Hi, I want to change the internal speaker cable for my speakers. However i have never done soldering before and now i am having trouble soldering the 14 gauge wire to the tab of the binding post. The problem i have is that the solder does not melt ! First i tried to tin the wire, but after heating the wire long enough that the insulation melted the solder does not get sucked into the wire. This is what i did : i touched the soldering iron on the underside of the wire and touched solder to the top of the wire. Is this the right way ? Am i doing something wrong or the soldering iron not good enough ?
This is the generic 60W iron that i bought for $6. When tinning this iron the solder sticks to it like glue and not flow.
This is the generic 60W iron that i bought for $6. When tinning this iron the solder sticks to it like glue and not flow.

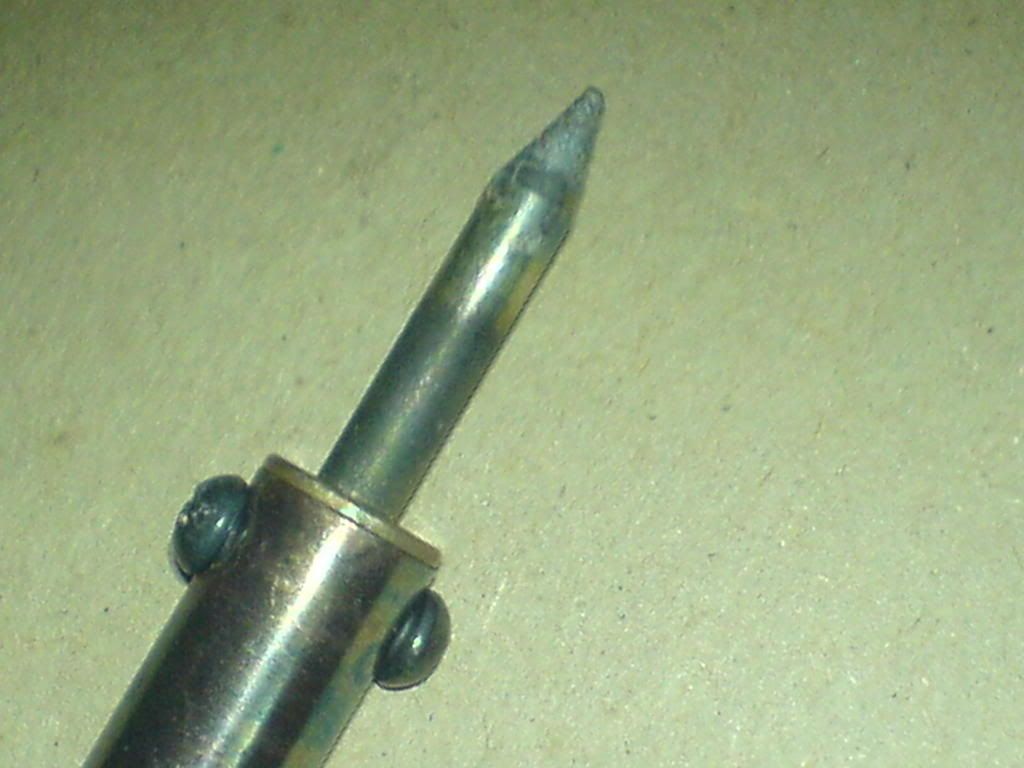
You say that when you try to 'tin' the iron, that the solder "sticks to it like glue, not flowing", that's indication that the iron is not hot enough.
Very typical for a cheap iron, very bad (no) temperature control.
My advise, if you can afford it buy a decent iron.
Hakko, Weller, can't remeber the others now.
Other option is not to solder but to use crimp connectors.
In theory a crimped joint is better than soldering.
This is because soldering heats the wire stands to a point where it creates a mechanical weak spot where the solder flow has stopped.
And although I have seen many instances of wires breaking at this point vs almost none that have been crimped.
For internal speaker connections I still preffer to solder.
Go figure 😕
Maybe crimp a male spade to the cable and solder that to the terminals ?
Very typical for a cheap iron, very bad (no) temperature control.
My advise, if you can afford it buy a decent iron.
Hakko, Weller, can't remeber the others now.
Other option is not to solder but to use crimp connectors.
In theory a crimped joint is better than soldering.
This is because soldering heats the wire stands to a point where it creates a mechanical weak spot where the solder flow has stopped.
And although I have seen many instances of wires breaking at this point vs almost none that have been crimped.
For internal speaker connections I still preffer to solder.
Go figure 😕
Maybe crimp a male spade to the cable and solder that to the terminals ?
Depending on the size of the internal wire, you might need up to 120W. Thick cables dissipate heat faster than the temperature rises, so you need an iron that will give heat faster than it can be dissipated.
Soldering should be done fast, you'll need a lot of power to do this with heavy gauge wire. That way stranded wire won't suck up the liquid solder too far (which indeed weakens the mechanical properties) as the wire will become stiff and function as a lever when the wire is pulled. The wire will break faster. Fast soldering will concentrate the heat on a smaller surface so the insulation won't have the chance to melt.
It is critical though that the solder melted entirely along the two surfaces that were bonded, so don't go too fast! (which will result in a 'cold' joint...) Timing is rather critical, if things won't go smoothly just let the surface cool down and try again using a different approach.
I like to use a 'microtorch' for the somewhat heavier work, they're cheap and incredibly effective.
http://www1.nl2.conrad.com/conrad_n.../nl_NL&fh_search=gasbrander&fh_refview=search
http://image01.conrad.com/s/4000_4999/4300/4330/4335/433586_LB_01_FB.EPS.gif
A good way to heat the wire faster is to melt the solder to form a heat bridge, start at the tip of the wire and the solder should start to suck up very effectively.
If it still won't go than you have either a bad iron or bad solder...(as mentioned in previous posts...)
It is critical though that the solder melted entirely along the two surfaces that were bonded, so don't go too fast! (which will result in a 'cold' joint...) Timing is rather critical, if things won't go smoothly just let the surface cool down and try again using a different approach.
I like to use a 'microtorch' for the somewhat heavier work, they're cheap and incredibly effective.
http://www1.nl2.conrad.com/conrad_n.../nl_NL&fh_search=gasbrander&fh_refview=search
http://image01.conrad.com/s/4000_4999/4300/4330/4335/433586_LB_01_FB.EPS.gif
A good way to heat the wire faster is to melt the solder to form a heat bridge, start at the tip of the wire and the solder should start to suck up very effectively.
If it still won't go than you have either a bad iron or bad solder...(as mentioned in previous posts...)
The biggest 2 mistakes people make with soldering:
1: Spreading the solder around with the iron like butter with a knife. this never, ever works. Keep the iron still and let the solder travel with the heat flow.
2: cheap solder. But the most expensive 60/40 solder you can find. That is without silver and special metal additives, a little bit of copper doesn't hurt. Buy thin solder, you can use thin solder for big jobs by twisting a few strands together, you can't cut thick solder in half.
It is sold by weight anyway. Buy the solder form an electronics shop, not the corner hardware store.
1: Spreading the solder around with the iron like butter with a knife. this never, ever works. Keep the iron still and let the solder travel with the heat flow.
2: cheap solder. But the most expensive 60/40 solder you can find. That is without silver and special metal additives, a little bit of copper doesn't hurt. Buy thin solder, you can use thin solder for big jobs by twisting a few strands together, you can't cut thick solder in half.
It is sold by weight anyway. Buy the solder form an electronics shop, not the corner hardware store.
I've found that I just burn up cheap irons like that one.
For big jobs, I bought a Weller ~100W gun and that gets it done a lot faster...no more waiting for the joint to heat up.
For big jobs, I bought a Weller ~100W gun and that gets it done a lot faster...no more waiting for the joint to heat up.
the solder i use has rosin core. By the way is right that i heat up the binding post connector and wire with the iron, and try to melt the solder by touching it on the wire and connector ? Because using this way the solder never melts ! So i heated the connector and wire with iron touching both and melting the solder on the tip of the iron and let them join. Is this the right way ?
Buzy said:
A quick google of "how to solder" turned up multiple sites, including this, which has illustrations and which answers the question.
Regards.
Aengus
Is this the right way ?
A quick google of "how to solder" turned up multiple sites, including this, which has illustrations and which answers the question.
Regards.
Aengus
Buzzy said:So i heated the connector and wire with iron touching both and melting the solder on the tip of the iron and let them join. Is this the right way ?
v-bro said:
A good way to heat the wire faster is to melt the solder to form a heat bridge...
The solder should indeed be melted on the tip creating the heat bridge that will trasfer the heat to the connector and wire. Best way is to pre-solder the wire and connector first. If you join them when still a bit warm it will go easier....but endeed allways add the solder by touching the tip first, when things are hot enough you can add the solder on other places...
Keep your fingers at a good distance from the heat and keep the wire still until the solder is hard again. Blowing at it helps to cool it down faster.
Let the tin solder do the job fore you, not the iron
First add some tin solder to each item to be soldered... not too much as it might make it difficult to heat up again.... it dont have to be perfect at this point
let it cool a few seconds and heat it again and THEN you might get more heat - when the solder starts to flow again, add more tin solder
But carefull with speaker drivers ... it gets VERY hot
And yes, thick multicored wire is a pain fore the unexperienced and are really not intended to be soldered
First add some tin solder to each item to be soldered... not too much as it might make it difficult to heat up again.... it dont have to be perfect at this point
let it cool a few seconds and heat it again and THEN you might get more heat - when the solder starts to flow again, add more tin solder
But carefull with speaker drivers ... it gets VERY hot
And yes, thick multicored wire is a pain fore the unexperienced and are really not intended to be soldered
Sorry, I forgot this...
When powering up the iron, leave it be fore some minutes to get hot
And when doing heavy soldering, do NOT use the point of the tip, but instead solder with sides of the tip to transfer more heat
But if its heavy wire it might be better to crimp on some solder lugs ... I think its called that
When powering up the iron, leave it be fore some minutes to get hot
And when doing heavy soldering, do NOT use the point of the tip, but instead solder with sides of the tip to transfer more heat
But if its heavy wire it might be better to crimp on some solder lugs ... I think its called that
Hang on guys, he's having trouble tinning the iron. If the iron can't melt the solder, he's going nowhere.
Buzzy, it seems your method is OK. I had one of those irons once. One problem is the 2 grub screws. Remove one, and tighten the other, pushing the tip firm against the bore of the barrel. You might then be able to melt the solder to tin the tip.
IIRC, it's only 15 or 20 watt, and took about 15 minutes to come up to temp. Only just big enough to solder small components on PCBs with no crosswind!
Go for a Weller or Hako if you plan to do more soldering. Personally, I don't like crimped connectors.
Geoff.
Buzzy, it seems your method is OK. I had one of those irons once. One problem is the 2 grub screws. Remove one, and tighten the other, pushing the tip firm against the bore of the barrel. You might then be able to melt the solder to tin the tip.
IIRC, it's only 15 or 20 watt, and took about 15 minutes to come up to temp. Only just big enough to solder small components on PCBs with no crosswind!
Go for a Weller or Hako if you plan to do more soldering. Personally, I don't like crimped connectors.
Geoff.
Where did you get the solder? I purchased some solder from an electronics store last year that was the worst I had ever used. Went down to RadioShack and bought their solder in a tube and it worked fine. I now buy it by the spool from reputable vendors.
A 60 watt iron should be more than enough to do what you are doing. I however, have never liked a round pointed tip for my irons. I prefer a tip with flats. Let the tip corode every where but the very last bit of the tip, around 3/16", helps the heat transfer.
A 60 watt iron should be more than enough to do what you are doing. I however, have never liked a round pointed tip for my irons. I prefer a tip with flats. Let the tip corode every where but the very last bit of the tip, around 3/16", helps the heat transfer.
Solid advise, sure... but I think his method is wrong
He says, he is heating underneath the wire and add solder tin to the top side
Thats not gonna work with thick multicore speaker wire
You need to add hot solder tin to make the heat spread better to the wire
And maybe you should clean your solder tip ... damp paper napkin will do .... when the tip is hot
He says, he is heating underneath the wire and add solder tin to the top side
Thats not gonna work with thick multicore speaker wire
You need to add hot solder tin to make the heat spread better to the wire
And maybe you should clean your solder tip ... damp paper napkin will do .... when the tip is hot
Geoff H said:Hang on guys, he's having trouble tinning the iron. If the iron can't melt the solder, he's going nowhere.
As far as I can see, he doesn't mention anywhere that he cant tin the iron. On the contrary, hes saying he can heat the wire up hot enough to melt the insulation but not the solder properly.
Aside from a couple of issues with regards to technique maybe, there is the simple fact that this iron may NOT be powerful enough to get the job done.
I used to hate trying to solder binding posts, I used to use an 18 watt antex iron. Great little thing for the money, but it had trouble with the bigger jobs. It eventually would manage to solder the join, but it would take ages and not do a very good job, this is with years of soldering under my belt so I know what I am doing here. Technique helps a lot with something like this, but you cannot get around the fact the iron may not have enough juice. I do however have a cheap and cheerful iron like the one you have there, and it IS capable of soldering binding posts, with time, so perhaps it is your technique, or a faulty iron(doubtful theres not a lot to go wrong).
If you cannot tin the wire properly then this suggests a power shortage. As suggested here, try using the side of the tip to transfer more heat, try doing this to just tin the wire. If the iron cant manage that, then you have no hope of the binding post.
FWIW I purchased a used Metcal from ebay for £50, takes around 10 seconds to solder heavy guage wire to a binding post. So I'd highly recommend getting one, new though they are just idiotically expensive.
I've been told that soldering wire to the tweeter's terminals can cause enough heat to damage the tweeter...just a FYI.
And I found that I needed to invest in a soldering station before I was able to consistantly get good results, but I'm also a noob.
And I found that I needed to invest in a soldering station before I was able to consistantly get good results, but I'm also a noob.
Soldering tweeters doesn't have to be dangerous. I use flux paste and load the tip with solder. Apply to the area and remove as soon as it flows. Grab the tab on the coil side with a pair of needlenose and hold 15 seconds. Repeat as necessary after it is cool. Clean the flux with alcohol. Never had a problem.
Fifth element, quoting Buzzy in his first post.
"When tinning this iron the solder sticks to it like glue and not flow."
The iron should be hot enough that the solder should remain "fluid" on the tip, and fall off the tip if tapped or wiped.
I always apply heat on the lower side of multi strand cables, and apply solder to the top. The heat draws the solder through the stands. If the iron is hot enough, and has enough mass in the tip, it's done quickly, and doesn't melt the insulation.
Then the lead can be soldered to the terminal or lug.
"When tinning this iron the solder sticks to it like glue and not flow."
The iron should be hot enough that the solder should remain "fluid" on the tip, and fall off the tip if tapped or wiped.
I always apply heat on the lower side of multi strand cables, and apply solder to the top. The heat draws the solder through the stands. If the iron is hot enough, and has enough mass in the tip, it's done quickly, and doesn't melt the insulation.
Then the lead can be soldered to the terminal or lug.
Cal Weldon said:Soldering tweeters doesn't have to be dangerous. I use flux paste and load the tip with solder. Apply to the area and remove as soon as it flows. Grab the tab on the coil side with a pair of needlenose and hold 15 seconds. Repeat as necessary after it is cool. Clean the flux with alcohol. Never had a problem.
That's some good advise! I used to touch delicate soldering with a piece of aluminum to cool down quicker....
As I mentioned before a gas soldering device is the cheapest and easiest way to do the more heavy soldering. I solder all heavier binding posts and thick multistrand wires that way. It's quick and dirty, but when applied carefully it makes a clean joint in seconds, no time wasted on the heating up!
Again:http://www1.nl2.conrad.com/conrad_n.../nl_NL&fh_search=gasbrander&fh_refview=search
Cheaper is IMPOSSIBLE!
Another soldering method that caught my eye:
http://www1.nl2.conrad.com/scripts/...&page=1&p_catalog_max_results=10&cachedetail=
It heats up in the blink of an eye and cools down with the same speed....
Attachments
- Status
- Not open for further replies.
- Home
- Loudspeakers
- Multi-Way
- Need help to solder speaker cable