I was wonder if anyone here builds custom horns? I am new here but not new to the hobby. I need to find a horn maker to start my new build.
Perhaps you could indicate the size of the horns that you are interested in having built...first. There are horns...and there are horns. Size is a factor. I certainly wouldn't try to 3-D print a K-402-sized horn (or any full-range horn for that matter).
Also, if you are thinking about doing something like an MEH (multiple entry horn), that would be of interest in the complexity and build geometries of said horns. If an MEH is the intent, have you considered having built a dual-flare horn, something like this:
Chris
Also, if you are thinking about doing something like an MEH (multiple entry horn), that would be of interest in the complexity and build geometries of said horns. If an MEH is the intent, have you considered having built a dual-flare horn, something like this:
Chris
https://inlowsound.weebly.com/I was wonder if anyone here builds custom horns? I am new here but not new to the hobby. I need to find a horn maker to start my new build.
Perhaps you could indicate the size of the horns that you are interested in having built...first. There are horns...and there are horns. Size is a factor. I certainly wouldn't try to 3-D print a K-402-sized horn (or any full-range horn for that matter).
Also, if you are thinking about doing something like an MEH (multiple entry horn), that would be of interest in the complexity and build geometries of said horns. If an MEH is the intent, have you considered having built a dual-flare horn, something like this:
View attachment 1244027
Chris
I am looking for someone that can build a K402 clone or something similar. I have lots of tools but no CNC although I do have a sliding table saw among other large machines. Never built a horn. I am sure that I am capable but would need you guys to do the design and help me figure out the angles and proportions.
Well, there are a couple of ways to go: you might be able to find someone to do them for you, or you (more likely) can make the horns yourself. I only know offshore DIYers (i.e., non-US) that have attempted a K-402 straight-side/tractrix mouth profile, and one lives in Australia (which, I'm sorry to say has really terrible import/export taxes compared to external EU rates). You might help yourself by thinking about the alternative horn profile/construction methods to doing it yourself.
I would seriously think about a dual flare design, like those used in the construction of Unity or Danley Sound Labs Synergy™ horns, even if you're not going to use multiple midranges and woofers on the same horn as the compression driver, i.e., a typical horn usage. There is a spreadsheet available to help you cut the pieces for the horn. The spreadsheet itself can be found here: http://www.libinst.com/SynergyDIY/V3/Synergy Calc v3.xls, and the pdf help file here: http://libinst.com/SynergyCalc/Synergy Calc V5.pdf. Here is a version of the spreadsheet for a horn that can drop into a Cornwall cabinet (although it will be a a bit thicker than the depth of the Cornwall with compression driver attached (compressed folder below):
The deal with the dual flare horns is that it is nice to smoothly round off the transition from the first flare (near the small end of the horn--the throat), to the secondary flare, to help minimize the so-called impedance bounce that a hard-edged transition presents to the sound source (the compression driver). To do roundover well, you need enough thickness of material to hold a good stiff joint between the two horn flares even after rounding off the transition. I'd recommend at least 1/2" plywood, with 3/4" plywood being even better and stiffer, but heavier.
If you want to build a tractrix-like horn mouth instead, I recommend looking at a kerf bend mouth: https://www.rockler.com/learn/bending-wood-part-i
The side angles of the kerf bent flare pieces joining would be a bit more involved, but I'd recommend prototyping it first to get the right jigs/angles. Additionally, I strongly recommend using some epoxy resin to backfill the remaining kerf slot void areas after horn assembly to regain as much strength and stiffness as possible.
As with everything else, I always strongly recommend waiting to buy the compression drivers only after the horns are built/ready. You may choose to use 1.4" exit compression drivers instead of 2", which have better high frequency polar coverage above 10 kHz (without the use of patented diverging horn lenses at the compression driver/horn interface).
Chris
I would seriously think about a dual flare design, like those used in the construction of Unity or Danley Sound Labs Synergy™ horns, even if you're not going to use multiple midranges and woofers on the same horn as the compression driver, i.e., a typical horn usage. There is a spreadsheet available to help you cut the pieces for the horn. The spreadsheet itself can be found here: http://www.libinst.com/SynergyDIY/V3/Synergy Calc v3.xls, and the pdf help file here: http://libinst.com/SynergyCalc/Synergy Calc V5.pdf. Here is a version of the spreadsheet for a horn that can drop into a Cornwall cabinet (although it will be a a bit thicker than the depth of the Cornwall with compression driver attached (compressed folder below):
The deal with the dual flare horns is that it is nice to smoothly round off the transition from the first flare (near the small end of the horn--the throat), to the secondary flare, to help minimize the so-called impedance bounce that a hard-edged transition presents to the sound source (the compression driver). To do roundover well, you need enough thickness of material to hold a good stiff joint between the two horn flares even after rounding off the transition. I'd recommend at least 1/2" plywood, with 3/4" plywood being even better and stiffer, but heavier.
If you want to build a tractrix-like horn mouth instead, I recommend looking at a kerf bend mouth: https://www.rockler.com/learn/bending-wood-part-i
The side angles of the kerf bent flare pieces joining would be a bit more involved, but I'd recommend prototyping it first to get the right jigs/angles. Additionally, I strongly recommend using some epoxy resin to backfill the remaining kerf slot void areas after horn assembly to regain as much strength and stiffness as possible.
As with everything else, I always strongly recommend waiting to buy the compression drivers only after the horns are built/ready. You may choose to use 1.4" exit compression drivers instead of 2", which have better high frequency polar coverage above 10 kHz (without the use of patented diverging horn lenses at the compression driver/horn interface).
Chris
Attachments
Last edited:
By the way, I think that you could sell horns of a K-402 size/shape once you figured out how to build them--due to pent-up demand. There are others that would pay money to get them (albeit at less cost than that Klipsch charges for their K-402-HF assemblies with attached compression drivers and minimal horn stands). Think about it.
Chris
Chris
Hi, I've built straight-sided/tractix K402 clones, based off the work of the Australian that Chris mentioned.I am looking for someone that can build a K402 clone or something similar. I have lots of tools but no CNC although I do have a sliding table saw among other large machines. Never built a horn. I am sure that I am capable but would need you guys to do the design and help me figure out the angles and proportions.
It's not something I could get involved with again as far as direct help or production, but can happily help point you in the DIY path i took.
Here's a pict...
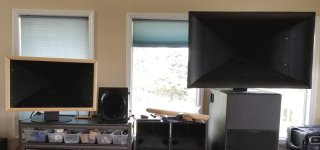
Right side has the secondary tractix flares attached to primary straight-sided horn section ; left side just has roundovers attached to primary horn
(I was comparing polars and listening to see the effect of the added tractix flares.)
The SynCalc spreadsheet Chris linked works great....heck of a gift to the DIY community from Mr Waslo.
If your sliding table saw is very large, the horn panels will be fairly easy to make once you get a feel. My Incra 500 miter table isn't big enough to make them easy.
I really like a plunging tracksaw, used with a 4x8ft table. A sheet of OSB on sawhorses, covered with a 1" sacrificial 4x8 foamboard, makes it really easy compared to a table saw.
The tracticx flares are made out of 2" thick rigid foamboard, using a hot-wire carving knife jig. (also learned from the kind Aussie...sorry can't find the link) yet)
FWIW, and maybe as a helpful motivator to get started with a unity/syn type build...
I've spent a lot of time comparing builds with and without secondary flares.....mainly because the secondary's at least quadruple the build difficulty, not to mention adding a lot of size and weight.
Like here are some straight-sided secondaries...that are removable for A/B comparisons.
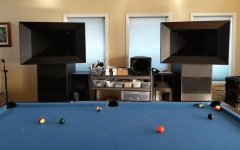
There is no question secondaries, either straight-sided or tractrix improve polar measurements. And everybody on earth knows mouth terminations matter for the smoothest directivity.
What I've found however, is within say a listening window of +/-30 degrees, the measurements don't improve that much (compared to wider angles),
and more importantly...I can't hear much, if any, difference. Maybe I'm just deaf 🙂
Anyway, point is...if you are encouraged to DIY a unity...I'd suggest to first try one without any secondaries.
If nothing else, the learning will be invaluable in avoiding mistakes with a more complicated build that adds them.
I now have all the builds pictured above out in a storage trailer. Here's what replaced them...
Again, fwiw
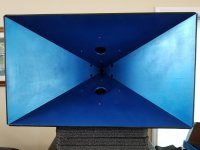
who has an opinion (or data) on making a curved (quadratic?) throat instead of the straight termination that we see on most DIY synergy horns? (and also on actual Klipsch horns)
how much of an effect can be seen on FR, driver loading, etc? obviously the curved throat is more difficult to build.
how much of an effect can be seen on FR, driver loading, etc? obviously the curved throat is more difficult to build.
Its several DIY horns here:
https://www.hifisentralen.no/forume...perlang-byggetråd.64088/page-288#post-3507486
https://www.hifisentralen.no/forume...perlang-byggetråd.64088/page-288#post-3507486
See https://www.stereonet.com/forums/topic/232459-klipsch-k402-replica-build/
Roy D. at Klipsch (their main horn designer) has never spoken clearly or openly about why they use the throat termination geometry that they do on all their horn designs. I do know that I've been using said K-402 horns for over 16 years now, and have no intention of replacing them with anything else. The horns are either compression molded (i.e., the older/25 lb. K-402s) or injection molded (current production 15 lb. horns), so Klipsch could have used a curved throat, like the 1.4" JBL horn used in the JBL Cinema 3732, 4722N loudspeakers if they wanted to do that:
Roy has commented that the curved throat geometries of the oblate spheroid or quadratic throat varieties don't actually work as advertised, and he said it in a way that was unambiguous that he had tried them both, and found them wanting. Remember that horn polar coverage performance is the most important design factor for Roy due to his audience (professional cinema) and their requirements, That means that his horns are optimized for polar coverage and avoidance of throat slots--which is still used by others, but which in my experience sound like loud trumpet players that need to empty out their spit valves when playing above ~4 kHz (2" diameter throat horns, that is).
The problem is: the JBL design is more complex to build (actually, it's much more complex)--you'd have to clone the horn in structural resin to get the shape right. Also unfortunately, it's too small for my needs, while the K-402 is the right size. Also, the JBL horn is 1.4 inch throat, while the K-402 is 2".
You could chop off the throat entrance on the JBL horn at the point where it mates flush with a 2" driver throat, but then you still have the problem of the smaller horn size not controlling polars down to the lower limit of the compression driver's capabilities (for home hi-fi use--not PA use) like a BMS 4592 ND dual diaphragm ring radiator or Radian 950BePB beryllium dome driver (or the more expensive TAD 2" Be diaphragm compression drivers).
Chris
I would try measuring one of each throat geometry to get a definitive answer. But I would not use simulation, however--such as BEM. The fracas over the effectiveness of the horn throat lens to spread out 2" compression driver polars last year (now patented by Klipsch) taught me a lot about horn sims...and unfortunately, a lot more about those running the sims and choosing optimization parameters that I wouldn't choose.who has an opinion (or data) on making a curved (quadratic?) throat instead of the straight termination that we see on most DIY synergy horns? (and also on actual Klipsch horns)
Roy D. at Klipsch (their main horn designer) has never spoken clearly or openly about why they use the throat termination geometry that they do on all their horn designs. I do know that I've been using said K-402 horns for over 16 years now, and have no intention of replacing them with anything else. The horns are either compression molded (i.e., the older/25 lb. K-402s) or injection molded (current production 15 lb. horns), so Klipsch could have used a curved throat, like the 1.4" JBL horn used in the JBL Cinema 3732, 4722N loudspeakers if they wanted to do that:
Roy has commented that the curved throat geometries of the oblate spheroid or quadratic throat varieties don't actually work as advertised, and he said it in a way that was unambiguous that he had tried them both, and found them wanting. Remember that horn polar coverage performance is the most important design factor for Roy due to his audience (professional cinema) and their requirements, That means that his horns are optimized for polar coverage and avoidance of throat slots--which is still used by others, but which in my experience sound like loud trumpet players that need to empty out their spit valves when playing above ~4 kHz (2" diameter throat horns, that is).
The problem is: the JBL design is more complex to build (actually, it's much more complex)--you'd have to clone the horn in structural resin to get the shape right. Also unfortunately, it's too small for my needs, while the K-402 is the right size. Also, the JBL horn is 1.4 inch throat, while the K-402 is 2".
You could chop off the throat entrance on the JBL horn at the point where it mates flush with a 2" driver throat, but then you still have the problem of the smaller horn size not controlling polars down to the lower limit of the compression driver's capabilities (for home hi-fi use--not PA use) like a BMS 4592 ND dual diaphragm ring radiator or Radian 950BePB beryllium dome driver (or the more expensive TAD 2" Be diaphragm compression drivers).
Chris
Last edited:
I guess I should point out that the Klipsch throat design is most probably optimized to drive up the frequencies of any induced horn modes to a frequency where you can't hear them (and the compression drivers likely don't excite them).
No one has said that out loud, but it's clear to me that's what's been implemented (and just about everyone else has missed--i.e., the "DIY horn purists"). It's a slick engineering trade.
Chris
No one has said that out loud, but it's clear to me that's what's been implemented (and just about everyone else has missed--i.e., the "DIY horn purists"). It's a slick engineering trade.
Chris
Thanks Chris. I always assumed the square mouth was a compromise to avoid a complex build.
But I do recall reading somewhere that Tom Danley talked about "getting the horn walls out of the way of the HF as quickly as possible" or something to that effect...
Does the use of a ring vs. dome diaphragm affect this design decision?
But I do recall reading somewhere that Tom Danley talked about "getting the horn walls out of the way of the HF as quickly as possible" or something to that effect...
Does the use of a ring vs. dome diaphragm affect this design decision?
Does the use of a ring vs. dome diaphragm affect this design decision?
Not to me.
If you see the stereonet link above, there are 2 builds, one using foam cut with a hot wire, and the second one using laminated plywood sheets that I shaped with a table saw and electric planer. But there are many other ways.. you could make a mould and fibreglass the whole thing (like the originals), mould it out of concrete or plaster, or simplify it with a straight expansion as calculated in the synergy spreadsheet.
There are lots of different horn profiles/designs you could make, just copy a good existing design that matches your needs to get started.
My next project is a pair of syntripp synergy horns, maybe with tractrix expansions... we'll see
There are lots of different horn profiles/designs you could make, just copy a good existing design that matches your needs to get started.
My next project is a pair of syntripp synergy horns, maybe with tractrix expansions... we'll see
Last edited:
- Home
- Loudspeakers
- Multi-Way
- Custom horns