Simulation done. I'd appreciate a second opinion on this, since I'm still a bit unsure about... everything. Attached two files; One with the Beta 8 loaded, another with the FE206E that the enclosure was designed for.
Some fairly juicy troughs in the FR chart in both cases, but maybe it's fine in practice?
Some fairly juicy troughs in the FR chart in both cases, but maybe it's fine in practice?
Attachments
Did you account for this?Note too that HR's auto driver/vent pathlength difference calculation is zero since that's normally the case with typical vented alignments, but presumably you're not going to be listening with your face buried in the cone, so the ROT is 1/2 the pathlength distance, which smooths it out somewhat and gets rid of the deep 3rd harmonic dip.
I got all confused about it and read somewhere that that parameter was supposed to be the exterior distance between driver and horn mouth, which came out to ~17cm with this particular design -- but that's a relief. Resulting FR doesn't look half bad now! Certainly workable.
From what I've gathered, a mean deviation of 6dB(+-3dB) is what most of the industry shoots for, and right now the sim is indicating that's about where we're at. Specifically between 67Hz and 93Hz. I'll be messing around to see what a couple small tweaks can do, but at what point would you typically call it good enough?
From what I've gathered, a mean deviation of 6dB(+-3dB) is what most of the industry shoots for, and right now the sim is indicating that's about where we're at. Specifically between 67Hz and 93Hz. I'll be messing around to see what a couple small tweaks can do, but at what point would you typically call it good enough?
Assuming you intend to put filling in the throat section the sim would show if this would clear up some of the ripple.
Yep, tried a bit of filling but no matter how I went about it it basically just killed a bit of the bass response for no significant gain anywhere else. Ripple stayed mostly the same. I'll just have to experiment "in-room" with the filling once they're built.Assuming you intend to put filling in the throat section the sim would show if this would clear up some of the ripple.
Anyways, I've gone and found the best config I can manage for the 8's I think. Here's the modified enclosure compared with the old one. Primarily did away with that big dip around 100Hz and extended the sub response marginally. Outside dimensions are 3cm deeper and 1.8cm taller, so fairly small concession, size wise. Hornresp file attached -- if anyone feels like taking a quick look through it I'd appreciate any pointers. Still very new to all of this.
For now I'm happy though. Going to let it rest for a bit and look at material options. Ideally I'd do baltic birch, but it's insanely expensive around here so MDF is looking more likely.
Attachments
Last edited:
FYI/FWIW, for a given cab's rigidity you'll ideally need extra bracing of the exterior panels and/or thicker ones: https://www.diyaudio.com/community/threads/what-mdf-thickness-is-acceptable.39991/#post-464294
'Ripple' has to do with horn terminus size for a given flare frequency, factor, IOW design a full size horn in free space and the response will be ~billiard table flat, so it's all about the horn/boundary acoustic impedance (mis)match. Note the horn's super rapid final flare as a compromised average to minimize it as much as practical that sets this horn apart from the norm.
'Ripple' has to do with horn terminus size for a given flare frequency, factor, IOW design a full size horn in free space and the response will be ~billiard table flat, so it's all about the horn/boundary acoustic impedance (mis)match. Note the horn's super rapid final flare as a compromised average to minimize it as much as practical that sets this horn apart from the norm.
Last edited:
Yeah -- we'll have to see what i can do about it. Might ultimately be worth it just to spring for the BB ply and save myself the hassle.
Has my uneducated meddling compromised this feature or would you say it still looks decent in the sims/models?Note the horn's super rapid final flare as a compromised average to minimize it as much as practical that sets this horn apart from the norm.
Looks like nice work. This is 100% outta my behind, but Ron's thing seemed to be as much about particle/ray properties as wave properties. The only thing that leapt to mind--and it's comparatively simple now that you've done all the CAD work--is to try to preserve the incidence/reflection angles at each turn. The reality is uglier and you can find that in other tools but IIRC Ron did the layout in 2-D and I recall admiring those turns at the time. That's the vibe about Ron's approach--preserving energy--still in my head from those discussions years ago (corrections welcome). Keep the HR goodness, and massage some angles, maybe. I never modeled that thing and maybe I'm all wrong, but it's what I'd do if I were trying to honor what Ron did in that thing. If you take the time to stare at those turns a while with Huygens/particle goggles on your imagination, it's evident that the man took extreme care making those turns. Walk your brain around that path with the intent to minimize loss, basically. FWIW. Of course there will be argument that none of that applies or even matters at the wavelengths involved...and yet it appears to be what was done. Or maybe it was Dave that went to all that trouble -- I lost Ron's stuff two hard drives ago.
As for the rest of it--blending the handoff between front and rear radiation, who knows...that's more work and you need curves to look harder. Probably wont see 1/8th-space boundary support, either... Gotta measure and/or do more-involved sims in other stuff.
Still and all, it's a fine effort, despite this curmudgeonly sounding post.
As for the rest of it--blending the handoff between front and rear radiation, who knows...that's more work and you need curves to look harder. Probably wont see 1/8th-space boundary support, either... Gotta measure and/or do more-involved sims in other stuff.
Still and all, it's a fine effort, despite this curmudgeonly sounding post.
Last edited by a moderator:
Assuming 3/4" MDF, just laminate an outside layer of same as 'close enough' or add a finished hardboard for the last 1/8" or go 'whole hog' with 1" MDF or appropriate thickness of apple, BB, marine ply........or my 'poor man' option of mass loading it with removable stone, concrete, etc.., top plate(s) or for the S.O., a decorative plant of their choosing and best to have a massive base or at least an 'outrigger' stand unless no worries WRT knocking them over.Yeah -- we'll have to see what i can do about it. Might ultimately be worth it just to spring for the BB ply and save myself the hassle.
Has my uneducated meddling compromised this feature or would you say it still looks decent in the sims/models?
Dunno haven't viewed them yet, though doubt it as it's not a high tech 'thing', just makes for a bit smoother horn/room impedance response with the 'biggie' making sure there's no corners that can reflect back upstream or you wind up with just a bunch of individual 1/2 WL resonators in series.
'Preciate the input, Grindstone! Good point about the angles. Depending on how long it takes to gather the funds necessary to build these things (Probably a good few months) I might get around to simulating both the 2D and 3D CFD properties to verify the geometry.
Can mass loading potentially help compensate for thinner wall materials, or does it mainly help in other ways?
I'm also a little tempted to experiment with composites. Maybe a honeycomb/gyroid-patterned foam core filled with some kind of acoustically inert concoction and laminated with cf/fiberglass? Would likely be a fair bit lighter and easier to create wild shapes with, long as one can wring some decent properties out of it.
Mass loading is definitely a probable solution. I've considered routing out the highlighted areas on one side to house removable concrete "casettes" that get screwed in place. Makes moving the speakers around easier when it comes to it. Also allows for a bit of experimenting.[...]'poor man' option of mass loading it with removable stone, concrete, etc.
Can mass loading potentially help compensate for thinner wall materials, or does it mainly help in other ways?
I'm also a little tempted to experiment with composites. Maybe a honeycomb/gyroid-patterned foam core filled with some kind of acoustically inert concoction and laminated with cf/fiberglass? Would likely be a fair bit lighter and easier to create wild shapes with, long as one can wring some decent properties out of it.
Yes, my early BLHs were ~replicas of the pioneer's refrigerator sized ones, so started with this size cardboard boxes that of course needed weight at the bottom and the neighbor that got me the boxes educated me on how to properly crate/brace, etc., with mass loading the top a substitute for the crate's 'lashing' to a pallet, so lots of box material latitude depending on how much/type of bracing/reinforcement used, though for box/horn internal panel(s) best to make them as rigid as practical.
Composites are great for speaker building, but either too expensive and/or not worth the effort overall if making some from scratch. I'm right at 30 yrs obsolete now, but it was amazing how relatively thin 'skinned' some explosion proof controllers I was involved in the design of wound up being.
Composites are great for speaker building, but either too expensive and/or not worth the effort overall if making some from scratch. I'm right at 30 yrs obsolete now, but it was amazing how relatively thin 'skinned' some explosion proof controllers I was involved in the design of wound up being.
@Scottmoose Can't remember if you were around when Ron joined (on the earlier FR forum IIRC) and made a 'quickie' RS 40-1354? MLTL to see what all the 'fuss' was about, so posted a picture with a huge stack of LPs perched precariously on top and decreed it a worthwhile tweak.
Okay, so ideally the weight would be placed as high up as possible then? A bit in the base too, I presume.
On the subject of bracing; I've read a bit about it but not quite sure how to approach it yet. I understand that any large, flat areas should have a bit of asymmetrically positioned braces to stiffen them up, much like one would find on the inside of an acoustic guitar -- Essentially ridges extending perpendicular to the surface.
But, when does a part call for cross-braces? As in braces running from one side of the cabinet to the other? I get that it depends, but let's just take a look at some spots I've identified as potentially being in need of bracing.
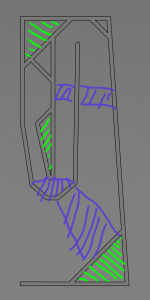
The purple sections are where I would run braces parallel to the sides, just to give a bit of extra support to the folds and such. Would most likely end up being thinner, laser-cut pieces to not eat up too much volume.
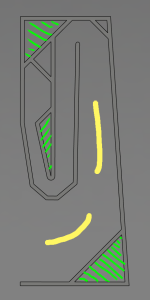
The yellow sections indicate areas where i might want to add bracing from side to side. Ideally they'd be placed further towards the mouth, but i don't really like the look of it.
Does this seem decent, or tawdry? Sincerely appreciate the help you guys have offered, I'm excited about this!
On the subject of bracing; I've read a bit about it but not quite sure how to approach it yet. I understand that any large, flat areas should have a bit of asymmetrically positioned braces to stiffen them up, much like one would find on the inside of an acoustic guitar -- Essentially ridges extending perpendicular to the surface.
But, when does a part call for cross-braces? As in braces running from one side of the cabinet to the other? I get that it depends, but let's just take a look at some spots I've identified as potentially being in need of bracing.
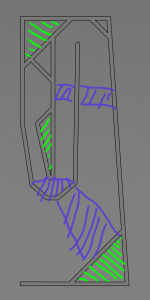
The purple sections are where I would run braces parallel to the sides, just to give a bit of extra support to the folds and such. Would most likely end up being thinner, laser-cut pieces to not eat up too much volume.
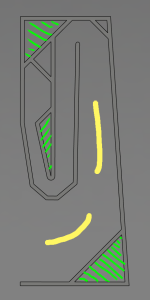
The yellow sections indicate areas where i might want to add bracing from side to side. Ideally they'd be placed further towards the mouth, but i don't really like the look of it.
Does this seem decent, or tawdry? Sincerely appreciate the help you guys have offered, I'm excited about this!
Last edited by a moderator:
Well, it's a 'substitute for the crate's 'lashing' to a pallet', so in theory no need for weight in the bottom, but as I noted in my cardboard box BLH I weighted the bottom some and also recommended either a removable massive base or outrigger stand, so yes if it's a significant amount, though still need enough to preload the cab or make it so @#$%^ rigid it winds up making the cab extremely heavy.
IOW, you can make it light and add weight or need a manual forklift to move it as it takes a lot of mass to thoroughly damp (make inert) any significant bass output and why 'we' normally try to raise the cab's Fs to ~an octave above a (sub) bass speaker's passband, which IME winds up around 1 kHz rather than push it below its passband a similar amount (~7-15 Hz).
IOW, you can make it light and add weight or need a manual forklift to move it as it takes a lot of mass to thoroughly damp (make inert) any significant bass output and why 'we' normally try to raise the cab's Fs to ~an octave above a (sub) bass speaker's passband, which IME winds up around 1 kHz rather than push it below its passband a similar amount (~7-15 Hz).
Re bracing; in general we want ~71% of the span braced and offset from the ends to randomize it and offset at some golden or acoustic ratio across it width.
That said, with a horn we want rigidity above all else, so as Dave noted, full length in general, but at the terminus/mouth it ideally needs to stop short to ensure no HF 'multicell disruption' for lack of a better description ATM.
Re 'holey' panels, never done or even read any research on these other than in muffler design, but personally wouldn't want any 'HF' disruption in a horn's path and judging by what the pioneers did and still do to this day in prosound horn design is either make it solid or as open as practical just as is shown in the above link.
That said, with a horn we want rigidity above all else, so as Dave noted, full length in general, but at the terminus/mouth it ideally needs to stop short to ensure no HF 'multicell disruption' for lack of a better description ATM.
Re 'holey' panels, never done or even read any research on these other than in muffler design, but personally wouldn't want any 'HF' disruption in a horn's path and judging by what the pioneers did and still do to this day in prosound horn design is either make it solid or as open as practical just as is shown in the above link.
Right, so the removable concrete casettes might be a good idea then. But I presume this would be in addition to an assumed minimum material thickness of 0.75"? Or could I go with something like 1/2" ply if I load it up lots?IOW, you can make it light and add weight or need a manual forklift to move it as it takes a lot of mass to thoroughly damp
I'm not sure I follow. When you say "~71% of the span" you mean 71% of the total acoustic path length having braces along the X-axis? Or Y/Z-axis? And with the golden ratio offset, you mean I should try to not place any Y/Z-braces dead center in the enclosure, but rather offset them?Re bracing; in general we want ~71% of the span braced and offset from the ends to randomize it and offset at some golden or acoustic ratio across it width.
I get that it's hard to explain without some sort of visual reference, so If there's some thread or document you have kicking around that might clear it up for me I'd be more than happy tackling that, rather than taking up a bunch of your time.
Either way, posted a pic below for axis reference. Holey bits are entirely arbitrary and will be optimized at a later time.
I think the "path" figure used might be a tad shorter, ie the distance between the speaker and mouth centres. I see the dip in (hornresp) around the 100-200 hz in a lot of the BLH horns that act as hybrid TL/horns. Not sure how it would manifest in the room at the listening position, as I haven't managed to settle on a design yet to build and never had the chance to listen to one. I think I am leaning towards a design where the mouth is at the rear of the enclosure.
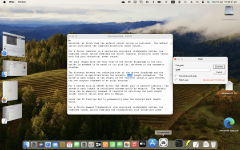
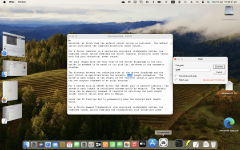
Right, so the removable concrete casettes might be a good idea then. But I presume this would be in addition to an assumed minimum material thickness of 0.75"? Or could I go with something like 1/2" ply if I load it up lots?
I'm not sure I follow. When you say "~71% of the span" you mean 71% of the total acoustic path length having braces along the X-axis? Or Y/Z-axis? And with the golden ratio offset, you mean I should try to not place any Y/Z-braces dead center in the enclosure, but rather offset them?
Yes, definitely need enough total mass to be inert and pre-stressed/coupled to the floor and as I noted, you can build it out of cardboard if you brace it enough. IOW it needs to 'ring' outside of its bandwidth, so either much heavier or much stiffer and since in the bass it's a lot less work, etc., to raise it with historically ~an octave** above its Fhm is sufficient.
'Span' = longest length
Yes, ~71% (0.707x) is to keep from developing joint 'hot spots' and offset some also to further randomize it
Correct
Yeah, keep telling myself to do a bracing write-up, though searching me you'll maybe find most of what I know that you need to know; can't remember if I've posted more here or on the original full range forum or the late 'basslist'.
**
Fh = Fl*2^n
Fl = Fh/2^n
n = ln(Fh/Fl)/ln(2)
where:
Fh = upper frequency
Fl = lower frequency, or the XO point in this case
n = octave spread
ln(2) = 0.6931
- Home
- Loudspeakers
- Full Range
- Modified Beta 8 BLH Design? Help!