If you don't do so already, then coat your tools with Camelia Oil. It is a non-toxic vegetable oil that oxidises on contact with air to become waterproof. A tiny amount will o a long way. Works on all metals, and indispensable in a maritime climate. ToS
Great tip! Will do
I do not subscribe to the void free, marine grade, multi-ply cult. While it makes sense on paper, I've not seen any evidence that it is it measurably better (whatever that means) than regular G1S. I do prefer fir over spruce unless the cabinet is huge and then I make up for it with stick bracing. I don't bother with shelf bracing, I believe it is more for the believers than a necessity. It's also a lot easier.
I've built a few speakers in 12mm, 15mm and 18mm poplar ply, 15mm poplar ply and a few well thought out braces gets you very far. It's not about adding max weight in any way, you just want to reduce movement in a few select places really.
Can also make structural integrity much higher with a few light aluminum L sections glued&screwed onto longer sections, with a few select wooden crosses between panels.
Cheap 12mm, 15mm or 18mm poplar ply (pending on project size) and "light but right" bracing works really good, the poplar ply always looks really nice on one side, so just get the "right side out", the rich people can enjoy the top notch BB ply.
And I agree 100% Cal, Stick bracing FTW!
Last edited:
It might be, but in the end he uses laminations with a viscous rubber in between.
I watched the video all the way through. He knows his onions. The use of a rubber-oid damper is interesting. I immediately thought of alternatives. If we lived at a time when the Voight tube was invented, we would using something else. From an environmental perspective, I am interested in what that something else might be.
ToS
the best material is one that has a stiff shell and a viscous inner core
a sandwich of two sheets of thin plywood with swedac damping glue inbetween is best
particle board is good also
a sandwich of two sheets of thin plywood with swedac damping glue inbetween is best
particle board is good also
Interesting thread and gets the noodle working. On another thread I asked a similar questions perhaps contributors to this one may be able to provide some guidance -
Possible way of producing an "inert" or heavily damped enclosure -
1) Use an elliptical (ish) curved rear shape (cross section) for the speaker - may not do anything for internal standing waves but will be more rigid than a rectangular box structure
2) For a 100cm tall floor stander add three window pane stiffeners at unequal distances e.g. at 30cm, 55cm and 75cm from the base
3) make the eliptical rear of the enclosure out of a laminate of 5mm flexiply, 5mm acoustic rubber, 5mm flexiply, 5mm acoustic rubber, 5mm flexiply (25mm total) - 5mm ply would give the bend radius I was looking at (40l enclosure) - all bonded together with roofing felt adhesive which stays flexible - Sound Proofing Acoustic Rubber Sheet Matting
4) front baffle made from butchers block worktop (beech or oak) - 28-38mm thick (TBD) - very stable, fairly dense and not too expensive.
Thoughts - may be over the top - could I just bond the three layers of ply (or would flexipl/flexi MDF/Flexiply be better) with only the flexible adhesive (green Glu or Swedac) or use thinner rubber sheet in-between.
Finally, internal will be damped with the Troels G style denim/acoustistuff scheme and there is the option of cladding the outer with a sheet of 1-1.5mm aluminium again applied with the flexible adhesive - mainly cosmetic but may provide another discontinuity in the materials.
All comments welcome as to whether I will hear any difference compared to an 18mm ply plus bracing rectangular enclosure (for info using mid range drivers - ES180Tia x2, 10F8824, SB26CDC - Bass Reflex ported)?
Possible way of producing an "inert" or heavily damped enclosure -
1) Use an elliptical (ish) curved rear shape (cross section) for the speaker - may not do anything for internal standing waves but will be more rigid than a rectangular box structure
2) For a 100cm tall floor stander add three window pane stiffeners at unequal distances e.g. at 30cm, 55cm and 75cm from the base
3) make the eliptical rear of the enclosure out of a laminate of 5mm flexiply, 5mm acoustic rubber, 5mm flexiply, 5mm acoustic rubber, 5mm flexiply (25mm total) - 5mm ply would give the bend radius I was looking at (40l enclosure) - all bonded together with roofing felt adhesive which stays flexible - Sound Proofing Acoustic Rubber Sheet Matting
4) front baffle made from butchers block worktop (beech or oak) - 28-38mm thick (TBD) - very stable, fairly dense and not too expensive.
Thoughts - may be over the top - could I just bond the three layers of ply (or would flexipl/flexi MDF/Flexiply be better) with only the flexible adhesive (green Glu or Swedac) or use thinner rubber sheet in-between.
Finally, internal will be damped with the Troels G style denim/acoustistuff scheme and there is the option of cladding the outer with a sheet of 1-1.5mm aluminium again applied with the flexible adhesive - mainly cosmetic but may provide another discontinuity in the materials.
All comments welcome as to whether I will hear any difference compared to an 18mm ply plus bracing rectangular enclosure (for info using mid range drivers - ES180Tia x2, 10F8824, SB26CDC - Bass Reflex ported)?
Last edited:
I thought about using neoprene between lamination more than 25 years ago. Sand before that. Just too lazy to do it. 😱
Spraying the internal cab with automotive panel deadening spray as well.
I would have done it with MDF anyway as plywood was not as popular a choice back then, not until Baltic birch anyway.
I think the whole plywood use is interesting, especially since I never believed it was better than MDF.
I still don't agree that if a cab makes a sound, it should be nice sound with the analogy of musical instrument bodies.
The only thing that should move is the cone and air.
Spraying the internal cab with automotive panel deadening spray as well.
I would have done it with MDF anyway as plywood was not as popular a choice back then, not until Baltic birch anyway.
I think the whole plywood use is interesting, especially since I never believed it was better than MDF.
I still don't agree that if a cab makes a sound, it should be nice sound with the analogy of musical instrument bodies.
The only thing that should move is the cone and air.
Last edited:
My kick bins or ‘midbass modules’....bottoms (whatever you want to label them)
are going to be semi enclosed into a cabinet that runs the bottom of the whole wall....
Plan on building a built in enclosure for the boxes to slide into with just enough room for tennis balls to fit tight on the sides, there will be a bed underneath with the balls also but packed with sand......might go with some sand up the sides too if I can figure out how to keep it in there.
Using 1” birch ply for the boxes.
are going to be semi enclosed into a cabinet that runs the bottom of the whole wall....
Plan on building a built in enclosure for the boxes to slide into with just enough room for tennis balls to fit tight on the sides, there will be a bed underneath with the balls also but packed with sand......might go with some sand up the sides too if I can figure out how to keep it in there.
Using 1” birch ply for the boxes.
Is there any reason to not use real wood, as opposed to manufactured wood products? I strongly dis like plywood, and MDF/particle board, is not allowed on my property.
I think yes. Mosly cause the enclosure will crack and leak air from changing humidity and temperatures
PHffffftttttt. That is the sound of the opening of a can of worms. Once out of the can, it is impossible to get them back in.
Hm.. I do believe I have some bubbles in the fridge🙂
Weight is not an asset with a speaker box. Given 2 materials of equal stiffness, the lighter one is preferred.
dave
dave
2) For a 100cm tall floor stander add three window pane stiffeners at unequal distances e.g. at 30cm, 55cm and 75cm from the base
Better bracing would run vertically, the subpanels after bracing should have a higher aspect ratio than the original panel.
...internal will be damped with the Troels G style denim/acoustistuff scheme...
Troels? That scheme started here.
dave
More on topic. I will make an important project with a group of collegues from now till the end of June. It will be a portable device that can reproduce music. I will make a dedicated thread when the results of the first brainstorm can be presented.
The enclosure needs to be very lightweight, so we will be willing to sacrifice a bit of soundquality for portability. At the same time its important to beat the soundquality of existing products on this niche-marked.
So can any of you advise me of some types of plywood that are light and stiff? Thanks!
The enclosure needs to be very lightweight, so we will be willing to sacrifice a bit of soundquality for portability. At the same time its important to beat the soundquality of existing products on this niche-marked.
So can any of you advise me of some types of plywood that are light and stiff? Thanks!
Thanks Dave for the info, and the correction, not been on here that long so went with where I found the stuffing regime documented (on the TG site).
However, getting a bit confused as to how to brace - top to bottom (as per Planet 10 MarKen10.2TT) or side to side (as per TG SBA16 MTM) or both. Assuming a fairly slim floor standers w23cm, d39cm, h100cm bass reflex with 7.5cm diam x 15cm port.
However, getting a bit confused as to how to brace - top to bottom (as per Planet 10 MarKen10.2TT) or side to side (as per TG SBA16 MTM) or both. Assuming a fairly slim floor standers w23cm, d39cm, h100cm bass reflex with 7.5cm diam x 15cm port.
Pinched from the AES paper:
You want to push panel resonances as high as possible. From this i derived the ratio rule above. Get that ratio hgh enuff and the short dimension takes precedence. Add-in an offset so that subpanels have different resonances, and the fundemental is fully supressed.
centre placed brace:
Shelf braces will push subpanel ratios closer to a square unless you use lots & lots of them.
I would be cautious with any panel damping that adds mass without stiffness. This lowers the (potential) panel resonance in frequency and broadens its Q. Broader Q means that it will accept a wider bandwidth of energy. A narrow, high Q (potential) resonance needs all the energy in a much narrower bandwidth… not much music will have that much energy, in that small a bandwidth for the time required to get it going.
At higher frequencies, the inherent damping in plywood from the glue between plies, is larger.
dave
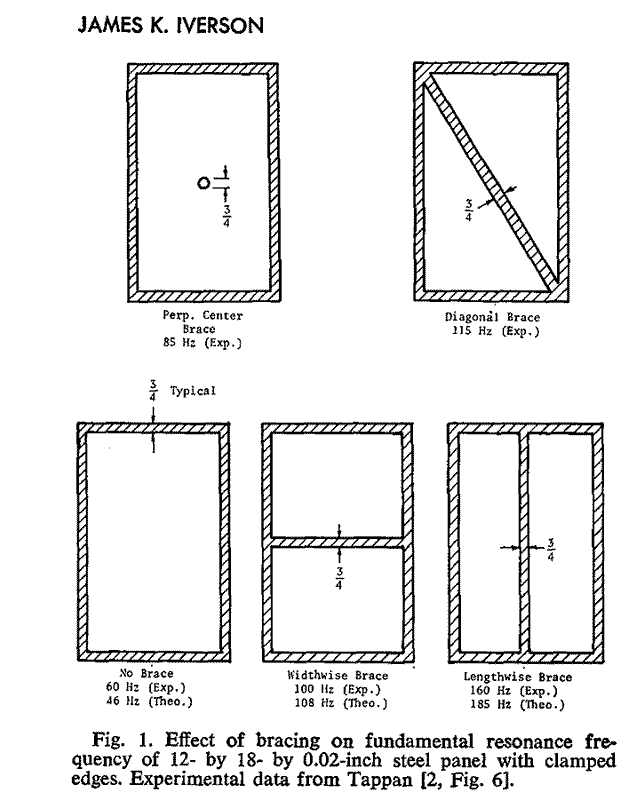
You want to push panel resonances as high as possible. From this i derived the ratio rule above. Get that ratio hgh enuff and the short dimension takes precedence. Add-in an offset so that subpanels have different resonances, and the fundemental is fully supressed.
centre placed brace:
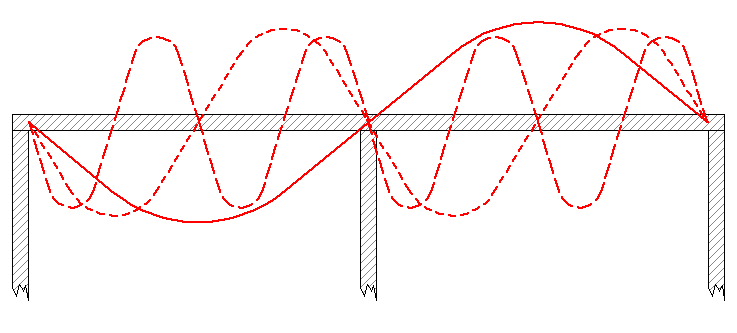
Shelf braces will push subpanel ratios closer to a square unless you use lots & lots of them.
I would be cautious with any panel damping that adds mass without stiffness. This lowers the (potential) panel resonance in frequency and broadens its Q. Broader Q means that it will accept a wider bandwidth of energy. A narrow, high Q (potential) resonance needs all the energy in a much narrower bandwidth… not much music will have that much energy, in that small a bandwidth for the time required to get it going.
At higher frequencies, the inherent damping in plywood from the glue between plies, is larger.
dave
Many thanks again Dave, much appreciated, the penny has dropped, what I thought was a top to bottom brace is actually a slightly offset front to back brace so I assume the brace has to be bonded to the front baffle and also the rear panel.
Weight is not an asset with a speaker box. Given 2 materials of equal stiffness, the lighter one is preferred.
dave
Mass is an asset because m1v1=m2v2 (Conservation of momentum). Twice the mass for the cone to react against, half the "vibrations" in that mass.
I suppose if you make that mass from light springy wood, then you might get a resonant mess of a music box.
Mass is an asset because m1v1=m2v2 (Conservation of momentum). Twice the mass for the cone to react against, half the "vibrations" in that mass.
But at half the frequency i believe. Lower so more likely to get excited. More energy at lower frequencies.
dave
But at half the frequency i believe. Lower so more likely to get excited. More energy at lower frequencies.
dave
m1v1=m2v2 is not about frequencies, but I'm already over my head here....
- Status
- Not open for further replies.
- Home
- Loudspeakers
- Multi-Way
- Ply vs MDF