I vaguely recall reading a paper, a couple of decades ago, about optimizing bracing. It must have been by a British speaker manufacturer. They said that the best bracing for the least amount of "work" (or complexity, or cost, or whatever) would be a panel, slightly smaller than the baffle, with a large elliptical cutout in the middle and placed vertically down the middle of the box, parallel to the baffle (pic below). They would then glue the elliptical cutouts -as well as the circular ones from the drivers, either whole or in pieces- to selectively mass-load the sides and back of the box as needed.
Obviously a manufacturer would try to justify whatever they did even if their motive was mere cost optimization, so a grain of salt there, FWIW. I guess the general idea was to use simple tools, like the ones used to cut the baffle and sides, and not waste any plywood. Also, vibrations would then have to work the length/width of the brace, which combines both rigidity and damping. If true, it is quite an elegant solution. Another such brace could be placed horizontally, between the main drivers, so as to reinforce the weak spot between them as well as the vertical brace. Neither brace would produce an early backwave reflection.
Obviously a manufacturer would try to justify whatever they did even if their motive was mere cost optimization, so a grain of salt there, FWIW. I guess the general idea was to use simple tools, like the ones used to cut the baffle and sides, and not waste any plywood. Also, vibrations would then have to work the length/width of the brace, which combines both rigidity and damping. If true, it is quite an elegant solution. Another such brace could be placed horizontally, between the main drivers, so as to reinforce the weak spot between them as well as the vertical brace. Neither brace would produce an early backwave reflection.
Attachments
Obviously, I can see how adding any kind of brace in the center of a rectangular panel will change the resonant mode from (1,1) to (2,1) and possibly (2,2).
You are thinking about independent panels, not a box. The monopole "BOX" mode has all panels moving like your (1,1) in phase. The dipole BOX mode has opposing panels in the same (1,1) PANEL mode, but now they are out of phase. Think more of a spherical shell than a flat panel, its more accurate.
What has not been mentioned, but probably assumed, is that the panels should be divided unequally.
This way it breaks the resonance mode so that no two panels have the same resonance frequency.
An externally hosted image should be here but it was not working when we last tested it.
+1 This is the advice GM gave to me. 😉 I did the same thing,except my cabinets are dual 15" woofer corner boxes.I also used the window braces that really stiffen them up quite a bit.I staggered them so the spaces were 17",18",19", so they wouldn't have the same resonant freq. 😀 I'm hoping to finish these in the next couple of weeks or so.No small bookshelf's for this Gent !! 😀
An externally hosted image should be here but it was not working when we last tested it.
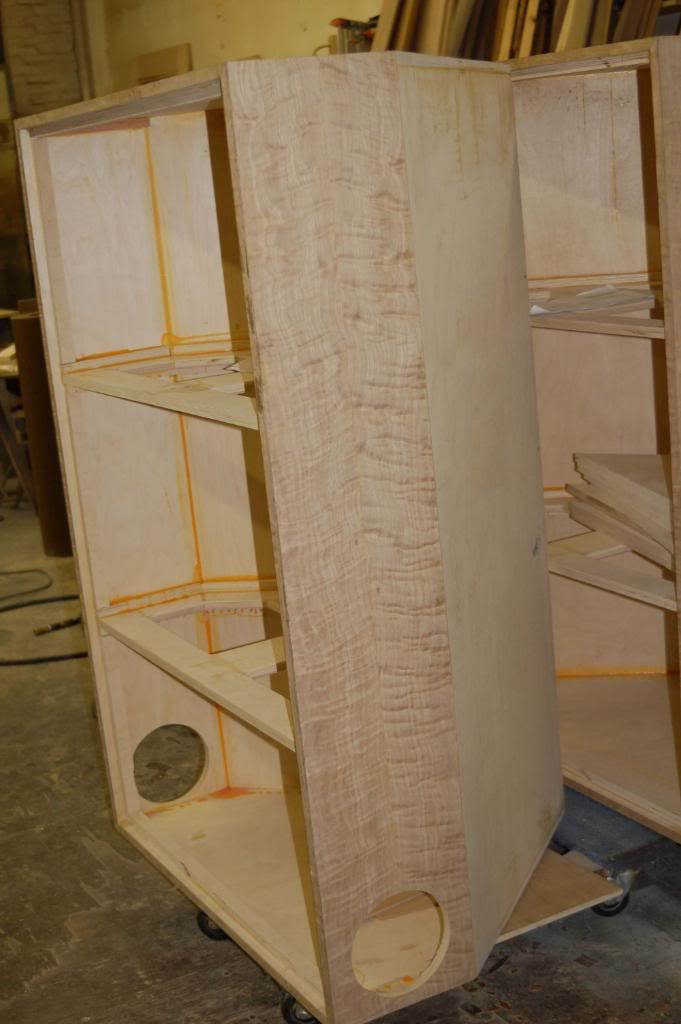
An externally hosted image should be here but it was not working when we last tested it.
Last edited:
+1 This is the advice GM gave to me. 😉 I did the same thing,except my cabinets are dual 15" woofer corner boxes.I also used the window braces that really stiffen them up quite a bit.I staggered them so the spaces were 17",18",19", so they wouldn't have the same resonant freq. 😀 I'm hoping to finish these in the next couple of weeks or so.No small bookshelf's for this Gent !! 😀
Sir! I salute you!!!

An externally hosted image should be here but it was not working when we last tested it.
Looks like tiger maple veneer, is that right? very pretty! I go through the stack of white birch ply at the Home Depot looking for wavy and clear grain. I've got some nice stuff that way.
An externally hosted image should be here but it was not working when we last tested it.
Are you going to screw those boxes to the walls? I think it's a good idea if you do so.
Loren Thank You Kindly !!! 😉Sir! I salute you!!!![]()
Looks like tiger maple veneer, is that right? very pretty!
Thanks ! It's actually "White Tiger Oak" and is very pretty up close and personal. 😀
Are you going to screw those boxes to the walls? I think it's a good idea if you do so.
No these are floorstanders that are pushed into the corner with a 2" base that I still have to make though. I will have lots of measuring to do.I'm gonna use a custom passive XO.I'm using a 511E with a 288 or 299-8A
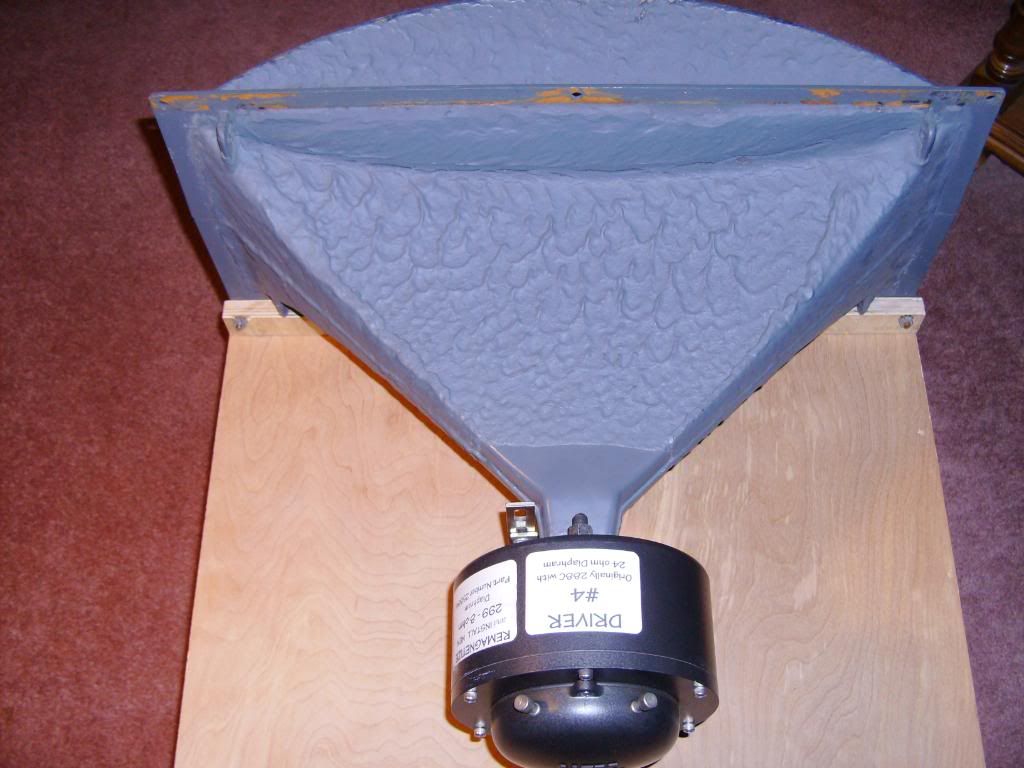
Last edited:
There are excellent articles with measurements done "German style" both in Klang & Ton and in Hobby HiFi. They try ut different braces as well as wall lamination, they own the material so I can not publish it in extenso. But I might write up a summery. (How measurement correlate with perception is an other can of worms that I will keep the lid on for now...)
Interesting read this thread, and not easy to get grip on since so many things affects the outcome. I have a question: since many here talk about the importance to dampen the resonances, what would happen if you used a bracing made from, say, hard rubber? Or something similar that would transform movement to heat. Some suggest damping material on the panel itself, but maybe my suggestion could also help?
There are excellent articles with measurements done "German style" both in Klang & Ton and in Hobby HiFi. They try ut different braces as well as wall lamination, they own the material so I can not publish it in extenso. But I might write up a summery. (How measurement correlate with perception is an other can of worms that I will keep the lid on for now...)
Do you mind sharing the year/number of the issue in which these articles appear? Thanks!
+1 This is the advice GM gave to me. 😉 I did the same thing,except my cabinets are dual 15" woofer corner boxes.I also used the window braces that really stiffen them up quite a bit.I staggered them so the spaces were 17",18",19", so they wouldn't have the same resonant freq. 😀 I'm hoping to finish these in the next couple of weeks or so.No small bookshelf's for this Gent !! 😀
An externally hosted image should be here but it was not working when we last tested it.
![]()
An externally hosted image should be here but it was not working when we last tested it.
Nice looking , unfortunately that enclosure is poorly braced , you are about 40% where you need to be ...
Bracing
I believe in bracing panels securely and making the cabinets as ridged as possible per: weight ratio!Meaning even for me, I do see somethings as overkill also! Back in 2002 or there abouts I read an article in Speaker Builder addressing this subject! In this extensive report they explained how the panels, when braced, created two smaller resonating planes of higher frequency and by adding another brace, creating four resonating planes! However the higher frequencies were considered MUTE having been tuned to an inaudible frequency and the transformation caused a lost of energy which also contributed to less parasitic noise influence! The article also recommended damping of the Drive Units and also touched on shielding the crossover! One point made also: By employing a pair of hardwood strips attached to the back of the baffle board in a vector shape with each leg of the 'V' shape passing over the woofer & tweeter mounting bolts, that the resonances created, would follow the grain direction of said hardwood and directed to the base of the cabinet where it could be bled off through spikes! Trouble with this opinion is I am pulling this from memory and could not, for sure, quote the exact issue of SPBuilder!
I believe in bracing panels securely and making the cabinets as ridged as possible per: weight ratio!Meaning even for me, I do see somethings as overkill also! Back in 2002 or there abouts I read an article in Speaker Builder addressing this subject! In this extensive report they explained how the panels, when braced, created two smaller resonating planes of higher frequency and by adding another brace, creating four resonating planes! However the higher frequencies were considered MUTE having been tuned to an inaudible frequency and the transformation caused a lost of energy which also contributed to less parasitic noise influence! The article also recommended damping of the Drive Units and also touched on shielding the crossover! One point made also: By employing a pair of hardwood strips attached to the back of the baffle board in a vector shape with each leg of the 'V' shape passing over the woofer & tweeter mounting bolts, that the resonances created, would follow the grain direction of said hardwood and directed to the base of the cabinet where it could be bled off through spikes! Trouble with this opinion is I am pulling this from memory and could not, for sure, quote the exact issue of SPBuilder!
Nice looking , unfortunately that enclosure is poorly braced , you are about 40% where you need to be ...
I can't tell how thick his panels are to begin with. But few are discussing the different bass air pressures generated by different designs. When he gets really large, the pounds per square inch is much less, due to the many square inches.
I made some large monitors using B&W matrix bracing techniques. I cut slots in masonite panels and assembled them like the seperators in cardboard wine crates. They put interlocking cardboard sheets into a big cardboard box so that it creates seperate individual sections for each wine bottle. This "matrix" brace as B&W called it, inserts into slots in the cabinet walls. I brushed boat-building epoxy on everything and also glued small strips of wooden moulding strips (with one 90-degree corner and a concave opposite side) to additionally connect every joint. I also slotted some wooden strips to slide over and 'terminate' any ends of the masonite panels where they were cut to accomodate the drivers. The masonite panels also had large holes drilled thru, so that pressure differences would not deflect the panels.
At first I was very disapopointed. Even with somewhat random spacing and different patterns of holes etc. the epoxy/masonite panels were very stiff and when you tapped one they all rang in sympathy, and as they pulled on the opposite-wall panels the braces were like strings of a guitar, made louder by the 'sounding board' speaker panels which I intended to damp.
So I coated the entire interior with automotive undercoating. All the problems went away. The cabinet walls were not particularly strong nor rigid, but when you rapped your knuckles on them they sounded very dead. Then I crammed some ply stuffing into those cubicles where each wine bottle would have gone. By adjusting the size of the opening to each cubicle I could actually create and adjust acoustical structures like little tube traps.
For brush-on or spray-on damping, consider automotive undercoating, clear rubberish automotive rocker schutz as someone else suggested (sometimes called spray-on chip-guard). Or there's a common Home Depot material here in California... I put granite flooring over concrete slab. With our earthquakes, we have to brush a few coats of rubber membrane over the slab before we can put on thinset moratar and granite. That way when there's an earthquake and the concrete cracks, those cracks don't propagate thru the attached granite. It comes in 5-gallon buckets and is bright pink, dries to a deep red. I'm about to apply it to the inside of my current project speakers this weekend. High-quality cheap rubber, it's similar to the stuff you can dip your tool handles into, except it comes in huge quantities for reasonable cost.
At first I was very disapopointed. Even with somewhat random spacing and different patterns of holes etc. the epoxy/masonite panels were very stiff and when you tapped one they all rang in sympathy, and as they pulled on the opposite-wall panels the braces were like strings of a guitar, made louder by the 'sounding board' speaker panels which I intended to damp.
So I coated the entire interior with automotive undercoating. All the problems went away. The cabinet walls were not particularly strong nor rigid, but when you rapped your knuckles on them they sounded very dead. Then I crammed some ply stuffing into those cubicles where each wine bottle would have gone. By adjusting the size of the opening to each cubicle I could actually create and adjust acoustical structures like little tube traps.
For brush-on or spray-on damping, consider automotive undercoating, clear rubberish automotive rocker schutz as someone else suggested (sometimes called spray-on chip-guard). Or there's a common Home Depot material here in California... I put granite flooring over concrete slab. With our earthquakes, we have to brush a few coats of rubber membrane over the slab before we can put on thinset moratar and granite. That way when there's an earthquake and the concrete cracks, those cracks don't propagate thru the attached granite. It comes in 5-gallon buckets and is bright pink, dries to a deep red. I'm about to apply it to the inside of my current project speakers this weekend. High-quality cheap rubber, it's similar to the stuff you can dip your tool handles into, except it comes in huge quantities for reasonable cost.
Last edited:
My new boxes are sealed clamshelled-isobarics. So the air pressures (and rarefactions) generated inside are very high. Isobaric allows you to use a box hafl the volume, but generates pressures in that box that are twice as high. Luckily a smaller box is inherently somewhat more rigid. I'll see whether I can post up some picutres.
The 'constrained' damping ideas expressed here are very interesting. Now that the big cross-panel braces are in place anchoring oppsed walls to each other, perhaps instead of gluing the last few braces of wood scraps onto the walls I might wait until the rubber coating dries and then slap scrap braces on with some more liquid rubber. Instead of anchoring the panel to make an anti-node and raise resonance, it might be better to just remove that energy.
BTW the rubber liquid is heavy.
The 'constrained' damping ideas expressed here are very interesting. Now that the big cross-panel braces are in place anchoring oppsed walls to each other, perhaps instead of gluing the last few braces of wood scraps onto the walls I might wait until the rubber coating dries and then slap scrap braces on with some more liquid rubber. Instead of anchoring the panel to make an anti-node and raise resonance, it might be better to just remove that energy.
BTW the rubber liquid is heavy.
Oh, BTW, Geddes uses the right term. The word is "damp" not "dampen"...unless you mean 'to make wet' or you were being "ironical"
I made some large monitors using B&W matrix bracing techniques. I cut slots in masonite panels and assembled them like the seperators in cardboard wine crates. They put interlocking cardboard sheets into a big cardboard box so that it creates seperate individual sections for each wine bottle. This "matrix" brace as B&W called it, inserts into slots in the cabinet walls. I brushed boat-building epoxy on everything and also glued small strips of wooden moulding strips (with one 90-degree corner and a concave opposite side) to additionally connect every joint. I also slotted some wooden strips to slide over and 'terminate' any ends of the masonite panels where they were cut to accomodate the drivers. The masonite panels also had large holes drilled thru, so that pressure differences would not deflect the panels.
At first I was very disapopointed. Even with somewhat random spacing and different patterns of holes etc. the epoxy/masonite panels were very stiff and when you tapped one they all rang in sympathy, and as they pulled on the opposite-wall panels the braces were like strings of a guitar, made louder by the 'sounding board' speaker panels which I intended to damp.
So I coated the entire interior with automotive undercoating. All the problems went away. The cabinet walls were not particularly strong nor rigid, but when you rapped your knuckles on them they sounded very dead. Then I crammed some ply stuffing into those cubicles where each wine bottle would have gone. By adjusting the size of the opening to each cubicle I could actually create and adjust acoustical structures like little tube traps.
For brush-on or spray-on damping, consider automotive undercoating, clear rubberish automotive rocker schutz as someone else suggested (sometimes called spray-on chip-guard). Or there's a common Home Depot material here in California... I put granite flooring over concrete slab. With our earthquakes, we have to brush a few coats of rubber membrane over the slab before we can put on thinset moratar and granite. That way when there's an earthquake and the concrete cracks, those cracks don't propagate thru the attached granite. It comes in 5-gallon buckets and is bright pink, dries to a deep red. I'm about to apply it to the inside of my current project speakers this weekend. High-quality cheap rubber, it's similar to the stuff you can dip your tool handles into, except it comes in huge quantities for reasonable cost.
Well u may have attempted to build an B&W matrix design , I can assure u they have no such issues ...
The pressure inside any sealed enclosure is not a big deal anyway. For example, my 15" MB drivers have 14mm Xmax peak. Assuming they are using all of their Xmax (unlikely) them the 855cm2 Sd, times 1.4cm equals 1197cc which for the 80L net of the enclosure is not much of a change. It's a bit higher for some large subs in sealed enclosure, but still trivial compared to the strength and rigidity of the materials in the enclosure.My new boxes are sealed clamshelled-isobarics. So the air pressures (and rarefactions) generated inside are very high. Isobaric allows you to use a box hafl the volume, but generates pressures in that box that are twice as high.
WRT to matrix, I've had no trouble building using the technique and getting inert cabs.
I didn't mean to give the wrong impression, like the matrix bracing didn't work or I had some problems with it, the results were excellent though my original cabinet walls were heavier than needed with such excellent bracing. I'm just sharing my experience and the pitfalls to avoid. Stuffing the cavities converts the worst problems into assets. IMHO for cabinets you don't intend to stuff you need to damp the resonances of the panels, and not make them all identical (randomize them). And however you construct them, it's important to bond all the pieces together, especially wherever a panel fits into a slot. Putting some holes in the panels is also a good idea. So is constraining the remaining free ends of the brace panels. But using interlocked sheet for bracing...it's engenious.
The pressure inside any sealed enclosure is not a big deal anyway...For example, my 15" MB drivers have 14mm Xmax peak. Assuming they are using all of their Xmax (unlikely) them the 855cm2 Sd, times 1.4cm equals 1197cc which for the 80L net of the enclosure is not much of a change. It's a bit higher for some large subs in sealed enclosure, but still trivial compared to the strength and rigidity of the materials in the enclosure.
I was talking about sealed subs, and that the forces on the cabinet are doubled in an "equivalent" isobaric. And the major job of the cabinet is not just to deal with the opposite forces generated by moving the mass of the moving elements, it's other and possibly primary job is to absorb the propagation of the pressures and rarefecations that are the reverse-polarity SOUND from the back side of the driver. You seem to think this primary objective is of no concern. That's right if you're just trying to make an air tank that contains one PSI, no big deal. But you're trying to make an absolutely motionless container that doesn't change shape or vibrate at all, for completely contaiing and absorbing a changing pressure. Not as easy, and critically important. Get that idea straight, and you're on the right track toward making effective braces.
Last edited:
- Status
- Not open for further replies.
- Home
- Loudspeakers
- Multi-Way
- Bracing overkill yay or nay ?