Not sure if this is the right forum, but here goes....
I've been using some old Audioquest speaker cable for years. Now I'm rearranging my listeing space and need to make a splice. Not sure exactly which one, I can't find it on their website any more. Anyway, it's about 15mm OD. The construction is 6 18 ga. stranded conductors for each polarity for a total of 12 conductors in a spiral. Tne whole thing is pretty damn stiff.
I'm not sure what the best approach would be for the splice. I'm thinking maybe stripping of 6" or so of each end of the jacket so I've got 6" of conductors to work with. Then butt splice each conductor for one polarity around the circumference from one side towards the other while maintaining the spiral. IOW first conductor splice is closest to the left cable using ~1" and 6" of the right cable. Next splice is shifted over an inch or so (2" of left conductor, 5" of right conductor) etc. Then last splice is closest to the right cable with the splices forming a staggered spiral. Repeat for other polarity opposite the first splice. Hope this makes sense. I can visualize, but hard to describe. It seems like this would reasonably preserve cable geometery and make for the thinnest splice. I typically use WBT "silver" solder. Obviously everything would be sealed and covered with heat shrink tubing,
So, is this a reasonable approach? I guess I'm a kind of cable skeptic so impact on sonics isn't foremost in my mind. But maybe it should be, so thoughts or experiences would be welcome if they're concrete - I can speculate on all the theoretical problems with splices with the best of them. 🤓 That said, suggestions, comments and experiences welcome! Thanks and cheers,
I've been using some old Audioquest speaker cable for years. Now I'm rearranging my listeing space and need to make a splice. Not sure exactly which one, I can't find it on their website any more. Anyway, it's about 15mm OD. The construction is 6 18 ga. stranded conductors for each polarity for a total of 12 conductors in a spiral. Tne whole thing is pretty damn stiff.
I'm not sure what the best approach would be for the splice. I'm thinking maybe stripping of 6" or so of each end of the jacket so I've got 6" of conductors to work with. Then butt splice each conductor for one polarity around the circumference from one side towards the other while maintaining the spiral. IOW first conductor splice is closest to the left cable using ~1" and 6" of the right cable. Next splice is shifted over an inch or so (2" of left conductor, 5" of right conductor) etc. Then last splice is closest to the right cable with the splices forming a staggered spiral. Repeat for other polarity opposite the first splice. Hope this makes sense. I can visualize, but hard to describe. It seems like this would reasonably preserve cable geometery and make for the thinnest splice. I typically use WBT "silver" solder. Obviously everything would be sealed and covered with heat shrink tubing,
So, is this a reasonable approach? I guess I'm a kind of cable skeptic so impact on sonics isn't foremost in my mind. But maybe it should be, so thoughts or experiences would be welcome if they're concrete - I can speculate on all the theoretical problems with splices with the best of them. 🤓 That said, suggestions, comments and experiences welcome! Thanks and cheers,
My approach would be to buy a spool of 16 gauge zip cord and sell your audiophile cables to someone who has not learned yet. 😈
If you insist on splicing, the "proper" in-line splice is known as the "Western Union Splice" Google it.
If you insist on splicing, the "proper" in-line splice is known as the "Western Union Splice" Google it.
I've been using some old Audioquest speaker cable for years ... pretty damn stiff.
I'm with tvrgeek. This sounds like an ideal opportunity to invest in new, more manageable, loudspeaker cables.
Just for a laugh, I submit the following link which seeks to answer the question, "What will splicing bring you?": https://charmkinggame.org/soldering/will-splicing-cause-damage-to-the-speakers-wires/
I quote:
"When you splice a wire that has a connection with the sound it will give you out a major disadvantage where the sound a will get cut at every particular interval and the transmitter will not be able to perform its action."
I hope that's perfectly clear! 😵
Yes, it´s a very reasonable approachNot sure if this is the right forum, but here goes....
I've been using some old Audioquest speaker cable for years. Now I'm rearranging my listeing space and need to make a splice...... it's about 15mm OD. The construction is 6 18 ga. stranded conductors for each polarity for a total of 12 conductors in a spiral. ...... I'm thinking maybe stripping of 6" or so of each end of the jacket so I've got 6" of conductors to work with. Then butt splice each conductor for one polarity around the circumference from one side towards the other while maintaining the spiral. IOW first conductor splice is closest to the left cable using ~1" and 6" of the right cable. Next splice is shifted over an inch or so (2" of left conductor, 5" of right conductor) etc. Then last splice is closest to the right cable with the splices forming a staggered spiral. Repeat for other polarity opposite the first splice. Hope this makes sense. I can visualize, but hard to describe. It seems like this would reasonably preserve cable geometery and make for the thinnest splice. I typically use WBT "silver" solder. Obviously everything would be sealed and covered with heat shrink tubing,
You call it a "splice" which is correct electrically, mechanically might be something else.
At each joint I would leave 8-10 mm copper exposed on each side, twist strands so as to make a sort of cylinder and tin that stub, then put them side by side and solder them together.
Then slide heat shrink over it and apply hot air.
Repeat for all others.
Staggering joint is a good idea and will look neater.
Personally don´t think spiral matters much but not arguing that, this splice/joint level will keep geometry anyway.
Which is nonsense here.If you insist on splicing, the "proper" in-line splice is known as the "Western Union Splice" Google it.
Typical DIY Audio answer where somebody googles the question and copypastes or parrots the answer without any analysis.
Yes, IF you google "what is the best splice?" you will probably get "Western Union Splice" .... so what?
Waste 30 seconds looking at the answer, not even need to read it.
Western Union was a TELEGRAPH Company, dating from the Cowboy era, its personnel had often to repair telegraph wires , in the middle of nowhere, with no electricity or soldering equipment available, so joint/splice would be "surface contact" only, and mechanically strong.
So they developed this elaborate wire to wire knot :
Mind you, telegraph signals are typically a couple mA at best, your speaker wire will pass Amperes.
Twisting will put them in contact, but no comparison with a fully soldered joint.
I think then you can save on the on both silver solder and tubing...... I guess I'm a kind of cable skeptic so impact on sonics isn't foremost in my mind. ...
Get some single solid core mains installation cable of say 1,5-2mm2 - get rid of the outer plastic shielding. Tie the ends of a pair of these now freed cables (1 brown & 1 blue?) together and fasten it to a door handle and fire up your screw driver and tie the other end of the cable pair to the chuck. Now tighten up the cables and start turning the screw driver and wait for an even twist - not too tight but a turn every say 1 or 2 cm (1 or 2 turns per inch).
Tada! - Your new high end cable... and DIY!!!
//
No idea why are there no pictures... some cables are much easier to splice than others. It will be traumatic in any case and i doubt it will sound quite the same post surgery. On the bright side, it's a wonderful opportunity to experiment with adding a "network box" instead of that horrid heatshrink.
Excuse me, but the WU splice meets the first priority, that the splice is physically sound. All connections should start by being physically sound before solder. In any case, with speaker cables it is basically irrelevant. If it sounds different, it is the placebo effect. Just physics. If you don't understand what I mean, take a look INSIDE a speaker and then tell me how a splice is going to have a measurable, let alone audible effect.
I'm an old guy and have always worked on the principle of making sure the connection is mechanically sound before soldering.All connections should start by being physically sound before solder.
It really grates with me when videos show wires simply being "tacked together" by solder which is carried on the tip of the soldering iron.
There must be at least six solder joints (per side) between the printed circuit board outlet on my amp and the bass driver in my speaker cabinet!
Perhaps I should go wireless? 🤔
Can someone please explain how a splice in a speaker cable can possibly make any difference in the sound you hear from the speakers. And then further explain how the exact type of splice can be heard.
The only reason would be more or lesser of L and C, susceptibility or admittance of RF that could harm the rest of the system.
//
//
And exactly how would a splice itself, much less the type of splice, change either of those parameters which are distributed along the entire length of the cable?The only reason would be more or lesser of L and C, susceptibility or admittance of RF that could harm the rest of the system.
//
Ya get a spool of 16 gauge zip cord and use it for speakers.
Strip and tin the ends for durability and to prevent fraying.
In a home with normal areas, the wire from speaker to amp being less than 30 feet or so, it's fine.
Anything else is a waste and rediculous.
Strip and tin the ends for durability and to prevent fraying.
In a home with normal areas, the wire from speaker to amp being less than 30 feet or so, it's fine.
Anything else is a waste and rediculous.
Its wont splice of course. But it will be a proper speaker cable.And exactly how would a splice itself, much less the type of splice, change either of those parameters which are distributed along the entire length of the cable?
//
Indeed, but remember to put the heat shrink on at the start - its all too easy to forget, which if you have connectors or a long stiff cable isn't great!So, is this a reasonable approach?
The quick way is a choc-block connector, but you end up with a lump or junction box doing that.
I have no idea what is meant by "a proper speaker cable". Perhaps you can define exactly what that might be.Its wont splice of course. But it will be a proper speaker cable.
//
Can you hear changes in L and C?
Before and after splicing?
If yes, get yourself certified and find work as an audiophile with golden ears.
That is a unique ability you have!
Before and after splicing?
If yes, get yourself certified and find work as an audiophile with golden ears.
That is a unique ability you have!
I always found the obsession with "make it mechanically sound before soldering" unnecessary or irrelevant in most cases.
Why?
Because for "the mechanical joint to protect the solder blob" the wire or leg must first try to move, actually move a little so then the mechanical connection can apply a counterforce to make it stay in place.
Newton´s Third Law or action-reaction principle.
If, say, a resistor leg is passed through a tube socket pin and twisted, then soldered, 99% of the force holding it there will be the solder alloy blob.
Of course, a proper soldered joint, where solder actually wets and joins both dissimilar metals being soldered.
Your
Yes, tyros need mechanical help, epoxying, whatever, because they are poor solderers ... but that´s a different problem.
IF a joint has enough stretch (by applying unnecessary force) to need the extra mechanical strength applied by twisting, etc, then solder is cracked and you are already in a deep pit.
Mechanical forces must be stopped before the joint, by clamps, whatever, not rely on it for mechnical strength anyway.
In this case, pretinned side by side cable stubs, 6 to 10 mm long, soldered together with enough solder so it slightly surrounds it in a barrel or olive shape (not just barely tinned wires where a couple strands touch each side) will mechanically hold very well.
FWIW 99% components in any PCB are solder-held, not twisted , and even if you bend throughole legs before soldering (I do) , still solder by itself does the main (all?) of the job.
In any case and in a shock of reality, somewhat related to this discussion: most parts are glued to a PCB .... because they are soldered to a very thin soft metal strip which in due time is glued to board base material.
The elephant in the room everybody seems to ignore.
Even large electrolytics are soldered to thin glued metal , except the VERY infrequent screw terminal "computer grade" ones.
No surprise that it is considered good practice to further glue cap cans to board.
Oh well, in any case, here there is no mechanical strain applied to speaker cable, so solder and heatshrink is more than enough, no need for elaborate hippie trinket type twisting.
Here, this beautiful piece of Art looks very much like some of the suggestions above, and will make for a very good speaker cable.
Even the beads can do a useful (electrical) job if made out of Ferrite, go figure 🙂
In fact, proficiency may lead to a new and lucrative career, of course I suggest studying and practicing first:
Why?
Because for "the mechanical joint to protect the solder blob" the wire or leg must first try to move, actually move a little so then the mechanical connection can apply a counterforce to make it stay in place.
Newton´s Third Law or action-reaction principle.
If, say, a resistor leg is passed through a tube socket pin and twisted, then soldered, 99% of the force holding it there will be the solder alloy blob.
Of course, a proper soldered joint, where solder actually wets and joins both dissimilar metals being soldered.
Your
does not apply here, I thought we were talking between Pros, not tyros.wires simply being "tacked together" by solder which is carried on the tip of the soldering iron
Yes, tyros need mechanical help, epoxying, whatever, because they are poor solderers ... but that´s a different problem.
IF a joint has enough stretch (by applying unnecessary force) to need the extra mechanical strength applied by twisting, etc, then solder is cracked and you are already in a deep pit.
Mechanical forces must be stopped before the joint, by clamps, whatever, not rely on it for mechnical strength anyway.
In this case, pretinned side by side cable stubs, 6 to 10 mm long, soldered together with enough solder so it slightly surrounds it in a barrel or olive shape (not just barely tinned wires where a couple strands touch each side) will mechanically hold very well.
FWIW 99% components in any PCB are solder-held, not twisted , and even if you bend throughole legs before soldering (I do) , still solder by itself does the main (all?) of the job.
In any case and in a shock of reality, somewhat related to this discussion: most parts are glued to a PCB .... because they are soldered to a very thin soft metal strip which in due time is glued to board base material.
The elephant in the room everybody seems to ignore.
Even large electrolytics are soldered to thin glued metal , except the VERY infrequent screw terminal "computer grade" ones.
No surprise that it is considered good practice to further glue cap cans to board.
Oh well, in any case, here there is no mechanical strain applied to speaker cable, so solder and heatshrink is more than enough, no need for elaborate hippie trinket type twisting.
Here, this beautiful piece of Art looks very much like some of the suggestions above, and will make for a very good speaker cable.
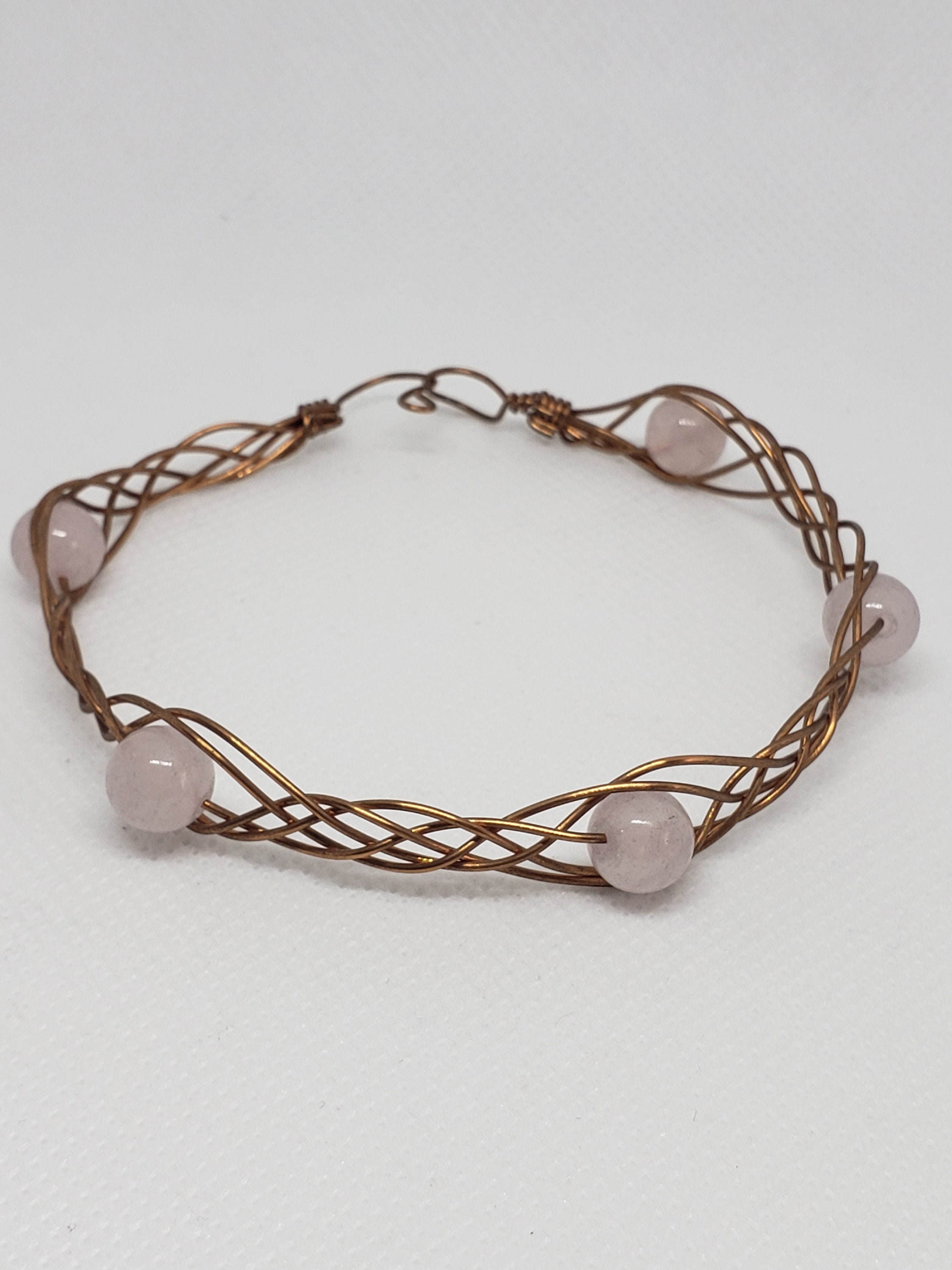
Even the beads can do a useful (electrical) job if made out of Ferrite, go figure 🙂
In fact, proficiency may lead to a new and lucrative career, of course I suggest studying and practicing first:

- Home
- General Interest
- Everything Else
- Splicing speaker cable