When I enter data of SM58 transformer, Material: Sil Steel mid Bsat, Xsection 36mm2, Freq:20Hz, primV:0.1 outputV:3, it gives me primary 25 and secondary 750. Does it make sense? And a have 0.1 and 0.2 mm enameled wires for winding secondary.I'm guessing its an excellent calculator
I tought I might use double wire from cheap 1:1 small red and yellow transformers sold dirt cheap on Aliexpressfor secondary, but those wires are really thin. BTW, I want to make ribbon mic with some gain like Cloudlifter circuit, two fets and few resistors.
Last edited:
Just make your own bobbin. For small cores thick cardstock works just fine. For big cores, 2.5mm plywood or even 3D printing works just great.Very little experience of winding toroids, the ones I have wound have been inductors on Sendust and powdered iron cores. Winding toroids by hand is extremely labour-intensive.
Having a core is one thing, you'll also need a suitable bobbin and they're often hard to find. If you get the right sized C shaped cores you can use two side by side in an EE type bobbin intended for ferrite cores.
Hand-winding toroids is fine right up to about 150 turns, at which point you'll start to go insane.
Very true. But taking 2 or 4 strands of wire may make it easier.. When I try to make one ribbon transformer on nanocrystal toroid, I will let you know how I did it. It will be with dual wire, maybe even 4.Hand-winding toroids is fine right up to about 150 turns, at which point you'll start to go insane.
When I enter data of SM58 transformer, Material: Sil Steel mid Bsat, Xsection 36mm2, Freq:20Hz, primV:0.1 outputV:3, it gives me primary 25 and secondary 750. Does it make sense?
Seems quite reasonable to me, it means the turns/volt for 20Hz is 250. Quite a bit better than for ferrite which would be in the region 700 or so and that'll be down to the higher Bmax for steel.
0.2mm sounds a bit thick for such small signal levels. Is your bobbin going to have enough space? In my classD input trafo which was wound onto EE25 I needed about 2000 turns to cope with 3V peak, I used 0.07mm I think.And a have 0.1 and 0.2 mm enameled wires for winding secondary.
I thought so, I guess I will order some 100m or 100g of some thin wire, perhaps 0.1mm.0.2mm sounds a bit thick for such small signal
About primary, is copper foil an overkill? I have some 0.6mm and I think its thick enough.
Yes. I am just not shure about what diameter wires are those I plan to wind it with...Look how thin they are.Do you have dimensions?
I wound it on that cardboard piece as I wished to try winding nanocrystaline torroid, but I dont know how to calculate number of turns on nanocry. material. I wish that I have data of torus to enter it in calculator that I mentioned..
I had a piece of 0.04 wire and compared them. I think its 0.04-0.05.
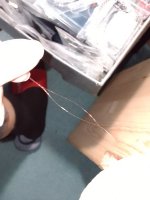
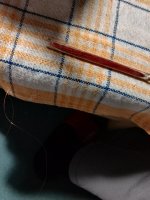
Last edited:
Sadly its closed for further discussion...If you're curious about making your own signal transformers I opened a thread to give some assistance here : https://www.diyaudio.com/community/...-input-transformer-step-by-step-guide.292658/
I wander how to enter nanocrystaline torus data into http://dicks-website.eu/coilcalculator/.. I have some of data about material, but when I calculate,
he gives me 1 turn for primary and 350 for secondary. For my purpose of DIY ribbon mic transformer, I know its usual for primary to have less than 15-20 turns,but 1... I dont think its ok.
I have EI40 power ferrite (PC40 material) transformer and some bigger ETDs, what do you think, can I make something of it? At least 1:30 transformer for ribbon mike? Or should I try to find core of another material with bigger Bsat?
Last edited:
I'm not surprised it gives 1 turn for the primary.
The voltage output from a ribbon microphone is absolutely miniscule. Metglas is almost a unicorn material - it has low losses at high switching frequencies, extremely high permeability, and extremely high Bsat. The trick may be trying to get that 1 turn primary to have low leakage inductance (although Metglas does make that easier). I'd be tempted to wind it out of copper foil, using kapton tape for insulation.
I also suspect that you could wind something pretty usable using ferrite. Again, the power levels we're talking about are microscopic here, even at 20 Hz it should be realistic to avoid saturation.
I'd give it a shot. It's not going to cost you much, and I can almost guarantee that you're going to learn a lot in the process.
The voltage output from a ribbon microphone is absolutely miniscule. Metglas is almost a unicorn material - it has low losses at high switching frequencies, extremely high permeability, and extremely high Bsat. The trick may be trying to get that 1 turn primary to have low leakage inductance (although Metglas does make that easier). I'd be tempted to wind it out of copper foil, using kapton tape for insulation.
I also suspect that you could wind something pretty usable using ferrite. Again, the power levels we're talking about are microscopic here, even at 20 Hz it should be realistic to avoid saturation.
I'd give it a shot. It's not going to cost you much, and I can almost guarantee that you're going to learn a lot in the process.
Yeah, I will definite do something, proppably with ferrite first as it is easier to wind.I'd give it a shot. It's not going to cost you much, and I can almost guarantee that you're going to learn a lot in the process.
Seems its too old! I thought they had a button for asking a mod to re-open a discussion but maybe not for such pre-historic threads as that one.Sadly its closed for further discussion...
That's a 1:350 step-up, leakage inductance and parasitic capacitance will likely kill its HF response.I wander how to enter nanocrystaline torus data into http://dicks-website.eu/coilcalculator/.. I have some of data about material, but when I calculate,
he gives me 1 turn for primary and 350 for secondary. For my purpose of DIY ribbon mic transformer, I know its usual for primary to have less than 15-20 turns,but 1... I dont think its ok.
I have EI40 power ferrite (PC40 material) transformer and some bigger ETDs, what do you think, can I make something of it? At least 1:30 transformer for ribbon mike? Or should I try to find core of another material with bigger Bsat?
You could indeed make something out of those cores but for this application I'd start with something smaller, PQ2016 sounds about right for a mic trafo. Its not so small that the wires are going to be ultra-fine.
Let's run the process of designing a 1:30 PQ2016 trafo :
T/V at 20Hz for this core is 395 so for 100mV peak you'll need 40 turns. Then 30X step up makes for 1200 turns on the secondary.
Winding window is 25mm^2. I work on the basis that the inner winding will occupy 40% of the window - this works for single pri/sec designs but you'll probably need interleaved windings to keep leakage under control. But it won't hurt to create the simplest winding structure first to get a measure of how bad the leakage is going to be. So initially start with the 40/60 split and lay the primary down first.
0.4*25mm^2 gives 10mm^2 with 40 turns that gives a wire diameter of 0.5mm - outside diameter. It'll be about 0.45mm inner diameter - which is how the wire's ordered.
The 1200 turns go into 15mm^2 window which gives outer diameter of 0.11mm, so 0.09mm wire will be needed which is quite thin for a novice at winding so let's bump up the core to PQ2020 and see what that gives.
On PQ2020 the winding window jumps up to 39mm^2 so your secondary has 23.4mm^2 which for 1200T gives 0.14mm outer diameter and 0.11mm wire for a conservative estimate. Still fairly thin.
As having the best optimized design for power transfer doesn't matter so much on signal trafos, we could see how it looks with a 30/70 window split on PQ2020.
0.3*39 = 11.7mm^2 so primary is 0.5mm inner diameter wire and secondary is 0.12mm. I think this should be manageable so I'd go with PQ2020 for a first pass.
Thank you very much for in depth explanation of winding on ferrite core.Let's run the process of designing a 1:30 PQ2016 trafo :
T/V at 20Hz for this core is 395 so for 100mV peak you'll need 40 turns. Then 30X step up makes for 1200 turns on the secondary.
Winding window is 25mm^2. I work on the basis that the inner winding will occupy 40% of the window - this works for single pri/sec designs but you'll probably need interleaved windings to keep leakage under control. But it won't hurt to create the simplest winding structure first to get a measure of how bad the leakage is going to be. So initially start with the 40/60 split and lay the primary down first.
0.4*25mm^2 gives 10mm^2 with 40 turns that gives a wire diameter of 0.5mm - outside diameter. It'll be about 0.45mm inner diameter - which is how the wire's ordered.
The 1200 turns go into 15mm^2 window which gives outer diameter of 0.11mm, so 0.09mm wire will be needed which is quite thin for a novice at winding so let's bump up the core to PQ2020 and see what that gives.
On PQ2020 the winding window jumps up to 39mm^2 so your secondary has 23.4mm^2 which for 1200T gives 0.14mm outer diameter and 0.11mm wire for a conservative estimate. Still fairly thin.
As having the best optimized design for power transfer doesn't matter so much on signal trafos, we could see how it looks with a 30/70 window split on PQ2020.
0.3*39 = 11.7mm^2 so primary is 0.5mm inner diameter wire and secondary is 0.12mm. I think this should be manageable so I'd go with PQ2020 for a first pass.
Its just, I would like to use core that I already have, and those are EI40, ETD/ER 35, and big EER42/42/20.
I was thinking about ETD/ER 35, what do you think about it? All are power ferrite material PC40/3C90. If I will be buying any more cores than Ill try to find core of better material for audio. And I do have an expirience with 0.1mm wire and I have manual winding mashine, the one thats available on AliX and ebay, pretty basic but does the work. I usually wind 0.25, 0.3 for tube OPT but 0.1 is not a problem either, just takes more time and being careful.
With your 35mm core you'll definitely not need anything as thin as 0.1mm.
In the Ferroxcube core catalog, ER35 has a core cross-sectional area of ~100mm^2 (there are two versions with slightly different numbers).
With that number I get T/V @ 20Hz to be 231. So 23 turns primary and 690 turns secondary. No bobbins are shown for the ER cores so we'd have to make some estimates of what might be possible.
Height of bobbin would be about 30mm, inner diameter 11mm and outer 26mm. If we take bobbin wall thickness as 1mm then we have 28mm for height, 13mm inner and 26mm for outer. To get the winding window subtract inner from outer (26-13 = 13) and divide by two (6.5). Multiply by height (6.5*28 = 182mm^2). Compared to the PQ2020 the winding window is huge now so maybe using all of it will result in impractically thick wire. Let's see...
23 turns in 40% of the window (72.8) is 1.8mm wire, definitely you'll find it no fun to wind with that and that's before you try to wrap it around the pins. The secondary is 690T in 103mm^2 giving 0.4mm outer dia wire. Definitely manageable. I can only suggest go for as thick wire as you can comfortably wind for the primary.
In the Ferroxcube core catalog, ER35 has a core cross-sectional area of ~100mm^2 (there are two versions with slightly different numbers).
With that number I get T/V @ 20Hz to be 231. So 23 turns primary and 690 turns secondary. No bobbins are shown for the ER cores so we'd have to make some estimates of what might be possible.
Height of bobbin would be about 30mm, inner diameter 11mm and outer 26mm. If we take bobbin wall thickness as 1mm then we have 28mm for height, 13mm inner and 26mm for outer. To get the winding window subtract inner from outer (26-13 = 13) and divide by two (6.5). Multiply by height (6.5*28 = 182mm^2). Compared to the PQ2020 the winding window is huge now so maybe using all of it will result in impractically thick wire. Let's see...
23 turns in 40% of the window (72.8) is 1.8mm wire, definitely you'll find it no fun to wind with that and that's before you try to wrap it around the pins. The secondary is 690T in 103mm^2 giving 0.4mm outer dia wire. Definitely manageable. I can only suggest go for as thick wire as you can comfortably wind for the primary.
Great, I got 30/900 so I guess I will go with your numbers.🙂With that number I get T/V @ 20Hz to be 231. So 23 turns primary and 690 turns secondary.
BTW bobbin is about 4.5mm deep and 26mm long/high and it is 100mm2, so there is enough space for more than 1000 turns of 0.2mm wire that I can buy cheaply here in Serbia. I thought to wind parts of primary on each 1/3 or 1/2 of secondary, somewhat similar like interleaving OPT. Sorry for my Eng, its not my first language.
I tought for primary some 0.6 or 0.8, and I have copper tape so I can try to wind a foil.. I will think a little more until wire comes.23 turns in 40% of the window (72.8) is 1.8mm wire, definitely you'll find it no fun to wind with that and that's before you try to wrap it around the pins. The secondary is 690T in 103mm^2 giving 0.4mm outer dia wire. Definitely manageable. I can only suggest go for as thick wire as you can comfortably wind for the primary.
Once again, your help is priceless, I knew some stuff that you confirmed and some I learned, definitely gave me tottaly new aspect of using ferrite for small signal audio. 🙂 And I will try to find source of better ferrite or nanocrystaline cores.
Last edited:
Oh I hadn't thought of that. You mean create the primary out of several paralleled windings of 23 turns (of much thinner wire) and interleave them with the secondary? That might be a way to reduce leakage. Do let us know whether it works! Sounds like a promising idea. I've never tried using tape so can't be of any help there.I thought to wind parts of primary on each 1/3 or 1/2 of secondary, somewhat similar like interleaving OPT.
(I'd not worry about your English, its waaay better than my Serbian.)
I thought of puting them in series but paralleling it is much better because its just 23 turns. It will drop the ressistance too. And I dont need a super thick wire, I think 0.6 would be enough. Thanks for idea, I am used to OPT where interleaving goes in series.You mean create the primary out of several paralleled windings of 23 turns (of much thinner wire) and interleave them with the secondary
I am still searching for other ferrites in pot cores, but if I find nothing, I will go with ER35. Wire will come in a 7-10 days and I will wind it
and I will post what I got. Cheers!

Yes paralleling windings which are interleaved solves two problems - wire which is too thick for practical winding and (potentially) leakage. I also have never tried interleaving paralleled windings, only series ones. I thought the idea came from you 😍 Do please report how you get on with the winding job.
Basically It did, but I thught to connect 2 or 3 parts of primary in series and you wrote to do the same but connect in parallel, whitch is for this paticular Xformer much better solution 😉.I thought the idea came from you 😍 Do please report how you get on with the winding job.
I will report as soon as I wind it and put it on the test.
I've done a bit of work on DIY trannys, needless to say i didn't get very far but it's one of my first posts on this profile if you wanna look at it, i found that the hardest part was finding cores with adequate permeability in audio frequencies, ime ferrite doesn't really lend itself well. MuMetal and similar nickel alloys are obviously ideal but buying laminations in hobbyist quantities turned out to be very impractical. Amorphous toroidal cores turn out to be an excellent candidate albeit also very elusive in terms of aquisition (also PITA to wind by hand lol). Please do update with your findings
- Home
- Design & Build
- Parts
- Low cost transformer for ribbon mic?