I just thought I’d drop a note (a long note) here about my recent experiences which I hope will help anyone who considers using solid wood as speaker cabinet building material. If you don’t want to read my story, you can go to the end and see my conclusions.
I’d like to start out by saying that I love working with solid wood; building entertainment units, shelves, and most of all speakers. I especially like working with thick slabs of heavy wood. It’s hard to explain but it feels like you’re carving and moulding your speaker cabinets instead of assembling panels. Which of course is nonsense, but I’m a tactile aesthetic kind of person; the kind of intolerable amateur woodworker who is always running a hand along a sanded surface and smiling. It makes me happy.
To be clear, I’ve got no beef with MDF or plywood – I have built two sets of speakers using MDF and one with ply – I just loved working on all the speakers I built with solid wood. I know the risks of building with a totally organic material like solid wood and I understand the extra care required in the treatment of the material, but I also appreciate that with care you can achieve furniture grade results. And my wife appreciates it too. Which is one of the reasons I can get away with filling our house with big speakers.
The speakers which this story is about are 1.45m tall floor-standers made of 31mm panels of solid Pacific Maple which give a lovely gold/tan/red colour in the grain. The back panel and bottom panel were made of a sandwich of ply and MDF because I had to cut costs somewhere. Wood is expensive.
The basic details of the speakers are below for those who are interested:
• Tweeter: Scan-speak D2905/9900
• Mid = Eton 7-360/37
• Woofers = 2 x Scan-speak 25W/8565-01
• Net internal volume of 133 litres with rear firing port tuned to 22Hz
I won’t go into the crossover details here because there were seven revisions since the original crossover design… I like to tinker.
It had third order filters with some impedance equalisation, mid smoothing and tweeter attenuation.
I was younger back then and I make no apologies for loving bass that went boom. Yes, I know it was wrong: I measured a 6dB peak around 50Hz – 60Hz, but I left it and I loved it! I listened to a lot more dance music back then.
Anyway, I finished building the speakers in 2008 when I was living in the Crows Nest area of Sydney. Crows Nest is surrounded by water inlets, dripping forests, is reasonably close to the beach, is at sea level, and not least of all quite close to that big harbour of Sydney. All those points add up to humidity levels between 50% and 95% every day – hot or cold. Which is fine because the wood I used was purchased from a supplier in the local area. The speakers lived quite happily in Crows Nest for seven years without any sign of wear or damage. It seemed like they would be upsetting neighbours for decades to come.
This time last year, some big changes happened in our lives and we had to move to Canberra. Canberra is an inland town, surrounded by cleared farmland, is at altitude, and has no natural waterways. There is no humidity to speak of whether it’s hot, cold or even raining. Canberra, although being a lovely town, is practically a desert.
After about three months of living in Canberra I noticed some cracks appearing in a few of the joints of the speakers. A month later the cracks had broadened and a few more had appeared in other joints. Almost all the panels had cracked in some way except for the ply/MDF back panel.
You can see in the picture the dark line where the front panel is pulling away from the sides. The top panel is also separating.
I found a local timber yard and furniture maker called Thor’s Hammer (great name!) which was recommended by friends who had bought furniture from them. I spoke to a bloke there named Gerry and told him about my situation. He said, “Yeah, that will happen. You should expect the moisture content to drop by about 12%, which means a lot of shrinkage.”
I asked if there was anything I could do to stop the moisture loss like sanding back and using oil to seal instead of varnish or something. The wood was expensive and I didn’t want to start again. Could I strengthen the joints?
“Nope. It’s going to shrink anyway. The joints are probably fine. The best you can do is leave it another couple of months to make sure the wood has reached the point where it’s as dry as it’s going to get, then sand back the varnish, fill the gaps with resin, sand back again, and use a flexible natural finish like oil.”
I had some time while I waited for the speaker cabinets to find their natural Canberra level of moisture and I figured if I was going to have to pull the speakers down, then I may as well tinker some more. I always thought the speakers sounded good (in all their versions), but the bass really was boomy with too much excursion. I’m older and …well … just older now and don’t appreciate the boom quite as much. I fired up Soundeasy and got designing. After a couple of months of designing and comparing options, I decided since the cabinets were already huge I could quite easily turn them into a transmission line.
I replaced the ply/MDF back panels with solid Pacific Maple like the rest of the cabinet. Sourced locally in Canberra. I took some more advice from Thor’s Hammer and left the lengths of wood inside to season for a month before joining lengths and cutting them into panels. This was also to find their moisture equilibrium.
Four months of repairing, woodworking, construction and a lot of sanding later, I have functioning speakers again. I used oil instead of varnish, which made the wood grain in the cabinets a little darker, but nicer looking. I finished a few months ago, but I let them settle in before I wrote this just to make sure there wasn’t going to be any more movement. So far, all good.
The only issue I have with the gaps now is my own mistakes I made with the resin. Otherwise it’s smooth to the touch (I ran my hand along many times), and they have a bit of a reclaimed timber look about it. From one metre away you can’t tell that there were ever any gaps.
As for the sound, this was my first attempt at a transmission line and it lead to a lot of tinkering… I was in heaven! I had my measurement mic out every weekend for months! I had some phase issues which resulted in a slightly unorthodox fourth order filter for the woofers and third order for the mid and tweeter which did the trick. I did a lot of experimenting and ended up with lots of heavy stuffing in the transmission line which seemed to have only a little effect on the bass extension, but did tighten it up nicely. I now understand what people mean when they say their transmission line has tight and clean bass. It really is something different to the ported and sealed enclosures I’ve built. It goes deeper without lots of cone excursion and kickdrums have a nice clean “thump” without the boom. That’s all the subjective remarks I’ll make.
I am very happy with the results. So, this is a precautionary tale but like all good stories, the main character learns a thing or two along the way and it has a happy ending.
In conclusion, if you choose to build with solid wood:
• Solid wood behaves like a live material – it expands and contracts with moisture levels.
• If you build with solid wood be aware that moving to a different climate may cause your panels to split or buckle.
• Source your wood locally and season it. If possible leave it inside your house for a month or two before you build.
• Don’t be scared off. There are ways to repair the damage from split wood, but not ways to stop it.
I’m sorry this ended up so long. I started typing and it just went on.
I hope this has been helpful to anyone who considers using solid wood. I intend to continue using solid wood.
AJ
I’d like to start out by saying that I love working with solid wood; building entertainment units, shelves, and most of all speakers. I especially like working with thick slabs of heavy wood. It’s hard to explain but it feels like you’re carving and moulding your speaker cabinets instead of assembling panels. Which of course is nonsense, but I’m a tactile aesthetic kind of person; the kind of intolerable amateur woodworker who is always running a hand along a sanded surface and smiling. It makes me happy.
To be clear, I’ve got no beef with MDF or plywood – I have built two sets of speakers using MDF and one with ply – I just loved working on all the speakers I built with solid wood. I know the risks of building with a totally organic material like solid wood and I understand the extra care required in the treatment of the material, but I also appreciate that with care you can achieve furniture grade results. And my wife appreciates it too. Which is one of the reasons I can get away with filling our house with big speakers.
The speakers which this story is about are 1.45m tall floor-standers made of 31mm panels of solid Pacific Maple which give a lovely gold/tan/red colour in the grain. The back panel and bottom panel were made of a sandwich of ply and MDF because I had to cut costs somewhere. Wood is expensive.
The basic details of the speakers are below for those who are interested:
• Tweeter: Scan-speak D2905/9900
• Mid = Eton 7-360/37
• Woofers = 2 x Scan-speak 25W/8565-01
• Net internal volume of 133 litres with rear firing port tuned to 22Hz
I won’t go into the crossover details here because there were seven revisions since the original crossover design… I like to tinker.
It had third order filters with some impedance equalisation, mid smoothing and tweeter attenuation.
I was younger back then and I make no apologies for loving bass that went boom. Yes, I know it was wrong: I measured a 6dB peak around 50Hz – 60Hz, but I left it and I loved it! I listened to a lot more dance music back then.
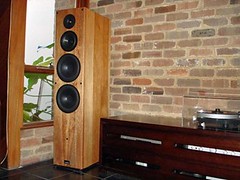
Anyway, I finished building the speakers in 2008 when I was living in the Crows Nest area of Sydney. Crows Nest is surrounded by water inlets, dripping forests, is reasonably close to the beach, is at sea level, and not least of all quite close to that big harbour of Sydney. All those points add up to humidity levels between 50% and 95% every day – hot or cold. Which is fine because the wood I used was purchased from a supplier in the local area. The speakers lived quite happily in Crows Nest for seven years without any sign of wear or damage. It seemed like they would be upsetting neighbours for decades to come.
This time last year, some big changes happened in our lives and we had to move to Canberra. Canberra is an inland town, surrounded by cleared farmland, is at altitude, and has no natural waterways. There is no humidity to speak of whether it’s hot, cold or even raining. Canberra, although being a lovely town, is practically a desert.
After about three months of living in Canberra I noticed some cracks appearing in a few of the joints of the speakers. A month later the cracks had broadened and a few more had appeared in other joints. Almost all the panels had cracked in some way except for the ply/MDF back panel.
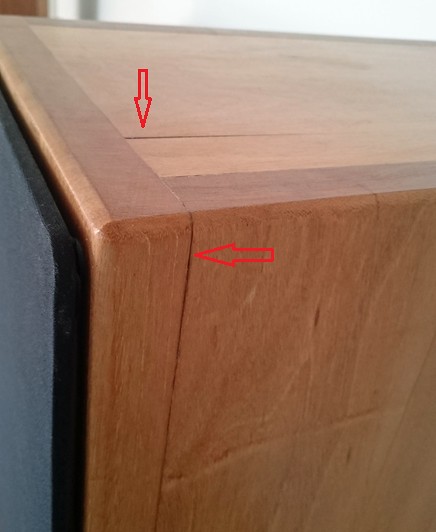
You can see in the picture the dark line where the front panel is pulling away from the sides. The top panel is also separating.
I found a local timber yard and furniture maker called Thor’s Hammer (great name!) which was recommended by friends who had bought furniture from them. I spoke to a bloke there named Gerry and told him about my situation. He said, “Yeah, that will happen. You should expect the moisture content to drop by about 12%, which means a lot of shrinkage.”
I asked if there was anything I could do to stop the moisture loss like sanding back and using oil to seal instead of varnish or something. The wood was expensive and I didn’t want to start again. Could I strengthen the joints?
“Nope. It’s going to shrink anyway. The joints are probably fine. The best you can do is leave it another couple of months to make sure the wood has reached the point where it’s as dry as it’s going to get, then sand back the varnish, fill the gaps with resin, sand back again, and use a flexible natural finish like oil.”
I had some time while I waited for the speaker cabinets to find their natural Canberra level of moisture and I figured if I was going to have to pull the speakers down, then I may as well tinker some more. I always thought the speakers sounded good (in all their versions), but the bass really was boomy with too much excursion. I’m older and …well … just older now and don’t appreciate the boom quite as much. I fired up Soundeasy and got designing. After a couple of months of designing and comparing options, I decided since the cabinets were already huge I could quite easily turn them into a transmission line.
I replaced the ply/MDF back panels with solid Pacific Maple like the rest of the cabinet. Sourced locally in Canberra. I took some more advice from Thor’s Hammer and left the lengths of wood inside to season for a month before joining lengths and cutting them into panels. This was also to find their moisture equilibrium.
Four months of repairing, woodworking, construction and a lot of sanding later, I have functioning speakers again. I used oil instead of varnish, which made the wood grain in the cabinets a little darker, but nicer looking. I finished a few months ago, but I let them settle in before I wrote this just to make sure there wasn’t going to be any more movement. So far, all good.
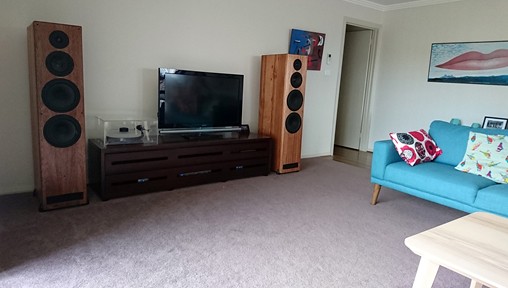
The only issue I have with the gaps now is my own mistakes I made with the resin. Otherwise it’s smooth to the touch (I ran my hand along many times), and they have a bit of a reclaimed timber look about it. From one metre away you can’t tell that there were ever any gaps.
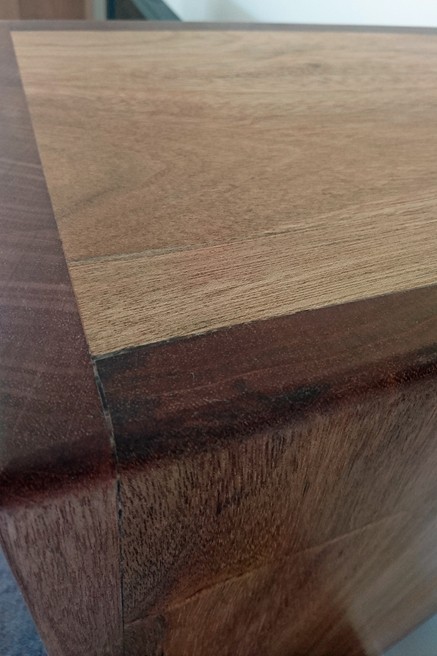
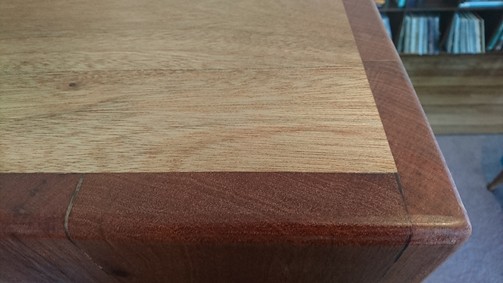
As for the sound, this was my first attempt at a transmission line and it lead to a lot of tinkering… I was in heaven! I had my measurement mic out every weekend for months! I had some phase issues which resulted in a slightly unorthodox fourth order filter for the woofers and third order for the mid and tweeter which did the trick. I did a lot of experimenting and ended up with lots of heavy stuffing in the transmission line which seemed to have only a little effect on the bass extension, but did tighten it up nicely. I now understand what people mean when they say their transmission line has tight and clean bass. It really is something different to the ported and sealed enclosures I’ve built. It goes deeper without lots of cone excursion and kickdrums have a nice clean “thump” without the boom. That’s all the subjective remarks I’ll make.
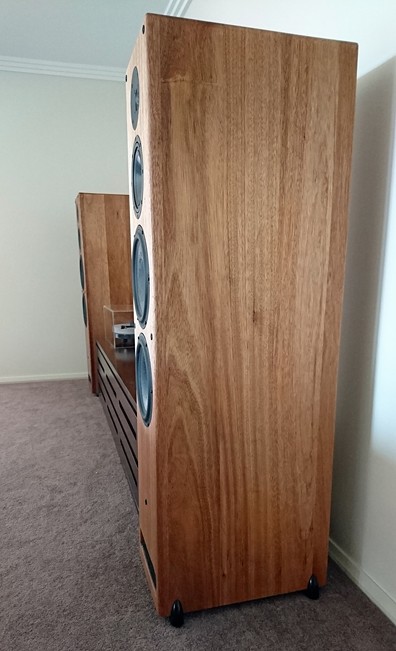
I am very happy with the results. So, this is a precautionary tale but like all good stories, the main character learns a thing or two along the way and it has a happy ending.
In conclusion, if you choose to build with solid wood:
• Solid wood behaves like a live material – it expands and contracts with moisture levels.
• If you build with solid wood be aware that moving to a different climate may cause your panels to split or buckle.
• Source your wood locally and season it. If possible leave it inside your house for a month or two before you build.
• Don’t be scared off. There are ways to repair the damage from split wood, but not ways to stop it.
I’m sorry this ended up so long. I started typing and it just went on.
I hope this has been helpful to anyone who considers using solid wood. I intend to continue using solid wood.
AJ
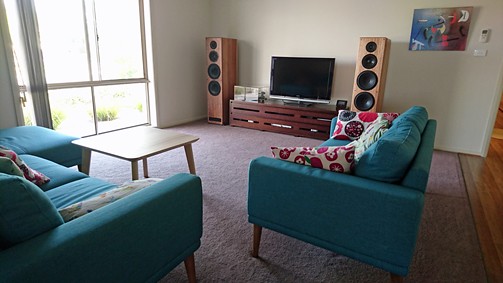
Last edited:
A lot of people think that veneered plywood is used because it's cheap. It's really just a better material to build cabinetry with -- the (sometimes but not always) lower cost of veneered plywood is just a side benefit.
Lovely story 🙂
Thanks for sharing. I'm sure there are many other woodworkers who instinctively want to use their favourite wood to build speakers. Even veneer can play up sometimes.
Thanks for sharing. I'm sure there are many other woodworkers who instinctively want to use their favourite wood to build speakers. Even veneer can play up sometimes.
Thanks for sharing your experience, solid wood is truly beautiful. I like the darker finish with oil, popping the wood grain brought some character.
Very informative! Question: what if you used thicker panels? Here in the US we can sometimes get panels almost 40 mm thick, though maybe not easily. Another question: did any of this actually cause leakage? Or just cosmetic? If leakage, maybe an important thing would be to put goopy anti-vibration coating (which I'm out of date with regards to good materials thereof)I just thought I’d drop a note (a long note) here about my recent experiences which I hope will help anyone who considers using solid wood as speaker cabinet building material...
Thanks guys, I appreciate it.
I've got to say it wasn't easy to write. I'm not particularly good at admitting that I made a mistake!
I've got to say it wasn't easy to write. I'm not particularly good at admitting that I made a mistake!
Very informative! Question: what if you used thicker panels? Here in the US we can sometimes get panels almost 40 mm thick, though maybe not easily. Another question: did any of this actually cause leakage? Or just cosmetic? If leakage, maybe an important thing would be to put goopy anti-vibration coating (which I'm out of date with regards to good materials thereof)
It was cosmetic. In the initial build I had coated the inside of the cabinet with silicone and that was still completely intact. I say it was cosmetic, but it really didn't look good. I wonder if I had left it untreated over time it may have continued to split and break through my silicon layer.
As for the thicker panels, I don't know but I would guess that 12% shrinkage is 12% shrinkage and the difference between 31mm and 40mm would simply be less predictable warping. But that's just a guess.
AJ
Sure is pretty wood, the speakers look great. What a heart break it must have been when the cracks opened.
The difficulty with solid wood is that the expansion is one direction only. In direction of the grain, expansion is close to zero, similar to plywood or MDF. Across the grain is where the expansion occurs. If the construction has all the solid wood in same orientation, no problem. You can make a box with 4 sides solid wood and front and back plywood or MDF and you would be ok. Internal bracing is difficult though - you cannot have different grain orientations so no stiffeners front to back.
This is a basic rule for solid wood construction. Wood thickness does not matter, probably crack faster because it has less give.
The difficulty with solid wood is that the expansion is one direction only. In direction of the grain, expansion is close to zero, similar to plywood or MDF. Across the grain is where the expansion occurs. If the construction has all the solid wood in same orientation, no problem. You can make a box with 4 sides solid wood and front and back plywood or MDF and you would be ok. Internal bracing is difficult though - you cannot have different grain orientations so no stiffeners front to back.
This is a basic rule for solid wood construction. Wood thickness does not matter, probably crack faster because it has less give.
Nice looking fix. I had the same misfortune with Ribbon Sapele enclosures.
Internal plywood braces and a rear port weren't enough to hold everything together through the first heating season in the Northeast US.
I suppose this is part of the appeal for Open Baffle designs.
Sent from my Nexus 6 using Tapatalk
Internal plywood braces and a rear port weren't enough to hold everything together through the first heating season in the Northeast US.
I suppose this is part of the appeal for Open Baffle designs.
Sent from my Nexus 6 using Tapatalk
I used ash for the front and top panels of tall floor standers.
They are now about 20years old.
No sign of any cracking or splits.
The 40mm thick ash was cut into 31.5mm wide by 40mm thick strips.
These were PVA glued together to form two panels 1500mm by 252mm
to give a front panel 1090mm tall by 250mm wide and top panel 395mm long.
Shaped and sanded and finished with three coats of Danish Oil.
They are now about 20years old.
No sign of any cracking or splits.
The 40mm thick ash was cut into 31.5mm wide by 40mm thick strips.
These were PVA glued together to form two panels 1500mm by 252mm
to give a front panel 1090mm tall by 250mm wide and top panel 395mm long.
Shaped and sanded and finished with three coats of Danish Oil.
The wood needs to be seasoned before use.
Leave it standing for a year before use.
Or you can buy ready seasoned wood.
Leave it standing for a year before use.
Or you can buy ready seasoned wood.
Excellent write-up by AJ Wykes. I have built a number of stringed instruments in my time, and dimensional stability is paramount in a glued-together body of thin wooden panels. My two cents formed by my experiences:
When building with solid wood, use quartersawn panels whenever possible. They are inherently more stable with changes in humidity. If quartersawn wood is not available, which it often is not, one can glue together numerous flat-sawn pieces arranged on their sides with the grain in a quartersawn fashion to get the required width of the necessary panel. This is very tedious and time consuming, but it is effective and has an appearance all its own;
Use wood species that do not change dimensions very much in response to changes in humidity. There are a number of reference books that give numerical values for the dimensional changes in various species, and one can always use the good old internet to compare these values also;
Build your speakers in an environment that is as dry, or drier, than any that the speakers will ever encounter. Wood expansion is much less harmful to the completed structure than wood shrinkage.
When building with solid wood, use quartersawn panels whenever possible. They are inherently more stable with changes in humidity. If quartersawn wood is not available, which it often is not, one can glue together numerous flat-sawn pieces arranged on their sides with the grain in a quartersawn fashion to get the required width of the necessary panel. This is very tedious and time consuming, but it is effective and has an appearance all its own;
Use wood species that do not change dimensions very much in response to changes in humidity. There are a number of reference books that give numerical values for the dimensional changes in various species, and one can always use the good old internet to compare these values also;
Build your speakers in an environment that is as dry, or drier, than any that the speakers will ever encounter. Wood expansion is much less harmful to the completed structure than wood shrinkage.
Speaking of stable wood, I have used butcherblock (countertop material) in my last couple of speaker builds and this seems like a great material. It is 100% wood, with 1x1 inch (or similar sized) strips glued together (in the material I purchased). There is a local supplier in my area that can make up tops in a wide variety of sizes (see: Perfect Plank Co) and they will ship them within the USA. I use Alder, because it routes a very clean line and the chips are dry, meaning the wood does not burn when you cut or route it compared to other woods I have worked with.
IKEA is another source of butcherblock. In the Kitchen Offerings > Kitchen products > Countertops look for "Hammarp". It's available in the USA in oak and birch. The material is 1-1/4 inches thick, 24 inches wide, and in lengths of 74 and 98 inches.
Butcherblock is very dimensionally stable because the grain of the blocks is alternated when the piece is assembled. I very much doubt that this material would ever crack. Because of the thickness it will be heavy, but on the other hand you only need one per panel.
IKEA is another source of butcherblock. In the Kitchen Offerings > Kitchen products > Countertops look for "Hammarp". It's available in the USA in oak and birch. The material is 1-1/4 inches thick, 24 inches wide, and in lengths of 74 and 98 inches.
Butcherblock is very dimensionally stable because the grain of the blocks is alternated when the piece is assembled. I very much doubt that this material would ever crack. Because of the thickness it will be heavy, but on the other hand you only need one per panel.
Great write-up. Nice photos. I'm glad you're sticking with solid wood.
My TL;DR contribution is: with hindsight, it might have been better to use old / recycled timber in shorter spans (two 75cm boxes rather than one 145cm box).
Interesting. I was lucky, when I dragged some (much less pretty) timber speakers through worse. They came from Brisbane to Canberra and then to Melbourne, and spent a couple of rainy Melbourne winters in a leaky garage before I gave them away. They didn't show the slightest trace of movement. Maybe the difference was:
-very seasoned timber (50 years? 100 years? Recycled 2x4 timber, I assume from the frames of demolished houses)
-presumably milled from old forest (not plantation) when there was still plenty of them (and abundance allowed them to be picky)
-shorter spans. A movement over 1.45m will be more likely to cause a split than the same % movement over 60cm
There are a few species to be avoided, but most widely available types seem to be around the centre of the bell curve. I guess they wouldn't be plantation-grown if they were awful 🙂
Note 1: most of the reference tables cover the % shrinkage between green and dried timber. That is, they are targeted at the mill / producer.
The amount of movement that seasoned timber will experience may be different.
Note 2: the relationship between air humidity and wood moisture % is not linear. Going from 90% to 60% humidity is a bigger problem than from 60% to 30% humidity.
Note 3: there's variation within species. Old growth timber is not exactly the same as plantation timber - another reason to use recycled stuff.
The OP commented in an earlier thread "My workshop is a garden shed designed to house a rake, a shelf, and if you're lucky a broom."
To get a low humidity environment in Sydney would require a dedicated workshop, with the air conditioning running 24/7 - a prohibitively space* & energy intensive requirement.
I like some of them. Local (eucalyptus-based) panels seem good.
Some are bad: one project I abandoned half-built, where I had a butcherblock of rubber wood (from Vietnam) glued to local, very seasoned hardwood. A few months later, the imported wood had shrunk. There wasn't just a crack - it had ruptured. I guess that relates to note 2 above. This seems like a good reason not to buy timber from tropical countries (another reason being that much of it is logged illegally).
*Non Australians may be surprised at how expensive our cities are: a house in Crows Nest costs about $2million. After tax, a basic annual salary (e.g. police constable, high school teacher) is roughly 2% of that.
My TL;DR contribution is: with hindsight, it might have been better to use old / recycled timber in shorter spans (two 75cm boxes rather than one 145cm box).
He said, “Yeah, that will happen. You should expect the moisture content to drop by about 12%, which means a lot of shrinkage.”
[...]
“Nope. It’s going to shrink anyway. The joints are probably fine. The best you can do is leave it another couple of months to make sure the wood has reached the point where it’s as dry as it’s going to get, then sand back the varnish, fill the gaps with resin, sand back again, and use a flexible natural finish like oil.”
Interesting. I was lucky, when I dragged some (much less pretty) timber speakers through worse. They came from Brisbane to Canberra and then to Melbourne, and spent a couple of rainy Melbourne winters in a leaky garage before I gave them away. They didn't show the slightest trace of movement. Maybe the difference was:
-very seasoned timber (50 years? 100 years? Recycled 2x4 timber, I assume from the frames of demolished houses)
-presumably milled from old forest (not plantation) when there was still plenty of them (and abundance allowed them to be picky)
-shorter spans. A movement over 1.45m will be more likely to cause a split than the same % movement over 60cm
Use wood species that do not change dimensions very much in response to changes in humidity. There are a number of reference books that give numerical values for the dimensional changes in various species, and one can always use the good old internet to compare these values also
There are a few species to be avoided, but most widely available types seem to be around the centre of the bell curve. I guess they wouldn't be plantation-grown if they were awful 🙂
Note 1: most of the reference tables cover the % shrinkage between green and dried timber. That is, they are targeted at the mill / producer.
The amount of movement that seasoned timber will experience may be different.
Note 2: the relationship between air humidity and wood moisture % is not linear. Going from 90% to 60% humidity is a bigger problem than from 60% to 30% humidity.
Note 3: there's variation within species. Old growth timber is not exactly the same as plantation timber - another reason to use recycled stuff.
Build your speakers in an environment that is as dry, or drier, than any that the speakers will ever encounter. Wood expansion is much less harmful to the completed structure than wood shrinkage.
The OP commented in an earlier thread "My workshop is a garden shed designed to house a rake, a shelf, and if you're lucky a broom."
To get a low humidity environment in Sydney would require a dedicated workshop, with the air conditioning running 24/7 - a prohibitively space* & energy intensive requirement.
butcherblock (countertop material) [...] seems like a great material [...] Butcherblock is very dimensionally stable because the grain of the blocks is alternated when the piece is assembled. I very much doubt that this material would ever crack. Because of the thickness it will be heavy, but on the other hand you only need one per panel.
I like some of them. Local (eucalyptus-based) panels seem good.
Some are bad: one project I abandoned half-built, where I had a butcherblock of rubber wood (from Vietnam) glued to local, very seasoned hardwood. A few months later, the imported wood had shrunk. There wasn't just a crack - it had ruptured. I guess that relates to note 2 above. This seems like a good reason not to buy timber from tropical countries (another reason being that much of it is logged illegally).
*Non Australians may be surprised at how expensive our cities are: a house in Crows Nest costs about $2million. After tax, a basic annual salary (e.g. police constable, high school teacher) is roughly 2% of that.
If you have solid wood speakers and moving from a humid climate to dry climate, the next DIY project should be built-in humidifiers for the speaker enclosures... ;-)
Cheers, hollowboy.
How good it looks
Density
Responsibly sourced
The last point being the most difficult. Back in 2007 when I was sourcing the wood, there was very little information about where the timber was sourced. The FSC label was practically unheard of. That was only ten years ago.
Interesting to note, my friend moved to Perth for two years and took the speakers with him. Perth is much dryer than Sydney but he had no trouble with splitting panels or joints. His speakers were made of 19mm Tasmanian Oak panels. Maybe Tassie Oak is not affected as much as Pacific Maple, or maybe it was the thinner panels... I need to research this some more.
AJ
Unfortunately, I wasn't thinking of that at the time. I had no intention of leaving Sydney (or even the suburb) so moisture content wasn't a factor in my decision. But things change, so it was pretty dumb of me to ignore it really. My primary considerations were:There are a few species to be avoided, but most widely available types seem to be around the centre of the bell curve. I guess they wouldn't be plantation-grown if they were awful
How good it looks
Density
Responsibly sourced
The last point being the most difficult. Back in 2007 when I was sourcing the wood, there was very little information about where the timber was sourced. The FSC label was practically unheard of. That was only ten years ago.
Yep. The picture below is me working on a two-way floor-stander for a friend of mine back in 2010. My backyard was practically a rain forest!The OP commented in an earlier thread "My workshop is a garden shed designed to house a rake, a shelf, and if you're lucky a broom.
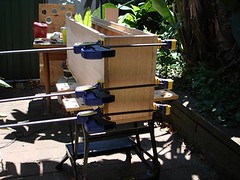
Interesting to note, my friend moved to Perth for two years and took the speakers with him. Perth is much dryer than Sydney but he had no trouble with splitting panels or joints. His speakers were made of 19mm Tasmanian Oak panels. Maybe Tassie Oak is not affected as much as Pacific Maple, or maybe it was the thinner panels... I need to research this some more.
We were renting that house - which was a two bedroom, one bathroom corridor - and when we left the owner sold it for $1.4 million. Insane!a house in Crows Nest costs about $2million
AJ
Last edited:
At the risk of sounding like me: recycled? If you can put up with short bursts of extreme noise + mess, you can use a router jig (made from scraps) to trim almost any grubby-looking salvaged timber down into clean and level beams.Responsibly sourced
Back in 2007 when I was sourcing the wood, there was very little information about where the timber was sourced. The FSC label was practically unheard of. That was only ten years ago.
I cannot currently do anything like this due to odd work spaces - I live in an apartment & have a bush block. Anything DIY is either done on a table in my living room, or under a tree, far from all power outlets 🙂
I think "Tasmanian Oak" and "Victorian Ash" get used pretty loosely - to mean any pale native timber.Perth is much dryer than Sydney but he had no trouble with splitting panels or joints. His speakers were made of 19mm Tasmanian Oak panels. Maybe Tassie Oak is not affected as much as Pacific Maple, or maybe it was the thinner panels... I need to research this some more.
http://www.5startimbers.com.au/downloads/Moisture-in-Timber.pdf
In the linked .pdf, note that these two timber types have "very high" shrinkage ratings (when drying the green timber), but that's only a problem for the producer. For the hardwoods, the initial shrinkage values and the post-drying variance (here called "unit tangential movement”) are unrelated. The latter, the UTM, is the number we users cares about - and they are all roughly the same.
I have some timber and half-finished projects sitting in a shack on my country block. It is pretty exposed to the weather - the "marine" ply is now heavily spotted with mould - but the large panel I made from gluing up some cheap, pale 19mm native hardwood (AKA "Tassie Oak") still looks perfect.
Hi guys,
Thanks to everyone for the comments, advice, and for sharing your experiences. This really is a great community.
I intended to post my story so I could share my experience and hopefully help anyone avoid unnecessary work. It was months of seasoning, re-designing and repairing… Who am I kidding! I loved the extra work! And I ended up with better speakers!
But sticking to the original intentions of my post, I thought I’d wrap it up by gathering together some of the knowledge and advice offered and re-writing it into a single post.
So again, in conclusion, if you choose to build with solid wood:
• Solid wood behaves like a live material – it expands and contracts with moisture levels. Research the post-drying variance of the timber, also called "unit tangential movement”. (Thanks hollowboy)
• If you build with solid wood be aware that moving to a different climate may cause your panels to split or buckle.
• Source your wood locally and season it. If possible leave it inside your house for a month or two before you build. If possible Leave it standing for a year before use. Or you can buy ready seasoned wood. (Thanks nigelwright7557)
• Don’t be scared off. There are ways to repair the damage from split wood, but not ways to stop it.
• Consider constructing your panels out of multiple lengths of thick but narrow timber. The example used in the thread was 40mm thick ash cut into 31.5mm wide by 40mm thick strips to make a 250mm panel. (Thanks AndrewT)
• Use quartersawn panels whenever possible. They are inherently more stable with changes in humidity. And again use wood species that do not change dimensions very much in response to changes in humidity. (Thanks majerjack)
• Butcherblock (countertop material) has been found to be a great material. It is 100% wood, with 1x1 inch (or similar sized) strips glued together. IKEA is a source of butcherblock. (Thanks CharlieLaub)
Cheers,
AJ
Thanks to everyone for the comments, advice, and for sharing your experiences. This really is a great community.
I intended to post my story so I could share my experience and hopefully help anyone avoid unnecessary work. It was months of seasoning, re-designing and repairing… Who am I kidding! I loved the extra work! And I ended up with better speakers!
But sticking to the original intentions of my post, I thought I’d wrap it up by gathering together some of the knowledge and advice offered and re-writing it into a single post.
So again, in conclusion, if you choose to build with solid wood:
• Solid wood behaves like a live material – it expands and contracts with moisture levels. Research the post-drying variance of the timber, also called "unit tangential movement”. (Thanks hollowboy)
• If you build with solid wood be aware that moving to a different climate may cause your panels to split or buckle.
• Source your wood locally and season it. If possible leave it inside your house for a month or two before you build. If possible Leave it standing for a year before use. Or you can buy ready seasoned wood. (Thanks nigelwright7557)
• Don’t be scared off. There are ways to repair the damage from split wood, but not ways to stop it.
• Consider constructing your panels out of multiple lengths of thick but narrow timber. The example used in the thread was 40mm thick ash cut into 31.5mm wide by 40mm thick strips to make a 250mm panel. (Thanks AndrewT)
• Use quartersawn panels whenever possible. They are inherently more stable with changes in humidity. And again use wood species that do not change dimensions very much in response to changes in humidity. (Thanks majerjack)
• Butcherblock (countertop material) has been found to be a great material. It is 100% wood, with 1x1 inch (or similar sized) strips glued together. IKEA is a source of butcherblock. (Thanks CharlieLaub)
Cheers,
AJ
I have made around 12 pairs of speakers from solid wood, Jarrah, Tassie Oak, Myrtle. None have shown any problems, and the oldest would be over 10 years old now. The Tassie Oak and Myrtle were quarter sawn, but the Jarrah is not. All have gone through humidity changes from around 90% down to less than 30%. Why no problems? They have been specifically designed to allow for movement of the wood across the grain. So, no cross grain gluing if it can be avoided, tall thin cabinets (MLTL), front and back are screwed on with a rubber strip to stop air leaks. If you design the cabinet to allow movement then the wood won't split. This is standard stuff for music instrument construction and furniture. No amount of seasoning or finishing will stop wood from moving. It certainly is a good idea to get it to EMC before starting work, but you must assume it will move a lot across the grain and allow for that. Many larger designs are not very practical in solid wood because of the cross grain dimensions or because of the cost, but solid wood is much stronger, stiffer and heavier than MDF, and in A/B comparisons with indentical MDF cabinets, my solid wood cabinets do sound better. Don't listen to the nay sayers. Solid wood cabinets can be very successful if you design them properly.
Last edited:
We've built "a few" solid hardwood cabinets and this is always a concern. A plywood, mdf or other "non-living" baffle, veneered with a thin solid and recessed into the front will prevent this cracking from happening. Using solid wood on 6 sides will always be a dice roll. You can slow down the shrinking/expanding problem, but you cant stop it completely (save for a humidity controlled room). Although, there are hardwoods that have been dried a specific way that stops the expansion/contraction but I'm afraid to see the prices!
- Home
- Loudspeakers
- Multi-Way
- A precautionary tale of building with solid wood.