The Dissipante Chassis
With the bulk of the soldering behind me, I turned to the chassis and did a trial assembly. First I sorted all the fasteners . . . there were five different varieties of machine screw and some plain nuts (no washers of any kind), but it wasn't difficult to figure out what went where. I had fifteen screws left over!
I assembled everything finger-tight and then snugged all the panels together. It all fitted quite well, except that the corner brackets that connect all the panels and heat sinks together were slightly short - I had to shim the rear panel with washers, otherwise it deformed when the screws were tightened.
I started laying out all the sub-assemblies in their general positions. As I've already mentioned, even a 400 mm deep chassis is tight on space along the heat sinks, especially when space needs to be allowed for wiring and connectors, so I was a little perturbed to discover that the aforementioned brackets were not as shown in the Sketchup drawing that I had been using for my layouts. The plain brackets in my drawing turned out to increase in width at the ends. I wanted to use the top edges of the brackets to locate my Modulus-686 amps and Power-686 power supplies, but the sloping transitions were getting in the way. Fortunately, a few minutes with a hacksaw and file solved the problem without compromising the strength of the brackets significantly.
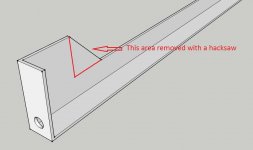
With the chassis reassembled with the modified brackets, it was a simple matter to hold each subassembly in position and mark the locations of the mounting holes on the heat sinks. I was pretty confident about the position of the transformer and Intelligent Soft Start on the bottom panel, so I laid those out by measurement along with four holes for the feet and a few others for ground connections. Now I was ready to move to the drill press.
The bottom panel was easy enough, although I was a little disappointed with the quality of the aluminum alloy which didn't drill very cleanly. However, the heat sinks were better. All the mounting holes in the heat sinks are blind holes that have to be drilled with tapping drills and then threaded by hand with M3 and M4 taps. I had another surprise here when the heat sinks turned out to be thinner than shown on my drawing, which meant that all the mounting screws that I had already bought were going to be too long.
It's worth buying decent quality taps for tapping the heat sinks. Taps are brittle and break easily - especially ones as small as M3 - and a broken tap is usually almost impossible to remove. I used a mixture of kerosene and linseed oil (both of which I happened to have to hand) as a lubricant. I also used a bottom tap after the taper tap to get a little extra usable thread in the blind holes. After I had completed all the holes, I took advantage of the two-piece heat sinks by dunking them in my ultrasonic cleaner. They were a tight fit, but close enough.
Next: starting the assembly process.
With the bulk of the soldering behind me, I turned to the chassis and did a trial assembly. First I sorted all the fasteners . . . there were five different varieties of machine screw and some plain nuts (no washers of any kind), but it wasn't difficult to figure out what went where. I had fifteen screws left over!
I assembled everything finger-tight and then snugged all the panels together. It all fitted quite well, except that the corner brackets that connect all the panels and heat sinks together were slightly short - I had to shim the rear panel with washers, otherwise it deformed when the screws were tightened.
I started laying out all the sub-assemblies in their general positions. As I've already mentioned, even a 400 mm deep chassis is tight on space along the heat sinks, especially when space needs to be allowed for wiring and connectors, so I was a little perturbed to discover that the aforementioned brackets were not as shown in the Sketchup drawing that I had been using for my layouts. The plain brackets in my drawing turned out to increase in width at the ends. I wanted to use the top edges of the brackets to locate my Modulus-686 amps and Power-686 power supplies, but the sloping transitions were getting in the way. Fortunately, a few minutes with a hacksaw and file solved the problem without compromising the strength of the brackets significantly.
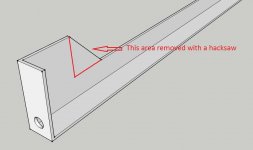
With the chassis reassembled with the modified brackets, it was a simple matter to hold each subassembly in position and mark the locations of the mounting holes on the heat sinks. I was pretty confident about the position of the transformer and Intelligent Soft Start on the bottom panel, so I laid those out by measurement along with four holes for the feet and a few others for ground connections. Now I was ready to move to the drill press.
The bottom panel was easy enough, although I was a little disappointed with the quality of the aluminum alloy which didn't drill very cleanly. However, the heat sinks were better. All the mounting holes in the heat sinks are blind holes that have to be drilled with tapping drills and then threaded by hand with M3 and M4 taps. I had another surprise here when the heat sinks turned out to be thinner than shown on my drawing, which meant that all the mounting screws that I had already bought were going to be too long.
It's worth buying decent quality taps for tapping the heat sinks. Taps are brittle and break easily - especially ones as small as M3 - and a broken tap is usually almost impossible to remove. I used a mixture of kerosene and linseed oil (both of which I happened to have to hand) as a lubricant. I also used a bottom tap after the taper tap to get a little extra usable thread in the blind holes. After I had completed all the holes, I took advantage of the two-piece heat sinks by dunking them in my ultrasonic cleaner. They were a tight fit, but close enough.
Next: starting the assembly process.
TiN coated taps are awesome. I have some with spiral flutes that I bought from McMaster-Carr. Those and A-9 aluminum cutting fluid (not to be confused with A-1 steak sauce) makes drilling and tapping the holes a breeze. I use a tapping block to keep the tap perpendicular to the heat sink.
Tom
Tom
Assembly and Wiring - the Power Components
I started by fitting the feet (supplied with the chassis) so that I didn't scratch the underside of the bottom panel of the chassis while sliding it around on my bench. The feet are quite serviceable, although it would have been nice if they had a soft insert (they're just hard plastic).
Then I fitted the Intelligent Soft Start (ISS) board in the middle of the bottom panel using M3 machine screws, spacers, and lock nuts. I thought I might want to run wiring underneath the board, so I made sure that there were no sharp pins protruding. As it turned out, this was an unnecessary precaution.
Next I mounted the Power-686 power supply boards and brackets to the heat sinks. I decided to use socket cap screws at all the mounting points on the heat sinks. I knew that access was going to be tight, and I have a set of ball-end socket cap screwdrivers. The latter are much more positive than cross-head screwdrivers and are designed to tolerate some misalignment. I used spring washers on plain washers to ensure that the screws stay put.
I mounted the transformer on four polyurethane bumper feet from Lee Valley (00S2021). I've used these quite often for speaker cabinets and know that they last. Apart from letting air circulate around the transformer, which must surely be a good thing, they allowed me to mount the transformer "upside down", i.e. with all the wires at the bottom. I had to buy a longer M8 bolt to accommodate the extra height, but it helped enormously in keeping the power wiring tidy. It also allowed me to run wires under the transformer from the ISS to the on/off switch and power LEDs on the faceplate.
I had to get power from the green and blue wires from the secondary windings of the transformer to two power supplies. These wires are 14 AWG and the terminal blocks on the power supply boards were too small to accept two wires, and I didn't want to use a big, ugly terminal strip. I found some similar wire at Home Depot, so I ran this from one power supply board to the other and spliced in the wires from the windings. I had to use a mini butane torch to get enough heat into each joint to get solder to flow. The whole thing was a minor battle, but the finished installation is quite neat.
Here's the transformer wired up to the power supply boards:
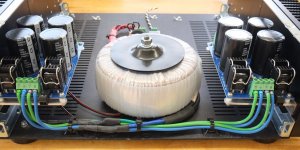
Next: the faceplate.
I started by fitting the feet (supplied with the chassis) so that I didn't scratch the underside of the bottom panel of the chassis while sliding it around on my bench. The feet are quite serviceable, although it would have been nice if they had a soft insert (they're just hard plastic).
Then I fitted the Intelligent Soft Start (ISS) board in the middle of the bottom panel using M3 machine screws, spacers, and lock nuts. I thought I might want to run wiring underneath the board, so I made sure that there were no sharp pins protruding. As it turned out, this was an unnecessary precaution.
Next I mounted the Power-686 power supply boards and brackets to the heat sinks. I decided to use socket cap screws at all the mounting points on the heat sinks. I knew that access was going to be tight, and I have a set of ball-end socket cap screwdrivers. The latter are much more positive than cross-head screwdrivers and are designed to tolerate some misalignment. I used spring washers on plain washers to ensure that the screws stay put.
I mounted the transformer on four polyurethane bumper feet from Lee Valley (00S2021). I've used these quite often for speaker cabinets and know that they last. Apart from letting air circulate around the transformer, which must surely be a good thing, they allowed me to mount the transformer "upside down", i.e. with all the wires at the bottom. I had to buy a longer M8 bolt to accommodate the extra height, but it helped enormously in keeping the power wiring tidy. It also allowed me to run wires under the transformer from the ISS to the on/off switch and power LEDs on the faceplate.
I had to get power from the green and blue wires from the secondary windings of the transformer to two power supplies. These wires are 14 AWG and the terminal blocks on the power supply boards were too small to accept two wires, and I didn't want to use a big, ugly terminal strip. I found some similar wire at Home Depot, so I ran this from one power supply board to the other and spliced in the wires from the windings. I had to use a mini butane torch to get enough heat into each joint to get solder to flow. The whole thing was a minor battle, but the finished installation is quite neat.
Here's the transformer wired up to the power supply boards:
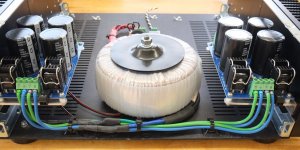
Next: the faceplate.
Preparing and Fitting the Faceplate
Of all the work involved in building this amplifier, the faceplate was the job I was dreading most. Somehow, I had to put a 16 mm diameter hole for the on/off switch through the 10 mm thick faceplate without scarring it for life. The moment had come.
The Power-686 power supply boards each have a small black connector (to the right of the green terminal blocks in the photo above) intended to drive an LED when there is power on the board. I decided to mount these in the faceplate either side of the on/off switch.
I started by marking the positions of the LEDs and on/off switch on the front of the faceplate and then drilling pilot holes at each position with a 3/32" drill (2.5 mm would be close enough) on my drill press. I then chucked a step drill and, with the faceplate firmly clamped to the table of the drill press, proceeded to work my way down to 5/8". I used a little kerosene mixed with linseed oil as a cutting fluid.
When I had gone as far as I could without breaking into the next diameter above 5/8", I turned the faceplate over, re-clamped it, and continued drilling. Drilling from both side didn't quite get me a clean hole all the way through - there was a small land remaining in the middle, but it was the work of only a few minutes with a round file to remove it.
I don't like bright lights on audio gear, so I decided to leave the 3/32" diameter holes on the front of the faceplate and to counter-bore from behind to house the body of the LEDs. With the faceplate clamped down again, I opened up the 3/32" holes with a 13/64" drill (5.16 mm). I kept testing the fit of the LED until the flange around its base just touched the surface of the faceplate - I didn't want to break through. When the holes were just deep enough. I cleaned the faceplate and then glued the LEDs into the holes with a little clear 5-minute epoxy.
I hadn't realised when I placed my order with Tom Christiansen at Neurochrome that his Intelligent Soft Start module has outputs intended to drive a two-colour LED, so that the LED will show one colour when on standby and the other colour when power is on. The intensity of each colour is adjustable via a pair of trim pots.
I had bought a switch with a single-colour illuminated ring. I also hadn't realised until Tom told me that the illuminated ring is on when the system is on standby as well as when the power is on. Fortunately, I will be able to use the trim pots on the ISS to adjust the brightness in both states. I intend to have a soft green glow from the switch when on standby, increasing to brighter green flanked by the pair of red LEDs when powered up.
With the faceplate lying flat in front of the chassis, I mounted the on/off switch and wired up the switch and the LEDs. Then I secured the faceplate to the chassis, checking that all the power wiring was not being subjected to undue strain as I went. This was another instance where I replaced the screws provided with button-head socket cap screws.
Here's the faceplate all ready for securing to the chassis:
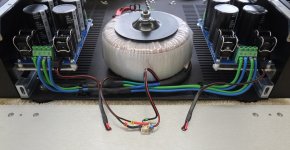
Next: the rear panel
Of all the work involved in building this amplifier, the faceplate was the job I was dreading most. Somehow, I had to put a 16 mm diameter hole for the on/off switch through the 10 mm thick faceplate without scarring it for life. The moment had come.
The Power-686 power supply boards each have a small black connector (to the right of the green terminal blocks in the photo above) intended to drive an LED when there is power on the board. I decided to mount these in the faceplate either side of the on/off switch.
I started by marking the positions of the LEDs and on/off switch on the front of the faceplate and then drilling pilot holes at each position with a 3/32" drill (2.5 mm would be close enough) on my drill press. I then chucked a step drill and, with the faceplate firmly clamped to the table of the drill press, proceeded to work my way down to 5/8". I used a little kerosene mixed with linseed oil as a cutting fluid.
When I had gone as far as I could without breaking into the next diameter above 5/8", I turned the faceplate over, re-clamped it, and continued drilling. Drilling from both side didn't quite get me a clean hole all the way through - there was a small land remaining in the middle, but it was the work of only a few minutes with a round file to remove it.
I don't like bright lights on audio gear, so I decided to leave the 3/32" diameter holes on the front of the faceplate and to counter-bore from behind to house the body of the LEDs. With the faceplate clamped down again, I opened up the 3/32" holes with a 13/64" drill (5.16 mm). I kept testing the fit of the LED until the flange around its base just touched the surface of the faceplate - I didn't want to break through. When the holes were just deep enough. I cleaned the faceplate and then glued the LEDs into the holes with a little clear 5-minute epoxy.
I hadn't realised when I placed my order with Tom Christiansen at Neurochrome that his Intelligent Soft Start module has outputs intended to drive a two-colour LED, so that the LED will show one colour when on standby and the other colour when power is on. The intensity of each colour is adjustable via a pair of trim pots.
I had bought a switch with a single-colour illuminated ring. I also hadn't realised until Tom told me that the illuminated ring is on when the system is on standby as well as when the power is on. Fortunately, I will be able to use the trim pots on the ISS to adjust the brightness in both states. I intend to have a soft green glow from the switch when on standby, increasing to brighter green flanked by the pair of red LEDs when powered up.
With the faceplate lying flat in front of the chassis, I mounted the on/off switch and wired up the switch and the LEDs. Then I secured the faceplate to the chassis, checking that all the power wiring was not being subjected to undue strain as I went. This was another instance where I replaced the screws provided with button-head socket cap screws.
Here's the faceplate all ready for securing to the chassis:
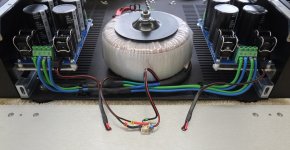
Next: the rear panel
I had bought a switch with a single-colour illuminated ring. I also hadn't realised until Tom told me that the illuminated ring is on when the system is on standby as well as when the power is on.
Yeah. An undocumented "feature" of the E-Switch PV6-series is that it has a bipolar LED even for the single colour options. The data sheet makes no mention of this and the switch body is clearly marked with + and -. Go figure.
As you point out, a quick turn of the STBY dimmer on the ISS turns the brightness to zero in standby mode. Or as bright as you want it.
Tom
I'm not a naturally showy person, so I surprised myself when I decided to keep the LED lit, albeit on low, when on standby.
I surprised myself even more by mounting the two power supply LEDs in the faceplate, bearing in mind that the benefit is marginal. I would have liked to use green ones to match the on/off switch, but couldn't find a green equivalent (but then I'm not very proficient at using Mouser's or Digikey's search filters).
I surprised myself even more by mounting the two power supply LEDs in the faceplate, bearing in mind that the benefit is marginal. I would have liked to use green ones to match the on/off switch, but couldn't find a green equivalent (but then I'm not very proficient at using Mouser's or Digikey's search filters).
Very well thought out build and a great commentary on it.
Just a couple of points.
Firstly:
Using a plain washer under a spring washer negates the effect of the spring washer locking the nut. You are effectively turning the nut, spring washer and plain washer into a single fastener which is free to come loose from the bolt.
Secondly:
You have installed the big top washer on the transformer upside down. The formed depression is meant to protrude down inside the center of the transformer. That way the fixing nut (or head of the bolt ) will not protrude above the height of the transformer.
Just a couple of points.
Firstly:
I used spring washers on plain washers to ensure that the screws stay put.
Using a plain washer under a spring washer negates the effect of the spring washer locking the nut. You are effectively turning the nut, spring washer and plain washer into a single fastener which is free to come loose from the bolt.
Secondly:
You have installed the big top washer on the transformer upside down. The formed depression is meant to protrude down inside the center of the transformer. That way the fixing nut (or head of the bolt ) will not protrude above the height of the transformer.
Thanks for your comments.
Just to be clear, my assembly order is nut, spring washer, plain washer, component. Threaded fasteners work by creating tension in the bolt or screw; this tension clamps the parts together. So the challenge is to maintain the tension and resist any torque that would tend to reduce it. This is the job of the spring washer. The spring washer is designed to slide on the adjacent surfaces when the fastener is being tightened, but to "dig in" to them and thus resist motion in the opposite direction. From this perspective, it makes little difference which washer is next to the nut. The function of the plain washer is to protect the surface of the component from excessive compressive load, damage from the rotating nut (in the absence of washers), and damage from the spring washer.
To your second point, well spotted. In this instance, I have plenty of headroom, but your point is well taken. There might not be enough thread on the bolt to invert the cap, but I'll take a closer look eventually.
Thanks again for your comments.
Just to be clear, my assembly order is nut, spring washer, plain washer, component. Threaded fasteners work by creating tension in the bolt or screw; this tension clamps the parts together. So the challenge is to maintain the tension and resist any torque that would tend to reduce it. This is the job of the spring washer. The spring washer is designed to slide on the adjacent surfaces when the fastener is being tightened, but to "dig in" to them and thus resist motion in the opposite direction. From this perspective, it makes little difference which washer is next to the nut. The function of the plain washer is to protect the surface of the component from excessive compressive load, damage from the rotating nut (in the absence of washers), and damage from the spring washer.
To your second point, well spotted. In this instance, I have plenty of headroom, but your point is well taken. There might not be enough thread on the bolt to invert the cap, but I'll take a closer look eventually.
Thanks again for your comments.
I would have liked to use green ones to match the on/off switch, but couldn't find a green equivalent (but then I'm not very proficient at using Mouser's or Digikey's search filters).
Broadcom HLMP-3507 (Mouser: 630-HLMP-3507) would be a good one.
In the past I've removed LEDs epoxied into faceplates by inserting a rod through the hole in the front and tapping it with a hammer. I use the same "small through hole, large counterbore" setup as you do. A piece of drill rod would be good for this.
Tom
Thanks for the tips.
I'll add a couple of those LEDs to my next buy-list anyway, although I think I'll live with the red for a while. These things usually become less important as time passes. It will probably end up being a wifely decision.
I'll add a couple of those LEDs to my next buy-list anyway, although I think I'll live with the red for a while. These things usually become less important as time passes. It will probably end up being a wifely decision.
Preparing the Rear Panel
The rear panel was another job that I wasn't looking forward to. Although only 3 mm thick instead of 10 mm like the faceplate, there were a lot more holes - and therefore a lot more potential for mistakes - and the two holes for the SpeakOn sockets were 31 mm diameter. Just to add a little additional complexity, each SpeakOn socket needed four screw holes, and each of the six XLR sockets needed two screw holes. Then there was the IED power entry module and two pairs of binding posts - thirty-five holes in all if I use a screw-on IEC. The job was unpleasantly messy, and it proved almost impossible to avoid marking the anodised surfaces. I used a 1.25" (31.75 mm) step drill for the SpeakOns and a 15/16" (23.8 mm) step drill for the XLRs. Never attempt something like this without a drill press and clamps!
I had originally intended holding everything in place using nuts and lock washers on the machine screws, but on impulse decided to try tapped holes instead. An M3 screw has a pitch of 0.5 mm, so even if the first thread is damaged, there should still be four full threads in 3 mm thick material. Using tapped holes has the advantages of being able to tighten the screws without having to struggle with access on the inside, and of there being no nuts and washers to fall off and get lost. The disadvantages are that your drilling has to be more precise and that it takes longer. As it turned out, tapping twenty-two M3 holes took me half an hour - time well spent for the frustration it will save.
After cleaning it up, I gave the panel a trial fit - remembering to include my shim washers to prevent the panel from being deformed. I couldn't resist loosely fitting a few connectors just to see how it was going to look.
I had spent a lot of time designing the layout of the rear panel, trying to keep everything away from everything else while avoiding an impossible wiring arrangement . As is usually the case, I was pleased with my final layout, but wondered why it had taken me so long to come up with it.
Predictably, the power enters in the middle. The XLR inputs for the tweeters, mids, and woofers are arranged vertically, reflecting their respective positions in a speaker cabinet, and also line up quite well with the input terminals on the amplifier modules. The SpeakOn output sockets are more or less centered in the space between the upper and lower amplifier modules, so that their terminals shouldn't be entirely impossible to connect to. The binding posts are a little more difficult, but not impossible.
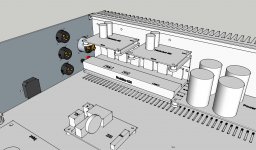
At this stage, I could test that the powers supplies were working properly. With the IEC power inlet connected to the Intelligent Soft Start module, all I had to do was to connect a power cord. Like magic, the on/off switch came to life. If you're old enough to remember tube radios, you'll remember the "magic eye". The on/off switch reminded me of that, only without the wait!
With a gentle press on the switch, the two red LEDs lit up as well. This was turning into a good day. The output terminals on both Power-686 modules showed 30.92 VDC on my multimeter. I was impressed.
Next: installing the amplifier modules.
The rear panel was another job that I wasn't looking forward to. Although only 3 mm thick instead of 10 mm like the faceplate, there were a lot more holes - and therefore a lot more potential for mistakes - and the two holes for the SpeakOn sockets were 31 mm diameter. Just to add a little additional complexity, each SpeakOn socket needed four screw holes, and each of the six XLR sockets needed two screw holes. Then there was the IED power entry module and two pairs of binding posts - thirty-five holes in all if I use a screw-on IEC. The job was unpleasantly messy, and it proved almost impossible to avoid marking the anodised surfaces. I used a 1.25" (31.75 mm) step drill for the SpeakOns and a 15/16" (23.8 mm) step drill for the XLRs. Never attempt something like this without a drill press and clamps!
I had originally intended holding everything in place using nuts and lock washers on the machine screws, but on impulse decided to try tapped holes instead. An M3 screw has a pitch of 0.5 mm, so even if the first thread is damaged, there should still be four full threads in 3 mm thick material. Using tapped holes has the advantages of being able to tighten the screws without having to struggle with access on the inside, and of there being no nuts and washers to fall off and get lost. The disadvantages are that your drilling has to be more precise and that it takes longer. As it turned out, tapping twenty-two M3 holes took me half an hour - time well spent for the frustration it will save.
After cleaning it up, I gave the panel a trial fit - remembering to include my shim washers to prevent the panel from being deformed. I couldn't resist loosely fitting a few connectors just to see how it was going to look.
I had spent a lot of time designing the layout of the rear panel, trying to keep everything away from everything else while avoiding an impossible wiring arrangement . As is usually the case, I was pleased with my final layout, but wondered why it had taken me so long to come up with it.
Predictably, the power enters in the middle. The XLR inputs for the tweeters, mids, and woofers are arranged vertically, reflecting their respective positions in a speaker cabinet, and also line up quite well with the input terminals on the amplifier modules. The SpeakOn output sockets are more or less centered in the space between the upper and lower amplifier modules, so that their terminals shouldn't be entirely impossible to connect to. The binding posts are a little more difficult, but not impossible.
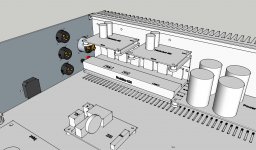
At this stage, I could test that the powers supplies were working properly. With the IEC power inlet connected to the Intelligent Soft Start module, all I had to do was to connect a power cord. Like magic, the on/off switch came to life. If you're old enough to remember tube radios, you'll remember the "magic eye". The on/off switch reminded me of that, only without the wait!
With a gentle press on the switch, the two red LEDs lit up as well. This was turning into a good day. The output terminals on both Power-686 modules showed 30.92 VDC on my multimeter. I was impressed.
Next: installing the amplifier modules.
The job was unpleasantly messy, and it proved almost impossible to avoid marking the anodised surfaces.
I put one or two layers of masking tape on the side that I want to protect and mark out on, and drill from, the other (inside) side.
Assembly and Wiring - the Amplifier Modules.
With only the mounting of the amplifier modules to the heat sinks and the running of the power, input, and output wiring remaining, it seemed like one more day would do it. This turned out to be a little optimistic.
Mounting the amplifier modules to the heat sinks was simple enough - one just has to go carefully in order to remember to use Keratherm and (easily forgotten) the little insulating bushes that prevent the mounting screws from shorting out the power amp IC. With the modules in place, I realised that I had miss-measured somewhere along the way - my Modulus-86 modules should have been a little higher on the heat sinks. This wasn't a disaster, but it did make access for wiring a little more congested. I was in no mood to strip it all down again to drill and tap another dozen holes just to move the boards up a bit.
Here's my Sketchup layout of the interior sans wiring:
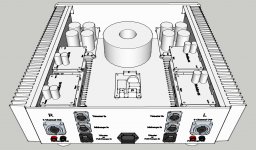
With each amplifier module having terminals for power input, signal input, and speaker output, the wiring is quite "busy". Furthermore, the left and right channels are not mirror images of each other, so the wiring is different on each side of the chassis. It took me several attempts and a long time to decide on what I hoped would be the optimum arrangement.
I began by running the power and speaker wiring in red and black stranded copper that I stripped from some surplus CL2 speaker cable that I had conveniently to hand. However, after expending quite a lot of effort, I noticed that the insulation on this wire tended to split very easily after it had been heated by tinning or soldering. This was too worrying to ignore, so I ripped it all out and started again - this time with some that had tougher insulation. I have my doubts that the original cable really was plenum-rated.
The Modulus-686 boards came pre-built from Neurochrome and feature power and speaker terminal blocks that take crimped connectors - Tom supplies ready-crimped cables specifically for this purpose. They're nice cables, but are quite stiff and therefore can be difficult to route in a tight space. Also, with the constant revisions to my wiring layout, I couldn't afford to end up with cables that were too short.
The signal input to the board is via a board-mounted socket and mating plug (also supplied by Tom). However, the wire entries are vertical, whereas horizontal would be better for my two-storey installation. I had ordered a couple of right-angle plugs from Mouser, but they were oriented the wrong way and faced inwards instead of outwards away from the board. I wasn't having a good time with the wiring.
I like to use Canare Star-Quad microphone cable for balanced signal wiring. It's enormously fiddly to work with, but it gives a good result. My philosophy with this sort of thing is that you suffer once but enjoy the benefit forever. Needless to say, it took a long time to strip both ends of six signal cables, tease out the screening, untwist and re-twist the pairs, and strip and solder them. Now I can look forward to doing it all again when I make up the interconnects from my miniDSP to my new amplifier.
This all paled into insignificance when compared to wiring the SpeakOn connectors and binding posts. As I've already mentioned, my careless miss-measurement made access more difficult than it should have been, particularly with respect to access to these speaker connections. In fact, pins 1 and 2 of the SpeakOn, which I use for the tweeter were blocked by the supporting bracket of the tweeter's Modulus-86 amplifier. Fortunately, since this is an 8-pole connector and I'm using only six of them, I was able to rotate the connector 90° so that it was the unused poles that were blocked. And to think that I had been really looking forward to the wiring after all that messy metal-work.
The final wiring task was to connect the ground tabs of the XLR input sockets to ground. I had already prepared a pair of mounting points in the bottom panel by removing the anodising around M3 clearance holes that I had drilled earlier. I ran a separate ground wire from each XLR ground tab to the ground points on the bottom panel. This is less tidy than simply connecting all the tabs together, but I want to be able to remove every connector from the rear panel without having to get out my soldering iron. This is so that I can remove the rear panel at some time in the future for engraving.
Here's how it all looks now:
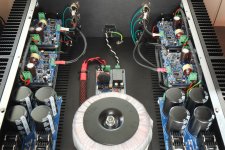
In addition to the usual red/black = positive/negative and red/black = right/left conventions, I've invented another one: white/red/black = tweeter/midrange/woofer, hence the heat shrink labelling on the input signal cables.
All the Neurochrome circuit boards are clearly marked with polarities, pin numbers, or other relevant information that the builders needs. Depending on the orientation of a board and the nature of the wiring in a particular design, some of these might be obscured. Also, they tend to be very small. I made life a lot easier for myself (and for anyone working on this amplifier in the future) by marking directly on the terminal blocks and also on the heatshrink on my cables with a fine Sharpie. For the number of times I ended up disconnecting or re-working the wiring, this really was very helpful. The other thing that I was thankful for was the decision to use tapped holes in the rear panel instead of nuts and washers. All those sockets went in and out a number of times and I was glad that I didn't have to fiddle with M3 nuts and washers repeatedly.
Here's the entire left channel:
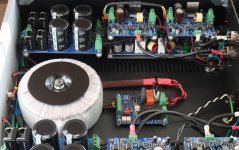
Next: clean-up and test.
With only the mounting of the amplifier modules to the heat sinks and the running of the power, input, and output wiring remaining, it seemed like one more day would do it. This turned out to be a little optimistic.
Mounting the amplifier modules to the heat sinks was simple enough - one just has to go carefully in order to remember to use Keratherm and (easily forgotten) the little insulating bushes that prevent the mounting screws from shorting out the power amp IC. With the modules in place, I realised that I had miss-measured somewhere along the way - my Modulus-86 modules should have been a little higher on the heat sinks. This wasn't a disaster, but it did make access for wiring a little more congested. I was in no mood to strip it all down again to drill and tap another dozen holes just to move the boards up a bit.
Here's my Sketchup layout of the interior sans wiring:
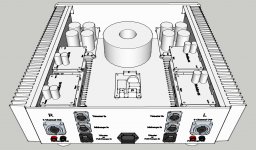
With each amplifier module having terminals for power input, signal input, and speaker output, the wiring is quite "busy". Furthermore, the left and right channels are not mirror images of each other, so the wiring is different on each side of the chassis. It took me several attempts and a long time to decide on what I hoped would be the optimum arrangement.
I began by running the power and speaker wiring in red and black stranded copper that I stripped from some surplus CL2 speaker cable that I had conveniently to hand. However, after expending quite a lot of effort, I noticed that the insulation on this wire tended to split very easily after it had been heated by tinning or soldering. This was too worrying to ignore, so I ripped it all out and started again - this time with some that had tougher insulation. I have my doubts that the original cable really was plenum-rated.
The Modulus-686 boards came pre-built from Neurochrome and feature power and speaker terminal blocks that take crimped connectors - Tom supplies ready-crimped cables specifically for this purpose. They're nice cables, but are quite stiff and therefore can be difficult to route in a tight space. Also, with the constant revisions to my wiring layout, I couldn't afford to end up with cables that were too short.
The signal input to the board is via a board-mounted socket and mating plug (also supplied by Tom). However, the wire entries are vertical, whereas horizontal would be better for my two-storey installation. I had ordered a couple of right-angle plugs from Mouser, but they were oriented the wrong way and faced inwards instead of outwards away from the board. I wasn't having a good time with the wiring.
I like to use Canare Star-Quad microphone cable for balanced signal wiring. It's enormously fiddly to work with, but it gives a good result. My philosophy with this sort of thing is that you suffer once but enjoy the benefit forever. Needless to say, it took a long time to strip both ends of six signal cables, tease out the screening, untwist and re-twist the pairs, and strip and solder them. Now I can look forward to doing it all again when I make up the interconnects from my miniDSP to my new amplifier.
This all paled into insignificance when compared to wiring the SpeakOn connectors and binding posts. As I've already mentioned, my careless miss-measurement made access more difficult than it should have been, particularly with respect to access to these speaker connections. In fact, pins 1 and 2 of the SpeakOn, which I use for the tweeter were blocked by the supporting bracket of the tweeter's Modulus-86 amplifier. Fortunately, since this is an 8-pole connector and I'm using only six of them, I was able to rotate the connector 90° so that it was the unused poles that were blocked. And to think that I had been really looking forward to the wiring after all that messy metal-work.
The final wiring task was to connect the ground tabs of the XLR input sockets to ground. I had already prepared a pair of mounting points in the bottom panel by removing the anodising around M3 clearance holes that I had drilled earlier. I ran a separate ground wire from each XLR ground tab to the ground points on the bottom panel. This is less tidy than simply connecting all the tabs together, but I want to be able to remove every connector from the rear panel without having to get out my soldering iron. This is so that I can remove the rear panel at some time in the future for engraving.
Here's how it all looks now:
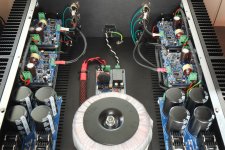
In addition to the usual red/black = positive/negative and red/black = right/left conventions, I've invented another one: white/red/black = tweeter/midrange/woofer, hence the heat shrink labelling on the input signal cables.
All the Neurochrome circuit boards are clearly marked with polarities, pin numbers, or other relevant information that the builders needs. Depending on the orientation of a board and the nature of the wiring in a particular design, some of these might be obscured. Also, they tend to be very small. I made life a lot easier for myself (and for anyone working on this amplifier in the future) by marking directly on the terminal blocks and also on the heatshrink on my cables with a fine Sharpie. For the number of times I ended up disconnecting or re-working the wiring, this really was very helpful. The other thing that I was thankful for was the decision to use tapped holes in the rear panel instead of nuts and washers. All those sockets went in and out a number of times and I was glad that I didn't have to fiddle with M3 nuts and washers repeatedly.
Here's the entire left channel:
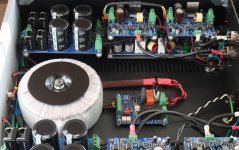
Next: clean-up and test.
Clean-Up and Test
There wasn't much to do in terms of clean-up. I used compressed air to carefully blow off every board and to clear any remaining debris and solder clippings from the chassis. The black anodised finish marks very easily with a finger nail, but the mark wipes off just as easily. I used a piece of towelling dampened with isopropyl alcohol for a final wipe-down.
I had already tested the power supplies, so all that remained was to test the six amplifier modules. Rather than have to disconnect all my careful power wiring to the amp modules yet again, I decided to double-check absolutely everything and then to cross my fingers and power everything up together. I went over every piece of wiring testing for continuity on every conductor. I even found an error where I had got some of my colour-coded heat shrink the wrong way around; it was only a signal cable, but I was pleased to have found it. I gave the whole thing a final round of scrutiny and then turned on the power. The 6.3 amp fuse in the IEC power inlet blew.
After some consultation with Tom and a day and a half of hand-wringing we had if sorted out. I use M3 machine screws to fix the Modulus-86 circuit boards to my mounting brackets. I allowed plenty of clearance in the holes in the brackets so that I could adjust the final alignment and minimise any strain on the amplifier ICs screwed to the heat sinks, and used self-locking nuts so that I didn't have to tighten them fully. The nuts closer to the heat sinks were held captive by the 90° mounting tab of the mounting brackets, thus the screws had to be turned instead of the nuts. I'm the kind of guy who likes to use a washer whenever a fastener is sliding on the thing it's clamping. Unfortunately, the fit of the washers on the board was marginal and in one instance a burr on the washer allowed an arc to jump and create a short.
I removed all the Modulus-86 boards, removed the washers, and then re-mounted the boards on the heat sinks, taking care to keep the amplifier chips unstressed and also well insulated from the heat sinks. I replaced the wiring in stages so that I could power up the amplifier modules individually this time. I left the amplifier powered up and sitting on my bench for a couple of hours while I started making up speaker cables.
I have a lot of input XLR cables to make, and I would also have to modify my house wiring to accommodate SpeakOn cables where the speaker cables pass through a wall plate and go under the floor. This meant that it would be some time before I was ready to test all six channels of amplification. However, I had designed this as a dual-purpose amplifier so that it could function as a two-channel stereo amplifier with conventional speakers with passive crossovers if required, so all I needed to make this work was a pair of RCA-to-XLR input cables, and I already had those.
It took about 15 minutes to find the input cables, a pair of speaker cables, and to get everything connected up. With three upstream volume controls turned down, I powered up, set my Squeezebox streaming, and then started turning up the volume controls. Bliss and joy!
Next: final installation.
There wasn't much to do in terms of clean-up. I used compressed air to carefully blow off every board and to clear any remaining debris and solder clippings from the chassis. The black anodised finish marks very easily with a finger nail, but the mark wipes off just as easily. I used a piece of towelling dampened with isopropyl alcohol for a final wipe-down.
I had already tested the power supplies, so all that remained was to test the six amplifier modules. Rather than have to disconnect all my careful power wiring to the amp modules yet again, I decided to double-check absolutely everything and then to cross my fingers and power everything up together. I went over every piece of wiring testing for continuity on every conductor. I even found an error where I had got some of my colour-coded heat shrink the wrong way around; it was only a signal cable, but I was pleased to have found it. I gave the whole thing a final round of scrutiny and then turned on the power. The 6.3 amp fuse in the IEC power inlet blew.
After some consultation with Tom and a day and a half of hand-wringing we had if sorted out. I use M3 machine screws to fix the Modulus-86 circuit boards to my mounting brackets. I allowed plenty of clearance in the holes in the brackets so that I could adjust the final alignment and minimise any strain on the amplifier ICs screwed to the heat sinks, and used self-locking nuts so that I didn't have to tighten them fully. The nuts closer to the heat sinks were held captive by the 90° mounting tab of the mounting brackets, thus the screws had to be turned instead of the nuts. I'm the kind of guy who likes to use a washer whenever a fastener is sliding on the thing it's clamping. Unfortunately, the fit of the washers on the board was marginal and in one instance a burr on the washer allowed an arc to jump and create a short.
I removed all the Modulus-86 boards, removed the washers, and then re-mounted the boards on the heat sinks, taking care to keep the amplifier chips unstressed and also well insulated from the heat sinks. I replaced the wiring in stages so that I could power up the amplifier modules individually this time. I left the amplifier powered up and sitting on my bench for a couple of hours while I started making up speaker cables.
I have a lot of input XLR cables to make, and I would also have to modify my house wiring to accommodate SpeakOn cables where the speaker cables pass through a wall plate and go under the floor. This meant that it would be some time before I was ready to test all six channels of amplification. However, I had designed this as a dual-purpose amplifier so that it could function as a two-channel stereo amplifier with conventional speakers with passive crossovers if required, so all I needed to make this work was a pair of RCA-to-XLR input cables, and I already had those.
It took about 15 minutes to find the input cables, a pair of speaker cables, and to get everything connected up. With three upstream volume controls turned down, I powered up, set my Squeezebox streaming, and then started turning up the volume controls. Bliss and joy!
Next: final installation.
Building this amp is my day job at the moment. Actually, Chris, it's all your fault - it was you who first told me about Neurochrome and put me in touch with Tom . . .
Either way works for me. 🙂
That's a nice build there! I admire the level of planning that you went through leading into the build.
Tom
That's a nice build there! I admire the level of planning that you went through leading into the build.
Tom
- Home
- Amplifiers
- Chip Amps
- Dual-Purpose Multichannel / Stereo Amplifier using Neurochrome Modules