I'm liking that TAD setup, the way they do the sides. Enough bracing to park a tank on too.
There are many similar boxes, these just the largest.
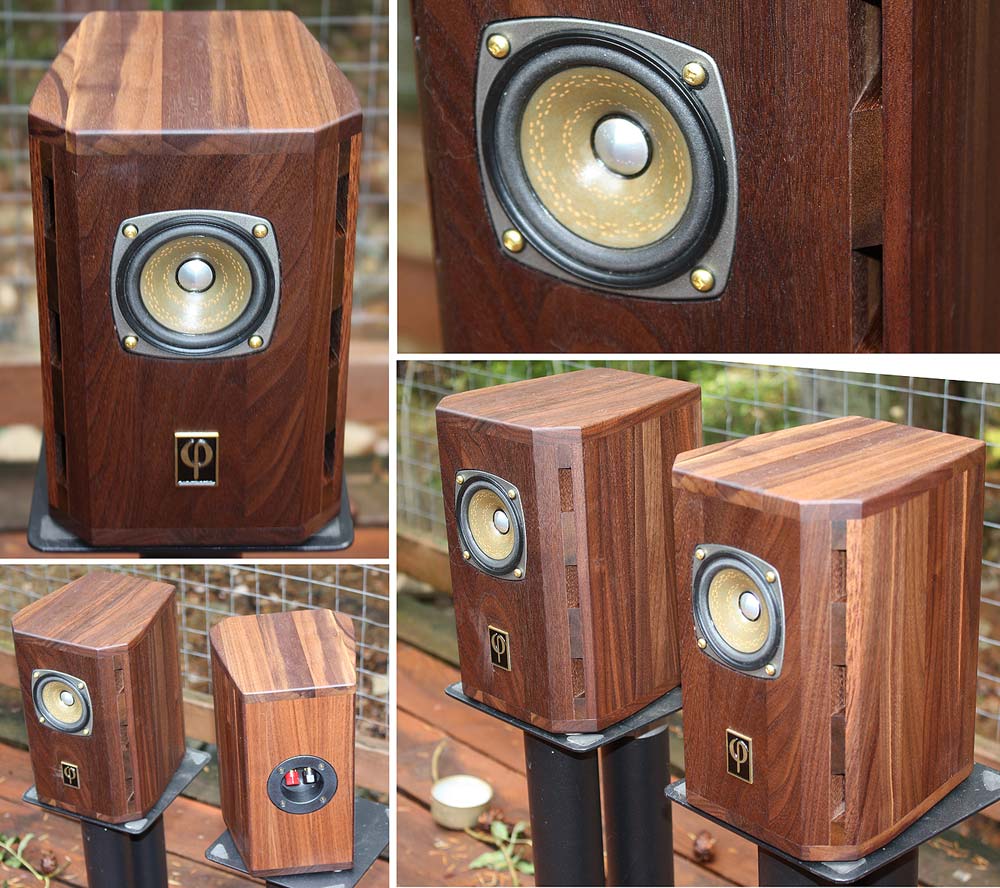
The shape, when looking in plan, approximates a teardrop.

dave
Yes, but which is more important?Intensity is important. Intensity decreases with distance from the source, or more accurately they are spread out more (assumming an approx circular source).
dave
Based on planet10's example of wide baffle, I am working on a scaled down version...

LS1v2 | Grimm Audio
dave
Is that because diffractions in the vertical plane are less detrimental to imagery? They will still cause ripples in the frequency response.In many speakers you only really need to worry about the vertical edges.
If the diffraction were only taken care of then we wouldn't be having this conversation.
Obviously. 🙂 The subject keeps coming up though, I think it's interesting.
Is that because diffractions in the vertical plane are less detrimental to imagery? They will still cause ripples in the frequency response.
Typically vertical diffraction (ie from the top edge) is not as great an issue. Diffraction off the sides will directly affect image/soundstage.
dave
Well, there you have it 😉
It occurred to me after the fact, that putting something as wide as a the shelf on the shelf might be a little hard to sell.
A foamcore build can be done that is both very stiff, very light, and constrained layer.
dave
I was recalling the frequency of the many samples of cf composite that I’ve handled, nearly akin to aluminum, and very expensive.
For something more than the fraction of a watt that foam cor will support, have you tried DiBond composite panels? I once made a subwoofer from a rotomolded bin as a teenager, a lesson learned there, sounded ok at very low levels…
The DiBond panels use a system of very thin aluminum skins with a polyethylene core, are many other brands using the same concept for signage, architectural cladding. The polyethylene is pretty good at damping.
Unfortunately are only available up to 6mm section if I recall, would require bonding, but can be formed into curved profiles.
DiBond seems similar to Alucobond which we considered once as a building skin material.
Alucobond(R) USA
Alucobond(R) USA
Years ago I made a fiberglass/marine honeycomb woofer box for my car. I don't think I ever managed to get it sounding even half way decent. I definitely see how problems may be inherent with composites, regarding acoustics.
About your aluminum to cfrp comparison- the properties of those two are very different, albeit I can see why they would behave acoustically similar, in that they are both way, way, stiffer than wood. Still, the average carbon composite is over twice as stiff as AL alloy. And it's about 40x stiffer than MDF assuming correct fiber orientation. But I believe carbon has positive damping properties, where aluminum is notorious for being harsh. Just put any cyclist through a punishing ride on a carbon frame vs an aluminum. It's gonna be 100% of the test subjects complaining that the AL frame beat the hell out of them, compared to carbon. I wonder that carbon is just so stiff that it cannot be made thin enough to 'give' in a way that's required. This has been a classic problem in the ski/snowboard industry, where historically carbon was rarely implemented because it made the boards so darn stiff. Still, high-end cabs are out there, like the Magico (cfrp/al honeycomb). Not to mention there are great performing carbon instruments.
It's got to come down to implementation IMO. I can contradict everything I just said by bringing the modulus of steel into the mix. It's about 25% stiffer than standard issue carbon/epoxy and yet steel frame bikes are the most compliant. Of the three, aluminum is the least stiff, by over 2x, and is the 'harshest material. Steel is the stiffest and is the most forgiving. This is to do with other factors. Steel is also hard and ductile and can be drawn to very thin walls and still be safe. To get the same compliance with carbon, it may be that the walls are too thin, and hey, it's half plastic, so easily damaged. Aluminum is so much less stiff, and much lower in tensile strength, that it has to take advantage of much larger physical geometry, i.e. larger tubing diameter. Yet AL frame bikes tend to be among the lightest because al is just that much lighter than steel. If you up your tube diameter with steel to increase the stiffness, you then hit a limit because the walls are now too thin to be safe; but if you maintain wall thickness your steel frame weighs twice that of the AL one.
For me, the main advantage of carbon is that it's easy to work with and much cheaper than metals. The reason it is cheaper than metals is that most of the metal is ultimately waste material because the process is subtractive. With composites you only use what you need. Plus it's obvious other advantages like being super lightweight.
The ultimate material, I'm talking real word here, not diamonds, would be something like gray cast iron. Products like Durabar gray iron are a sort of gold standard when it comes to vibration damping and stability, which is why it is the top choice for frames and bases of large precision machinery. A Durabar cabinet would be insane! Heavily insane!
About your aluminum to cfrp comparison- the properties of those two are very different, albeit I can see why they would behave acoustically similar, in that they are both way, way, stiffer than wood. Still, the average carbon composite is over twice as stiff as AL alloy. And it's about 40x stiffer than MDF assuming correct fiber orientation. But I believe carbon has positive damping properties, where aluminum is notorious for being harsh. Just put any cyclist through a punishing ride on a carbon frame vs an aluminum. It's gonna be 100% of the test subjects complaining that the AL frame beat the hell out of them, compared to carbon. I wonder that carbon is just so stiff that it cannot be made thin enough to 'give' in a way that's required. This has been a classic problem in the ski/snowboard industry, where historically carbon was rarely implemented because it made the boards so darn stiff. Still, high-end cabs are out there, like the Magico (cfrp/al honeycomb). Not to mention there are great performing carbon instruments.
It's got to come down to implementation IMO. I can contradict everything I just said by bringing the modulus of steel into the mix. It's about 25% stiffer than standard issue carbon/epoxy and yet steel frame bikes are the most compliant. Of the three, aluminum is the least stiff, by over 2x, and is the 'harshest material. Steel is the stiffest and is the most forgiving. This is to do with other factors. Steel is also hard and ductile and can be drawn to very thin walls and still be safe. To get the same compliance with carbon, it may be that the walls are too thin, and hey, it's half plastic, so easily damaged. Aluminum is so much less stiff, and much lower in tensile strength, that it has to take advantage of much larger physical geometry, i.e. larger tubing diameter. Yet AL frame bikes tend to be among the lightest because al is just that much lighter than steel. If you up your tube diameter with steel to increase the stiffness, you then hit a limit because the walls are now too thin to be safe; but if you maintain wall thickness your steel frame weighs twice that of the AL one.
For me, the main advantage of carbon is that it's easy to work with and much cheaper than metals. The reason it is cheaper than metals is that most of the metal is ultimately waste material because the process is subtractive. With composites you only use what you need. Plus it's obvious other advantages like being super lightweight.
The ultimate material, I'm talking real word here, not diamonds, would be something like gray cast iron. Products like Durabar gray iron are a sort of gold standard when it comes to vibration damping and stability, which is why it is the top choice for frames and bases of large precision machinery. A Durabar cabinet would be insane! Heavily insane!
Attachments
For anyone wanting to do quick material stiffness modeling...
Use wood for, well, wood. Use Nylon for MDF as it should be closer. Depending on the wood, it's about 2x to 3x stiffer than MDF.
ENGINEERING.com | Beam Deflection Calculators
Use wood for, well, wood. Use Nylon for MDF as it should be closer. Depending on the wood, it's about 2x to 3x stiffer than MDF.
ENGINEERING.com | Beam Deflection Calculators
Use wood for, well, wood.
You want a stiff “wood” panel? Stranded (fossilized) banmboo plywood.
PlybooStrand(R) Bamboo Plywood and Veneer - Plyboo by Smith & Fong
dave
I'm sort of a composite tech. machinist hybrid. Started out in aerospace composites, late 90s, then got into machining/mfg about ten years ago. Tbh, most of my time is blown on cad modeling though. A lot cheaper to model stuff 😀. But I'm dead set on doing a composite Purifi build, IRL-
I think that there are much more effective ways to achieve a great sounding speaker without jet fighter technology for a cabinet. I prefer higher density polyethylene for a baffle myself.
If your goal is to make high priced speakers then that’s another thing.
I do by the way own what was likely worlds first carbon fiber skateboard however.
If your goal is to make high priced speakers then that’s another thing.
I do by the way own what was likely worlds first carbon fiber skateboard however.
I used this stuff to get a 44mm edge radius. Costs $50 out the door for 12 feet to my local hardware store.
Moulding | Fypon Decorative Millwork
I've done listening tests and measurements w/ and w/o the edge. If I mess with the tweeter timing to make it come way sooner than anything it makes it easier to hear a difference. IMO a large edge makes high-frequency things harder to localize.
Don't forget you can simulate an edge radius in virtuixcad's baffle sim.
My speaker is still a WIP.
Moulding | Fypon Decorative Millwork
I've done listening tests and measurements w/ and w/o the edge. If I mess with the tweeter timing to make it come way sooner than anything it makes it easier to hear a difference. IMO a large edge makes high-frequency things harder to localize.
Don't forget you can simulate an edge radius in virtuixcad's baffle sim.
My speaker is still a WIP.
Attachments
- Home
- Loudspeakers
- Multi-Way
- Baffle Design....Diffraction and Crammed Tweeter?