I think rebating the driver 'decreases' the complexity.....acoustically.
You seem to be disappointed there isn't a definitive answer to your query.
It's in the nature of this type of thing that measurements can be inconsistent and hard to resolve for the particular thing you're looking for.
I'm not sure what would satisfy you.
Dave.
You seem to be disappointed there isn't a definitive answer to your query.
It's in the nature of this type of thing that measurements can be inconsistent and hard to resolve for the particular thing you're looking for.
I'm not sure what would satisfy you.
Dave.
The choice to veneer an MDF baffle would make me question the recess as well. In my case, I use thick slabs of whatever wood that is chosen for the baffle. Less chance for a mistake that can't be easily dealt with.
About woodworking in general; Good tools may take you much further towards projects, when completed, that are something to show off. I have done plenty of handplaning, sanding and chiseling, but the router became king very quickly in my shop, as it is capable of so many functions, and accurate as well.
About woodworking in general; Good tools may take you much further towards projects, when completed, that are something to show off. I have done plenty of handplaning, sanding and chiseling, but the router became king very quickly in my shop, as it is capable of so many functions, and accurate as well.
A router is an intimidating tool, and it should be. I personally consider the router to be the most dangerous power tool in my shop, meaning I feel I have the highest probability of injury while using the hand held router or router table.
A surface mounted tweeter with a circular flange will usually have a diffraction induced response variation of +/- 2 dB from 3k - 10k. This may or may not make much difference. If a design has other diffraction reducing features, such as large radius baffle edges, or deep bevels, the surface mounting of the tweeter may wreck all these benefits. On the other hand, if the design has sharp edges on the baffle, or a grill frame with reflective surfaces, then a surface mount tweeter may not be very detrimental at all.
To get a truly excellent 3D presentation, with a wide, deep soundstage and precise imaging, we need to minimize diffraction (in my opinion). But that level of high performance is not necessary for a speaker to sound good and be musically satisfying.
No one should feel pressured into using a tool they are not comfortable with. When it comes to power tools, trust your inner anxieties...Statements that using a router is easy and everyone has one are not helpful.
A surface mounted tweeter with a circular flange will usually have a diffraction induced response variation of +/- 2 dB from 3k - 10k. This may or may not make much difference. If a design has other diffraction reducing features, such as large radius baffle edges, or deep bevels, the surface mounting of the tweeter may wreck all these benefits. On the other hand, if the design has sharp edges on the baffle, or a grill frame with reflective surfaces, then a surface mount tweeter may not be very detrimental at all.
To get a truly excellent 3D presentation, with a wide, deep soundstage and precise imaging, we need to minimize diffraction (in my opinion). But that level of high performance is not necessary for a speaker to sound good and be musically satisfying.
Sounds like the McLaren M23 or the Lotus 72?I am reminded of a racing team developing an F1 car though, in the winter season they realised that the basic car had nothing wrong with it, so they spent the winter making little small improvements by attention to detail, each improvement wasn't really worth much,
Geoff
There are so many dangerous power tools out there. Number one to me is the band saw. I won't even own one. A die grinder can be very nasty too. Not just the bit but the metal that it throws at high speed everywhere. A circular handheld saw is safe if used correctly . This is also true with large machines, but a great deal of caution is number one.
Routers? Yes, they can be very dangerous, especially if you forget which way the bit is spinning! And also if you are taking too deep of a cut. Taking a 1/2" chamfer in just a few cuts is asking for excitement. And never think that you might need clamps to hold a particular job in place while working it.
Routers? Yes, they can be very dangerous, especially if you forget which way the bit is spinning! And also if you are taking too deep of a cut. Taking a 1/2" chamfer in just a few cuts is asking for excitement. And never think that you might need clamps to hold a particular job in place while working it.
Last edited:
I got a small 3018 CNC so that I could build small speaker boxes. Recessing was a motivation. I live in an apartment and it's hard to use the router without making a mes.
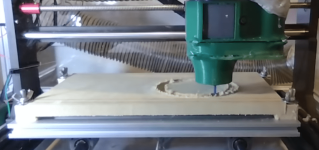

Then I got a 3040 that I have in a big box for soundproofing and dust management. Daughter for scale.
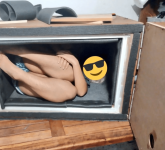
And I got a used one that is bigger that I need to install when I get the time and make the space.
It's a lot of work but it's great to be able to design and then get the pieces you need.
Downsides:
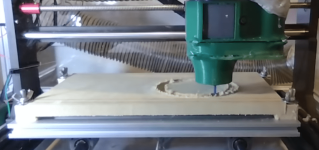

Then I got a 3040 that I have in a big box for soundproofing and dust management. Daughter for scale.
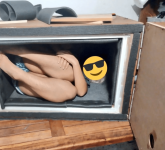
And I got a used one that is bigger that I need to install when I get the time and make the space.
It's a lot of work but it's great to be able to design and then get the pieces you need.
Downsides:
- Need to learn CAD
- Need to learn the tricks. For instance, you need to cut fast and make chips and not dust. It's easier for the machine to go fast.
- Needs space
- Produces noise, dangerous dust and fumes that you need to deal with
- You need to be able to fix and build stuff for the CNC. Like the people who own an old car and know how to fix it. If you don't know basic electronics it's hard to service a CNC.
- You need to sand a bit and also paint, you need to be careful.
- What I paint is not pretty.
- Get distracted. Another rabbit hole that distracts.
- Build fast when you have an idea, build what you want. I had a few boxes made and it took them a lot of time to make. They do a great paint job but it's too much time. Woodworkers usually have a lot in their plates.
- It's nice to have repeatable precision.
- Design once, cut many times.
- Learn interesting stuff.
Attachments
Last edited:
...the question is really whether its all that big a deal compared to other aspects...
The answer is, rebating a driver is not a prerequisite for a good sounding loudspeaker. What is, is how you voice the crossover filter and that you
measure T/S parameters to ensure an exemplary driver loading.
What rebating does most is making a product look more professional. The measured influence on sound is more hurtful to the eyes than ears.
There are so many dangerous power tools out there. Number one to me is the band saw. I won't even own one. A die grinder can be very nasty too. Not just the bit but the metal that it throws at high speed everywhere. A circular handheld saw is safe if used correctly
A hand held angle grinder with an abrasive cutting disk is another one that can be dangerous if the disk comes apart while running. Of course chain saws are the king of tools when it comes to shredding human flesh and bone...
I don't find my band saw to be dangerous, if fact the opposite. I consider it one of the safest ways to cut small parts, and I feel comfortable with my fingers very close to the blade as I gently ease the work piece into the blade.
Now cutting a workpiece that is too thick, or pushing the work too fast through the blade, I could see that can be dangerous if the blade gets pushed out of alignment.
This is a thread on the hazards of woodworking tools now????
You're in DIY audio for crying out loud!
Maybe if you're into the electronics portion of it you should quit because you might burn your finger with a soldering iron??
Dave.
You're in DIY audio for crying out loud!
Maybe if you're into the electronics portion of it you should quit because you might burn your finger with a soldering iron??
Dave.
It is a thread about whether recessed mounting of drivers lers people avoid diy. Speaking of dangerous tools fits perfectly, imho.
That's not the entire truth to the story.The answer is, rebating a driver is not a prerequisite for a good sounding loudspeaker. What is, is how you voice the crossover filter and that you
measure T/S parameters to ensure an exemplary driver loading.
What rebating does most is making a product look more professional. The measured influence on sound is more hurtful to the eyes than ears.
Woofers can but needn't to be rebated but there are reasons to do so.
On the backside you need to ensure that the panel is not blocking the airflow especially if you make the Frontpanel twice as thick as the rest of the speaker.
Mid an high are highly influenced by the sharp edges and depending on the distance between listener and source can be heard.
If the drivers are rebated they see a complete different area/distance to the next edge and the sounding will vary to a non-rebated one.
We are talking about small influences but nowadays you got plenty of Onlineshops that CNC mill the panels for you or if this hobby is more an addiction we don't have problems with using a router and a circular jig.
Do it cheap and quick and dirty and the result will work but is far of satisfying, optically nothing for long-term usage.
Take your time make something fun and pleasing for eye and ear and not only the WAF increases by alot but also it's a piece to be proud.
If anything sounds weird you can clearly state you did everything you could to have a proper housing.
Even with cheap drivers I achieved better results by having proper clean enclosures.
It should be worth it
I have a feeling it was a McLaren.Sounds like the McLaren M23 or the Lotus 72?
Geoff
I thinks it's understandable to be cautious with power tools, not many Carpenters have a full compliment of finger tips - one at work caught the tip of his finger in a planer, he was very lucky that it didn't pull his arm in. But if you are careful, you can gain confidence with them in time - but a band saw blade snapping will always make you jump, even when you have the warning "tick tick tick" before hand.
Let's face it, if you made some speakers you don't like, at least you tried; if you do like them but didn't rebate the drivers, you could always add an extra piece that fits snugly around the drivers, perhaps stick some grill cloth on it.
Perhaps taking a long time to make some speakers could be a good thing, especially if you're running out of space for the ones that you've already made.
Do you have a reference for that?A surface mounted tweeter with a circular flange will usually have a diffraction induced response variation of +/- 2 dB from 3k - 10k. This may or may not make much difference.
I'd change that to 'crossover to beaming' given that many 25-30mm tweeters can cross somewhat lower and may start to beam before that. My reading of what you are saying is that this is based on diffraction at the rim of the tweeter's flange, and is not considering the nearby (mid)woofer, which will provide a source of difraction and reflection even if it is flush mounted.
My understanding is that what people do in practice does not actually meet the reality of 'large radius', though I'd have to have a good session with a search engine to find evidence, I suspect. A small one might be cosmetic depending on the finish - it is going to make veneering harder. And painting.If a design has other diffraction reducing features, such as large radius baffle edges, or deep bevels, the surface mounting of the tweeter may wreck all these benefits. On the other hand, if the design has sharp edges on the baffle, or a grill frame with reflective surfaces, then a surface mount tweeter may not be very detrimental at all.
If we accept that cabinet edge diffraction is a thing - and then we get a crapload of reflections in room as well - it may be that the +-2dB is a minor effect and the smoothed response for trend line is more important. After all, if you look at high frequency plots from conical structures, whether coax, horns, or full range drivers, they all show significant deviation from flat on axis and I believe these are early reflection artifacts and they don't actually matter in the big picture, given the evidence that these can be very satisfying.
I'd actually be quite happy to try felt as a baffle finish BUT I'm concerned that a tidy solution would require accurately cutting circular holes in a felt sheet, and I'm not sure how that would go. Most of the experiments I've seen reported have used rectangular felt blocks and clearly work better with a grill to hide the visuals.
Well, as you say - that's opinion. Somehow, LS3/5A had (and in some cases has) quite a good reputation.. And yet the baffle construction of 'historically accurate' LS3/5A is quite disturbing if we believe in currently accepted mantras.To get a truly excellent 3D presentation, with a wide, deep soundstage and precise imaging, we need to minimize diffraction (in my opinion). But that level of high performance is not necessary for a speaker to sound good and be musically satisfying.
Falcon
Musical Fidelity
Stirling
Rogers
Graham - not so clear, but still showing a baffle recessed into the cabinet, with a flush fit grill.
I look at these and I'm 'WTF?' - because the theory about the early diffraction etc etc seems understandable and reasonable and apart from a bit of stapled on felt these things just seem to be antipattern examples.
I can't help an uneasy feeling that I'm missing a big picture prioritisation and a whole lot of premature optimisation is available to me.
Eg (for an IT analogue) I am optimising a bit of C++ in my code base, that sits right between two RPC calls to servers in a remote datacentre. I can profile my code, I can optimise my code, I can feel good, because I did my bit - and I can't change the speed of light or the latency from the intermediate switches and routers anyway. But a complete waste of time. Don't do that.
Have you tried converting to JSON and back again? 🙂Eg (for an IT analogue) I am optimising a bit of C++ in my code base, that sits right between two RPC calls to servers in a remote datacentre. I can profile my code, I can optimise my code, I can feel good, because I did my bit - and I can't change the speed of light or the latency from the intermediate switches and routers anyway. But a complete waste of time. Don't do that.
Seriously, sometimes I reflect on what is what I want to DIY and what not. Sometimes the baffle, sometimes electronics that I've been learning a lot because of the hobby. Sometimes the objective is to work on a tool and I do that a lot.
When I get lost in the details, projects take too long and I cannot listen to music.
Here is one... my own measurements are similar...Do you have a reference for that?
http://www.troelsgravesen.dk/measurements.htm
Regarding the audibility of diffraction - All I can tell you is that my experience from building a variety of speakers is that very low diffraction (and zero reflection) in the first 20 cm of sound travel leads to a step-wise improvement in the spatial 3D performance of the speaker system.
This one uses 37 mm radius roundovers on the sides, and a 37 mm deep bevel along the top.
This one uses a waveguide for the tweeter, with a 37 mm radius to terminate the edge of the waveguide. The midrange enclosure is also a very low diffraction design on the front, sides, and back of the cabinet.
Both systems create a very believable spatial presentation. Much better than any of the sharp-edged boxes I have made in the past.
As I said in my post, a very low diffraction design is not necessary for a musically satisfying experience. Most commercially available speakers are not really low diffraction designs, so a DIY speaker with a conventional box can equal a lot of these systems... many of which are rather expensive.
The closer I sit to my speakers, the more important the low diffraction becomes. If I sit well back in the room, my ears are dominated by the reflected sound, and spatial localization gets nebulous. If that is how I did most of my listening, I might not bother with all this effort to make low diffraction systems.
You should build what you want. Listen, evaluate, make up your own mind. But if you are making the argument that a low diffraction design makes no difference and is a waste of time and effort... Sorry, you are not going to convince me of that.
This is mine experience, I sit 4m away in a large room...If I sit well back in the room, my ears are dominated by the reflected sound, and spatial localization gets nebulous. If that is how I did most of my listening, I might not bother with all this effort to make low diffraction systems.
Do you have a reference for that?
how many do you want?
in post 32 this information was presented (which you "liked") 🤔
But as @jmansion has said multiple times, that didn't include a woofer below the tweeter, which surely creates it's own diffraction. So that evidence isn't enough. He has a point there, the end result will be the sum of all components.
As @hifijim said, listening conditions may play a large role of what choices become valid compromises. But isn't that the beauty of DIY audio? Being able to determine your own set of compromises? One builder will do all the work of designing and building himself. Another might find pleasure in building a design in kit form and finishing it with a nice veneer. A third may even want to create his/her own drivers. For some the hobby is building something with your own two hands, for others it might be the passion for music that has driven their attempt. Then there's the ones that have worked in Audio all of their lives and are here to share their knowledge or simply to correct the wrongs they encounter.
We have all these different type of DIY people here, all with slightly differing views or priorities. What works for you might not work for me and vice versa. But having all of these experiences, plus all the data available, that's key right? Then you can pick what you deem important and go with that.
As @hifijim said, listening conditions may play a large role of what choices become valid compromises. But isn't that the beauty of DIY audio? Being able to determine your own set of compromises? One builder will do all the work of designing and building himself. Another might find pleasure in building a design in kit form and finishing it with a nice veneer. A third may even want to create his/her own drivers. For some the hobby is building something with your own two hands, for others it might be the passion for music that has driven their attempt. Then there's the ones that have worked in Audio all of their lives and are here to share their knowledge or simply to correct the wrongs they encounter.
We have all these different type of DIY people here, all with slightly differing views or priorities. What works for you might not work for me and vice versa. But having all of these experiences, plus all the data available, that's key right? Then you can pick what you deem important and go with that.
A mean looking, innovative, cool and long lasting F1 car: I think it did 1970, 71, 72, 73 and 74 seasons with World Championships in 1970 (posthumously for Jochen Rindt) and 1972 for Emerson. Really set the design concept for most F1 and F5000 cars from its inception, including the almost as successful McLaren M23 (World Champion in 1974 and 76). Unfortunately, like most F1 cars of that era, neither strong nor safe.![]()
dave
Going back to topic, making and finishing the cabinets was what really put me off DIY to begin with; luckily my first pair were made by a family friend who was a pattern maker with GM-Holden. Woofers and tweeters recessed, 'wenge' stained oak veneer MDF and lovely finish. Before he was 'volunteered' to make them, I tried a dozen cabinet makers, only one of whom would quote and the price was plain silly.
I then bought a cheap router, jig saw etc and have made three pairs since then, although I have to get the MDF panels cut to size. No way will I put myself at risk with a circular or table saw for the sake of saving a few $.
Geoff
- Home
- Loudspeakers
- Multi-Way
- Driver recessing - how important? And does it cause people to avoid DIY?