Hello Micheal .
What can I say ,I love your work .
I have also posted your webpage and this thread link to an
Australian forum .
http://www.stereo.net.au/forums/index.php.
Cheers
What can I say ,I love your work .
I have also posted your webpage and this thread link to an
Australian forum .
http://www.stereo.net.au/forums/index.php.
Cheers
MiWi said:2.) Find your personal concrete-mix. This depends on what cement and what additives you can get an what kind of sand and other additives (pigments etc.) you use.
For first tries refer to the manufacturer datasheets, then start to vary. Our first few attempts were cr*p, but learning by doing is a good way to go. You have to get a feeling for the material first.
[/B]
What mix and additives did you use?
Hi.
Ingrdients (percentage still vary): white cement (high resistance, pressure about 100N/mm², tension without reinforcement 15N/mm²), sand, water, deaerate-additive, flow-additive, glassfibres, pigment if you wish to.
This very special concrete must be mixed with only a water/cement value of appr. 0,15 which is very low.
MiWi said:
Can you be more specific about the flow-additive and the deaerate-additive? Is there a brand name of these products you use, or are they something you make yourself? I can not figure out how you could get such good mold pouring results without the concrete mix being very liquid in nature. However, you say you only use 0.15 water/cement value.
Rgs, JLH
We use products from grace http://www.graceconstruction.com/portal.html
I can´t remember the names.
I got a spec-sheet with the mix in the workshop, which is 30km from here. I can´t find this sheet in the web, but will look at it, next time I´m in the shop, o.k.?
The concret with w/z of about 0.15 is very stiff, but when putting a little energy in it or just wait a few minutes, it starts flowing.
We pour it in the mold and constantly knock just a little bit. To much knocking isn´t good, the flowstone is selfcompressing.
More w/z makes it more fluid but this isn´t good because you get no good results at the top of the mold / at the flange (to mach water at the top). We tried this first, but this way it´s better.
I can´t remember the names.
I got a spec-sheet with the mix in the workshop, which is 30km from here. I can´t find this sheet in the web, but will look at it, next time I´m in the shop, o.k.?
The concret with w/z of about 0.15 is very stiff, but when putting a little energy in it or just wait a few minutes, it starts flowing.
We pour it in the mold and constantly knock just a little bit. To much knocking isn´t good, the flowstone is selfcompressing.
More w/z makes it more fluid but this isn´t good because you get no good results at the top of the mold / at the flange (to mach water at the top). We tried this first, but this way it´s better.
Thank you for the reply.
It looks like everything that is needed to mold horns in the States can be found here--> http://www.smooth-on.com/
Rgs, JLH
It looks like everything that is needed to mold horns in the States can be found here--> http://www.smooth-on.com/
Rgs, JLH
The key words to include in the description of these concrete admixtures would be superplasticizer or hi-range water reducer. These are necessary to make Self Consolidating Concrete (SCC).
These products should be available from most ready-mix concrete sources. Consultation with their admixture representative would likely be helpful to assure material compatibility.
It may be that Euro-based materials will have differing formulations or names. They ship cement across the Atlantic. I don't know about the admixes.
These products should be available from most ready-mix concrete sources. Consultation with their admixture representative would likely be helpful to assure material compatibility.
It may be that Euro-based materials will have differing formulations or names. They ship cement across the Atlantic. I don't know about the admixes.
From what I can see the concrete looks to be difficult to use. I can certainly recommend the cast polyurethanes (as seen in the link above) as I have been having a great deal of success with it (after several failures). The material when cured is strong, lightweight and very very well damped. It is reasonably priced and reasonably easy to work with. In larger castings like waveguides you do need to get the slow cure stuff as the rapid cure can setup before you get a large quantity mixed.
I'm going to try and make a bronze waveguide.
I'm going to try and make a bronze waveguide.
Hi Michael
I'm currently looking at building a turntable plinth and was serioulsy thinking about slate until I saw this. This offers far more possibilities and I've found reading what you've done and the explanations fascinating. Having built folded corner horns myself, partly using using concrete panelled main structures, the finish you've managed to achieve is absolutely fantastic. Congratulations!
Looking at the mixture, it would appear to be more of a true mortar mix rather than concrete as it doesn't have any aggregate - or does it? If so, what particle size did you use? I also take it the sand was a special type. If so, can you advise what it is or provide more details?
You mention you use fibreglass as an ingredient. Was this as strands or as fabric in small pieces? and if the latter, how did you layer this into the mixture to act as rebar?
Cheers
h
I'm currently looking at building a turntable plinth and was serioulsy thinking about slate until I saw this. This offers far more possibilities and I've found reading what you've done and the explanations fascinating. Having built folded corner horns myself, partly using using concrete panelled main structures, the finish you've managed to achieve is absolutely fantastic. Congratulations!

Looking at the mixture, it would appear to be more of a true mortar mix rather than concrete as it doesn't have any aggregate - or does it? If so, what particle size did you use? I also take it the sand was a special type. If so, can you advise what it is or provide more details?
You mention you use fibreglass as an ingredient. Was this as strands or as fabric in small pieces? and if the latter, how did you layer this into the mixture to act as rebar?
Cheers
h
Hi h.
I used quarry sand (0-5mm), but all kinds of sand will do fine with this white cement. I´ve also made some objects with 3-5mm split, which gives a nice effect with the black stones in the white cement.
The fibres are so called short fibres.
Short fibres used for epoxy or polyurethane won´t work. They do not resist the alkaline concrete. This are special reinforcement fibres for concrete. Don´t use the polypropylene fibres usually used for floor screed, because they are far to flexible and are only used to prevent early cracks during hardening process of the floor screed.
The alkaline resistant fibres are mixed in the concrete.
I used quarry sand (0-5mm), but all kinds of sand will do fine with this white cement. I´ve also made some objects with 3-5mm split, which gives a nice effect with the black stones in the white cement.
The fibres are so called short fibres.
Short fibres used for epoxy or polyurethane won´t work. They do not resist the alkaline concrete. This are special reinforcement fibres for concrete. Don´t use the polypropylene fibres usually used for floor screed, because they are far to flexible and are only used to prevent early cracks during hardening process of the floor screed.
The alkaline resistant fibres are mixed in the concrete.
Casting with concrete
Mods: I'm happy if you feel this would be better split into a new thread.
Hi Michael,
I've been admiring the work you've been doing with your concrete horns, and was wondering if you (or anyone else) could offer advice for some casting I want to do.
I've been creating spherical speaker cabinets by cutting rings of MDF, gluing them together, then running them on a home-made lathe. This smooths the outside surface, and leaves the inside edges of the MDF rings untouched.
It's easier to see the results from some renderings than photos of the real objects:
http://spikyfish.com/casting/1.png
http://spikyfish.com/casting/4.png
http://spikyfish.com/casting/5.png
A cross section of the object looks like the image below. The red line indicates the split point - I glue the slices to make two halves (which are later glued together to make a finished box).
http://spikyfish.com/casting/halves.gif
Because of the time it takes to make a single box, I want to try to cast them, probably using concrete. I guess I could cast the two halves separately, then attach them together, but I'd love to be able to cast a single, finished unit.
What I've been wondering about doing is shown in the following image:
http://spikyfish.com/casting/shell.gif
The blue rectangle would be a solid square base plate. The cyan area would be a circular plug, fitting into the mouth of where the object would be cast.
The magenta areas are a two piece mold, for the external shape of the object. Concrete would be pored inside this mold, but obviously, something within the green area is required, to ensure the resulting object is hollow.
Obviously, this internal mold cannot be completely solid, as it couldn't be removed from the finished concrete box, but would have to be strong enough to withstand the concrete pour.
I was thinking that I could take one of the MDF originals (as two halves), and use it to cast an inner mold, which would then be placed within the magenta outer mold (i.e. it would be the volume inside the green area in the above drawing).
Is there something I could mix with sand, that would set it hard enough to mold, but could then be washed from the inside of a cured concrete object? Could I use some form of expanding foam or polystyrene (which could later be removed mechanically, or melted away with thinners)?
I suppose wax would be an obviously choice, but melting away a large volume of wax would be time consuming, and very messy.
Any suggestions greatly welcomed!
Mods: I'm happy if you feel this would be better split into a new thread.
Hi Michael,
I've been admiring the work you've been doing with your concrete horns, and was wondering if you (or anyone else) could offer advice for some casting I want to do.
I've been creating spherical speaker cabinets by cutting rings of MDF, gluing them together, then running them on a home-made lathe. This smooths the outside surface, and leaves the inside edges of the MDF rings untouched.
It's easier to see the results from some renderings than photos of the real objects:
http://spikyfish.com/casting/1.png
http://spikyfish.com/casting/4.png
http://spikyfish.com/casting/5.png
A cross section of the object looks like the image below. The red line indicates the split point - I glue the slices to make two halves (which are later glued together to make a finished box).
http://spikyfish.com/casting/halves.gif
Because of the time it takes to make a single box, I want to try to cast them, probably using concrete. I guess I could cast the two halves separately, then attach them together, but I'd love to be able to cast a single, finished unit.
What I've been wondering about doing is shown in the following image:
http://spikyfish.com/casting/shell.gif
The blue rectangle would be a solid square base plate. The cyan area would be a circular plug, fitting into the mouth of where the object would be cast.
The magenta areas are a two piece mold, for the external shape of the object. Concrete would be pored inside this mold, but obviously, something within the green area is required, to ensure the resulting object is hollow.
Obviously, this internal mold cannot be completely solid, as it couldn't be removed from the finished concrete box, but would have to be strong enough to withstand the concrete pour.
I was thinking that I could take one of the MDF originals (as two halves), and use it to cast an inner mold, which would then be placed within the magenta outer mold (i.e. it would be the volume inside the green area in the above drawing).
Is there something I could mix with sand, that would set it hard enough to mold, but could then be washed from the inside of a cured concrete object? Could I use some form of expanding foam or polystyrene (which could later be removed mechanically, or melted away with thinners)?
I suppose wax would be an obviously choice, but melting away a large volume of wax would be time consuming, and very messy.
Any suggestions greatly welcomed!
You could use a light polyurethane foam cast in a mold and then use as the inner part of the mold. This foam breaks up easily and comes in lots of densities so if one isn't strong enough you go to the next higher density. Casting this stuff is tricky however because it expands so much with a very large force that it can actually blow appart molds if you are not careful. Its expansion rate is unpredictable because the material is so sensitive to heat and humidity. Sometimes you can cast in stages, but this is timne consuming.
Earl - thanks, that sounds ideal.
What I'd thought about was having a circular cap (like the cyan coloured object in the 'shell' drawing), and taking a two part MDF original (like the one shown in the 'halves' drawing).
I'd clamp the two halves together, then add the foam, and put on a cap. This cap would have a hole in the top (say, 1/4" diameter) so would hopefully cause a little pressure to build inside (so the internal mold would be accurate) and any extra would bleed out the hole. Any bleed out could then be removed after curing, then the foam inner transferred inside the outer mold along with the plug.
Does that sound remotely feasible? Do you know of the names of any suitable foam products, as I don't really know where to start?
I guess the outer mold could either be made of a casting rubber, or perhaps a fiberglass skin (which is what I think Michael has been using for his horns).
What I'd thought about was having a circular cap (like the cyan coloured object in the 'shell' drawing), and taking a two part MDF original (like the one shown in the 'halves' drawing).
I'd clamp the two halves together, then add the foam, and put on a cap. This cap would have a hole in the top (say, 1/4" diameter) so would hopefully cause a little pressure to build inside (so the internal mold would be accurate) and any extra would bleed out the hole. Any bleed out could then be removed after curing, then the foam inner transferred inside the outer mold along with the plug.
Does that sound remotely feasible? Do you know of the names of any suitable foam products, as I don't really know where to start?
I guess the outer mold could either be made of a casting rubber, or perhaps a fiberglass skin (which is what I think Michael has been using for his horns).
The problem with the foam is that it exapands long after the mold will fill. What will happen is that the material will expand and fill the hole and cure blocking off the release. Then as the bulk of the material continues to expand, it will do so with a force sufficient to break appart the mold, unless it were say steel or someting else capable of holding this kind of pressure. We have bent steel reinforcing rods with polyurethane expansion. You will just have to experiment. Two or more stages may be required.
Two part foams are avaialble from numerous places here in the US, like US Composites (http://www.shopmaninc.com/). In Aus I don't know where you would get it.
Two part foams are avaialble from numerous places here in the US, like US Composites (http://www.shopmaninc.com/). In Aus I don't know where you would get it.
Hi Michael,
Great work I have bin building back loaded horns and fantasized also over making concrete horns . Or combining exiting horns and drivers.
I am really impressed by your work. I did talk to a bricklayer about concrete and cracks in it. Because I wondered about what a good mixture would be.
He said that when you ad fluid soap in the mixture the concrete is more flexible and won't crack that fast. Cloud be he played jokes on me I don't know. But he seemed serious about it.
Now I have bin 8 years simulating horns. And hve a nice 2 way frontloaded horn concept worked out.
And now I am considering open baffle setup
My active backloaded horn projects. With ti100.
I like your design style and setup.
And in style with your interior very good result.
I would like to hear it.
Let me guess BMS driver?
Regards, Helmuth
Great work I have bin building back loaded horns and fantasized also over making concrete horns . Or combining exiting horns and drivers.
I am really impressed by your work. I did talk to a bricklayer about concrete and cracks in it. Because I wondered about what a good mixture would be.
He said that when you ad fluid soap in the mixture the concrete is more flexible and won't crack that fast. Cloud be he played jokes on me I don't know. But he seemed serious about it.
Now I have bin 8 years simulating horns. And hve a nice 2 way frontloaded horn concept worked out.
And now I am considering open baffle setup

My active backloaded horn projects. With ti100.
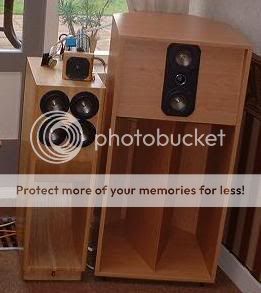
I like your design style and setup.

I would like to hear it.
Let me guess BMS driver?
An externally hosted image should be here but it was not working when we last tested it.
Regards, Helmuth
gedlee said:The problem with the foam is that it exapands long after the mold will fill...
...Two part foams are avaialble from numerous places here in the US, like US Composites (http://www.shopmaninc.com/). In Aus I don't know where you would get it.
Earl - good points, and thanks for the link (though I'm in the UK, not Oz... can't you tell from my accent
The FAQ for that urethane foam indicates expansion for 5 mins, so I guess I could use the plug until foam started to push through (to ensure a good internal mold) then remove it and allow the expansion to finish unobstructed.
Now, one of the things I notice about the product is that it apparently sticks to just about anything. Do you have any idea what I might use to coat MDF in order to prevent adhesion? I guess I could seal the MDF using varnish, then apply some sort of mold release agent before pouring the foam (possibly petroleum jelly?).
The second thing I noticed was that it claims good solvent resistance. This could be more of a problem, as it would mean the foam would have to be mechanically removed after casting the concrete around it (I was planning on doing some mechanical removal, but cleaning up with a solvent). I guess there must be some mold release agent that could be applied to the cured foam, so that the concrete wouldn't stick to it (making the removal process easier).
That has led me to an alternative thought... is there a foam that would be suitable as speaker insulation (something acoustically equivalent to mineral wool/fiberboard)? That way, not all of the foam would have to be removed from the inside of the concrete box - in fact, having a layer of the foam attached to the inside would provide the insulation you'd normally add afterwards. I presume that as a closed cell foam, the urethane wouldn't be suitable for this application?
Helmuth said:...I am really impressed by your work. I did talk to a bricklayer about concrete and cracks in it. Because I wondered about what a good mixture would be....
Helmuth - I think Michael has been using some fairly exotic white concrete (there's info about it earlier on in this thread). I wasn't planning anything quite so special, but was going to look into mixtures later.
I did once find a website of a guy who was casting artistic objects in concrete; from small jewelery items (30mm long) to larger objects (1m long). He had a list of 'recipes' he used for casting different sized objects. I don't have the link with me, but if you did some google searches you'd probably find info on good mixes.
You have to keep in mind that there is is a big difference between "flowing" and "expanding". The material will only flow for a minute or two then its solid enough to block off any ports and it won't flow anymore even if you do open up new ports. It then continues to expand for several more minutes. This is the real problem.
You would have to seal the MDF very well or the poly will stick to it very well. Then use any release agent. The fact that this poly will not disolve is a problem. I have heard that some paint strippers will disolve it. Look into Polystyrene foam. I know nothing about it except that Acetone will disolve it.
Closed cell foam in the enclosure is a no-no, but open cell polyurethane foam, like I use in my waveguides, is an ideal interior material. But its expensive and hard to cut accurately. It could be left in place after the casting, but being open cell the concrete would difuse into it depending on how thin the concrete was.
You would have to seal the MDF very well or the poly will stick to it very well. Then use any release agent. The fact that this poly will not disolve is a problem. I have heard that some paint strippers will disolve it. Look into Polystyrene foam. I know nothing about it except that Acetone will disolve it.
Closed cell foam in the enclosure is a no-no, but open cell polyurethane foam, like I use in my waveguides, is an ideal interior material. But its expensive and hard to cut accurately. It could be left in place after the casting, but being open cell the concrete would difuse into it depending on how thin the concrete was.
Hi Miwi,
It is a long horn for frequencies over 1kHz. So how about horn colouration of high frequencies.
By the knowledge I have one cant prefect the different path length of the high frequencies through the horn.
This is the mayor concern by using large horns. I can imagine that the BMS driver sound good by its low distortion. But horn colouration will always be there IMO when the path through the horn is longer than the wave length.
Did you use a 18sound horn to make the mold for the concrete horn.
Regards Helmuth
It is a long horn for frequencies over 1kHz. So how about horn colouration of high frequencies.
By the knowledge I have one cant prefect the different path length of the high frequencies through the horn.
This is the mayor concern by using large horns. I can imagine that the BMS driver sound good by its low distortion. But horn colouration will always be there IMO when the path through the horn is longer than the wave length.
Did you use a 18sound horn to make the mold for the concrete horn.
Regards Helmuth
- Status
- This old topic is closed. If you want to reopen this topic, contact a moderator using the "Report Post" button.
- Home
- Loudspeakers
- Multi-Way
- Concrete Horns