If I remember correctly, the TAD Reference 1 is also a translaminated design. Correction; The TAD Model 1 was. The Reference 1 is a newer version that does not use this technique.
6moons.com - industry features: Home Entertainment 2003 in San Francisco
6moons.com - industry features: Home Entertainment 2003 in San Francisco
Last edited:
Highlight the area of interest, so for eg., the inside bottom area of the cabinet. Right click and select Entity Info. Area is up at the top.
Yep, perfect. Thanks for that!
My walls are really thcik so I was worrying I wouldn't be able to get the internal area big enough but one slice is ust over 1 ltr which is perfect.
I don’t know if you guys can get to the Google image search i did, there are many examples:
translam speaker - Google Search
IIRC there is/was a Finnish company making translam speakers with CNCed in waveguides.
dave
translam speaker - Google Search
IIRC there is/was a Finnish company making translam speakers with CNCed in waveguides.
dave
IIRC there is/was a Finnish company making translam speakers with CNCed in waveguides.
Might be these guys. If so they have abandoned translam.
Amphion Loudspeakers – Speakers for your home – monitors for your studio
Big 3D printers capable of printing speakers like in Post #1 are coming down in price with improving finesse, but with even greater control and not near so much waste.
If you have big bucks you can buy such a printer now.
And a whole world of printing smaller pieves together with stuff that might aid in resonance control.
dave
Re the system in the1st post. Cabinet design = bad idea for a ported system. Generates flow restrictions, turbulence and noise.
Besides that, one is not using the ply in the direction of its strengths, so the walls have to be thicker.
This is true. The translam construction can be advantageous from the perspective of making complex shapes. But from the standpoint of strength and stiffness, a translam wall will not be as stiff or as strong as a conventional plywood wall of the same thickness.
In plywood (or fiberglass, or kevlar, or carbon fiber), you only get strength from the fibers running in the direction of the load. A wall which is subjected to out of plane bending (like air pressure) sees a 2 dimensional stress state. Conventional laminated structure is perfect to react this load. Conventional laminates (like plywood) have fibers oriented in a symmetrical pattern with plies at 0, 90, +45, -45 degrees.
With translam, only 25% of the ply layers are ideally positioned to react panel wall bending. It will need to be thicker than a conventional laminate in order to be as strong and stiff.
This does not mean it can not be effective. And I am not criticizing anyone who chose this method. For some complex shapes, it may be the only practical method. We just need to be aware of the limitations.
Supposedly, TAD gave up on the method because of the complexities involved. Here's an excerpt from the absolute sound..
In 2000, TAD decided to create a division that would bring to the consumer market some of the technologies the company had developed for the professional audio world. They hired the talented loudspeaker designer Andrew Jones, who had spent much of his career at KEF working with legends of British loudspeaker design including Raymond Cooke, Laurie Fincham, and Peter Baxandal. Jones’ first product for TAD was the Model One, an audacious ground-up design whose massive cabinet was built from horizontally stacked birch ply. This construction was revived a few years later by Magico in the Mini, scaled down in size by an order of magnitude. The Model One was a sonic success (our Anthony H. Cordesman bought a pair), but the enclosure turned out to be just too difficult and expensive to manufacture.
In 2000, TAD decided to create a division that would bring to the consumer market some of the technologies the company had developed for the professional audio world. They hired the talented loudspeaker designer Andrew Jones, who had spent much of his career at KEF working with legends of British loudspeaker design including Raymond Cooke, Laurie Fincham, and Peter Baxandal. Jones’ first product for TAD was the Model One, an audacious ground-up design whose massive cabinet was built from horizontally stacked birch ply. This construction was revived a few years later by Magico in the Mini, scaled down in size by an order of magnitude. The Model One was a sonic success (our Anthony H. Cordesman bought a pair), but the enclosure turned out to be just too difficult and expensive to manufacture.
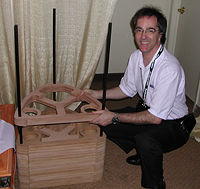
Last edited:
OP speaker doesn't have any diffusing at top and bottom plates, but filling? I don't think BR flow will make extra noise, but I an't really see how BR tubes go.
Finnish Penaudio uses translam, but I guess internals is normal.
I designed and a carpenter made MDF discs with pentagonal cutout for bass box of AINOs, glue has held perfectly for 7 years now. Painted professionally too
Finnish Penaudio uses translam, but I guess internals is normal.

I designed and a carpenter made MDF discs with pentagonal cutout for bass box of AINOs, glue has held perfectly for 7 years now. Painted professionally too
Attachments
Why someone would want to use this technique for anything other than complex, difficult shapes is beyond me. A total waste, from a functional perspective.
And of course, Magico, which used tensioning rods connecting the aluminum baffle to the aluminum back(Somewhat similar to what Vivid employs, but they use it on the actual drivers), which allows the baffle to be somewhat mechanically decoupled from the cabinet.
Last edited:
If I were going to DIY a speaker with strongly curved walls, I would build a frame which would define the shape of the curved walls, then I would bend multiple layers of 1/4 inch material and glue them in place. I would probably use plywood-mdf-plywood, bonded with Weicon as Augerpro recommends.
This seems a lot easier than routing out a very large number of stackable plates.
Bending wood across bulkheads and frames is how wood boat hulls are built.
This seems a lot easier than routing out a very large number of stackable plates.
Bending wood across bulkheads and frames is how wood boat hulls are built.
On smaller cabinets, the routing method would be easier, especially for one and done situations. But for larger cabinets and commercial ventures, the mould technique would be the only practical method. This is what TAD opted for after abandoning the Model 1 cabinet construction method..
The TAD Reference One features our new SILENT (Structurally Inert Laminated Enclosure Technology) cabinet: the ultimate in elegant curves and immense stability. It is constructed from carefully selected materials to resonances, in order that the superior performance of the drive unit is maintained to the maximum degree. The basis of our efforts to eliminate resonance is the strong enclosure design, inspired by the structural theory of aircraft wings and ships. The structure consists of a strong framework with a skeleton having a 21mm (0.9 in.) thick birch plywood transverse bulkhead. It is clad with a hybrid of materials that combine 50mm (2 in.) thick side panels made by high frequency hot press forming glued to CNC machined plywood panels with a maximum thickness of 137mm (5.7 in.). Use of the teardrop form, a design incorporating the concept of hydrodynamics in acoustic engineering, minimizes sound diffraction anomalies. Finally, by applying ABD technology, a technique whereby the dual bass drivers are located so as to eliminate the formation of higher frequency standing waves inside the enclosure that negatively impact sound quality, we achieved a revolutionary enclosure.
The TAD Reference One features our new SILENT (Structurally Inert Laminated Enclosure Technology) cabinet: the ultimate in elegant curves and immense stability. It is constructed from carefully selected materials to resonances, in order that the superior performance of the drive unit is maintained to the maximum degree. The basis of our efforts to eliminate resonance is the strong enclosure design, inspired by the structural theory of aircraft wings and ships. The structure consists of a strong framework with a skeleton having a 21mm (0.9 in.) thick birch plywood transverse bulkhead. It is clad with a hybrid of materials that combine 50mm (2 in.) thick side panels made by high frequency hot press forming glued to CNC machined plywood panels with a maximum thickness of 137mm (5.7 in.). Use of the teardrop form, a design incorporating the concept of hydrodynamics in acoustic engineering, minimizes sound diffraction anomalies. Finally, by applying ABD technology, a technique whereby the dual bass drivers are located so as to eliminate the formation of higher frequency standing waves inside the enclosure that negatively impact sound quality, we achieved a revolutionary enclosure.
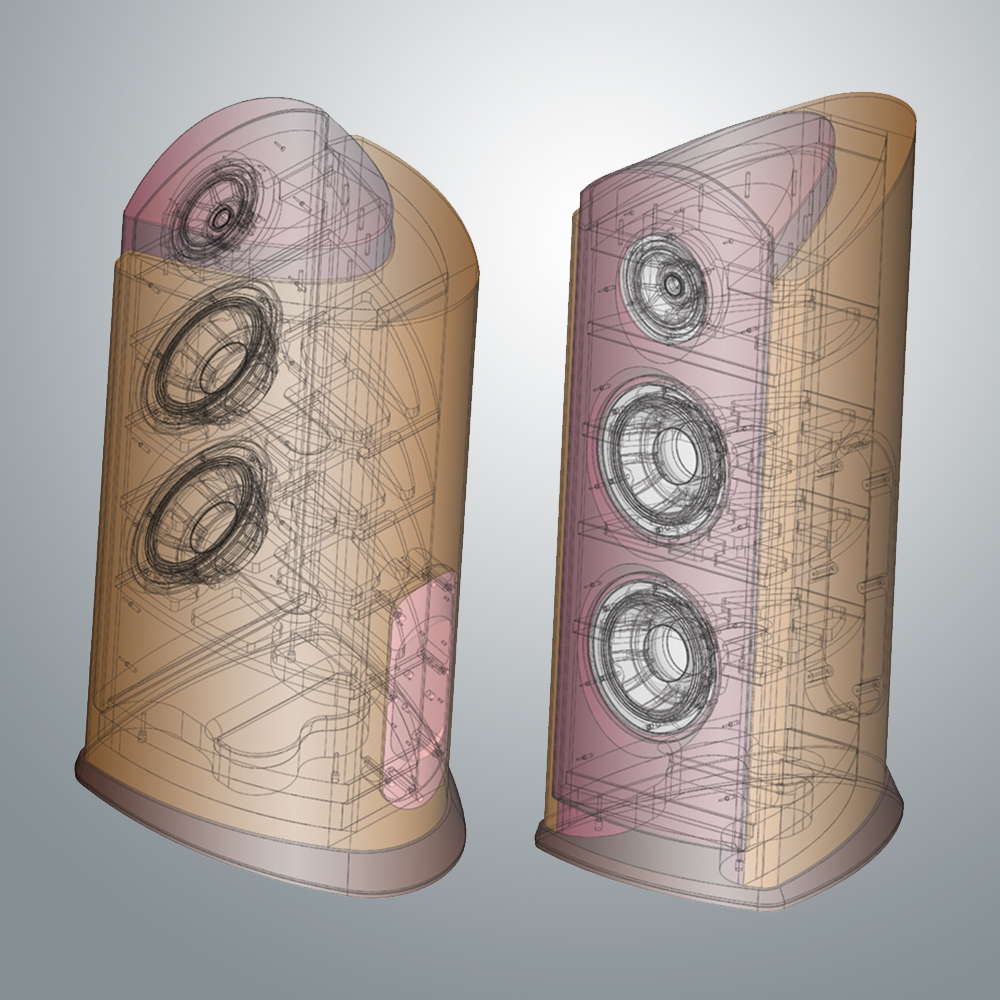
Last edited:
For some complex shapes, it may be the only practical method. We just need to be aware of the limitations.
3D printing promises even more versatolity without so many drawbacks and way less waste.
dave
Hifijim
B&W also employs this technique..
Making a B&W 800 Series Diamond Speaker - YouTube
Diy version..
B&W 800D DIY Speaker - YouTube
B&W also employs this technique..
Making a B&W 800 Series Diamond Speaker - YouTube
Diy version..
B&W 800D DIY Speaker - YouTube
Last edited:
If I were going to DIY a speaker with strongly curved walls, I would build a frame which would define the shape of the curved walls, then I would bend multiple layers of 1/4 inch material and glue them in place. I would probably use plywood-mdf-plywood, bonded with Weicon as Augerpro recommends.
Not as easy as it sounds, we burned our 1st attempt at that. Our successfull attempt used an MDF form (heavier and more material than the actual speaker, double layers of rubber ply, and a vaccuum bag.
dave
Making a B&W 800 Series Diamond Speaker
I love that video. AFAIK the shell that you see being made with all that veneer is in Denmark not the UK.
Essentially they are making quality plywood into exactly the shape they need. You have to sell more than a few speakers to pay for that tool.
dave
Attachments
I am sure it is harder than it sounds, and it already sounds pretty hard.Not as easy as it sounds
- Home
- Loudspeakers
- Multi-Way
- Now that's what I call a cabinet!