I realize that I'm a little off topic here, not being specific to audio power. This trafo is however going to be used to power an aluminum casting furnace that is to be used for casting misc. audio components.
Here's what I need:
110V 1phase primary to around 1-6 volts secondary, with high current handling on the secondary.
What I did:
Coiled a 5" wide 'slit' of Arnon7 NGOES electrical steel into approx. 4.5 ID x 6 OD by 5" tall. Taped in place using high temp. flash tape. Wrapped single layer of aluminized fiberglass and taped in place with flash tape. Wound 12awg magnet wire to 110 turns. Wound 4awg single turn secondary. Applied power....SPARKS. Removed secondary and checked for shorts. No shorts found. Added 30amp fuse wire to primary (plus 20amp mains breaker) (no secondary winding) and applied power. No fuses/breakers tripped but the enamel burned off at exactly the mid point in the winding. This further confirms my belief that a short is not the issue (regarding bare wires in contact, I mean).
Okay, now what? The main thing I am aware of is that my aspect ratio is very bad, approx 1:1. And I know that 2:1 is optimal, or 1:2, depending on how you frame the definition. Is this the issue? Or am I way off kilter elsewhere too? I know that the Arnon material is pretty exotic stuff so maybe that is not helping matters either?
What to do? I had originally planned to coil the Arnon and then saw it into two cores for the ideal geometry, will that perhaps solve the problem?
Here's what I need:
110V 1phase primary to around 1-6 volts secondary, with high current handling on the secondary.
What I did:
Coiled a 5" wide 'slit' of Arnon7 NGOES electrical steel into approx. 4.5 ID x 6 OD by 5" tall. Taped in place using high temp. flash tape. Wrapped single layer of aluminized fiberglass and taped in place with flash tape. Wound 12awg magnet wire to 110 turns. Wound 4awg single turn secondary. Applied power....SPARKS. Removed secondary and checked for shorts. No shorts found. Added 30amp fuse wire to primary (plus 20amp mains breaker) (no secondary winding) and applied power. No fuses/breakers tripped but the enamel burned off at exactly the mid point in the winding. This further confirms my belief that a short is not the issue (regarding bare wires in contact, I mean).
Okay, now what? The main thing I am aware of is that my aspect ratio is very bad, approx 1:1. And I know that 2:1 is optimal, or 1:2, depending on how you frame the definition. Is this the issue? Or am I way off kilter elsewhere too? I know that the Arnon material is pretty exotic stuff so maybe that is not helping matters either?
What to do? I had originally planned to coil the Arnon and then saw it into two cores for the ideal geometry, will that perhaps solve the problem?
Attachments
Did you size the primary winding according to the geometric properties (mainly Ae) and magnetic properties (mainly Bsat) of the core?
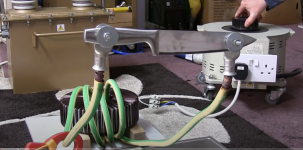
I sized the primary in relation to the expected current draw, <10 amps, and the required id of the core to fit adequate wire gauge of the primary.
Arnon is kind of a weird animal and I couldn't figure out the Bsat. I know it's NGOES and has a relatively high silicon content. But all their spec looks different to the basic parameters I found on the toroid calculators.
I just figured out the basic minimum size and slapped it together and crossed my fingers. But in terms of what to do correctly I wouldn't even know where to start.
Photonicinduction on youtube used a similar approach to melt a knife. Looking at his unit, in hindsight, it appears he has about twice the steel in his trafo. But he his pulling 1000 amps, and I just need about 100 on the secondary.
Edit: If the design requires significant study and wherever I went wrong is not some "Doh" stupid error; can I talk someone into sorting it out for a little horse trading? I can swap time for Solidworks modeling and Keyshot rendering, hour for hour, if I can just get a definitive "do this" explanation. Will provide Arnon spec. if needed. Keyshot/Cad example attached...
Attachments
Last edited:
What is the cross-section of your toroid? That's what will govern the number of turns of the primary. You are currently at ~1V/turn, which looks very large but not completely impossible if the iron is large enough.
The output current has nothing to do with the primary turns number. You have to sort that out first.
I recommend you search the net for "transformer design", you need to get your basics right, otherwise you will continue to make sparks and melt copper for a long time before you arrive at something workable
The output current has nothing to do with the primary turns number. You have to sort that out first.
I recommend you search the net for "transformer design", you need to get your basics right, otherwise you will continue to make sparks and melt copper for a long time before you arrive at something workable
Thanks for the continued feedback, Elvee!
Regarding the primary vs secondary current, yes I'm aware, I may have stated something awkwardly there. Regarding current, I'm just assuming total power, I know I need lv/high current on the secondary. I took total pwr and translated that to the primary side @120v and the current was fairly negligible on the primary. 12awg is a little on the anemic side but the resistive load rises with temp, and so the peak current is limited to the warmup phase.
Core cross section is ~1" x 5" so 5in^2.
Regarding the primary vs secondary current, yes I'm aware, I may have stated something awkwardly there. Regarding current, I'm just assuming total power, I know I need lv/high current on the secondary. I took total pwr and translated that to the primary side @120v and the current was fairly negligible on the primary. 12awg is a little on the anemic side but the resistive load rises with temp, and so the peak current is limited to the warmup phase.
Core cross section is ~1" x 5" so 5in^2.
You are not that far away: assuming a filling factor of 0.9 and a maximum induction of 1 tesla, you need 160 primary turns.
This means that you just need to add ~50turns to avoid saturation.
Before you go further, check that estimation by feeding the primary ~70V, using a variac, autoformer or anything else suitable.
Use a dim light bulb tester in series (always for tests!), and measure the current: it shouldn't exceed one or two hundreds of mA. If it does, there is something wrong with the assumptions
This means that you just need to add ~50turns to avoid saturation.
Before you go further, check that estimation by feeding the primary ~70V, using a variac, autoformer or anything else suitable.
Use a dim light bulb tester in series (always for tests!), and measure the current: it shouldn't exceed one or two hundreds of mA. If it does, there is something wrong with the assumptions
@Osvaldo de
I'll describe exactly what happened in case something sticks out-
-First powerup: Energized at breaker (60A) and a very bright spark emitted. Instantly turned breaker off. The spark was like a flash and I thought it came frim the ID of the coil. Mains cable was connected via wire nuts. A single turn flexible copper 4awg cable had a single turn around the center, farthest distance from the beginning/end of the primary.
-Second attempt: Removed secondary. Connected only one leg. Took second leg and with long pliers and scraped the other leg. Bright welding type arcs came off the connection making intermittent contact. So bright I had to switch to torch goggles. No sign of shorting or sparks anywhere on the coil (aside from the connection).
-Third attempt. No noticeable damage/shorting on the primary prior to test. Wired 30A fuse between coil and mains. Stepped mains breaker down to 20A. Added 30A fused throw lever. Energized. No sparks. Energized for a longer duration. No sparks. Energized a third time, no sparks--smoke emerged from coil. The majority of the coil was cool to the touch. But the at the center point you could feel the heat and this is where the enamel cooked and obviously smoked.
I can't guarantee nothing was shorted in the coil. But no visual evidence, and the fact that the winding heated at dead center along the winding seemed suspicious. The areas that cooked, in the center, showed no prior signs of being shorted.
I've attached some spec. on the core material in case there's something there-
I'll describe exactly what happened in case something sticks out-
-First powerup: Energized at breaker (60A) and a very bright spark emitted. Instantly turned breaker off. The spark was like a flash and I thought it came frim the ID of the coil. Mains cable was connected via wire nuts. A single turn flexible copper 4awg cable had a single turn around the center, farthest distance from the beginning/end of the primary.
-Second attempt: Removed secondary. Connected only one leg. Took second leg and with long pliers and scraped the other leg. Bright welding type arcs came off the connection making intermittent contact. So bright I had to switch to torch goggles. No sign of shorting or sparks anywhere on the coil (aside from the connection).
-Third attempt. No noticeable damage/shorting on the primary prior to test. Wired 30A fuse between coil and mains. Stepped mains breaker down to 20A. Added 30A fused throw lever. Energized. No sparks. Energized for a longer duration. No sparks. Energized a third time, no sparks--smoke emerged from coil. The majority of the coil was cool to the touch. But the at the center point you could feel the heat and this is where the enamel cooked and obviously smoked.
I can't guarantee nothing was shorted in the coil. But no visual evidence, and the fact that the winding heated at dead center along the winding seemed suspicious. The areas that cooked, in the center, showed no prior signs of being shorted.
I've attached some spec. on the core material in case there's something there-
Attachments
You are not that far away: assuming a filling factor of 0.9 and a maximum induction of 1 tesla, you need 160 primary turns.
This means that you just need to add ~50turns to avoid saturation.
Before you go further, check that estimation by feeding the primary ~70V, using a variac, autoformer or anything else suitable.
Use a dim light bulb tester in series (always for tests!), and measure the current: it shouldn't exceed one or two hundreds of mA. If it does, there is something wrong with the assumptions
Okay, good info. I wish I had a variac, but I may be able to use some other transformers to get into a more safe voltage for experimenting. I'll have to study your suggestions some and ponder how to proceed.
I did drum up some info on the Arnon, if it makes a difference (posted in the prev. response). Thx again-
Your material is good to 10~12kG, that's 1~1.2T, so my calculation remains valid, it will get you a small safety margin.
Thus, all you should have to do is add 50 turns to get an operational primary. But make the transformer test anyway.
Thus, all you should have to do is add 50 turns to get an operational primary. But make the transformer test anyway.
- Home
- Amplifiers
- Power Supplies
- General Toroid Trafo Question