/8" radius in each corner too as a router bearing wouldn't get into a tight 90d corner.
Next I used a 3/4" spade bit and put a hole in each corner, I drilled half way on each side to prevent exit splintering
Now it was just a matter of cutting straight lines to connect the holes, initially I was going to use the router with a spiral cutter in it along the edge guide but decided on the saber saw, this technique worked well and allowed me to hold the 1.5" wall thickness well
On the cross cuts I couldn't use that saw guide so I just ran the saber saw down the edge guide.
Once I cut out all the panels, I sanded everything down and was left with this, the first center piece of the first enclosure and the pattern for all 27 other pieces
Using this piece I could now start patterning other pieces with the router, this beastly Freud bit has worked wonderfully making the smoothest, cleanest cuts, very pleased with it! As a bonus it would work well to protect during an enemy invasion or zombie apocalypse.
cont...
An externally hosted image should be here but it was not working when we last tested it.
Where I left off yesterday was the last picture, I was about half done with the first layer and ultimate template for every other layer. The outside of the template came out how I wanted it to, using the edge guide and some careful circular saw work I was able to get nice straight cuts, didn't splinter the plywood at all (got a really nice fine finish blade, the edge doesn't even need sanding after the cut), etc. The inside would be trickier but at the same time not quite as important to get perfect visually.
I marked out the inner walls to match the volumes I had calculated, I also put a 3/8" radius in each corner too as a router bearing wouldn't get into a tight 90d corner.
Next I used a 3/4" spade bit and put a hole in each corner, I drilled half way on each side to prevent exit splintering
Now it was just a matter of cutting straight lines to connect the holes, initially I was going to use the router with a spiral cutter in it along the edge guide but decided on the saber saw, this technique worked well and allowed me to hold the 1.5" wall thickness well
On the cross cuts I couldn't use that saw guide so I just ran the saber saw down the edge guide.
Once I cut out all the panels, I sanded everything down and was left with this, the first center piece of the first enclosure and the pattern for all 27 other pieces
Using this piece I could now start patterning other pieces with the router, this beastly Freud bit has worked wonderfully making the smoothest, cleanest cuts, very pleased with it! As a bonus it would work well to protect during an enemy invasion or zombie apocalypse.
cont...
In order to limit router dust I rough cut the second piece with the saber saw, this is a quick step and leaves about 1/4" for the router bit to deal with. After a bunch of dust (kids pretended it was snowing outside...), I was left with two virtually identical pieces, the center of each enclosure
Next step was to glue a sheet to each template, rough cut it with the jig saw, router it and have the first two layers attached and ready for the 3rd, etc.
After glue dried and routered, a seamless laminated layer.
And onto the 3rd layer which is now glued and drying and tomorrow (if I can get home early enough), will router both sides of the 3rd layer.
The box has the mid/tweet section and then the outside section which is the lower larger width section which houses the subwoofer and midbass. The mid/tweet enclosure is made up of 4 center layers, then one layer on each side of that to seal up the mid/tweet enclosure, then 4 lower panels go on each side of that giving a final total width of 10.5".
I'm still pondering what I want to do for finished edges, currently contemplating either a 3/4" round over or 45 degree bevel, we'll see, if I want to do anything with the back curved section I need to router it before I add any additional layers onto that. So that's that, more to come!
Next step was to glue a sheet to each template, rough cut it with the jig saw, router it and have the first two layers attached and ready for the 3rd, etc.
After glue dried and routered, a seamless laminated layer.
And onto the 3rd layer which is now glued and drying and tomorrow (if I can get home early enough), will router both sides of the 3rd layer.
The box has the mid/tweet section and then the outside section which is the lower larger width section which houses the subwoofer and midbass. The mid/tweet enclosure is made up of 4 center layers, then one layer on each side of that to seal up the mid/tweet enclosure, then 4 lower panels go on each side of that giving a final total width of 10.5".
I'm still pondering what I want to do for finished edges, currently contemplating either a 3/4" round over or 45 degree bevel, we'll see, if I want to do anything with the back curved section I need to router it before I add any additional layers onto that. So that's that, more to come!
Got some more work done tonight (in case anyone is still following
)
So I ended yesterday with a 3rd layer laminated on, this layer will essentially be the center of the enclosure (even number of layers so it will be just to the side of dead center. I wanted to use this layer for bracing front to back, and I'll finish with some wooden dowels that go through the braces and glue to them side to side.
Here is what I started with, drilling holes that will make up the corners of the braces
From the other side
Then using a jig saw I made straight cuts, for other parts that lined up with the layer below, a flush cut router but would suffice.
And routering things out
The finished product
Both sides done, next up layer 4,5,6 and the center enclosure will be finished

So I ended yesterday with a 3rd layer laminated on, this layer will essentially be the center of the enclosure (even number of layers so it will be just to the side of dead center. I wanted to use this layer for bracing front to back, and I'll finish with some wooden dowels that go through the braces and glue to them side to side.
Here is what I started with, drilling holes that will make up the corners of the braces

From the other side

Then using a jig saw I made straight cuts, for other parts that lined up with the layer below, a flush cut router but would suffice.

And routering things out

The finished product

Both sides done, next up layer 4,5,6 and the center enclosure will be finished

Looks very cool, you'll have months (maybe years) of fun twiddling with the DSP. Active is awesome 🙂
Looks very cool, you'll have months (maybe years) of fun twiddling with the DSP. Active is awesome 🙂
Thanks, I can't wait to get started =)
Got some more work done today! Things are really coming together
Starting where I left off, the last layer was the brace layer, which meant the next layer wouldn't have braces so I have to do things a little differently than just gluing and routering the next layer.
So I attached the next layer with screws, did all the routering I could, then separated them, finished the cuts with a jog saw and then glued.
Here holes are drilled to give access to the flush cut bit
Making cuts where the braces are
Gluing up
And that layer is done, ready for the next one!
Next the capping layers went on each side for the mid/tweet enclosure,finally less routering needed little by little
Once those were done then the lower midbass/subwoofer enclosure continued with shorter pieces.
The first piece on each side required a perfectly straight finished edge since it was up against the center of the enclosure, which I accomplished with the edge clamp and flush cut router bit
Gluing up
Where things left off
And some silver stain I'm considering, thinking this with the front baffle in black, not crazy about it with just stain but was going to throw some clear on it to see what it looks like, thoughts welcome!
More tomorrow!

Starting where I left off, the last layer was the brace layer, which meant the next layer wouldn't have braces so I have to do things a little differently than just gluing and routering the next layer.
So I attached the next layer with screws, did all the routering I could, then separated them, finished the cuts with a jog saw and then glued.
Here holes are drilled to give access to the flush cut bit


Making cuts where the braces are

Gluing up

And that layer is done, ready for the next one!

Next the capping layers went on each side for the mid/tweet enclosure,finally less routering needed little by little


Once those were done then the lower midbass/subwoofer enclosure continued with shorter pieces.
The first piece on each side required a perfectly straight finished edge since it was up against the center of the enclosure, which I accomplished with the edge clamp and flush cut router bit

Gluing up

Where things left off


And some silver stain I'm considering, thinking this with the front baffle in black, not crazy about it with just stain but was going to throw some clear on it to see what it looks like, thoughts welcome!

More tomorrow!
I'm using this for coloring (ral 9005 jet black version):
HOUTBEITS
And this for varnish:
VERNITHANE GLANZEND
Finished it looks like this:
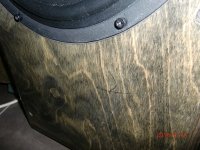
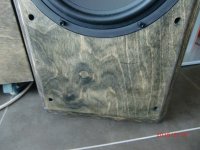
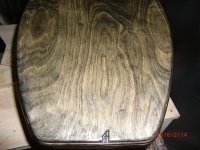
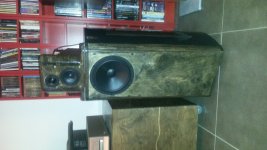
It's polished to a mirror finish, but that is very difficult to get on camera
HOUTBEITS
And this for varnish:
VERNITHANE GLANZEND
Finished it looks like this:
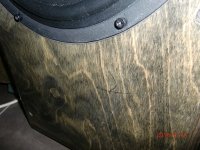
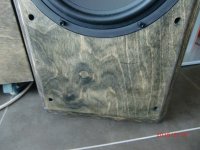
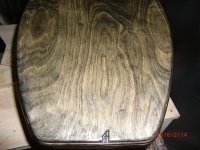
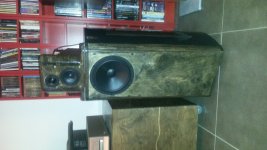
It's polished to a mirror finish, but that is very difficult to get on camera
Attachments
Thanks that looks nice, I am also considering some "black" Minwax stain as well, and will do a clear lacquer finish with sanding between coats, still need to do some more tests to see what I like. [emoji4]
Sent from my iPhone using Tapatalk
Sent from my iPhone using Tapatalk
I wetsand with 600Gritt between varnish layers. Don't put any detergent in the water, it makes the sanding go easier but leaves a film which messes up the bonding between layers (I found out the hard way). A bit of detergent in the water is very good to use for the final polishing (600-800-1200-2000 gritt)
The varnish I'm using (and most clear ones) dry very slowly. Full curing time is 1 week, sanding and putting on another layer is fine every 24 hours but don't put any masking tape on a varnished piece before 1 full week of drying (needs light to cure too) or you run the risk of pulling a layer off (also found out the hard way...)
The varnish I'm using (and most clear ones) dry very slowly. Full curing time is 1 week, sanding and putting on another layer is fine every 24 hours but don't put any masking tape on a varnished piece before 1 full week of drying (needs light to cure too) or you run the risk of pulling a layer off (also found out the hard way...)
Last edited:
Yea I've only ever used water but it's been a while, saw online that some people added soap but made me wonder about that hurting bonding. Not sure how much final polishing I'll do, mainly looking to have a smooth and uniform semigloss coating - but I have a ways to go for that [emoji1362]
Sent from my iPhone using Tapatalk
Sent from my iPhone using Tapatalk
More progress today, have all panels glued and laminated, just 4 more routering sessions and I'm done with the messy part
Added the final layer of the open enclosure layers, all routered and waiting for 2 more panels on each side to make up the 1.5" wall of the outside of the enclosure.
You can see how the bracing came out as well.
Some detail of the inside
Lots of layers!
First solid layer clamped up
Last layer getting glued, I spread out glue then added more beads just to ensure plenty of adhesion
I used small finish nails to position the final outside layer just so it wouldn't slide around during clamping, I removed these and filled with wood filler.
Will finish up the final construction tomorrow and post tomorrow, any comments or observations are welcome!

Added the final layer of the open enclosure layers, all routered and waiting for 2 more panels on each side to make up the 1.5" wall of the outside of the enclosure.
You can see how the bracing came out as well.

Some detail of the inside

Lots of layers!

First solid layer clamped up

Last layer getting glued, I spread out glue then added more beads just to ensure plenty of adhesion



I used small finish nails to position the final outside layer just so it wouldn't slide around during clamping, I removed these and filled with wood filler.

Will finish up the final construction tomorrow and post tomorrow, any comments or observations are welcome!

That's a very impressive design - and a whole lot of wood. What did the raw materials weigh? 🙂
I like the RS line of drivers also - wondered if you have considered the paper cone variety RS225P, RS100P, etc. I have the RS100P and RS100 (aluminum) and like the sound of the paper better - less ringing. I also have an aluminum RS225 and had to EQ the resonant peak down - not a big deal with minidsp. Recently just got some RS180P's and really like them too. They measured spot on TS wise with factory numbers and are nearly 90dB sensitive. One thing about 1.5in thick baffles is that you need to heavily undercut the driver holes to allow room to breathe.
I like the RS line of drivers also - wondered if you have considered the paper cone variety RS225P, RS100P, etc. I have the RS100P and RS100 (aluminum) and like the sound of the paper better - less ringing. I also have an aluminum RS225 and had to EQ the resonant peak down - not a big deal with minidsp. Recently just got some RS180P's and really like them too. They measured spot on TS wise with factory numbers and are nearly 90dB sensitive. One thing about 1.5in thick baffles is that you need to heavily undercut the driver holes to allow room to breathe.
I wetsand with 600Gritt between varnish layers. Don't put any detergent in the water, it makes the sanding go easier but leaves a film which messes up the bonding between layers (I found out the hard way). A bit of detergent in the water is very good to use for the final polishing (600-800-1200-2000 gritt)
The varnish I'm using (and most clear ones) dry very slowly. Full curing time is 1 week, sanding and putting on another layer is fine every 24 hours but don't put any masking tape on a varnished piece before 1 full week of drying (needs light to cure too) or you run the risk of pulling a layer off (also found out the hard way...)
Your methods seem close to mine, except I used a PU floor clear coat. I put on 6 layers and polished to a mirror finish...

Was pretty happy with the results, until my enclosure cracked 🙁.
But what else to expect stacking 128 pieces of ply with ridged metal rods.
Anyway it's fixed but different now. I think I must have tried about 8 different recipe's for my stain/clear coat job. Never to be seen again 🙂.
- Status
- Not open for further replies.
- Home
- Loudspeakers
- Multi-Way
- RS4 - Digital 4-way XO, Long. Lam, Dayton Reference, Adcom System