The only issue I see with blue painters tape is that you'll need pressure to ensure it grips well. Then, when removing it from the unfinished, and unsealed veneer, you have a chance of lifting/tearing some of the wood fibres (somewhat wood dependant, of course - hard maple probably not, African Mahogany it's guaranteed). Veneer tape, not matter how long it's left on, won't stain. I can't say that about 'masking' tapes in my experience. Veneer tape is, well 'veneer' tape for a reason. And really it comes off quickly when sanding with 150 & 180 grit. (As an aside you probably don't want to go beyond 220 anyway - finer grits at this point tend to polish the wood and inhibit finishing absorption)Interesting. I like that idea. And may try with blue painters tape.
Depends on surface size and shape, as in is it curved or flat, are you doing a panel or a cabinet, and what's the substrate?This is the way to go. The only question is which glue?
I have only used paper-backed veneer with water-based contact adhesive for dozens of projects. Very easy to work with and provides professional results.
Not sure what glue to use for un-backed veneer.
The bondo will be stained black. And if it comes out looking iffy, I will cover it with stainless steel tape strips.so the look will be wood veneer, bondo, wood veneer, bondo, etc. ?
I've never done it but I've heard it mentioned before: you can make your own iron-on veneer quite easily with regular Titebond and apparently it works pretty well:
Only with paper backed veneer, otherwise splits & lifting over time. Don't ask why I know this 🤬
This is the type of look I am going for.
Hence the filling in of gaps between individual strips of veneer.
Hence the filling in of gaps between individual strips of veneer.
One way would be to lay up the veneer on the sheet of ply or mdf while it was flat, use a router to cut the grooves slightly deeper than the veneer thickness and glue in thin wood strips of a contrasting color. Sand everything smooth while the sheet is still flat then bend and glue the sheet to the curved form.This is the type of look I am going for.....Hence the filling in of gaps between individual strips of veneer.
There are many ways to do it, that is just one idea.
Last edited:
For a curved assembly like that, we would usually make a forms using interlocking mdf panels into upper and lower egg-crate arrangements. Make the panels oversized and trim afterwards with a router using a test part for a jig.
Two part epoxy or even moisture cure urethane will work but have to watch out to make sure that it doesn’t get onto any part of the untrimmed areas.
Two part epoxy or even moisture cure urethane will work but have to watch out to make sure that it doesn’t get onto any part of the untrimmed areas.
Here the carpenters use rubber based contact cement, clean surfaces and proper spreading / applying technique are important for good results.
Removing excess cement before applying neighboring piece can be a pain.
Also, the epoxy and moisture cure urethane may take longer to set, which has its advantage in allowing positioning, but can flow out of place...which is a disadvantage, so keep the job flat, not vertical.
I would practice on a scrap piece first.
Removing excess cement before applying neighboring piece can be a pain.
Also, the epoxy and moisture cure urethane may take longer to set, which has its advantage in allowing positioning, but can flow out of place...which is a disadvantage, so keep the job flat, not vertical.
I would practice on a scrap piece first.
Seams are taped with specialized tape. Dont use contact cement.
Resin based glue is the standard.
As mentioned brand names such as Bond X or Rely X
Not sure how Sonus does it. By the look it is similar to Wood Boat finishes.
For a curved object or flat surface , clamping pressure for curing.
Likely a custom press or Vacuum bag for curved surface.
If they are using epoxy highly likely to be vacuum bag.
Having never done wood boat style finish. I have seen the process
in numerous online sources and they usually list typical brand name
products. As usual in the boat/marine industry, overpriced pretty names and
labels using = 3M products. So older experienced builders often reference the 3M
products directly
Resin based glue is the standard.
As mentioned brand names such as Bond X or Rely X
Not sure how Sonus does it. By the look it is similar to Wood Boat finishes.
For a curved object or flat surface , clamping pressure for curing.
Likely a custom press or Vacuum bag for curved surface.
If they are using epoxy highly likely to be vacuum bag.
Having never done wood boat style finish. I have seen the process
in numerous online sources and they usually list typical brand name
products. As usual in the boat/marine industry, overpriced pretty names and
labels using = 3M products. So older experienced builders often reference the 3M
products directly
Unfortunately, I had to drop the unbacked veneer approach. It was too fragile for the bend, and split easily.
I decided to go with a product I had previous experience with: backed walnut veneer with 3M pressure sensitive adhesive. Far easier to apply.
I decided to go with a product I had previous experience with: backed walnut veneer with 3M pressure sensitive adhesive. Far easier to apply.
Paper-backed veneer is really easy to work with. Most of the veneer work I've done is on flat surfaces but when I need to bend the veneer, the paper-backed is a life saver.
I use the type of paper-backed veneer that requires contact cement, water-based is the way to go.
Here's a console cabinet I restored a few years ago. I needed to bend the veneer around a sharp corner that was parallel to the grain along the entire width at the bottom, un-backed veneer would have split along the grain for sure....
It would have been impossible to get a tight joint at the obtuse corner had I used two pieces of veneer so using one piece and bending it was the only way...
Finished product....
Seamless joint along the bottom rail....
I use the type of paper-backed veneer that requires contact cement, water-based is the way to go.
Here's a console cabinet I restored a few years ago. I needed to bend the veneer around a sharp corner that was parallel to the grain along the entire width at the bottom, un-backed veneer would have split along the grain for sure....
It would have been impossible to get a tight joint at the obtuse corner had I used two pieces of veneer so using one piece and bending it was the only way...
Finished product....
Seamless joint along the bottom rail....
This is the adhesive I've been using for the past 30 years, it works for plastic laminate (Formica) and plain paper-backed veneer....
https://www.wilsonart.com/wilsonart-h2o-waterbased-contact-adhesive-wa-h2o
https://www.wilsonart.com/wilsonart-h2o-waterbased-contact-adhesive-wa-h2o
No No No. No painters tape. Too many reasons why.Interesting. I like that idea. And may try with blue painters tape.
There's a reason why this 100's of years old method is still the best today especially with the modern update of Better Bond X-press adhesive. And it's not difficult. You need the paper tape pfarrell mentioned plus veneer pins commonly known as push pins and a new blade every few cuts razor knife. The blade will want to follow the grain of the wood so make several very light cuts with the blade at 90 degrees, never slanted, to the metal straight edge you will clamp at each end of the veneer strip. Do this on a known flat piece of plywood or MDF large enough to accommodate the entire finished size of the veneer. Use one edge of the plywood to register the short side of each strip so as you lay them out and tape them together the long edges meet properly after cutting. It's entirely possible that the strips you have acquired were machine cut so see of they mate before you do any cutting. If not, and if you're having difficulty getting them tight together. overlap them slightly so you're cutting througn two at once which will guarantee they mate.
Square up and pin the first strip to the board, then cut and pin the next and so on. Then, dragging the tape through a shallow dish to wet it or using a wet sponge, apply the tape. I always use the sponge to wet and press the tape in place at the same time. Not too wet now. You'll quickly get the hang of it. Once done and dry you'll have afull size leaf ready to glue up.
Use a hard rubber roller or a Bondo type spreader to spread the Better Bond on both the leaf and the substrate. Less is more. If you put on too much the veneer will want to skate around at the slightest touch. You should be able to see the grain of the wood through the glue. Done right there will be enough tackiness to hold the leaf in place after a few seconds.
Of course, you'll have had the clamps, cauls, and a platen ready to go before you spread the glue. The platen is a double thick layer of MDF for it's weight, screwed together slightly over-sized to the workpiece. The cauls are any scrap lumber cut to the size of the platen that you have planed or sanded so they are slightly, very slightly convex with the middle inches flat. this will ensure that when you tighten the clamps the middle of the cauls will be forced down with equal pressure to the ends. Ideally, you will have enough clamps to place no more than 6" apart.
Next day carefully flip the veneered side down onto a flat surface and trim back the veneer with the knife, once again taking multiple light cuts. Very slight overlap can just be planed back with a block plane and then sandpaper.
Then Viola!
Pay no attention to the bald spot on the face veneer. It was the Cat.
Sorry, I missed your post about wanting that Sonus Faber look. If I were you and didn't desire to get into having Luthier's supplies and techniques, here's what I would do:
Layup and glue down the strips as in my post above. Then lightly spray the veneer with a Bulls Eye rattle can of clear shellac. You can apply any finish you desire over it, it's de-waxed. Now spend the outrageous $22 on a Mohawk (it must be Mohawk) Ultra Mark pen to draw the lines you want to simulate. Don't skip the shellac, the color from the pen will spread if you do.
After you've done all this there will be no stopping you. Post pix of your triumph!
Layup and glue down the strips as in my post above. Then lightly spray the veneer with a Bulls Eye rattle can of clear shellac. You can apply any finish you desire over it, it's de-waxed. Now spend the outrageous $22 on a Mohawk (it must be Mohawk) Ultra Mark pen to draw the lines you want to simulate. Don't skip the shellac, the color from the pen will spread if you do.
After you've done all this there will be no stopping you. Post pix of your triumph!
Lubricate both adhesive surfaces with PVA. Let them dry almost completely. Next, put the veneer in place. Use an iron with a setting to full power (cotton). The veneer can then be ironed neatly in place as PVA is thermoplastic. If you think this is scary, just test this on a test piece first, and you're good to go.
It's much easier to perfect technique than it is to perfect a design.
For inspiration, I always start with what I consider the high point of design in the 20th century which is from "Bauhaus" to "mid-century" and then some of the quirkier designs of the 1970's. There is very little that I find visually appealing starting in the 1980's and beyond.
For inspiration, I always start with what I consider the high point of design in the 20th century which is from "Bauhaus" to "mid-century" and then some of the quirkier designs of the 1970's. There is very little that I find visually appealing starting in the 1980's and beyond.
Last edited:
That is a great idea!Now spend the outrageous $22 on a Mohawk (it must be Mohawk) Ultra Mark pen to draw the lines you want to simulate
Here is where I am at right now. Walnut PVA veneer on the top and sides. 1/4" walnut board for the bottom front. With one coat of water-based poly on it (to keep the raw walnut wood look).
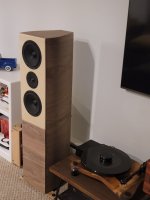
I am strongly considering that Mohawk pen, and then another coat of poly.
Tbd on the color for the front baffle where the drivers are mounted.
Glad I could help. Do a test piece with the poly to make sure the marker works as well as it does with shellac. If you're not aware of it I highly recommend General Finishes High Performance gloss or satin. Even though I'm a polyurethane hater I used it on the maple in this build for the same reasons as you want on the walnut. 4 years later it's still as white as at first. And not plasticky looking.
https://www.audioasylum.com/forums/amp/messages/23/236010.html
https://www.audioasylum.com/forums/amp/messages/23/236010.html
- Home
- Design & Build
- Construction Tips
- Veneer adhesive?