I just draw the layout on a piece of paper (or print a 1:1 computer drawing), and use that
as a template to center punch the holes. You can use the same template for both the metal panel
and the insulating panel, so everything will automatically line up properly.
as a template to center punch the holes. You can use the same template for both the metal panel
and the insulating panel, so everything will automatically line up properly.
Nice one! Sounds like an interesting project, especially with a separated display. These things tend to evolve, so don't beat yourself up about the planning. I've just finished giving my own preamp a major face-lift, 30 years after having gotten it working but looking like a state and thinking that'll do. She's always been a trooper, but she's reel purdy now!
If you have no access to published specification; I'd use some vernier calipers for measurement, so you can work out hole centres from the edges and diameter of the sockets.
Print or draw outlines of the over-sized (I'm guessing 12 - 13mm) socket holes and 2 x (4mm?) screw holes and centre lines. Stick them to the case good with 3M spraymount ideally (or double sided tape, or whatever). Draw or print the centre lines for the holes on another bit of paper and stick it to some spare 3mm+ thick metal or plastic (or scribe these marking lines on it) as a template guide. Carefully punch, centre drill, then pilot some small holes in this guide piece, then stick that to the case with masking tape (or a clamp) to align with the stuck hole and centre pattern, for drilling the same sized small pilot holes through into the case. Drill out the screw holes to 3mm. The screw holes could potentially be a bit oversized (4mm?) to give the PCB fit some wiggle room (or for isolating the screws) and you can always use pan head screws. (I guess the phono socket modules take those blunt self tapping style screws, do they?) You may wish to use these holes as you drill them to firmly secure the template guide to the case, while drilling other pilot holes.
Remove the template guide and drill out the 8 pilot holes slightly undersize, in case of drift. Then file them out carefully to the printed oversized outlines. For example, you may wish to go from a 3mm pilot to 12mm final hole size in stages of 6mm, then 9mm, to preserve the centre positions. If you then end with an 11mm bit, there can be 0.5mm of file clean-up around each hole, which might account for any drift in the drilling. This may not be necessary if the pilots are well drilled, of course, but is a way to assess and gain lost accuracy. The stuck paper guide should act as slight protection too. (Step drills will make a mess of it.) Try keeping the case firmly secured if filing, and use purposeful, considered, vertical strokes only. Hold both ends of the circular file. Finish with 150, then 300 grit paper wrapped on the file to remove file marks.
If you do want to isolate the sockets from the amp chassis, then the screws will somehow need a sleeved insulating washer (you could use a TO3 isolating spacer, for example) and not be able to touch the sides of the holes drilled for them. But I doubt these sockets do need to be isolated, since they seem designed to make contact and are depicted that way on your link picture.
These phono holes are big, so their accuracy of fit to the socket is not that vital. The accuracy is in the positioning of the 2 screw holes in relation to the PCB in your case, then in the relationship of those 8 phono holes to those screw holes. So even if they are off; if they're big enough, you won't really notice, since the sockets themselves will always be aligned.
Apologies if any if this is stating the obvious, missing the mark, or appears over-complicated. This all can be done with a hand drill, although I hope it's a powered one!
If you have no access to published specification; I'd use some vernier calipers for measurement, so you can work out hole centres from the edges and diameter of the sockets.
Print or draw outlines of the over-sized (I'm guessing 12 - 13mm) socket holes and 2 x (4mm?) screw holes and centre lines. Stick them to the case good with 3M spraymount ideally (or double sided tape, or whatever). Draw or print the centre lines for the holes on another bit of paper and stick it to some spare 3mm+ thick metal or plastic (or scribe these marking lines on it) as a template guide. Carefully punch, centre drill, then pilot some small holes in this guide piece, then stick that to the case with masking tape (or a clamp) to align with the stuck hole and centre pattern, for drilling the same sized small pilot holes through into the case. Drill out the screw holes to 3mm. The screw holes could potentially be a bit oversized (4mm?) to give the PCB fit some wiggle room (or for isolating the screws) and you can always use pan head screws. (I guess the phono socket modules take those blunt self tapping style screws, do they?) You may wish to use these holes as you drill them to firmly secure the template guide to the case, while drilling other pilot holes.
Remove the template guide and drill out the 8 pilot holes slightly undersize, in case of drift. Then file them out carefully to the printed oversized outlines. For example, you may wish to go from a 3mm pilot to 12mm final hole size in stages of 6mm, then 9mm, to preserve the centre positions. If you then end with an 11mm bit, there can be 0.5mm of file clean-up around each hole, which might account for any drift in the drilling. This may not be necessary if the pilots are well drilled, of course, but is a way to assess and gain lost accuracy. The stuck paper guide should act as slight protection too. (Step drills will make a mess of it.) Try keeping the case firmly secured if filing, and use purposeful, considered, vertical strokes only. Hold both ends of the circular file. Finish with 150, then 300 grit paper wrapped on the file to remove file marks.
If you do want to isolate the sockets from the amp chassis, then the screws will somehow need a sleeved insulating washer (you could use a TO3 isolating spacer, for example) and not be able to touch the sides of the holes drilled for them. But I doubt these sockets do need to be isolated, since they seem designed to make contact and are depicted that way on your link picture.
These phono holes are big, so their accuracy of fit to the socket is not that vital. The accuracy is in the positioning of the 2 screw holes in relation to the PCB in your case, then in the relationship of those 8 phono holes to those screw holes. So even if they are off; if they're big enough, you won't really notice, since the sockets themselves will always be aligned.
Apologies if any if this is stating the obvious, missing the mark, or appears over-complicated. This all can be done with a hand drill, although I hope it's a powered one!
How about a chassis punch? Much cleaner, and it will work for both materials.I don't have a drill press, but if I drill the case I will need to use a hand drill.
Last edited:
Two screws. I cut those holes with a step bit.
I use the one on the right in this picture. 3/8 should do. I put a piece of paper over the RCA jacks and punch it where the centre holes are. Then, I use that as a template to drill the chassis. I always use a hand drill for this stuff... My drill press is not as good in reality.
Measure yours, but most of them are the same layout:
I use the middle bit one to get to 3/8, then go one more step with the one on the right (13/32).
I use the one on the right in this picture. 3/8 should do. I put a piece of paper over the RCA jacks and punch it where the centre holes are. Then, I use that as a template to drill the chassis. I always use a hand drill for this stuff... My drill press is not as good in reality.
Measure yours, but most of them are the same layout:
I use the middle bit one to get to 3/8, then go one more step with the one on the right (13/32).
Last edited:
I didn't know that was an option- that's a great idea! @dizGB I do have calipers so I can take measurements and draw some templates. What software would you recommend for creating those CADs? Hell if the spacing is logical I could probably just pencil in the center holes on the case and then go from there. And yea the fact that all the components of the amp work OK is enough of a triumph for me. I can refine and fine tune as I go.How about a chassis punch? Much cleaner, and it will work for both materials.
Exactly. Typically RCA sockets have those grounded collars to get good electromagnetic/RF shielding around the sockets. That can be necessary to pass EMC tests.I completely agree - it seems these particular sockets were obviously designed to be part of a ground plane - perhaps attached to a metalised plastic sheet, inside of a moulded plastic case, or something like that. Else, why have the metallic screw hole and excess metal around the sockets?
Tom
Step bit in a drill press at 500 RPM is my go-to for stuff like this. Pre-drill with regular drills until you reach the smallest step on the step drill. Clamp the workpiece! Use cutting fluid!I cut those holes with a step bit.
Why not just draw a 14 mm square with a ruler? Then draw the two diagonals and you have the centre location as well. I'd use a machinist's ruler for this, but in reality the LINEX 2616 I picked up in grade school would do just as well.I put a piece of paper over the RCA jacks and punch it where the centre holes are.
Tom
I use my step bit in a impact driver. When I get close to the actual size I need, I back off the speed and pressure, and them I ream out the backside of the hole with the next step on the bit. I don't use cutting oil usually, but if I was working thicker material, I would.
You can use lard (for steel) according to my tap and die set.
Here's the result in 0.4mm mild steel.
You can use lard (for steel) according to my tap and die set.
Here's the result in 0.4mm mild steel.
I didn't know that was an option- that's a great idea! @dizGB I do have calipers so I can take measurements and draw some templates. What software would you recommend for creating those CADs? Hell if the spacing is logical I could probably just pencil in the center holes on the case and then go from there. And yea the fact that all the components of the amp work OK is enough of a triumph for me. I can refine and fine tune as I go.
In case you decide to draw something up, I can recommend LibreCAD. https://librecad.org/
A punch would be a great idea, but depends on thickness of your case and access to where you want the holes. You also would need the correct size punch. I think the holes would be too close together for a step drill to maintain accuracy, especially by hand without a stand, but I'm no expert, only an enthusiastic amateur.
As for drawing programs, right now I'd do it by hand, since I have some circle guides. something like this would be printed on anything that can make a 1:1 line print. I used to love Fusion360, until they wanted paying for it! There are too many options to choose from really, especially with something this simple as thin lines and thin circles. I'm still bitter from being reduced to Tinkercad.
EDIT: I'd add that you can get super precise accuracy from scribing, especially if you can punch to the grooved crossing scribe lines. Having a height gauge would come in very handy for this type of thing, although you can end up with unsightly scratches on your case, if you're not careful.
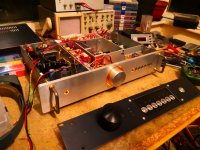
I thought at this stage I'd introduce some of my own work to show I'm not just talking shite. This is my preamp, recently refreshed, after decades of service. The old panel is below. I rustled up some "floating back-lit" push-buttons in 10mm Alu plate. The big knob is in the middle because I only had 2 short bits of plate! I did a new back panel too, but that was only 3mm thick.
As for drawing programs, right now I'd do it by hand, since I have some circle guides. something like this would be printed on anything that can make a 1:1 line print. I used to love Fusion360, until they wanted paying for it! There are too many options to choose from really, especially with something this simple as thin lines and thin circles. I'm still bitter from being reduced to Tinkercad.
EDIT: I'd add that you can get super precise accuracy from scribing, especially if you can punch to the grooved crossing scribe lines. Having a height gauge would come in very handy for this type of thing, although you can end up with unsightly scratches on your case, if you're not careful.
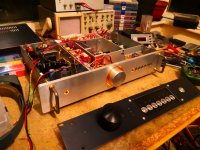
I thought at this stage I'd introduce some of my own work to show I'm not just talking shite. This is my preamp, recently refreshed, after decades of service. The old panel is below. I rustled up some "floating back-lit" push-buttons in 10mm Alu plate. The big knob is in the middle because I only had 2 short bits of plate! I did a new back panel too, but that was only 3mm thick.
Last edited:
The technical reason why step drills may be less accurate than twist drills is that they tend to only have 1 flute, so cut on one side. This detracts in centre precision from a twist drill that cuts on both sides, which may be aggravated by lack of support from a drill press.
Last edited:
No way can you use a step drill and have accurately placed, clean round holes with hand work.The technical reason why step drills may be less accurate than twist drills is that they tend to only have 1 flute, so cut on one side. This detracts in centre precision from a twist drill that cuts on both sides, which may be aggravated by lack of support from a drill press.
This requires a center punch to fix the hole locations, and then a drill press, bench punch, or chassis punch.
The bench punch has the advantage of not needing to drill any pilot holes.
Accurate enough for RCA jacks on an amplifier, and all of the other mounting holes for the PCBs I mount. I even used to use it for tube socket holes before I got a punch set. The smallest hole is 7/8" though so not useful for RCA.
I bought a drill press and never use it. It collects dust in a storage locker.
I bought a drill press and never use it. It collects dust in a storage locker.
Last time I used a step drill it was by hand.No way can you use a step drill and have accurately placed, clean round holes with hand work.
Couldn't fit the box under the bench drill.
Drilled small pilot followed by largest standard drill I could, followed by step drill.
Tricky part was knowing when to stop, knowing when I had reached the right diameter step.
Surely it depends on the material hardness and thickness you're drilling: You can't escape the physics of the lack of symmetrical cutting surfaces on a step drill, compared to a twill drill bit. Punches would require a press, or certainly more clearance around the hole you are making (for support) than a drill bit, which my be relevant if you're drilling near the edges of a case.
To say a drill press is "useless" for increasing accuracy is tantamount to Luddism.
To say a drill press is "useless" for increasing accuracy is tantamount to Luddism.
That's what a chassis punch is for, and what we've always used for one-off construction.Last time I used a step drill it was by hand.
Couldn't fit the box under the bench drill.
Until today I did not know what a chassis punch was. This might come in handy one day... thanks!
I certainly believe that people have done these kinds of holes with a handheld drill. However, if someone else has material which is thicker/harder, or their drill is less powerful, they might get different results. There's only one way to find out!
I certainly believe that people have done these kinds of holes with a handheld drill. However, if someone else has material which is thicker/harder, or their drill is less powerful, they might get different results. There's only one way to find out!
You really need a drill press for drilling accurate, clean holes over 1/4" or so,
not to mention for thicker material.
Chassis punches are good for DIY, though they are usually only intended for 1/16" aluminum
or 1/32" steel. I have gone thicker, but it takes torque and lube.
not to mention for thicker material.
Chassis punches are good for DIY, though they are usually only intended for 1/16" aluminum
or 1/32" steel. I have gone thicker, but it takes torque and lube.
- Home
- Design & Build
- Construction Tips
- Best way to mount RCA board to amp chassis?