It's relatively easy for an amplifier to drive a purely resistive load. So these circuits are someone's idea of loading the amplifier as they may be when connected to a speaker, or worse-than a typical speaker. Thinking being if it can drive that successfully, it can drive anything...with the added R2 and C1 for "complex stability" testing at different frequencies.
Since you're concerned with base functionality of your amplifier; does it amplify without anomaly, put out clean current into a very reasonable load, the straight no chaser load design will suffice. Once you establish the amp works, then maybe investigate does it work into a more "tough time" loading situation.
Let's get your base amplifier output tester built, setup and working first. Maybe even "see how it sounds" when connected to your speakers, after it successfully puts out a voltage across those resistors - at rated power. Which it probably will.
Hi jjasniew,
Sorry for my confusing post, I grabbed a schematic and was trying to describe the portion that I thought was what I needed to use. I have no plan other than to load test and safely measure with a PC oscilloscope. I've cropped the image to show what I envisioned (7Ω for R1) , with the leads to the right feeding the required "High Ω" resistor on the "+" leg to drop the voltage to a safe level for "Mic in". I hope this makes more sense. Thanks again, Mike
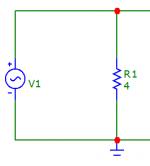
Sorry for my confusing post, I grabbed a schematic and was trying to describe the portion that I thought was what I needed to use. I have no plan other than to load test and safely measure with a PC oscilloscope. I've cropped the image to show what I envisioned (7Ω for R1) , with the leads to the right feeding the required "High Ω" resistor on the "+" leg to drop the voltage to a safe level for "Mic in". I hope this makes more sense. Thanks again, Mike
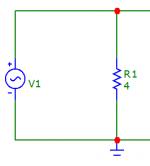
An understanding of how each component works is a good start.
Things fail like burned out resistor, blown transistor and bad capacitors.
Some faults blow out fuses so no point just replacing the fuse.
After that its just down to logical thinking and breaking down equipment into sub sections that can be checked.
Things fail like burned out resistor, blown transistor and bad capacitors.
Some faults blow out fuses so no point just replacing the fuse.
After that its just down to logical thinking and breaking down equipment into sub sections that can be checked.
Hello Nigel,An understanding of how each component works is a good start.
Things fail like burned out resistor, blown transistor and bad capacitors.
Some faults blow out fuses so no point just replacing the fuse.
After that its just down to logical thinking and breaking down equipment into sub sections that can be checked.
Truer words were never spoken!
As to my background; I've worked in Radiation Protection since 1979 (Three Mile Island) and eventually became tasked with "Root Cause Analysis", which can be human, equipment, procedure, or all of the above. At the same time, I often traded shifts so I could work Midnight-8am and pursue other activities during the day--I'm well versed on many things, but "in-situ" electronic troubleshooting isn't one of them.
I learned at an early age that troubleshooting, rather than just changing failed parts was essential to proper equipment repair. I consider myself well versed on electricity, and I understand the function and testing of resistors, capacitors, transistors, diodes, etc. When "out of circuit". I've also worked on most aspects of auto repair (I'll leave body work to someone else) and Heavy equipment repair as well as being an average to above average machinist, welder/fabricator.Your comment reminds me of an equipment failure that presented a challenge, and I feel some pride in being able to properly troubleshoot and ultimately facilitate a proper repair, when others who claimed to be way more qualified failed to perform basic troubleshooting:
I have a friend who owns a trucking and excavating business, and some years back one of his machines, a Komatsu PC400 excavator, was experiencing hydraulic main control valve failure (excessive drift), and so his "Mechanics" replaced the valve assembly. 2 months later it was "Bad" again. So they replaced it again. A little over a month after that it was "Bad" again!
That's when my friend Mark called me. I spoke with the equipment operator, who reported that within a day or so of having a new valve installed, the control would "kick" slightly on release, with an accompanying mechanical "pop". I made some phone calls to Komatsu service to no avail--just guesses and speculation, like "the pump is probably shot", or "It's a pilot valve issue". I told Mark we needed to get the factory service manual, and when he protested about the $200 price, I reminded him that he'd blown about $12k on parts alone and the problem was only getting worse. As luck would have it, all the "bad" valves were still in the corner of the shop, so I did a tear-down and inspection. I immediately noticed black gritty deposits and a burned smell.
The manual goes into detail on how to properly bleed all the air from the hydraulics after service, and importantly mentions that "trapped air may damage hydraulic components". The operator had previously demonstrated how loading the upper arm followed by lowering the (lower) boom would produce the aforementioned "kick" and "pop" when the stick was returned to center.
This is a medium pressure (5000psi nominal) system, and all the seals in the system must not only hold that pressure in, they also need to prevent "atmospheric intrusion" on cylinders or any other component subject to a "Non-commanded" load--such as the arm being "commanded" while the lower boom is in the "hold" position.
More reading of the manual describes how to perform a vacuum test on pilot valves, cylinder seals etc.
So we fabbed up a test rig, and found one of the lower boom seal heads was allowing substantial air intrusion. I tested all the cylinders that were connected to the "burnt" spool sections, and the rest passed.
When I explained that I had found the root cause of the Main Control Valve failure, I was met with a dismissive attitude by Mark's main mechanic. He grudgingly made the repair (both cylinders sent out for seal head rebuild) and the problem was fixed.
What I suspected was happening, and was later confirmed, was that air induced into the boom cylinder was eventually migrating to the Control Valve, where it was then subject to greater than 5000psi as the boom assembly was arrested on descent. This, in turn, compressed the air, heating to the ~400F (or more) temperature required for compression ignition i.e. "Diesel". With hydraulic oil right there, ignition was insured--and these valves aren't designed operate as mini-Diesel engines!
So if there's a moral to my incredibly long-winded story, it's to learn as much as possible before proceeding, and know when to ask for help.
Thank You for commenting, Sincerely, Mike
https://www.aliexpress.com/item/400...-1;0.89;-1;-1@salePrice;CAD;search-mainSearch
2x15R 100W parallel or 4x 33R parallel, parallel is always better than in series, P= I^2 x R, two equal Rs parallel and every resistor gets only half the current, in series all Rs see the same I!
It’s easy to destroy your sound card / PC when measuring output voltages at a OT. Be careful about potentials (it’s possible that a OT common is NOT connected to GND, see my PP post in this forum, this will present two non-GND potentials at both output terminals!). Do not forget you usually have a ground loop via the power adapter of the laptop/PC and USB/sound card GND and the amp power supply and common GND in the amp.
It’s better to use a cheap isolated USB scope, like a VDS 1022(I). The (I) is the most important. It does isolate the DUT from GND/EARTH your USB is connected to. Or at least use you laptop on battery only to isolate it from mains GND/EARTH! Using a PC, you can use a transformer to power your PC to isolate from mains GND. And last but not least do not forget that on a multi channel scope the GND on each BNC connectors are connected. If you forget this then harmful potential differences can destroy the scope or something in the amp, what ever is dying first.
2x15R 100W parallel or 4x 33R parallel, parallel is always better than in series, P= I^2 x R, two equal Rs parallel and every resistor gets only half the current, in series all Rs see the same I!
It’s easy to destroy your sound card / PC when measuring output voltages at a OT. Be careful about potentials (it’s possible that a OT common is NOT connected to GND, see my PP post in this forum, this will present two non-GND potentials at both output terminals!). Do not forget you usually have a ground loop via the power adapter of the laptop/PC and USB/sound card GND and the amp power supply and common GND in the amp.
It’s better to use a cheap isolated USB scope, like a VDS 1022(I). The (I) is the most important. It does isolate the DUT from GND/EARTH your USB is connected to. Or at least use you laptop on battery only to isolate it from mains GND/EARTH! Using a PC, you can use a transformer to power your PC to isolate from mains GND. And last but not least do not forget that on a multi channel scope the GND on each BNC connectors are connected. If you forget this then harmful potential differences can destroy the scope or something in the amp, what ever is dying first.
Last edited:
There is a New Jersey Audio Society -- Wife and I usually have babysitting duties on Sunday when they meet, but they have some great guys and very nice meetings. PM me if interested.
Thanks Tubekiddo,
I already have 3 250 watt plate resistors, measuring 6.9, 7.0 & 7.1 ohms. They were advertised as "6.8 ohms", but since the Amps I intend to load test are all supposedly qualified for 4-8 ohm speaker impedance, I intend to use the 2 higher value units, one per channel, and then add the needed resistance beyond to supply a signal voltage that won't fry my laptop. Determining that value, given "Mic in" soundcard specs, Windows or Linux OS and "Virtual 'Scope" app (I plan to use REW) is where I want to err on the low side voltage-wise and work from there. From everything I can glean, my target voltage should be 0.001v to 0.7v at full Amp output voltage.
I'm pretty sure all the Amps I have are "OK", as they pass the visual and smell test, but I'd rather run them on a dummy load for some time prior to connecting them to speakers--just out of an abundance of caution.
Thank you for your input, Sincerely, Mike
I already have 3 250 watt plate resistors, measuring 6.9, 7.0 & 7.1 ohms. They were advertised as "6.8 ohms", but since the Amps I intend to load test are all supposedly qualified for 4-8 ohm speaker impedance, I intend to use the 2 higher value units, one per channel, and then add the needed resistance beyond to supply a signal voltage that won't fry my laptop. Determining that value, given "Mic in" soundcard specs, Windows or Linux OS and "Virtual 'Scope" app (I plan to use REW) is where I want to err on the low side voltage-wise and work from there. From everything I can glean, my target voltage should be 0.001v to 0.7v at full Amp output voltage.
I'm pretty sure all the Amps I have are "OK", as they pass the visual and smell test, but I'd rather run them on a dummy load for some time prior to connecting them to speakers--just out of an abundance of caution.
Thank you for your input, Sincerely, Mike
Just make sure your ‘GND/Common ground’ speaker terminal is Really connected to GND/Earth. Otherwise you’ll have a potential difference to your PC’s sound card GND (when connected via power adapter) which will fry your sound card/PC. Not sure you really understood the issue…
Thank You for your advice,Just make sure your ‘GND/Common ground’ speaker terminal is Really connected to GND/Earth. Otherwise you’ll have a potential difference to your PC’s sound card GND (when connected via power adapter) which will fry your sound card/PC. Not sure you really understood the issue…
Yes, I'm all too familiar with fried servers and PSU's! (Employers, not mine) And even though I have 7 Dell E6400's that I bought as a lot at auction for the equivalent of ~$40/ea. I have no desire to carelessly fry one! Unless I'm wrong on this, my 810 watt APC UPS should insure the Amp being tested and the laptop(s) should share an isolated common ground. I'm also planning on connecting the Amp Chassis GND. to the 115v ground on the UPS. Beyond that, testing for ANY voltage between channel GND and chassis GND would be cause for further investigation before feeding a signal to my laptop. Please correct me if I'm missing something here.
Sincerely, Mike
Thanks tubekido!
I try not to overthink things, but I've also seen plenty of (pick a craft; electrician, machinist, mechanic, etc.) just wing it and expect success! I've heard plenty of stories about damaged/destroyed equipment, and also-sadly- some injury/fatality stories that were 100% avoidable--mostly Linemen and Tree service related, But I've made it this far by erring on the side of caution, and that includes asking for advice or help when I'm pretty certain I already know the answer.
For that I am Very Appreciative of the generous and helpful responses such as yours. Regards, Mike
I try not to overthink things, but I've also seen plenty of (pick a craft; electrician, machinist, mechanic, etc.) just wing it and expect success! I've heard plenty of stories about damaged/destroyed equipment, and also-sadly- some injury/fatality stories that were 100% avoidable--mostly Linemen and Tree service related, But I've made it this far by erring on the side of caution, and that includes asking for advice or help when I'm pretty certain I already know the answer.
For that I am Very Appreciative of the generous and helpful responses such as yours. Regards, Mike
- Home
- Member Areas
- Introductions
- Intimidated, but just trying to learn some basics