Yes these are bucking magnets. As the TSP of the 26W disco cry for large enclosures I decided to lower Qes --> Qts with the additional magnets that increase BL by nearly 10%. As positive side effect the efficiency is increased also a bit and the magnetic circuit gets better saturated which lowers Le a little (this might decrease iron distortion also accordingly)
I've attached my simple Excel file for sizing the absorber:
I've attached my simple Excel file for sizing the absorber:
Attachments
Some new arrivals:
SB Acoustics Satori MR13TX-4. Did not like that beauty rubber rings without use and put them off. Very pretty driver.
Have decided that the Bliesma M74A is oversized from price and SPL capabilities and took the SBs now.
(~230.-€ each at TLHP.fr, so about half the price of the M74A at my location)
Will pair it with the Bliesma T25A in a waveguide designed by @fluid printed of PA12 nylon. Will lacquer them black:
The 104mm outer diameter and 6mm depth is nice as other tweeters from Scan Speak, SB or Seas can easily be switched in:
This is hopefully the final setup to build the enclosures for, as all drivers and other parts are in the house now:
Will go to the last details, part drawings and BOM now.
Another point is measurements, I'm not happy with my current turntable and mic stand...
SB Acoustics Satori MR13TX-4. Did not like that beauty rubber rings without use and put them off. Very pretty driver.
Have decided that the Bliesma M74A is oversized from price and SPL capabilities and took the SBs now.
(~230.-€ each at TLHP.fr, so about half the price of the M74A at my location)
Will pair it with the Bliesma T25A in a waveguide designed by @fluid printed of PA12 nylon. Will lacquer them black:
The 104mm outer diameter and 6mm depth is nice as other tweeters from Scan Speak, SB or Seas can easily be switched in:
This is hopefully the final setup to build the enclosures for, as all drivers and other parts are in the house now:
Will go to the last details, part drawings and BOM now.
Another point is measurements, I'm not happy with my current turntable and mic stand...
It really is a shame that it won't be seen in the box.Very pretty driver.
I made myself an automated table, very quick and accurate to take a set of polar measurements in ARTA. Belt driven stepper motor, working code in the first post. This is the end result which is quite different to where I started 🙂Another point is measurements, I'm not happy with my current turntable and mic stand...
https://www.diyaudio.com/community/...-motor-and-tic-controller.387325/post-7776912
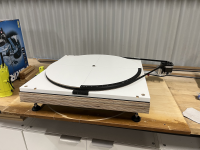
Looking forward to see your measurements and thoughts on the different combinations.
Wonder if one can make the break up of this Satori by puting a non touchint foam circle over the moat to smooth the transition ? Makes me think of the aerogel 13 cm from Audax and the Kartesian mid you already has !
looks good indeed. Finaly went to my conclusion but w/o tested the idea, textrem is best used for the mid or bass range,, not necessarily so for the trebles.
looks good indeed. Finaly went to my conclusion but w/o tested the idea, textrem is best used for the mid or bass range,, not necessarily so for the trebles.
@diyiggy : Thanks, but sorry i did not get what you mean exactly with "non touchint foam circle over the moat". May you explain it a bit more?
@fluid : Thanks again for the waveguide design. And your turntable looks good, especially the automation!
This is the current setup:
I've invested last year in a used Thinkpad and Motu M2 to avoid carrying my PC and monitor around, an Isemcon IMX-7150 mic for better measurements an a DATS V3 to get rid of the Arta switchbox.
I want to improve now on the turntable mechanical setup also for better accuracy, alignment and repeatability.
The current setup has following main issues:
I have the goal to make quasi-anechoic requirements in 2m distance with a resolution of 100Hz, this means in ~2,5m height (outside or in a hall) according calculation. Nearfield measurements +merging is nice, but i want to see also the woofer-mid transition part sufficiently in the "farfield" spin during developing 3+ -way speakers, especially i want to see the phase transitions.
The 2,5 m is hard to get, thinking of a ~< 1m overall turntable diameter with such kind of bearing in ~80 cm diameter:
and mounting such PA-speaker lift on it:
Must detail this also now, will need some milled plywood parts for the stand/turntable construction and want to order them together with the speaker parts...
@fluid : Thanks again for the waveguide design. And your turntable looks good, especially the automation!
This is the current setup:
I've invested last year in a used Thinkpad and Motu M2 to avoid carrying my PC and monitor around, an Isemcon IMX-7150 mic for better measurements an a DATS V3 to get rid of the Arta switchbox.
I want to improve now on the turntable mechanical setup also for better accuracy, alignment and repeatability.
The current setup has following main issues:
- turntable parallax error as the speaker front panel cannot be in line with the turn axis
- mic stand too short and wobbly. Aiming the mic to the speaker's acoustic axis is hard to get right
- Speaker stand not adjustable for correct vertical alignment and speaker balance
- Limited speaker size and weight capability, mostly coming from the issue to get the speakers up there and balanced manually
I have the goal to make quasi-anechoic requirements in 2m distance with a resolution of 100Hz, this means in ~2,5m height (outside or in a hall) according calculation. Nearfield measurements +merging is nice, but i want to see also the woofer-mid transition part sufficiently in the "farfield" spin during developing 3+ -way speakers, especially i want to see the phase transitions.
The 2,5 m is hard to get, thinking of a ~< 1m overall turntable diameter with such kind of bearing in ~80 cm diameter:
and mounting such PA-speaker lift on it:
Must detail this also now, will need some milled plywood parts for the stand/turntable construction and want to order them together with the speaker parts...
I was talking of the inverted surround znd its steep transition from the edge. While better than standard bumped surrounds, it should be better with a planar foam ring not touching the cone edge but covering almost fully the "moat".
Story to rreducethe main break up.
Story to rreducethe main break up.
Okay so you mean to cover the groove of the inverted surround to make the surface flat for the sound coming from the cone? I think it will have no influence to the main cone breakup frequency. It will influence the breakup when some material touches the cone...
Well I think with the inverted surround everything is fine. Looking at the front view the Satori has more in common with the Kartesian regarding cone and surround shape than with the Scan Speak 15M or SB15NBAC which appear also much larger and different in kind.
The SB Textreme cone has inverted dome shape but is very flat which is good for open midrange sound. Kartesian cone is also very flat paper made with inverse dome shape carbon fibre dustcap covering nearly half the cone area. Both share inverse surround as mentioned, SB one made of low loss rubber and Kartesian made of very low loss fabric(!). These drivers are really exhausted small cone mids and I'm excited to get them properly running.
Well I think with the inverted surround everything is fine. Looking at the front view the Satori has more in common with the Kartesian regarding cone and surround shape than with the Scan Speak 15M or SB15NBAC which appear also much larger and different in kind.
The SB Textreme cone has inverted dome shape but is very flat which is good for open midrange sound. Kartesian cone is also very flat paper made with inverse dome shape carbon fibre dustcap covering nearly half the cone area. Both share inverse surround as mentioned, SB one made of low loss rubber and Kartesian made of very low loss fabric(!). These drivers are really exhausted small cone mids and I'm excited to get them properly running.
Last edited:
I tried to use a couple of bearing methods but I was not very happy with the stability or smoothness even though they both worked. Simply using melamine sheets with a lubricant inbetween (white lithium spray grease) and a pin or bolt in the middle has provided a very stable base with no rocking or wobbling and is supported over the whole platform making it strong. This is important if the weight will be on the rear half to avoid parallax error. Whether manual or automatic movement this is a simple option but I was not able to improve by making it complicated 🙂The current setup has following main issues:
- turntable parallax error as the speaker front panel cannot be in line with the turn axis
- mic stand too short and wobbly. Aiming the mic to the speaker's acoustic axis is hard to get right
- Speaker stand not adjustable for correct vertical alignment and speaker balance
- Limited speaker size and weight capability, mostly coming from the issue to get the speakers up there and balanced manually
I got a 3m lighting stand to use as a mic stand with a few 3D printed bits to hold a mic tube onto it.
The height is a bit of a practical issue, I quite like the idea of using lighting truss that comes in 1m sections and can be bolted together, I have seen kimmo using it on his turntable.
Those K&M cranks are quite wobbly and might need some reinforcement if the speakers are large or heavy. Without a block and tackle or some powered lifting device a big speaker is going to be hard to raise to 2.5m.
The turntable can be placed on a desk or similar so the actual tower part doen't need to be so tall.
Might work, although the table will be on the heavier side to turn and carry. But I understand that I need some sturdiness....
don't know if I've expected r_eff correctly, will review that again...
don't know if I've expected r_eff correctly, will review that again...
Last edited:
Have made a wrong assumption, so r_eff is 0,4m and so F_hand will double to equivalent 10 kg. Will correct that....
So it's much simpler, the above is wrong:
Mmmh, I like the light truss but still not sure about the bearing concept.
Mmmh, I like the light truss but still not sure about the bearing concept.
I can only pass on my own experience of having tried these things out. I also originally aimed to reduce friction, as static friction is the biggest single factor that limits the ability of a motor to turn a heavy load in calculations. When you try to acheive this in reality you realise that having no resistance is actually a bad thing. Even with the melamine I tried a few different lubricants trying to reduce friction (PTFE, Bicycle Fork Grease). I cleaned them off and put some more sticky grease on because it just works better for the application. For manually turning a heavy load you might prefer a little less resistance, for turning with a belt and motor a little bit more resistance smooths the movement out.Mmmh, I like the light truss but still not sure about the bearing concept.
If you go with a large ring bearing on the outside you can use larger single balls in a ring in the centre or spread out to help with spreading the weight more evenly for support, like in one of the examples from ARTA.
With those large ring bearings the best way to reduce friction is to get rid of the metal balls and replace them with POM or Acetal. They really fly and you will be able to spin it freely with one finger.
With a turntable which is rotated manually, some friction is very useful in holding the rig at a particular position. There is no locking mechanism, so friction is the only thing which prevents the table from drifting out of alignment... your 45 degree scan drifts slowly to 48 degrees, which is annoying and a waste of time.
Of course, with a stepper motor (or equivalent), the motor holds things quite stationary.
When I started making polar scans with a manual turntable, I was concerned that manually rotating the rig would be slow. With a bit of practice, I have found that the frequency sweeps are the biggest consumers of time. The process of stepping over to the rig and rotating it 10 or 15 degrees is rather fast in comparison.
j.
Of course, with a stepper motor (or equivalent), the motor holds things quite stationary.
When I started making polar scans with a manual turntable, I was concerned that manually rotating the rig would be slow. With a bit of practice, I have found that the frequency sweeps are the biggest consumers of time. The process of stepping over to the rig and rotating it 10 or 15 degrees is rather fast in comparison.
j.
There is relatively little value in using long sweeps for polar frequency response measurements. The speed might not matter that much if is only done rarely as the set up time of everything else can be the biggest drain. The automated table is really fast only a couple of minutes for 0 to 180 in 10 degree steps, but the consistency and ease of making smaller angle increments accurately is probably its best feature.With a bit of practice, I have found that the frequency sweeps are the biggest consumers of time.
Yes, exactly: manually rotating the measurement tower doesn't mean any particular effort for me either.When I started making polar scans with a manual turntable, I was concerned that manually rotating the rig would be slow. With a bit of practice, I have found that the frequency sweeps are the biggest consumers of time. The process of stepping over to the rig and rotating it 10 or 15 degrees is rather fast in comparison.
And since REW has introduced a mechanism that automatically generates meaningful file names, this time waster has also disappeared.
Here is an example in which the tweeter XY is to be measured from -90 degrees in steps of 10 degrees, whereby the manual rotation of the measurement tower by 10 degrees and two mouse clicks are required between each measurement:
"hor" signals to the VituixCAD file name parser that the measurements are horizontal.
Btw.: this is my measurement tower:
Bitte entschuldigt die Unordnung......🙄
edit:
Unfortunately, the tower is not particularly immune to asymmetrical loads, which inevitably occur with vertical measurements. It seems obvious to me that lightning truss is much stiffer and therefore probably more suitable than four unconnected steel tubes.
Last edited:
Oh, clearly you have not seen my garage... 🙂Bitte entschuldigt die Unordnung......
- Home
- Loudspeakers
- Multi-Way
- Peter's modular loudspeaker platform