Cured silicone is inert, but most common silicone caulks use something like acetic acid as a curing agent.Silicone (polydimethylsiloxane, precisely speaking) is inert. So inert you could eat it (E900 additive). We use it to improve sealing on
https://siliconedepot.com/blog/do-you-need-acetoxy-silicone-or-neutral-cure-silicone/
Petter, cant you also do a dedicated thread to your build - it would be interesting to follow 🙂
//
//
I was speaking about the other kind of silicone - non-curing, stable silicone oil, clear viscous liquid. Polydimethylsiloxane.Cured silicone is inert, but most common silicone caulks use something like acetic acid as a curing agent.
Unfortunately, store-bought products almost never use proper terminology, so misunderstandings happen.
We get different thicknesses of gasket paper and gasket sheet here, quite cheap, the thicker ones are sold by the kilo.
The thinnest one would be about 4x thickness of 70 grams/square meter paper.
Price starts about 15 cents for a half news paper size sheet.
The black material in above post #15 is commonly used for head and manifold gaskets, should be easy to obtain.
The issue with silicon is the fact that it degrades over time, particularly in hot areas.
And such a thin layer is hard to apply.
Liquid ruber gasket is also used to bond / seal motorcycle engine halves together, you could try that, it is light grey in color, quite different from contact cement.
The thinnest one would be about 4x thickness of 70 grams/square meter paper.
Price starts about 15 cents for a half news paper size sheet.
The black material in above post #15 is commonly used for head and manifold gaskets, should be easy to obtain.
The issue with silicon is the fact that it degrades over time, particularly in hot areas.
And such a thin layer is hard to apply.
Liquid ruber gasket is also used to bond / seal motorcycle engine halves together, you could try that, it is light grey in color, quite different from contact cement.
Last edited:
Hey guys, anybody have some before and after measurements showing the effects of sealing?
(I have to confess I've never been able to measure what I'd call a significant difference....)
thx, mark
(I have to confess I've never been able to measure what I'd call a significant difference....)
thx, mark
I had a dip on a printed horn that was most probably related to lack of sealing / leak in the throat area. Never managed to fix it to see if it was really it🙂
Your "throat" profile looks a bit wrong ATM. Try starting it with a vertical segment right at the surround with height about equal to the height of the surround. Kind of like this:
A lot of great info can be found in this thread:
https://www.diyaudio.com/community/threads/open-source-waveguides-for-cnc-3d-printing.318190/
Why not roll in the edge so that the far (non-radiating) part of the surround is covered up as well? Is essentially dead space and will let the waveguide start a bit closer to the actual origin
Back in my karting days (...40 years ago...), to fine-tune the ignition chamber volume, we used gasket paper between carter and cylinder block, easily available in thickness steps of 0.1mm. Some added a thin layer of grease or lubricant just for the peace of mind.
I don't think things have changed since.
I don't think things have changed since.
It doesn't seem to work well, covering outer half of the surround messes up the top octave. Surrounds are non-pistonic, so simulation is less reliable, but commercial WGs for dome radiators never cover anything, which kinda proves Axidriver results.Why not roll in the edge so that the far (non-radiating) part of the surround is covered up as well? Is essentially dead space and will let the waveguide start a bit closer to the actual origin
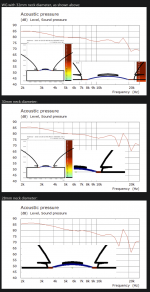
https://www.diy-hifi-forum.eu/forum...547e102b2ed8bb&p=192332&viewfull=1#post192332
OTOH, even 2 mm gap is allowable, and 2 mm vertical standoff appears to work best (at least on the SB26 alu dome).
![2018-05-01_Elliptical_WG_Kontur_V2_SB26ADC_neu_Step0-5mm_image_1a[1].png 2018-05-01_Elliptical_WG_Kontur_V2_SB26ADC_neu_Step0-5mm_image_1a[1].png](https://www.diyaudio.com/community/data/attachments/1053/1053792-01d964c58bf333a90956cc51fb7b6df3.jpg?hash=AdlkxYvzM6)
![2018-05-01_Elliptical_WG_contour_V2_spline_SB26ADC_neu_Step_0-5mm_1[1].jpg 2018-05-01_Elliptical_WG_contour_V2_spline_SB26ADC_neu_Step_0-5mm_1[1].jpg](https://www.diyaudio.com/community/data/attachments/1053/1053791-c0180143fe5cd474e2d48e078f226a16.jpg?hash=wBgBQ_5c1H)
https://www.diyaudio.com/community/...uides-for-cnc-3d-printing.318190/post-5425755
Kudos to @Gaga for thorough numerical investigations.
This is an old trick one might have learned on the farm.
You can make a custom gasket that will conform to any irregularities in the surfaces. Use two pieces of parchment or wax paper with a smear of silicone caulk between. Tighten very lightly into your application. Allow to set. Mark the orientation of the gasket (important). Remove and trim to size. When mounting you have the choice of removing the paper and using only the silicone if you wish. This time tighten as you would normally.
I have done this many times for a number of different uses including automotive applications. If you can't use paper layers, you deliberately contaminate one of the surfaces to act as a release agent. It's important to only tighten softly when forming the gasket to allow for compression during final tightening
You can make a custom gasket that will conform to any irregularities in the surfaces. Use two pieces of parchment or wax paper with a smear of silicone caulk between. Tighten very lightly into your application. Allow to set. Mark the orientation of the gasket (important). Remove and trim to size. When mounting you have the choice of removing the paper and using only the silicone if you wish. This time tighten as you would normally.
I have done this many times for a number of different uses including automotive applications. If you can't use paper layers, you deliberately contaminate one of the surfaces to act as a release agent. It's important to only tighten softly when forming the gasket to allow for compression during final tightening
https://www.ebay.com/itm/2552650167...ivdhwvs7NS+vK3b5Qx+ky6xK76|tkp:Bk9SR7LMpP7PYQ
Compresses to very thin.
Compresses to very thin.
Very easy and cheap trick is to cut a nitrile rubber glove apart and use the flat part to cut out a gasket. Use the WG flange to mark out the pattern. I do this on all the drivers which don't have a gasket.
Another easy and quick way is to use blue painters tape. One or two layers will do the job, evenly placed on the WG flange and trim with a razor blade when done.
If the WG is a little bit wavy, take a sheet of roughly 320.grit wet/dry sand paper placed.on a glass table top or other known flat surface and sand the flange in a circulat motion to flatten it. You'll see the progress as you go based on the amount of sanded surface area. When it's flat enough, wipe it thoroughly clean with a moistened paper towel and you're done.
Another easy and quick way is to use blue painters tape. One or two layers will do the job, evenly placed on the WG flange and trim with a razor blade when done.
If the WG is a little bit wavy, take a sheet of roughly 320.grit wet/dry sand paper placed.on a glass table top or other known flat surface and sand the flange in a circulat motion to flatten it. You'll see the progress as you go based on the amount of sanded surface area. When it's flat enough, wipe it thoroughly clean with a moistened paper towel and you're done.
The thin foam sheet used for packing fragile items like miniature tube lights will work, it is LDPE foam, about 1 mm thick.
Basically you are trying to seal a small gap...for that matter the sealant sold to fill gaps in auto panels will also work.
The one I have in mind is used to seal between panel before spot welding, I think it is called under body sealant.
If you do not intend to dismantle it, epoxy putty will work, and some materials are hard to stick, so there you are.
Even a toothpaste carton type stiff paper should be adequate.
Basically you are trying to seal a small gap...for that matter the sealant sold to fill gaps in auto panels will also work.
The one I have in mind is used to seal between panel before spot welding, I think it is called under body sealant.
If you do not intend to dismantle it, epoxy putty will work, and some materials are hard to stick, so there you are.
Even a toothpaste carton type stiff paper should be adequate.
I forgot about the aluminum adhesive tape used to seal HVAC duct work. That stuff has a million uses. One layer will do and its very pliable to take up uneven surfaces.
So in essence virtually anything thin and flat will work. Just make sure both surfaces are flat. Otherwise you'll end up with damage. I would stay away from anything liquid that has to dry. Just safer to not use chemical sealants that can cause problems later when trying to remove stuff..
So in essence virtually anything thin and flat will work. Just make sure both surfaces are flat. Otherwise you'll end up with damage. I would stay away from anything liquid that has to dry. Just safer to not use chemical sealants that can cause problems later when trying to remove stuff..
I'd go for gasket-paper 0.6~1mm thick, if the surfaces are not perfectly flat, yet not too uneven.
It is hard to tear, and will not deform laterally even if strongly tightened.
It is mildly compressible and will fill small surface irregularities, yet it's not springy and will cause less vibration than rubber for example, if loosely tightened.
https://www.ramgaskets.com/gasket-materials/gasket-paper/
https://www.ramgaskets.com/gasket-materials/
It is hard to tear, and will not deform laterally even if strongly tightened.
It is mildly compressible and will fill small surface irregularities, yet it's not springy and will cause less vibration than rubber for example, if loosely tightened.
https://www.ramgaskets.com/gasket-materials/gasket-paper/
https://www.ramgaskets.com/gasket-materials/
- Home
- Loudspeakers
- Multi-Way
- How to seal between the mounting plate and waveguide?