The scary one is the strong resonance introduced at 500 Hz. Unlike the higher ones, this probably has a chance at being excited (what is the planned XO).
Did you do anything else inbetween other than the damping? Any differences in the way the removed woofer was reinstalled?
Neat how you do those blink things 🙂
Crossover will coincide with baffle step - I haven't calculated yet but I expect somewhere around 250-300Hz.
One thing is that output is lower again by a couple db so that 500Hz might be at the same level as in earlier plots.
No real difference in the way I put in the woofer - it is held in with 10-24 bolts into t-nuts and has no gasket yet. I did move the accelerometer slightly - I was losing adhesion due to a grease spot from the duct seal.
The hot melt glue works great but it removes some of the hardboard surface when I remove it. Not a big deal as these boxes will be veneered.
My dream damping mechanism involves external bracing.
You have me thinking...more for appearance than for actual bracing but what if I add ribs on the outside, laterally. It would take on the Battlestar Galactica look:
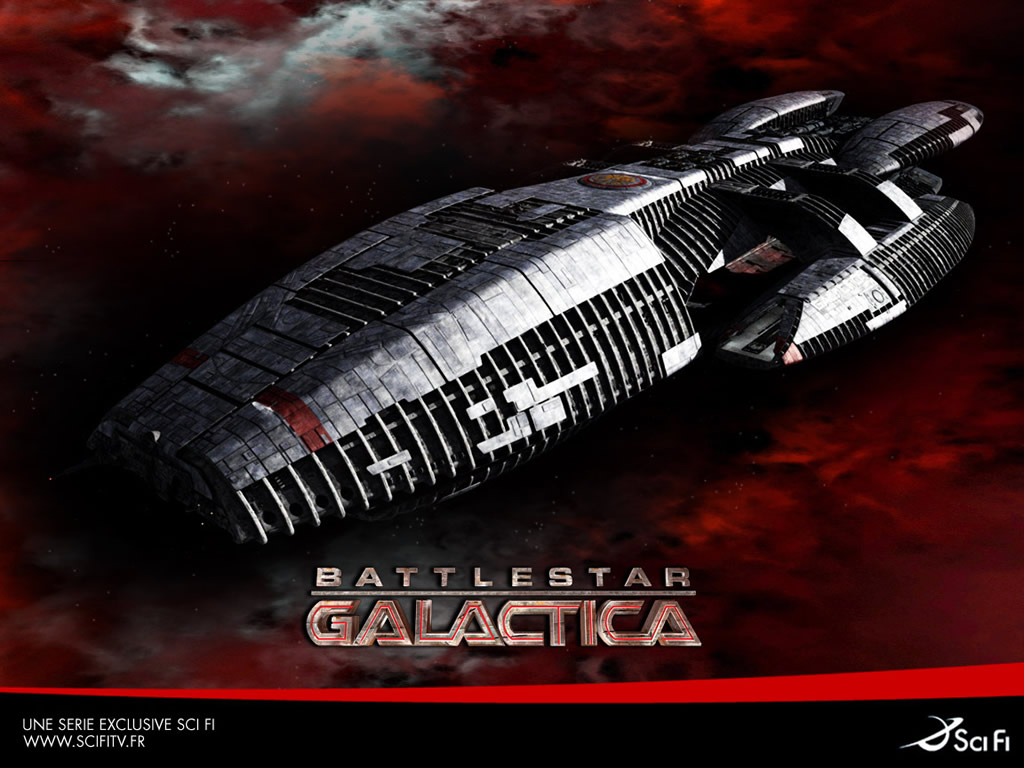
Veneer underneath, black ribs.
😎
You have me thinking...more for appearance than for actual bracing but what if I add ribs on the outside, laterally. It would take on the Battlestar Galactica look:
![]()
Veneer underneath, black ribs.
😎
Is that vented?
The ship or the speaker? 😀
Speaker is vented.
Oh, silly me! I thought that was a speaker! 😀
Also I would like to develop a way to mechanically isolate the driver frame from the enclosure. I'm convinced that much of what I'm seeing on the measurements are direct mechanical contribution from the drivers.
No comment on this Dave?
I'm toying with the idea of cutting a void through the sub-baffle around the woofer, say 1/4" to 3/8" wide and filling that with silicone (yes, I love silicone 🙂 ). How effective would this be in cutting down mechanical vibration from the basket to the baffle? Obviously I'd need to do a similar isolation at the magnet where it meets the central brace.
This I need to try but on a mock up, rather than this speaker. Tomorrow being "family day" here, it's a holiday - a good day to play around with this idea.
Lord. Just pour a cabinet out of reinforced cement and be done with it. 😀
I could but that would be boring.
There is also the prospect of active vibration cancellation. Accelerometers would be mounted on each panel in the box, they would feed several amplifiers that would in turn drive transducers that would excite the panels with an inverse signal which would cancel the resonance...

No comment on this Dave?
It doesn't work. The energy has to go somewhere. If you can successfully isolate the driver (unlikely) then all the energy is going to have to be dissipated in the driver itself which is going to excite everything potentially nasty that there is in the driver.
Follow that far enuff and you get back to active vibration cancelation via a pair of tightly coupled push-push drivers. Done well it should reduce mechanical box loads to the order of 10% of the same drivers facing the same way.
dave
There is also the prospect of active vibration cancellation. Accelerometers would be mounted on each panel in the box, they would feed several amplifiers that would in turn drive transducers that would excite the panels with an inverse signal which would cancel the resonance...![]()
Wouldn't push-push be a whole lot simplier?
(see John run out to the shop to construct a simple push-push test box)
dave
It doesn't work. The energy has to go somewhere.
The silicone is the damping layer - it goes there, at least (hopefully) a lot of it.
I still have one of those test boxes from the materials discussion thread, I'll stick a driver in that and test it, then I do the isolation procedure and test it again and see what the difference is, if any.
Wouldn't push-push be a whole lot simplier?
(see John run out to the shop to construct a simple push-push test box)
dave
It is but the mechanical energy will not be completely canceled and will be transfered to any panel that is rigidly attached to the driver frame.
I wasn't really serious about the active scheme...yet 🙂
It is but the mechanical energy will not be completely canceled and will be transfered to any panel that is rigidly attached to the driver frame.
A whole lot more mass & damping in those panels to dissipate the energy than in the basket alone.
Besides you will never achieve complete decoupling.
dave
The silicone is the damping layer - it goes there, at least (hopefully) a lot of it.
There we are, We can now use response 4 in the poll 🙂
dave
Wouldn't push-push be a whole lot simplier?
(see John run out to the shop to construct a simple push-push test box)
There we are, We can now use response 4 in the poll 🙂
These are rather weak attempts at humour Dave, I'm disappointed. 🙁
No comment on this Dave?
I'm toying with the idea of cutting a void through the sub-baffle around the woofer, say 1/4" to 3/8" wide and filling that with silicone (yes, I love silicone 🙂 ). How effective would this be in cutting down mechanical vibration from the basket to the baffle? Obviously I'd need to do a similar isolation at the magnet where it meets the central brace.
This I need to try but on a mock up, rather than this speaker. Tomorrow being "family day" here, it's a holiday - a good day to play around with this idea.
John, see this link:Dipole Main Panel
Apparently SL believes it helps.
John
- Status
- Not open for further replies.
- Home
- Loudspeakers
- Multi-Way
- Large 3-ways design / build