Hy everyone,
I would like to open a new tutorial for people like me who want to make his own diy turntable spindle bearing avoiding waste too much time on bed working experiments.
As a standard bearing I suggest the bearing of the following image
A lot of thigs, can be customized from the diy'er, for example:
- design
- recirculating oil pump like the spindle of the image
- external geometry of the spindle housing
- choice of the material for the ball
- thrust pad (delrin PTFE for example)
- Plate weight between 3 and 15 kg
On the other hand, some point of the project is extremely important and fixed, like:
- materials to use (steel, bronze?)
- clearance-tolerance between the bore and the spindle for a perfect precise work
- grade of polishing the internal part of the bore and the spindle
- typeof oil
- other?
I think that a lot of diy'ers who have a medium lathe, are attracted to machining their own bearing, but is not easy to find all detailed information about this particular project.
Personally I find some intresting table like the following:
And this
But I'm unable to define which tolerance is optimal for my project
I also believe, that with chineese lathes (I have a small sieg and a bigger newton 25), is possible to turning a spindle precise in a 2-4/1000 of millimeter (between 2 or 4 um), so there is no reason to not try building a really good spindle.
Of course is extremely important to have precision reading instruments like external and internal micrometer, good and sharped tools, and a lot of patience.
As a starting example idea:
1- machining a 15.000 millimeters housing, (15.000 millimeters allow you to work and polishing the hole)
2- machining the spindle to the right diameter, but which is the right diameter?
14.960mm? 14.985mm? 14.990mm?
I hope some member of this forum will contribute to define the basics for this tricky work, I'm sure that a lot of undecided diy'er will start to machining his own super bearing system!
Thaks to all
Luis
I would like to open a new tutorial for people like me who want to make his own diy turntable spindle bearing avoiding waste too much time on bed working experiments.
As a standard bearing I suggest the bearing of the following image
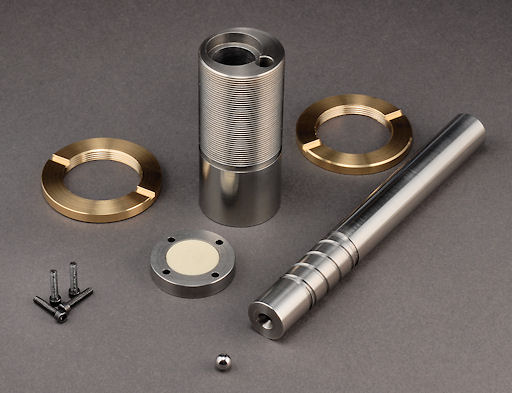
A lot of thigs, can be customized from the diy'er, for example:
- design
- recirculating oil pump like the spindle of the image
- external geometry of the spindle housing
- choice of the material for the ball
- thrust pad (delrin PTFE for example)
- Plate weight between 3 and 15 kg
On the other hand, some point of the project is extremely important and fixed, like:
- materials to use (steel, bronze?)
- clearance-tolerance between the bore and the spindle for a perfect precise work
- grade of polishing the internal part of the bore and the spindle
- typeof oil
- other?
I think that a lot of diy'ers who have a medium lathe, are attracted to machining their own bearing, but is not easy to find all detailed information about this particular project.
Personally I find some intresting table like the following:
An externally hosted image should be here but it was not working when we last tested it.
And this
An externally hosted image should be here but it was not working when we last tested it.
But I'm unable to define which tolerance is optimal for my project
I also believe, that with chineese lathes (I have a small sieg and a bigger newton 25), is possible to turning a spindle precise in a 2-4/1000 of millimeter (between 2 or 4 um), so there is no reason to not try building a really good spindle.
Of course is extremely important to have precision reading instruments like external and internal micrometer, good and sharped tools, and a lot of patience.
As a starting example idea:
1- machining a 15.000 millimeters housing, (15.000 millimeters allow you to work and polishing the hole)
2- machining the spindle to the right diameter, but which is the right diameter?
14.960mm? 14.985mm? 14.990mm?
I hope some member of this forum will contribute to define the basics for this tricky work, I'm sure that a lot of undecided diy'er will start to machining his own super bearing system!
Thaks to all
Luis
Wow, holding tolerances of that nature on a small chinese lathe (2 to 4 um) is unheard of. It would be challanging on a Hardinge or even my Monarch 10EE.
Anyway, as far as your spindle design is concerned I don't see any bearing material in your housing. I would press in bronze sleeves and hone or lap the bore to size. The spindle should be hardened and ground to size. Use the center on the end of your spindle where the ball goes so that after grinding it is concentric to the OD of the spindle.
It looks like your planning on running a steel shaft in a steel housing. Don't, it will gall up. Plain bearings work best if the materials are very different from one another. Hardened steel shaft running in a bronze bushing or even in a fine grade of cast iron works well. I would think that a running clearance of some where between 0.007 um to about 0.012 um should work well. I base this from building machinery and using a rule of thumb for plain bearings of 0.001/per inch of shaft diameter. I'm not used to working in the metric system so double check my calculations.
BillWojo
Anyway, as far as your spindle design is concerned I don't see any bearing material in your housing. I would press in bronze sleeves and hone or lap the bore to size. The spindle should be hardened and ground to size. Use the center on the end of your spindle where the ball goes so that after grinding it is concentric to the OD of the spindle.
It looks like your planning on running a steel shaft in a steel housing. Don't, it will gall up. Plain bearings work best if the materials are very different from one another. Hardened steel shaft running in a bronze bushing or even in a fine grade of cast iron works well. I would think that a running clearance of some where between 0.007 um to about 0.012 um should work well. I base this from building machinery and using a rule of thumb for plain bearings of 0.001/per inch of shaft diameter. I'm not used to working in the metric system so double check my calculations.
BillWojo
GiuzO, take a look at a thread about a dozen post down from this one titled "Modern bearing engineering, a sad story" on how not to design a spindle bearing. Also if you can get your hands on a Pioneer PL-41 TT or one of it's variants, take a long hard look at the design of that. It's very well engineered. Study the materials and the surface finishes.
BillWojo
BillWojo
Centerless grinding and proper heat treating are the proper way to exact tolerances for the shaft.
Oilite bushings cannot be bored and honed, but bronze and brass can. But do you want to bore and hone? The oilite style bushing is much better and more difficult to get a proper tolerance, but doable
The spiral grooves are not necessary and reduce surface area. If you use proper machining an oil film is enough. Looks like the fill hole will keep it topped off anyway
You would be better off looking for a VPI bearing assembly that come up quite often on Ebay or Audiogon, if you can,t get proper linear dimensions on your own.
Regards
David
Oilite bushings cannot be bored and honed, but bronze and brass can. But do you want to bore and hone? The oilite style bushing is much better and more difficult to get a proper tolerance, but doable
The spiral grooves are not necessary and reduce surface area. If you use proper machining an oil film is enough. Looks like the fill hole will keep it topped off anyway
You would be better off looking for a VPI bearing assembly that come up quite often on Ebay or Audiogon, if you can,t get proper linear dimensions on your own.
Regards
David
Last edited:
Oilite bushings cannot be bored and honed, but bronze and brass can. But do you want to bore and hone? The oilite style bushing is much better and more difficult to get a proper tolerance, but doable
I've bored hundreds of oilite bushings, to .0002/.0004" clearance, manually. Easy peazy.
jeff
AVWERK, the reason I would use a regular cylindrical grinder on the shaft is so the center drilled end would be supported by the center of the tailstock. This would place the center of the ball bearing in the center of the shaft. Centerless grinding is a mass production type of grinder and not suitable for this application.
As far as oilite bearings go, I would not use them in this application. Reaming them to size spears the surface and boring them to size leaves a lot of loose particles enbedded in the surface. I think something like Ammco 630 bronze would be the ticket. It's nice to machine to.
A small Sunnen hone is a joy to use and it's so easy to "split tenths". The OP would have to check around to find a shop that has the required mandrel size. Or since he has a lathe, go on ebay and get a mandrel, set of stones and a driver he can rig up in the lathe. Leave about 0.005" in the hole and check often. Use lots of oil for flushing. Doesn't take much skill to hold really tight tolerences. Sounds like a fun project.
BillWojo
As far as oilite bearings go, I would not use them in this application. Reaming them to size spears the surface and boring them to size leaves a lot of loose particles enbedded in the surface. I think something like Ammco 630 bronze would be the ticket. It's nice to machine to.
A small Sunnen hone is a joy to use and it's so easy to "split tenths". The OP would have to check around to find a shop that has the required mandrel size. Or since he has a lathe, go on ebay and get a mandrel, set of stones and a driver he can rig up in the lathe. Leave about 0.005" in the hole and check often. Use lots of oil for flushing. Doesn't take much skill to hold really tight tolerences. Sounds like a fun project.
BillWojo
A friend of mine made his own turntable and for the bearing he used the head of a vhs vcr. It worked VERY well. Very cheap, no need to "machine" anything as that has already been done for you. You can pick up a vcr from a thrift shop for about 5 - 10 bucks.
Give it a try, it works great.
Give it a try, it works great.
Thanks for your replies guys!
About chineese lathe (im)precision, I need to specify exactly what I meen, in fact is possible to reach tight tolerances, but only without moving the piece from the chuck, and once all the carriage screws are properly tighten.
I'm not a professional lathemaster, but from my little experience if you start and finish turning the piece without move it from the chuck is possible to reach a good precision.
Bill, I take a look to the thread you mentioned me, and sadly I have to confirm you that now I'm not sure to machining my own spindle.
Probably, even if the spindle and the housing are made with an unbelievable precision, there are lot of variants that can compromise the (supposed to be long) life of the bearing system.
At the moment I'm stuck with my turntable project, the arm is finished, both bases also, I only need to solve this "little" problem then I will be ready for painting.
I will not consider to buy expensive finished bearings, the goal of a diy'er when possible is to create a lot with less in a reasonable way, so I will check all the solutions.
I think this afternoon I will considering to disassemble my VCR and take a look on the vcr head
Anyway, about this thread purpose, at this point will be interesting to hear someone that already built a good working spindle that is running from a certain amount of time
Thanks GG
About chineese lathe (im)precision, I need to specify exactly what I meen, in fact is possible to reach tight tolerances, but only without moving the piece from the chuck, and once all the carriage screws are properly tighten.
I'm not a professional lathemaster, but from my little experience if you start and finish turning the piece without move it from the chuck is possible to reach a good precision.
Bill, I take a look to the thread you mentioned me, and sadly I have to confirm you that now I'm not sure to machining my own spindle.
Probably, even if the spindle and the housing are made with an unbelievable precision, there are lot of variants that can compromise the (supposed to be long) life of the bearing system.
At the moment I'm stuck with my turntable project, the arm is finished, both bases also, I only need to solve this "little" problem then I will be ready for painting.
I will not consider to buy expensive finished bearings, the goal of a diy'er when possible is to create a lot with less in a reasonable way, so I will check all the solutions.
I think this afternoon I will considering to disassemble my VCR and take a look on the vcr head
Anyway, about this thread purpose, at this point will be interesting to hear someone that already built a good working spindle that is running from a certain amount of time
Thanks GG
giuzO I never meant to discourage you. I think you have the required skills to make a very good if not great spindle bearing setup with some additional work. I can see that your skills on the lathe are very good and your 100% correct about doing everything you can in one chucking to keep concentricity in check. Just look at the other thread I pointed you to, That was an expensive TT and allready I see you have more skill than the maker of that TT.
Forget about VCR heads, I'm pretty sure it uses a rolling bearing element of some sort. A plain bearing is what you want to use. Since you have limited equipment to work with, lets look at what's avalable commercially. Precision ground drill rod is not expensive and is avalable in air, oil and water hardening. I'm not sure what you would call it over there but a common alloy would be 01 tool steel. This would give you a precision ground but machinable blank length of steel to work with. Over here it's commonly avalable in 18" and 36" lengths at a reasonable cost. Plenty of info on the net about how to harden it.
Bronze bearings can be pressed in and bored almost to size. Look on the net for how to make a split lap to finish it to size,
A great resource for machining help is the website Practicalmachinist.com
Keep us posted on your progress. I like where your going with this.
BillWojo
Forget about VCR heads, I'm pretty sure it uses a rolling bearing element of some sort. A plain bearing is what you want to use. Since you have limited equipment to work with, lets look at what's avalable commercially. Precision ground drill rod is not expensive and is avalable in air, oil and water hardening. I'm not sure what you would call it over there but a common alloy would be 01 tool steel. This would give you a precision ground but machinable blank length of steel to work with. Over here it's commonly avalable in 18" and 36" lengths at a reasonable cost. Plenty of info on the net about how to harden it.
Bronze bearings can be pressed in and bored almost to size. Look on the net for how to make a split lap to finish it to size,
A great resource for machining help is the website Practicalmachinist.com
Keep us posted on your progress. I like where your going with this.
BillWojo
How about some new materials ? For example 'Delrin' bushes. I don't know how Delrin and steel interact but idea is to deliberately have one material wear out sooner (with reference to steel) and design a turntable bearing in such a way that it can be easily replaced, say after one or two years or so.
Regards.
Regards.
Hiten, a properly designed TT spindle bearing should never really wear out. If there is a film of oil between the spindle and bushing than there is no metal to metal contact. The real load happens at the bottom of the spindle shaft. A single ball bearing spinning on a pad of delrin with a tiny contact area supporting the weight of the platter. Yet this bearing setup seems to work out very well.
BillWojo
BillWojo
Billwojo,
You are absolutely right. Effort should be to have long lasting bearing. Even my cheap pioneer served me almost 30 years with hardly any play on bearing. (Was brought by my granddad) I was thinking more on the lines of Connoisseur Craftsman nylon bearing. Delrin is said to have lowest friction and high durability. Don't know about lubricant. but upward moving spiral groove (Designed by giuz0) would be great I think.
Regards.
You are absolutely right. Effort should be to have long lasting bearing. Even my cheap pioneer served me almost 30 years with hardly any play on bearing. (Was brought by my granddad) I was thinking more on the lines of Connoisseur Craftsman nylon bearing. Delrin is said to have lowest friction and high durability. Don't know about lubricant. but upward moving spiral groove (Designed by giuz0) would be great I think.
Regards.
So now for me is time to study the best solution before attempting to machining a new spindle, so I will not give new updates to this thread before a while.
Anyway, today afternoon I pick up my daewoo vcr from my garage, and I removed its head.
At the end of the post I attached some picture of the head
Ok, almost all low cost and high end turntables seems to avoiding ball bearing, and for sure there is a valid reason to obtaining for other choices, by the way, I decide to test anyway this ball bearing system.
Well, if the upper flange (I dont know if flange is the proper name, anyway the rotor), is rotating with any load on it, ball bearings produce a very little sound, or hum as you want to call it.
But what happen if I put on the flange my 3 kg turntable plate?
With the load of the plate on the flange the ball bearings make almost no audible sound!
I put a stethoscope on the base of the spindle, and still very low noise is audible.
A real test would be hearing a test disk on this system, with a felt mat between the plate and the disk, I think it will be interesting.
Of course the most important thing is to decoupling the base which support the spindle stator from the arm, but this is another issue.
What about rotational error or free play?
No free play at all, and the 31cm plexy disk, (not fixed on the rotor, but only put it on it), on the edge of the plate, I've measured only +/-2 cents (millimeter cents) of error with my dial gauge.
I think is a good result, I've seen a lot of really good turntables wobbling a little bit, and this wobbling was not measured, but visible!
Last test regards the friction of the spindle, I run the 3kg plate put it on the upper flange.
From more or less 30 rpm the plate need 4 minutes and 3 second to complete stop.
What to said if not this vcr head is an interesting object?
Thanks all!!!
Anyway, today afternoon I pick up my daewoo vcr from my garage, and I removed its head.
At the end of the post I attached some picture of the head
Ok, almost all low cost and high end turntables seems to avoiding ball bearing, and for sure there is a valid reason to obtaining for other choices, by the way, I decide to test anyway this ball bearing system.
Well, if the upper flange (I dont know if flange is the proper name, anyway the rotor), is rotating with any load on it, ball bearings produce a very little sound, or hum as you want to call it.
But what happen if I put on the flange my 3 kg turntable plate?
With the load of the plate on the flange the ball bearings make almost no audible sound!
I put a stethoscope on the base of the spindle, and still very low noise is audible.
A real test would be hearing a test disk on this system, with a felt mat between the plate and the disk, I think it will be interesting.
Of course the most important thing is to decoupling the base which support the spindle stator from the arm, but this is another issue.
What about rotational error or free play?
No free play at all, and the 31cm plexy disk, (not fixed on the rotor, but only put it on it), on the edge of the plate, I've measured only +/-2 cents (millimeter cents) of error with my dial gauge.
I think is a good result, I've seen a lot of really good turntables wobbling a little bit, and this wobbling was not measured, but visible!
Last test regards the friction of the spindle, I run the 3kg plate put it on the upper flange.
From more or less 30 rpm the plate need 4 minutes and 3 second to complete stop.
What to said if not this vcr head is an interesting object?
Thanks all!!!
Attachments
giuz0,
Making the shaft very precise can be very difficult for most non machinist.
If you look on ebay ( USA ) under "carbide blanks" you can usually find precision ground tungsten carbide in various lengths and diameters. Then you can build your bearing around the super hard, precision ground shaft. If you choose, you can further polish the shaft using various grades of diamond paste ( also on ebay ) for not much money.
A cheaper alternative would be to buy a piece of linear bearing shaft material in the diameter you choose ( also on ebay ) for not much money. This shaft material is already precision ground and hardened. Just fit some Delrin, Teflon or one if its variants or bearing bronze bushing and you are good to go. Hope this info helps.
Making the shaft very precise can be very difficult for most non machinist.
If you look on ebay ( USA ) under "carbide blanks" you can usually find precision ground tungsten carbide in various lengths and diameters. Then you can build your bearing around the super hard, precision ground shaft. If you choose, you can further polish the shaft using various grades of diamond paste ( also on ebay ) for not much money.
A cheaper alternative would be to buy a piece of linear bearing shaft material in the diameter you choose ( also on ebay ) for not much money. This shaft material is already precision ground and hardened. Just fit some Delrin, Teflon or one if its variants or bearing bronze bushing and you are good to go. Hope this info helps.
FWIW
Oilite NSK mentions at their site that only the sharpest reamers can be used at the penalty of destroying some of the porous material along with it.
Grinding and honing should not be done at all according to them.
Kind of defeats the purpose and that's why it's a little more difficult to use these properly without messing with the bore
Regards
David
Oilite NSK mentions at their site that only the sharpest reamers can be used at the penalty of destroying some of the porous material along with it.
Grinding and honing should not be done at all according to them.
Kind of defeats the purpose and that's why it's a little more difficult to use these properly without messing with the bore
Regards
David
I would imagine you could tweek the ID a little by the amount of press fit. I'd still look at honing a bronze or cast iron bushing to get a perfect fit. Have you talked to any of the local machine shops in your area? A well equipted engine rebuilding or race shop should have what you need. 15mm is more a motorcycle wrist pin size.
BillWojo
BillWojo
Yes, that's the best way ( oilite) Heated body and press fit to what you want.
I have rebuilt too many engines over the years and BTDT
The wrist pin is an excellent idea for the DIYer. Very high Rockwell hardness. Have a few from a CR480 honda dirt bike.
The bronze valve guide and valve is an easy simple way also. Those ream easily.
I have rebuilt too many engines over the years and BTDT
The wrist pin is an excellent idea for the DIYer. Very high Rockwell hardness. Have a few from a CR480 honda dirt bike.
The bronze valve guide and valve is an easy simple way also. Those ream easily.
- Status
- This old topic is closed. If you want to reopen this topic, contact a moderator using the "Report Post" button.
- Home
- Source & Line
- Analogue Source
- DIY turntable spindle bearing tutorial