What a concept! I just sent the link to your video to my mentor, who is also extremely knowledgeable about RF and Radar, along with the following remarks:
I wouldn't go so broad as to limit the entire spectrum going into the subs, but rather, I would use swept sine waves and setup multiple parametric compressors, a la the Behringer. The excursion graphs on subs are very linear and go straight up and back down, so one compressor for the leading edge, one for the peak, and one for the trailing edge of the excursion peak should get it right.
I wouldn't go so broad as to limit the entire spectrum going into the subs, but rather, I would use swept sine waves and setup multiple parametric compressors, a la the Behringer. The excursion graphs on subs are very linear and go straight up and back down, so one compressor for the leading edge, one for the peak, and one for the trailing edge of the excursion peak should get it right.
That's an interesting idea. I first thought of a sliding high-pass filter, but banded limiters would be interesting especially when tuned to a particular cab's behavior. A TH for example has a large displacement bump in the passband above the cutoff and completely unloads below it. If you tuned the filters to those ranges, you'd have something nice.
The whole idea is just to prevent audible distortion from the driver traveling too far, so you can operate it under it's passband for low level operation without fear. With your banded idea, you can hit the thresholds much harder without adverse side affects.
The whole idea is just to prevent audible distortion from the driver traveling too far, so you can operate it under it's passband for low level operation without fear. With your banded idea, you can hit the thresholds much harder without adverse side affects.
You know.. a couple of hours after sending that email and making the post.. I was on the interstate and I saw one of those hopped-up trucks on 35" wheels with lifted suspension, it said "Excursion Limited" on the back, as in, Ford Excursion, Limited Edition.. so it got me thinking about this again. Not to demean your work, but the radar is basically irrelevant (yet still very cool!). You haven't demonstrated the ability to measure the excursion in millimeters, but rather, the ability to measure physical artifacts associated with overextruding the cone. I submit that this can and should be measured audibly instead. That's essentially what you're after - detecting audible distortion. I guess in an extreme case, you could brush up on Xlim whilst barely creating any audible artifacts (read: less than 5 or 10% distortion, which is the wideband threshold that I, personally, can detect audible distortion - YMMV). But overall, if your radar can see that distortion, so can a microphone - and I would think that audible distortion is a good indicator as to whether you're asking the transducer to do something that it wasn't designed to do. The question then becomes, how to build a cheap distortion analyzer? Maybe this is better done with software?
You haven't demonstrated the ability to measure the excursion in millimeters
Do your own homework. I was going to explain how to do it, but felt otherwise and deleted it. It doesn't require an interferometer to do it. Why should I explain how?
Wow.. where to begin?
You act as if I don't know the first thing about radar. On the contrary, I was licensed by the FCC at age 10 to run limitless amounts of radiation on point-to-point microwave links within certain pockets of spectrum between 2 and 60 Ghz. That required at least a rudimentary understanding of SHF, and by extension, concepts like radar. But radar, or my knowledge thereof, is completely immaterial.
Getting back to the part where I said "the radar is basically irrelevant", what I was attempting to convey is that I'm not sure we care about Xmax. Distortion metering is the be-all, end-all methodology, IMHO. If we're not approaching the point of cone damage, or thermal damage, then distortion is the only thing left. It would take a sort of "compensating" distortion analyzer, which would be aware of the massive phase shifts and group delays associated with speaker enclosures, but it could definitely be done, and even automated with sine and amplitude sweeps. i.e. "Show me what voltage level at the speaker terminals will produce 10% distortion or less, and draw the distortion graph". Maybe such a thing exists already?
p.s. If you're stuck on this radar thing, a good source of transducers is old microwave-based waveguides used to automatically open the sliding doors at grocery stores. You'll quickly recognize them because the enclosures are rectangular, perhaps 7 inches long or so, as opposed to the modern ones which use infrared and are considerably smaller. But I reeeeally think you're barking up the wrong tree.. 🙂
Do your own homework. I was going to explain how to do it, but felt otherwise and deleted it. It doesn't require an interferometer to do it. Why should I explain how?
You act as if I don't know the first thing about radar. On the contrary, I was licensed by the FCC at age 10 to run limitless amounts of radiation on point-to-point microwave links within certain pockets of spectrum between 2 and 60 Ghz. That required at least a rudimentary understanding of SHF, and by extension, concepts like radar. But radar, or my knowledge thereof, is completely immaterial.
Getting back to the part where I said "the radar is basically irrelevant", what I was attempting to convey is that I'm not sure we care about Xmax. Distortion metering is the be-all, end-all methodology, IMHO. If we're not approaching the point of cone damage, or thermal damage, then distortion is the only thing left. It would take a sort of "compensating" distortion analyzer, which would be aware of the massive phase shifts and group delays associated with speaker enclosures, but it could definitely be done, and even automated with sine and amplitude sweeps. i.e. "Show me what voltage level at the speaker terminals will produce 10% distortion or less, and draw the distortion graph". Maybe such a thing exists already?
p.s. If you're stuck on this radar thing, a good source of transducers is old microwave-based waveguides used to automatically open the sliding doors at grocery stores. You'll quickly recognize them because the enclosures are rectangular, perhaps 7 inches long or so, as opposed to the modern ones which use infrared and are considerably smaller. But I reeeeally think you're barking up the wrong tree.. 🙂
Wow.. where to begin?
Yeah, same here. You've missed the boat. The part you got correct is "absolute distance referenced to a standard" is irrelevant. I built that unit from a $35 toy. Any project that combines hardware and software with regards to the DSP method using a microphone you described, would at minimum be a full-time project for you that would last 6 months. I built mine from a toy, and it took me 3 days. Good luck on your direction, and if we were competing with products (not that I'm considering it), I'd beat you to market.
Yeah, same here. You've missed the boat.
Apparently I have. After I explained the foregoing to my mentor, he reminded me that distortion analyzers are nothing more than a voltmeter with a steep notch filter to null out the signal-under-test. Whatever voltage is left over comprises distortion.
So I was wrong about the "compensation" - phase and delay are completely irrelevant. All that'd be necessary to pull off the aforementioned is a quality automatic distortion analyzer with a digital output, like this one: Krohn-Hite Model 6900B 1MHz Distortion Analyzer along with a microcontroller (to translate the BCD from the analyzer into something usable for a PC), and a laptop connected to the microcontroller via serial. The code for the microcontroller can be whipped up in a matter of minutes and tweaked/tested in a couple of hours. The programming for tone generation and data logging/graphing on the PC would take perhaps a day.
As we're both trying to hypothetically market these things, methinks my product beats yours to market because it doesn't have to undergo any kind of radiation testing or independent Part 68 certification as yours does 🙂
I've already got everything it takes to build such a thing, except the distortion analyzer, and i'll probably build one if/when I ever get serious about sound reinforcement.
Ask yourself this... Where does the distortion in a subwoofer come from? Microphones are wonderful when you want to mix the rest of the world in your test signal.
No clue where the distortion comes from, as I've yet to meter one with a distortion analyzer. But overall, I'd have to assume distortion comes from resonances within the box or the environment. That's precisely why I chose an arbitrarily high (and presumably audible) amount of distortion in the example above (10%). In the real-world, I have a feeling that subwoofer distortion doesn't sound obnoxiously bad until you reach 40% or so. But the essence of my premise is that the test apparatus captures all of the ills of a subwoofer, be they environmental, internal, or fill-in-the-blank.
I should reiterate that the radar is "still very cool", I just don't think it tells the whole tale.
I should reiterate that the radar is "still very cool", I just don't think it tells the whole tale.
No clue where the distortion comes from, as I've yet to meter one with a distortion analyzer.
I'll save you some time, then. The motor of the driver itself has many non-linear properties. All of them are exercised by at actually moving. And pretty much 60Hz and below is where the motion is taking place. Here's an example.
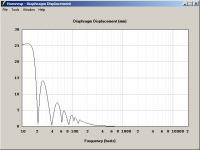
If the motor of the driver is operating correct, thus the cone motion, then how is it possible the sound output could be distorted?
$15 transceiver module, you supply the pringles can for the wave guide.
I'd swear this looks nearly identical to the one used in the Hot Wheels toy (minus the wave guide).
I'd swear this looks nearly identical to the one used in the Hot Wheels toy (minus the wave guide).
So - with one of these modules and a decent o-scope, how much more circuitry would I need to measure my in-cabinet displacement? I don't need the limiter, I'm generally the one running the controls.
A stable +5v supply and around 70dB of gain on the IF output. Just the first half of that diagram I made. You *might* want to include the 633 to compensate for inverse square. It makes the waveform look prettier.
Maybe these guys, too?
Maybe these guys, too?
Last edited:
I got the crazy idea of wanting to paint a target on the driver and add some sort of metal dust to it like crystalline aluminum powder (I'm not making thermite) or iron oxide. Anyone know which has a better reflectivity index in the X-band?
I bet it doesn't matter and I'm, as usual, over thinking something simple: improve reflected signal, done, next.
I bet it doesn't matter and I'm, as usual, over thinking something simple: improve reflected signal, done, next.
If the motor of the driver is operating correct, thus the cone motion, then how is it possible the sound output could be distorted?
If the cone motion becomes nonlinear with amplitude....
Over in Solid State is a discussion of motional feedback, cable effects (no, not the Golden Eared sort), and Kenwood Basic M1 amp Sigma Drive.
My own take is this. Does not make a lot of sense measuring an expensive driver using a radar toy whose own frequency response and distortion are entirely mysterious. Or for that matter, home-made capacitor, cheap accelerometer, or mic. Back EMF from the voice coil (in a bridge) is better.
http://www.diyaudio.com/forums/solid-state/76421-lowering-cable-resistance-extending-feedback-loop.html
My own take is this. Does not make a lot of sense measuring an expensive driver using a radar toy whose own frequency response and distortion are entirely mysterious. Or for that matter, home-made capacitor, cheap accelerometer, or mic. Back EMF from the voice coil (in a bridge) is better.
http://www.diyaudio.com/forums/solid-state/76421-lowering-cable-resistance-extending-feedback-loop.html
Last edited:
It makes no sense to me to close a feedback loop with this radar thing. That's silly mainly because displacement is far removed from sound level response. I'm just using it to give me a displacement output that I use to trigger a limiter. It only needs to be linear from DC (which it is) to like 60Hz from what I've seen. Response of the IF output might be accurate to 40 MHz if one was to use a carrier over it, but I don't care for such things.
Last edited:
Back EMF from the voice coil (in a bridge) is better.
Sorry to hijack.. but what is "back EMF" ? You mean ringing? It sounds almost as if you're referring to some kind of induced radiation, a la inductive coupling from RFI.
- Status
- Not open for further replies.
- Home
- Loudspeakers
- Subwoofers
- Reading driver displacement with radar!